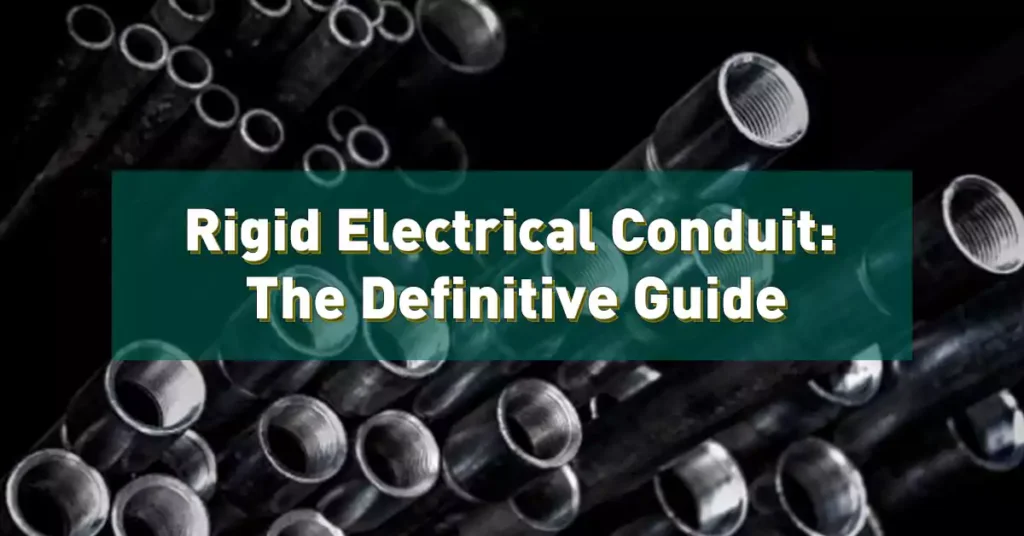
目录
Rigid electrical conduit is a staple in electrical systems, known for its durability and protective qualities, which make it an ideal solution for a range of applications. This guide offers an in-depth exploration of rigid electrical conduit, from types and features to installation guidelines and compliance with codes and standards. By the end, you’ll be well-versed in everything needed to select, install, and maintain rigid conduit for both industrial and residential projects.
Understanding Rigid Electrical Conduit
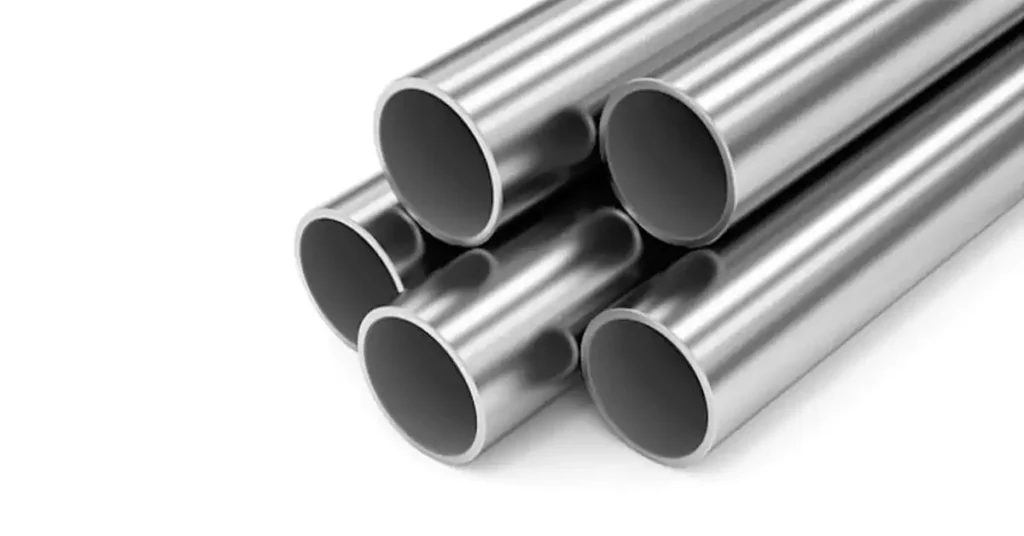
Rigid electrical conduit serves as a robust pathway that houses and protects wiring in various environments. Unlike flexible conduit, rigid types are firm and unyielding, offering excellent protection against environmental hazards, physical damage, and even electromagnetic interference in certain cases. This category encompasses several specific conduit types, each with its unique material composition and suitability for different scenarios.
6 Benefits of Rigid Electrical Conduit
Rigid conduit provides several advantages that make it a valuable choice in both commercial and residential applications:
1. Superior Protection
Rigid electrical conduit provides a high level of mechanical protection against physical damage. Constructed from strong materials like steel, aluminum, and PVC, it acts as a shield, preventing accidental impacts, crushing, and abrasion from compromising the enclosed wires. This durability ensures that wiring remains secure even in high-traffic or industrial environments.
2. Durability and Long Lifespan
One of the most significant benefits of rigid electrical conduit is its long lifespan. Conduits made from galvanized steel or aluminum can last decades without significant wear and tear. PVC conduits, while non-metallic, also boast excellent durability when exposed to various environmental conditions. This long service life reduces maintenance costs and the need for frequent replacements, making rigid conduit a cost-effective option over time.
3. Corrosion Resistance
Corrosion resistance is an essential factor, especially for conduits used outdoors or in damp, corrosive environments. Rigid metal conduits like galvanized steel are treated with a zinc coating that resists rust and corrosion. Aluminum rigid conduit offers a natural resistance to corrosion without additional coatings, making it ideal for installations in marine and other high-moisture areas. PVC conduits, being non-metallic, are inherently immune to corrosion, making them a popular choice for underground or outdoor applications where moisture is a concern.
4. Fire Resistance
Many rigid conduits, particularly those made from metal, provide excellent fire resistance. This is a crucial safety feature in commercial and industrial settings where fire hazards exist. Metal conduits can contain electrical fires and prevent them from spreading, offering an added layer of protection to both the building and its occupants. This feature aligns with various safety codes that prioritize fire resistance in building materials.
5. Electromagnetic Interference (EMI) Shielding
In sensitive environments where electronic devices are used, EMI can disrupt signals and lead to operational inefficiencies. Metal conduits, particularly steel and aluminum, act as a natural shield against EMI, ensuring that sensitive equipment remains unaffected. This property makes rigid metal conduit an excellent choice for data centers, hospitals, and industrial facilities where electronic reliability is paramount.
6. Ease of Installation
Rigid conduit, especially aluminum and PVC types, is easier to handle than many people assume. While rigid metal conduit like galvanized steel can be heavy, modern installation techniques and tools simplify the process. Aluminum conduits are lightweight and easier to cut and thread, making them a preferred choice for projects requiring less labor-intensive handling. PVC conduits are even lighter, easy to cut with simple tools, and can be joined using PVC cement for fast installation.
5 Types of Rigid Electrical Conduit
Rigid electrical conduit comes in different types, each tailored to specific applications and environments. Understanding their properties, advantages, and limitations is crucial for selecting the right type for your project. Below, we explore the five main types of rigid electrical conduit, detailing their pros and cons and including relevant sizing requirements as stipulated by industry standards.
刚性金属导管 (RMC)
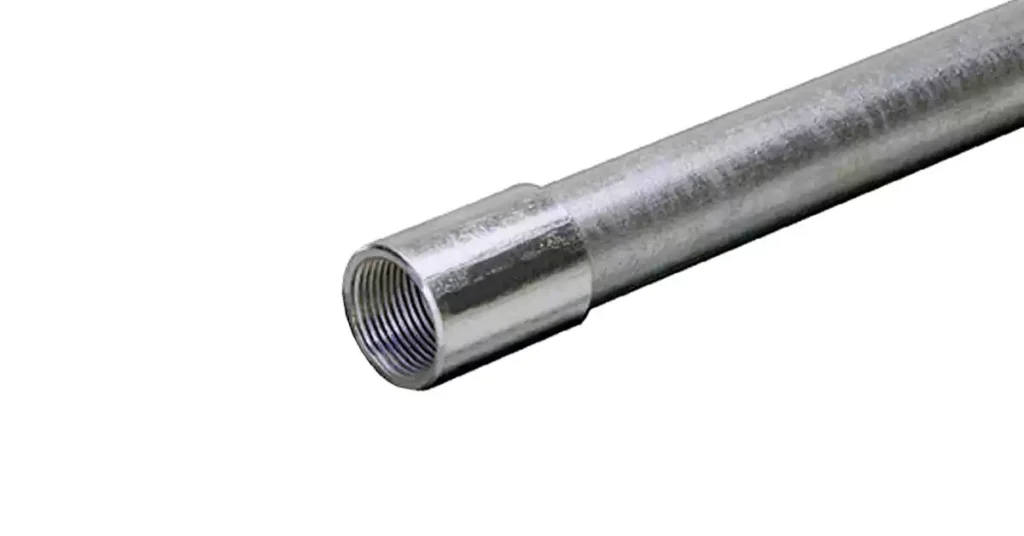
RMC is the heaviest and thickest type of rigid electrical conduit, typically made from galvanized steel. It is designed for use in physically demanding environments where maximum protection is necessary. The conduit is threaded and joined with couplings and fittings to create a robust, grounded pathway for electrical wiring.
- 优点: Provides the highest level of mechanical protection; excellent fire resistance; suitable for areas requiring robust grounding.
- 缺点: Heavy and challenging to install; more expensive than lighter alternatives; prone to corrosion without proper galvanization or protective coating.
Sizing Requirements:
Minimum Size: RMC smaller than metric designator 16 (trade size ½ inch) should not be used.
Maximum Size: RMC larger than metric designator 155 (trade size 6) should not be used, per NEC guidelines.
Rigid Aluminum Conduit
Rigid aluminum conduit is similar to RMC in terms of thickness and strength but is significantly lighter due to the material. It is naturally corrosion-resistant, making it ideal for outdoor and marine applications.
- 优点: Naturally corrosion-resistant, making it perfect for damp or coastal environments; lighter weight simplifies handling and installation.
- 缺点: Less fire-resistant compared to steel conduits; may require specialized fittings to connect with other components.
硬质 PVC 导管
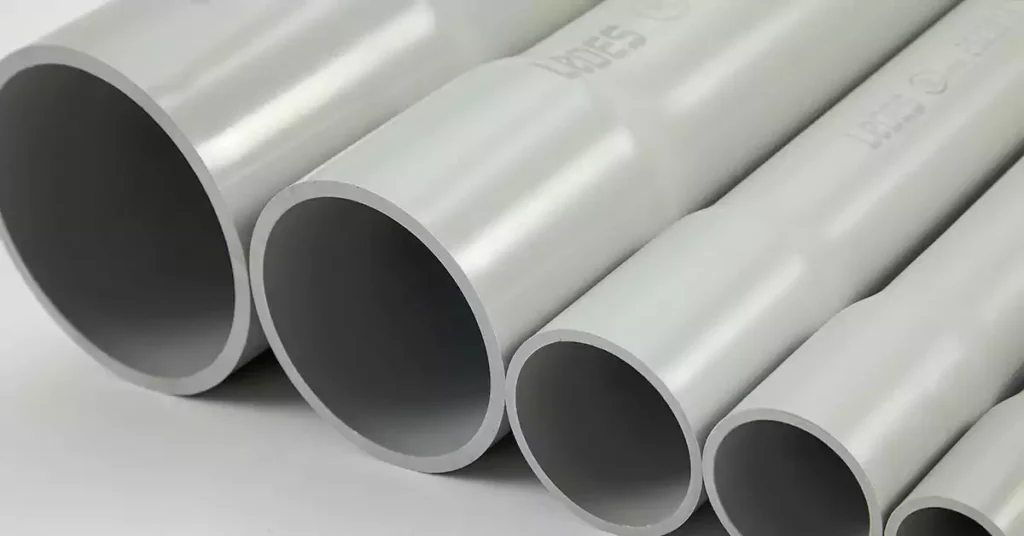
Rigid PVC conduit is a non-metallic alternative known for its light weight and resistance to corrosion and chemicals. It is typically used in underground or outdoor applications where moisture is a concern. PVC conduit can be glued with solvent cement for a secure, watertight connection.
- 优点: Immune to rust and corrosion; lightweight, making cutting and assembly straightforward; cost-effective, especially for large-scale projects.
- 缺点: Sensitive to temperature extremes, potentially causing brittleness in cold weather; limited fire resistance; exposure to UV light can degrade non-stabilized PVC over time.
中间金属导管 (IMC)
IMC is a lighter version of RMC, offering a similar level of mechanical protection but with thinner walls. It was designed to reduce the cost and weight associated with using RMC while maintaining strength and durability.
- 优点: Balances strength and weight well; provides significant protection at a lower cost than RMC; suitable for many outdoor applications.
- 缺点: May not be as effective as RMC for grounding; special tools may be needed for installation.
Fiberglass Conduit (RTRC)
Fiberglass Reinforced Thermosetting Resin Conduit (RTRC) is a non-metallic option known for its high strength, durability, and resistance to corrosion. It’s often used in industrial, outdoor, and harsh environments where chemical exposure or moisture are concerns. Fiberglass conduit is joined using special adhesive or mechanical fittings, ensuring a secure, durable connection.
- 优点: Highly resistant to corrosion and chemicals; lightweight yet strong, simplifying handling and installation; does not conduct electricity, adding safety benefits; maintains performance in extreme temperatures.
- 缺点: Higher upfront cost compared to PVC and metal conduits; requires careful handling to avoid damage; exposure to UV light can degrade non-stabilized fiberglass without protective coatings; special tools may be needed for cutting and installation.
5 Types of Rigid Electrical Conduit Summary
Type of Conduit | 材料 | 重量 | 应用 | Special Features |
刚性金属导管 (RMC) | Galvanized steel | 重的 | Industrial, Outdoor | Fire-resistant, grounding path |
Rigid Aluminum Conduit | 铝 | 轻的 | Marine, High-moisture | Corrosion-resistant |
硬质 PVC 导管 | PVC (Polyvinyl Chloride) | 轻的 | Residential, Outdoor | Non-metallic, UV-resistant |
中间金属导管 (IMC) | 镀锌钢 | 中等的 | Commercial, Residential | Lighter than RMC, strong |
Fiberglass Conduit (RTRC) | Fiberglass-reinforced resin | 轻的 | Harsh environments, chemical plants, outdoor | High corrosion resistance, withstands extreme temperatures |
Each type of rigid electrical conduit has its advantages and specific use cases. The decision to use one type over another depends on factors such as the environmental conditions, budget, and installation requirements. Selecting the correct size and type ensures compliance with NEC and NEMA standards, which helps maintain safety and efficiency in electrical installations.
EMT Conduit Vs. Rigid Metal Conduit

When choosing between Electrical Metallic Tubing (EMT) and Rigid Metal Conduit (RMC), understanding their differences is essential to match the right type to the project’s needs. Although both serve as protective pathways for electrical wiring, they have distinct characteristics that affect their suitability for different applications.
What is EMT Conduit (Electrical Metallic Tubing)?
EMT conduit Often referred to as “thin-walled” conduit, EMT is made of galvanized steel or aluminum. It is lightweight and has thinner walls than rigid conduits, making it easy to work with, bend, and install. EMT is commonly used in indoor settings where mechanical protection is required but not as intense as in industrial environments.
9 Differences Between EMT Conduit and Rigid Metal Conduit
方面 | EMT Conduit | 刚性金属导管 (RMC) |
壁厚 | Thin-walled | Thick-walled |
重量 | Lightweight, easy to handle | Heavy, more challenging to install |
耐用性 | Provides moderate mechanical protection | Offers superior protection against physical impact and environmental hazards |
灵活性 | Highly flexible; easy to bend with a conduit bender | Low flexibility; difficult to bend without specialized equipment |
安装 | Easier to bend and cut; ideal for quick installations | Requires threading and coupling, making installation more labor-intensive |
应用 | Typically used in indoor, protected environments such as commercial buildings and residential settings | Suitable for outdoor, underground, or industrial settings with potential exposure to harsh conditions |
成本 | Generally more affordable | More expensive due to material thickness and durability |
防火性能 | Provides basic fire resistance | High fire resistance due to thicker walls |
Grounding | Can serve as an equipment grounding conductor | Acts as an effective grounding path and provides robust electrical continuity |
Code Compliance and Standards
Both EMT and RMC must meet NEC (National Electrical Code) requirements to ensure safe and compliant installation. While EMT is governed under NEC Article 358, RMC is covered by NEC Article 344. The code defines the conditions for use, support, grounding, and allowable fittings for each type of conduit.
Choosing Between EMT and RMC
The decision between EMT and RMC depends on the project’s unique requirements:
Choose EMT if the project is indoors, requires cost-effectiveness, and allows for easy modifications.
Opt for RMC if maximum durability, superior protection, and outdoor or industrial-grade installation are needed.
Careful consideration of the pros and cons, along with compliance with NEC guidelines, will ensure that the selected conduit type meets the safety and functional requirements of the project.
5 Applications of Rigid Electrical Conduit
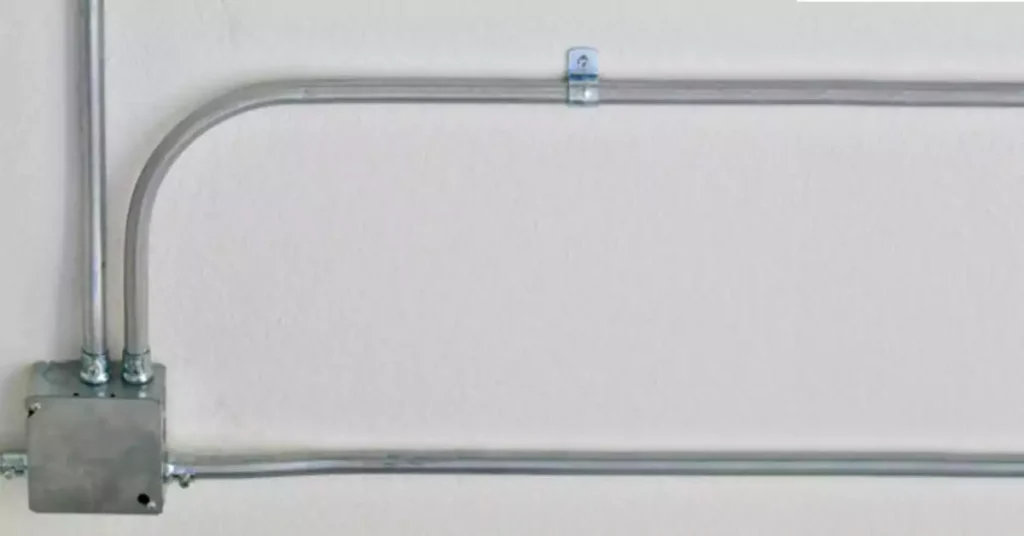
The most commonly used types are metal conduits (such as Rigid Metal Conduit, or RMC) and PVC conduits. Each type has specific applications, advantages, and NEC (National Electrical Code) guidelines that determine their appropriate use.
Below, we explore the permitted uses for both metal and PVC rigid conduits according to the NEC, focusing on Article 344.10 for metal conduit and Article 352.10 for PVC conduit.
Rigid Metal Conduit (RMC) – Uses Permitted (NEC Article 344.10)
Rigid Metal Conduit (RMC) is known for its durability and is suitable for various demanding applications. According to NEC Article 344.10, the permitted uses for RMC include:
- General Use:
RMC can be installed in exposed and concealed locations.
It is suitable for both dry and wet conditions, as well as in locations subject to physical damage.
The NEC permits RMC in all atmospheric conditions and exposures, provided it is installed with the proper protective coating.
- Outdoor Applications:
RMC is ideal for outdoor installations due to its robust construction, providing mechanical protection against weather and physical impacts.
Common outdoor uses include wiring pathways for buildings, parking structures, and outdoor lighting systems.
- Underground Installations:
When installed with appropriate fittings, RMC is permitted to be used in underground locations.
This makes it a popular choice for sub-surface wiring to protect against moisture and corrosion.
- Hazardous Locations:
The NEC allows RMC in hazardous (classified) locations due to its mechanical strength and fire resistance, such as in Class I, Division 1 and 2 areas, which involve flammable gases or vapors.
- Corrosive Environments:
RMC can be installed in environments with moderate to severe corrosive influences when adequately coated or made from corrosion-resistant materials such as stainless steel.
PVC Conduit – Uses Permitted (NEC Article 352.10)
PVC 导管 is a non-metallic option known for its resistance to moisture and corrosion. NEC Article 352.10 outlines the following permitted uses for PVC conduit:
- Above ground and Underground Installations:
PVC conduit can be used both above ground and underground. When installed above ground, it must be secured and supported as per NEC requirements.
It is widely used in underground installations due to its natural resistance to moisture and corrosion. This makes it ideal for protecting buried electrical systems.
- Exposed and Concealed Locations:
PVC conduit can be installed in exposed locations but must be protected from physical damage where necessary.
It is commonly used in concealed spaces within walls, ceilings, and floors in residential, commercial, and industrial buildings.
- Corrosive Environments:
PVC conduit is excellent for environments that are chemically aggressive or prone to corrosion, such as chemical plants or areas with high moisture content.
- 潮湿的地方:
NEC permits PVC conduit in wet locations due to its non-conductive and water-resistant properties.
It is commonly used in pool areas, car washes, and similar wet environments.
- Direct Sunlight Exposure:
PVC conduit can be used in locations exposed to direct sunlight if it is specifically marked or treated for UV resistance.
- 温度考虑因素:
PVC conduit can withstand temperature fluctuations but should be chosen based on its rated temperature. For areas with extreme temperatures, ensure that the PVC conduit type meets the temperature rating outlined in the NEC.
Code Compliance & Standards
Code compliance and adherence to standards are essential for ensuring the safety, efficiency, and longevity of electrical installations. The National Electrical Code (NEC) provides clear guidelines and requirements for different types of conduits, including rigid metal and PVC rigid conduits. While we have introduced PVC conduit in previous articles, this part will offer an in-depth interpretation of NEC Article 344, which outlines the description and requirements for Rigid Metal Conduit (RMC).
Rigid Metal Conduit: Article 344, NEC
PVC Conduit: Article 352, NEC
Overview of NEC Article 344: Rigid Metal Conduit
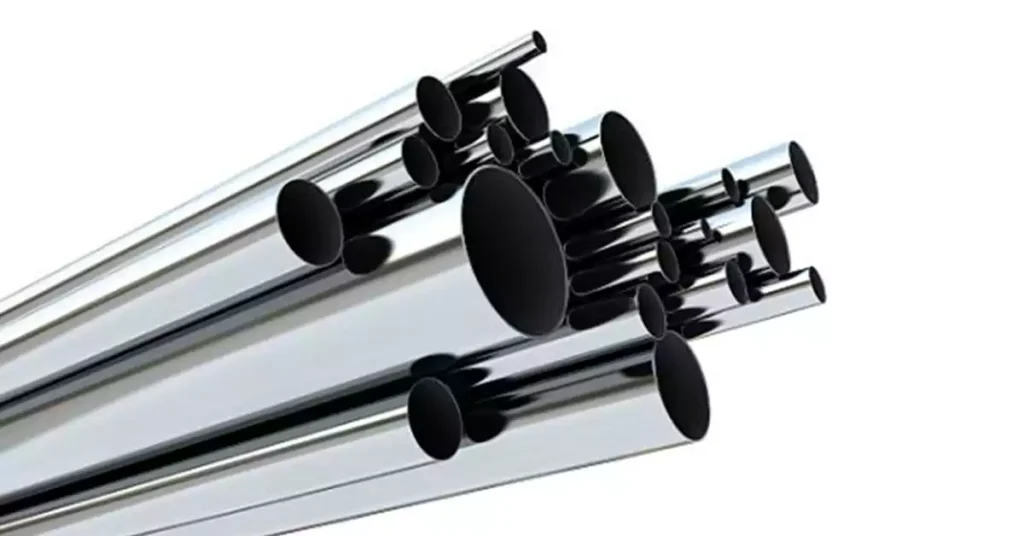
NEC Article 344 sets forth comprehensive guidelines for the use, installation, and characteristics of Rigid Metal Conduit. These requirements are crucial for maintaining electrical safety, structural integrity, and code compliance across various applications. The article encompasses aspects like permitted uses, construction specifications, grounding, and support requirements.
Size Specifications (344.20):
The NEC defines the allowable trade sizes for RMC, ranging from metric designator 16 (trade size 1/2) to metric designator 155 (trade size 6). Sizes outside this range are not permitted to ensure optimal mechanical performance and compatibility with standard fittings.
Number of Conductors(344.22)
The NEC requires that the number of conductors within an RMC must comply with the fill capacity limits outlined in Chapter 9, Table 1 and related tables to prevent overheating and allow for safe heat dissipation.
The Numbers of Conductors for RMC(344.22)
Number of Conductors or Cables | Cross- Sectional Area (%) |
1 | 53 |
2 | 31 |
Over 2 | 40 |
Bending Requirements (344.24):
When bending RMC, it is essential to maintain the conduit’s internal diameter without deformation. The NEC specifies minimum bending radii to prevent damage and facilitate easy cable pulling. This helps protect the wiring from excessive force that could cause insulation damage or conductor strain.
Threading and Reaming (344.28):
Cut ends of RMC must be reamed to remove sharp edges, ensuring cables can pass through without risk of damage. Additionally, threads on conduits should be clean and properly formed to guarantee tight, secure connections that maintain electrical and mechanical continuity.
Securing and Supporting (344.30):
RMC must be properly secured and supported within 3 feet (900 mm) of any termination point, such as a box or fitting, and at intervals not exceeding 10 feet (3 m). This requirement prevents sagging, which could compromise the safety and reliability of the installation.
Securing and Supporting for NEC Code 344.30
Conduit Size | Maximum Distance Between Rigid Metal Conduit Supports | |
交易规模 | m | ft |
1/2 – 3/4 | 3.0 | 10 |
1 | 3.7 | 12 |
1-1/4 – 1-1/2 | 4.3 | 14 |
2 – 2-1/2 | 4.9 | 16 |
3 及以上 | 6.1 | 20 |
Grounding and Bonding (344.60):
RMC is permitted to serve as an equipment grounding conductor when properly installed. This ensures a low-impedance path for fault current, facilitating the operation of overcurrent protection devices and enhancing overall system safety.
Rigid Electrical Conduit Accessories & Fittings
To ensure a safe, reliable, and code-compliant electrical conduit system, various accessories and fittings are used during installation. These components are essential for connecting, securing, and transitioning conduit runs. Here, we explore the most commonly used fittings for Rigid Metal Conduit (RMC) and Rigid PVC Conduit, highlighting the differences between them and their applications.
8 Common Fittings for Rigid Metal Conduit (RMC)
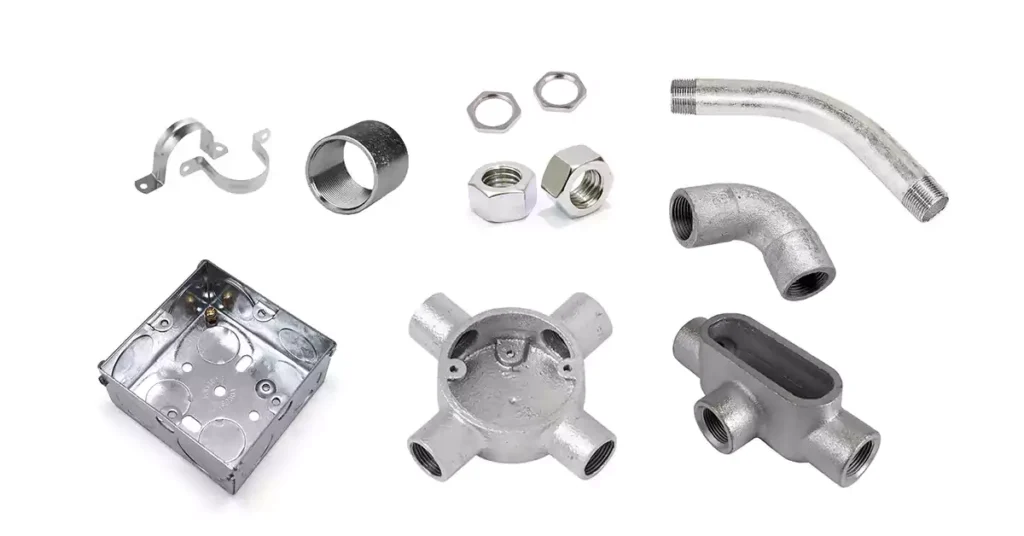
There are 8 common fittings of RMC conduit in electrical installation,
- Couplings: Connects two sections of RMC to create a continuous path. Typically threaded for secure, strong connections.
- Connectors: Attaches RMC to electrical boxes or enclosures, ensuring grounding and stability.
- Elbows: Pre-formed bends for changing direction, maintaining a smooth path for wire pulling.
- Locknuts & Bushings: Locknuts secure conduit to boxes; bushings protect wire insulation.
- Straps & Clamps: Support and secure conduit to surfaces, preventing movement.
- Conduit Bodies : Provide access for wire pulling, splicing, or maintenance.
- Junction Boxes: Metal boxes used for connecting multiple conduit runs, housing splices, and protecting electrical connections.
- RMC Outlet Boxes: Made of metal to ensure grounding, durable and able to handle high-stress environments; available in weatherproof models for outdoor use.
8 Common Fittings for Rigid PVC Conduit
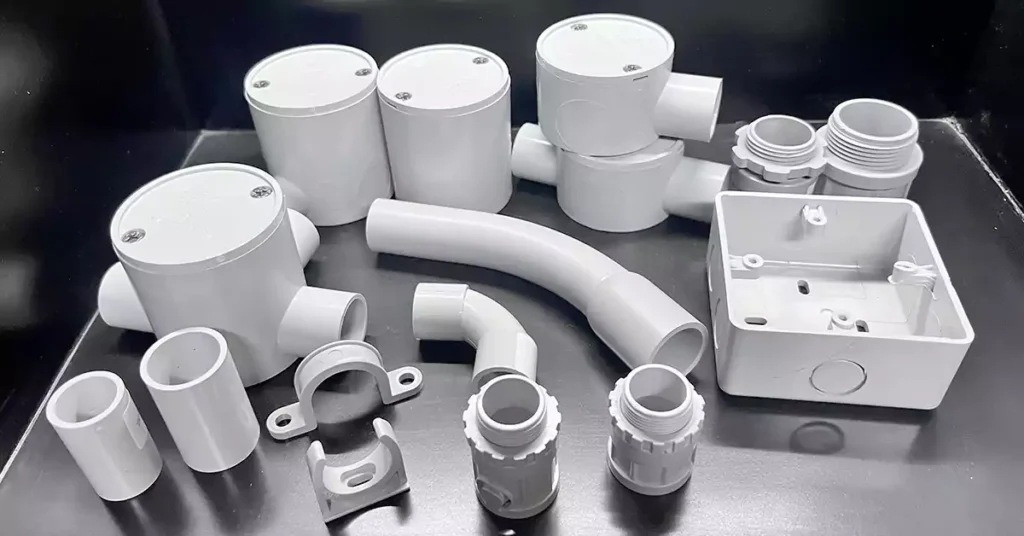
We list the 8 common types of PVC conduit fittings here,
- PVC Couplings: Used to join sections of PVC conduit with solvent cement, ensuring watertight seals.
- Connectors: Attach PVC conduit to boxes, with types such as male and female adapters.
- Expansion Couplings: Allow for expansion and contraction due to temperature changes.
- Elbows: Pre-formed bends for changes in direction, available in 90° and 45° angles.
- Straps & Clamps: Used to fasten PVC conduit to surfaces for stability.
- Conduit Bodies: Provide entry points for pulling or splicing wires and are useful for directional changes.
- Junction Boxes: PVC boxes for housing connections and splices, commonly used in outdoor or wet environments due to their corrosion resistance.
- PVC Outlet Boxes: Non-conductive, corrosion-resistant PVC, lightweight, resistant to moisture and chemicals; available in models with sealed covers for wet environments.
Differences Between RMC and PVC Conduit Fittings
材质成分: RMC fittings are typically made from metal (steel or aluminum) to match the durability and grounding properties of the conduit. PVC fittings are made from polyvinyl chloride, which is lightweight and resistant to corrosion.
Connection Method: RMC fittings often use threading or mechanical connections to join sections, while PVC fittings are joined using solvent cement to create a watertight seal.
Grounding Requirements: Metal conduit fittings play an integral role in grounding the electrical system, whereas PVC conduit systems may require separate grounding conductors since the PVC itself is non-conductive.
灵活性: PVC fittings provide more flexibility and resistance to moisture and chemicals, making them better suited for wet or corrosive environments. RMC fittings, on the other hand, are more robust for environments requiring enhanced mechanical protection.
Rigid Electrical Conduit Installation Guide
Proper installation of Rigid Metal Conduit (RMC) ensures a safe and durable electrical system that meets code requirements and functions effectively for its intended purpose. Below, we provide a step-by-step guide for installing RMC. For details on PVC conduit installation, please refer to our comprehensive guide for PVC conduit installation.
Step-by-Step Installation Guide for Rigid Metal Conduit (RMC)
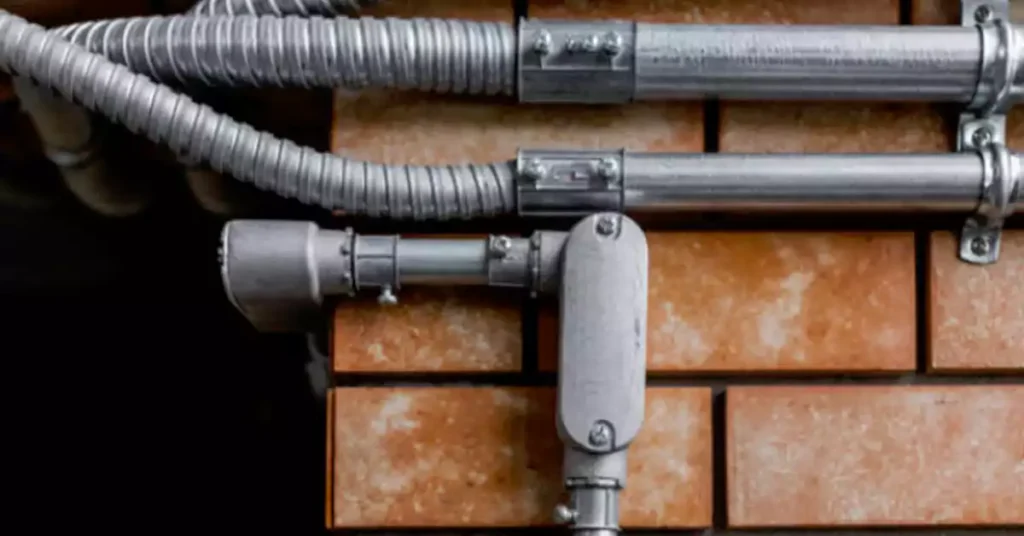
- 规划路线:
Assess the Path: Determine the most efficient path, minimizing bends.
Code Check: Ensure the planned route meets NEC Article 344 and local code requirements.
- Measure and Cut the Conduit:
Measure: Mark the needed length accurately.
Cut: Use a pipe cutter or hacksaw and ensure a clean, square cut.
Deburr: Smooth any rough edges with a reamer or file to protect the wires.
- Threading:
Create Threads: Use a threading die to add threads to the ends of the conduit.
Apply Oil: Use threading oil to make the process smoother and prevent damage.
- Attach Fittings:
Connect Couplings: Thread couplings or connectors onto the ends of the conduit.
Tighten Securely: Use a wrench to tighten, being careful not to overtighten.
- Bend as Needed:
Use a Bender: For direction changes, use a manual or hydraulic bender.
Avoid Sharp Bends: Ensure bends meet NEC radius standards.
- Mount the Conduit:
Secure with Straps: Attach the conduit to surfaces using metal straps at required intervals (usually within 3 feet of a box and at 10-foot intervals for straight sections).
Spacing: Follow NEC spacing requirements.
- 拉电线:
Insert Fish Tape: Feed fish tape through the conduit and attach the wiring.
Apply Lubricant: Use wire-pulling lubricant for long runs.
Pull Carefully: Pull wires through gently to avoid kinks.
- Final Check:
Tighten and Secure: Ensure all fittings are securely connected.
Check Grounding: Verify proper grounding as per NEC Article 250.
Test Continuity: Perform a test to confirm a continuous ground path.
- Weatherproofing (for Outdoor Installations):
Seal Entrances: Use sealant to keep moisture out.
Install Bushings: Protect wire insulation at conduit entry points.
Safety Tips for Installation
Protective Gear: Wear safety glasses, gloves, and boots.
Avoid Power Lines: Ensure the area is clear of active power lines.
Use Proper Tools: Always use tools designed for RMC work.
Top 10 Rigid Electrical Conduit Manufacturers in the USA & Canada
Here’s an overview of ten leading manufacturers of rigid electrical conduit in the USA and Canada, highlighting their company background, product offerings, and market presence.
1. ABB
Company Overview: ABB is a global leader in electrification and automation, with a strong presence in North America. Known for their focus on innovation and sustainability, ABB offers solutions designed to optimize energy efficiency across a wide range of industries.
Products: ABB’s conduit solutions include rigid metal conduit (RMC) and electrical metallic tubing (EMT), focusing on durable, high-performance materials.
Market Position: Known for innovative technology and reliable products, ABB serves various sectors, including industrial and commercial applications.
2. Atkore
Company Overview: Atkore is a leading manufacturer of electrical conduit and cable management solutions. Their wide range of products is designed to meet the needs of various industries, from industrial to residential construction.
Products: Their product line includes rigid metal conduit (RMC), electrical metallic tubing (EMT), and PVC conduit, with a focus on versatility and compliance with stringent standards.
Market Leadership: Known for robust distribution networks, Atkore ensures timely product availability throughout North America.
3. Robroy Industries
Company: Specializing in corrosion-resistant conduit systems, Robroy Industries has built a reputation for delivering durable solutions for harsh environments, particularly in the oil, gas, and chemical industries.
Products: They produce rigid steel and PVC-coated rigid metal conduits, which are ideal for harsh environments.
Industry Experience: With over 100 years of experience, Robroy focuses on providing conduit solutions that are built to last, offering customers peace of mind for projects in extreme weather or corrosive environments.
4. Western Tube
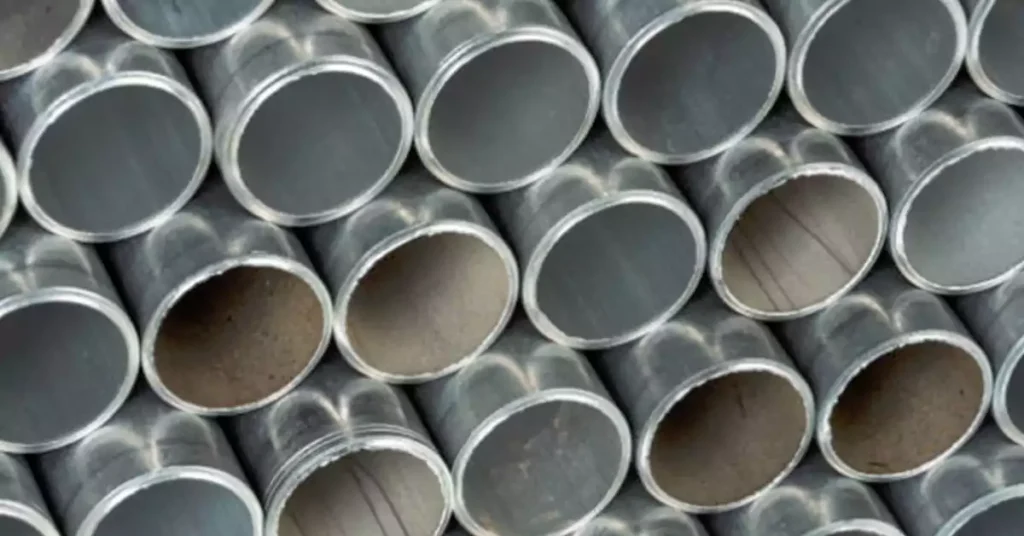
Company Overview: Part of Zekelman Industries, Western Tube manufactures high-quality steel conduit products with a strong focus on domestic production and fast delivery.
Products: They offer a broad range of rigid metal conduit (RMC) and electrical metallic tubing (EMT), designed to meet the electrical needs of residential, commercial, and industrial applications.
市场认可: Western Tube has an established presence in the North American market, with a reputation for producing high-performance products that comply with national standards, while maintaining cost-effective pricing.
5. Ipex
Company Overview: Ipex is a global leader in thermoplastic piping and conduit systems. Based in Canada, Ipex has an extensive product portfolio and has been a key player in the North American market for over 50 years.
Products: They specialize in rigid PVC conduit, which is lightweight, corrosion-resistant, and cost-effective, with applications ranging from residential to large commercial projects.
Environmental Sustainability: Ipex is committed to environmental sustainability, using eco-friendly manufacturing processes and materials to create products that meet stringent regulatory requirements and environmental standards.
6. JM Eagle
Company Overview: JM Eagle is one of the largest plastic pipe and conduit manufacturers in the world. They have a long history of producing high-quality, durable products at scale.
Products: Known for their rigid PVC conduit, JM Eagle’s products are highly regarded for their strength, affordability, and ease of installation.
Sustainability: JM Eagle has a robust commitment to sustainability, offering products made from recycled materials and focusing on reducing environmental impact through energy-efficient manufacturing processes.
7. RITTAL
Company Overview: RITTAL is known primarily for its enclosures, IT infrastructure solutions, and automation systems. Their electrical conduit offerings complement their broader industrial solutions.
Products: RITTAL’s rigid electrical conduit products are designed to integrate with their wide array of automation and industrial enclosure solutions, providing comprehensive protection for electrical systems in high-tech environments.
Company Focus: RITTAL is highly focused on providing tailored solutions for complex industries such as IT, telecommunications, and manufacturing, where precision and reliability are paramount.
8. Wheatland Tube
Company Overview: As a division of Zekelman Industries, Wheatland Tube has over 80 years of experience in the manufacturing of steel conduit. They are one of the largest producers of electrical conduit products in North America.
Products: Wheatland Tube produces a wide range of rigid metal conduit (RMC) and EMT, providing excellent protection for electrical wiring in a variety of environments.
High Quality: Wheatland Tube is known for their commitment to quality and customer service, offering products that meet or exceed NEC standards and ensuring timely deliveries for large-scale projects.
9. NUCOR Public Conduit
Company Overview: A major player in the steel industry, NUCOR produces high-quality conduit solutions as part of its vast portfolio. Known for its sustainability efforts, NUCOR is a leader in energy-efficient steel production.
Products: NUCOR’s rigid metal conduit (RMC) is known for its durability and strength, making it ideal for large infrastructure projects in industrial and commercial applications.
Sustainability: NUCOR’s conduit products reflect their commitment to sustainability, offering customers eco-friendly, long-lasting solutions that meet the highest quality standards.
10. Ledes
Company Overview: Ledes conduit specializes in high-performance electrical conduit systems designed for residential, commercial and industrial applications.
Products: Ledes offers PVC conduit, low-smoke, halogen-free rigid conduit, primarily used in environments where safety and fire resistance are critical, such as healthcare facilities and public buildings.
Commitment to Quality: With a focus on safety and compliance with the industry regulations, Ledes is a trusted supplier for projects requiring enhanced environmental and safety standards.
How to Choose the Right Rigid Electrical Conduit for Your Project
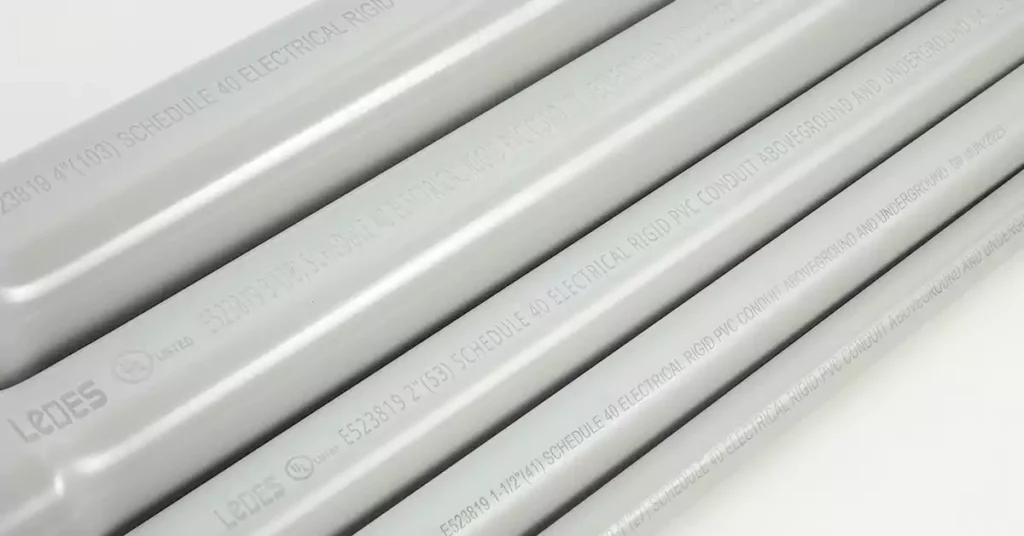
Choosing the right rigid electrical conduit is essential for the safety, durability, and efficiency of your electrical system. Here are some simple guidelines to help you select the best conduit for your project:
1. Consider the Environment
Outdoor Exposure: If the conduit will be exposed to weather, go for materials that resist corrosion, such as rigid metal conduit (RMC) or aluminum rigid conduit (ALR). PVC conduit is also a good option for areas that won’t face extreme weather.
腐蚀: For areas with high moisture or chemicals (like coastal areas or factories), PVC-coated RMC or PVC conduit offers extra protection against rust.
2. Understand Your Application
Residential vs. Industrial: For residential or commercial use, PVC conduit or EMT conduit are affordable and easy to install. For industrial sites that need extra protection, RMC is more suitable.
Fire Safety: If fire safety is a priority (for example, in hospitals or schools), look for low-smoke, halogen-free rigid conduit or fire-resistant PVC conduits.
3. Check the Right Size
Make sure the conduit is large enough to fit the wiring and allows for proper airflow. Don’t over-stuff the conduit, as this can lead to overheating and damage. Also, be aware of size limits: RMC should not be smaller than 1/2 inch or larger than 6 inches, as specified by NEC Article 344.
4. Ensure Compatibility
配件: The type of conduit you choose must match the fittings, connectors, and boxes used. For example, RMC needs specific types of connectors, while PVC conduit has its own set of fittings and may be easier to handle and install.
Existing Systems: If you are expanding or updating an electrical system, choose conduit that matches your existing setup to avoid extra modifications.
5. Follow Codes and Standards
NEC Compliance: Your conduit needs to meet the National Electrical Code (NEC). RMC is covered by Article 344, and PVC conduit by Article 352. Make sure you review these codes to ensure your project is compliant.
Local Codes: Check if there are any local building codes or extra requirements specific to your area or project.
6. Consider Cost and Ease of Installation
安装简便: PVC conduit is lighter and easier to install compared to RMC, which may need special tools and more labor. Consider your project timeline when choosing.
成本: PVC conduit is generally cheaper than RMC but may not offer the same level of protection. Think about balancing upfront cost with long-term durability.
7. Plan for Future Changes
Expansion: If you expect to expand or modify your system in the future, consider the flexibility of the conduit. EMT is more flexible, while RMC offers more protection but is harder to modify.
Maintenance: PVC conduit is low-maintenance, while metal conduits may need periodic checks for rust or damage.
Selecting the right rigid electrical conduit depends on your project’s needs, environmental conditions, budget, and compliance with building codes. Consider the factors above, and if in doubt, consult an electrician to ensure your system is safe and up to code.
Rigid Electrical Conduit Resources
For additional resources, consult:
NEC Code: Official NEC publications offer guidelines on conduit use.
NEMA Standards: NEMA’s website provides access to ratings and requirements for conduit materials.
Manufacturer Data Sheets: Specific installation guidelines are often provided in product datasheets.
Consult an Electrician: An experienced electrician can offer insights on local code requirements and best practices.
结论
Choosing the right rigid electrical conduit is a crucial step in ensuring the safety, durability, and efficiency of your electrical system. From understanding the different types of rigid conduits, such as RMC, PVC conduit, and EMT, to considering factors like environmental exposure, fire safety, and code compliance, each decision plays a key role in the overall performance of your installation. By evaluating the specific needs of your project and selecting the appropriate conduit, fittings, and accessories, you can create a reliable and long-lasting electrical system.
As we’ve seen throughout this guide, it’s important to understand the benefits, applications, and installation requirements of each conduit type, as well as how they align with the standards set forth by the NEC and other codes. Whether you’re working on a residential, commercial, or industrial project, the right conduit ensures your electrical system stays protected and efficient for years to come.
Always keep in mind factors like installation ease, cost, future maintenance, and expansion when making your choice. And, of course, consult with professionals to ensure your system meets all safety and regulatory standards. With this knowledge in hand, you’re now ready to make an informed decision and confidently choose the best rigid electrical conduit for your next project.
We always highly appreciate if you can touch with us if you still have any questions; our electrical conduit expert will reply to you in 1 business day.