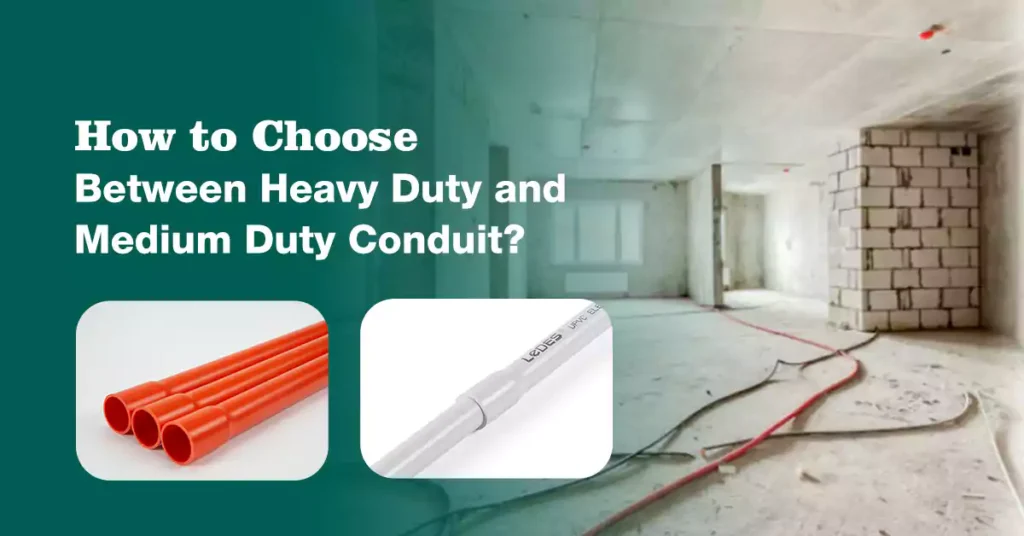
目录
When planning electrical installations, choosing the right conduit is a critical decision that can significantly impact the durability, safety, and efficiency of your project. Among the many factors to consider, understanding the differences between heavy-duty and medium-duty conduits is essential, especially when adhering to standards such as the Australian Standard (AS).
This article provides a comprehensive guide to help you make an informed choice. We will explore the key parameters, specifications, and applications of heavy-duty and medium-duty conduits as defined in the AS standard. Furthermore, we’ll discuss how these specifications apply to different types of conduits, including rigid PVC conduit, corrugated conduit, flexible conduit, and solar conduit. A dedicated section will cover the unique requirements for solar applications, offering insights into conduit selection for sustainable energy systems.
After reading this article, you’ll gain a clear understanding of:
- The primary differences between heavy-duty and medium-duty conduits
- Different conduit types and their uses
- Benefits of using PVC conduit
- The different requirements of AS/NZS 2053 and IEC 61386 for conduits
- Factors you need to consider to choose the appropriate conduit
Electrical conduits are protective ducts designed to house and safeguard electrical and communication cables. These conduits provide critical protection against physical damage, environmental exposure, and mechanical stress, ensuring the integrity and safety of underground or exposed wiring systems.
PVC conduits, a popular choice, are manufactured from durable, non-corrosive plastic and are commonly available in sizes ranging from 16mm to 200mm in diameter. The specific application often determines the size and color of the conduit, adhering to industry and authority standards. Standard colors include:
- 橙子: Used for heavy-duty electrical conduits, typically for low voltage (LV) and high voltage (HV) underground installations.
- 灰色的: Associated with medium-duty electrical conduits, commonly used in domestic and commercial environments.
- 白色的: Reserved for communication conduits, including telco, fibre optics, and National Broadband Network (NBN) installations.
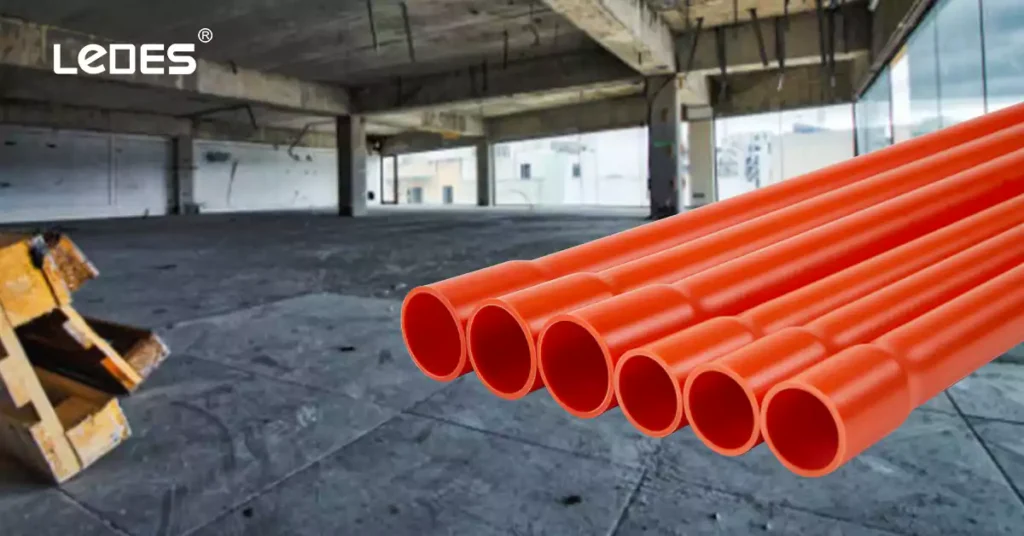
Conduits are integral to diverse industries and sectors, providing safe and reliable pathways for electrical and communication wiring. Common applications include:
- Telecommunications: Safeguarding cables for fibre optic and broadband networks.
- Electrical Power: Supporting LV and HV installations in residential, commercial, and industrial settings.
- Infrastructure Projects: Used in roads, railways, and other public works.
- Defence and Security: Providing robust solutions for secure installations.
- Renewable Energy: Especially important in solar and other sustainable energy systems, where environmental resilience is crucial.
Australian standards classify conduits into light-duty, medium-duty, and heavy-duty categories, depending on their wall thickness and mechanical performance. This classification determines their suitability for different environments and applications:
- Heavy-Duty Conduit: Identified by its greater wall thickness and superior compressive and impact strength, heavy-duty conduit is predominantly orange and is ideal for underground electrical installations.
- Medium-Duty Conduit: A versatile choice, typically grey, used for domestic and commercial installations.
- Light-Duty Conduit: Primarily for non-critical, low-impact applications, often orange in color for underground LV and HV systems.
- Communication Conduit: Generally white, available in both medium- and heavy-duty variations, designed for telco and fibre optic networks.
These classifications provide a standardized approach to conduit selection, helping ensure proper functionality, durability, and compliance in diverse installation scenarios.
Solar Conduits
Solar conduits are a specialized type of conduit designed to meet the unique demands of photovoltaic (PV) systems. These conduits provide robust protection for wiring exposed to harsh environmental conditions, such as intense sunlight, temperature fluctuations, and moisture. Key characteristics of solar conduits include:
- 抗紫外线: To prevent degradation from prolonged sun exposure.
- Thermal Stability: Ensures consistent performance in high-temperature environments.
- Weatherproofing: Protects against rain, wind, and dust in outdoor installations.
- Compliance Standards: Solar conduits adhere to specific guidelines for renewable energy applications, ensuring they meet performance and safety criteria.
Solar conduits are critical for ensuring the longevity and reliability of solar installations, safeguarding the wiring that connects PV panels, inverters, and storage systems. Available in rigid and corrugated forms, solar conduits cater to both above-ground and underground installations, providing flexibility and durability as required.
Conduits are categorized not only by their duty classifications (heavy, medium, or light) but also by the materials used in their construction. Material selection is crucial because it determines the conduit’s durability, application range, environmental performance, and compliance with standards. According to AS/NZS 2053.1, Clause 5, conduits are classified into four primary material categories:
- Metal
- Insulating
- Composite
- Fibre-Reinforced Concrete
This section provides an overview of these materials, focusing on their properties, applications, and suitability for different installation environments.
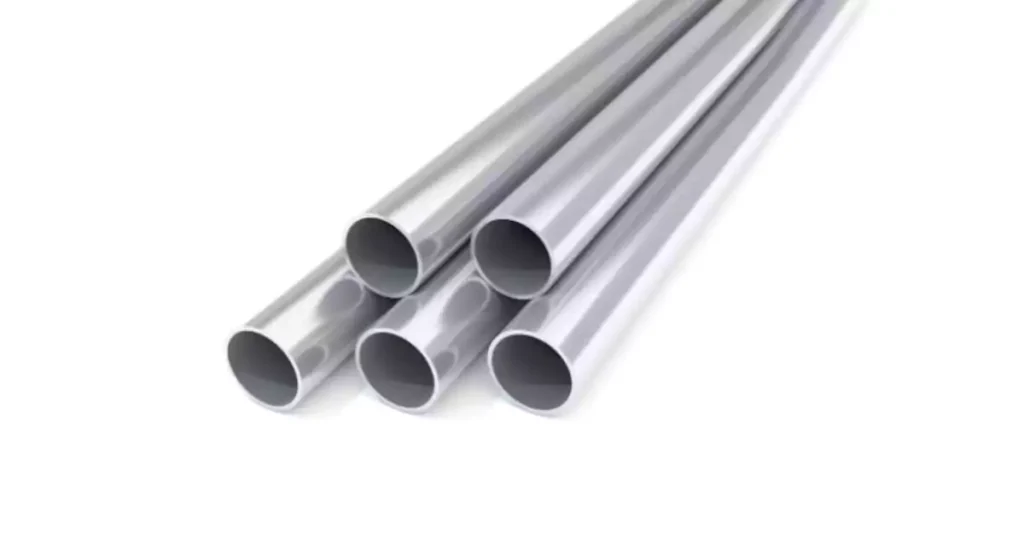
Metal conduits are robust and reliable, often used in applications requiring high mechanical protection or fire resistance. Common types include:
电气金属管(EMT):
Lightweight steel conduit often used in commercial and industrial environments. It offers minimal protection against impact but is easy to install.
刚性金属导管(RMC):
A thicker, galvanized steel conduit with superior durability and corrosion resistance, suitable for outdoor and underground installations.
中间金属导管 (IMC):
Lighter than RMC but with comparable strength, making it ideal for exposed applications where weight savings are beneficial.
柔性金属导管(FMC):
A corrugated, flexible metal conduit used in applications requiring frequent directional changes or vibration resistance, such as machine tools or HVAC systems.
Insulating conduits, primarily made from PVC or other plastics, are versatile and widely used. Types include:
硬质 PVC 导管:
A durable, non-metallic conduit ideal for underground and outdoor applications, available in heavy-duty, medium-duty, and light-duty classifications.
Corrugated PVC Conduit:
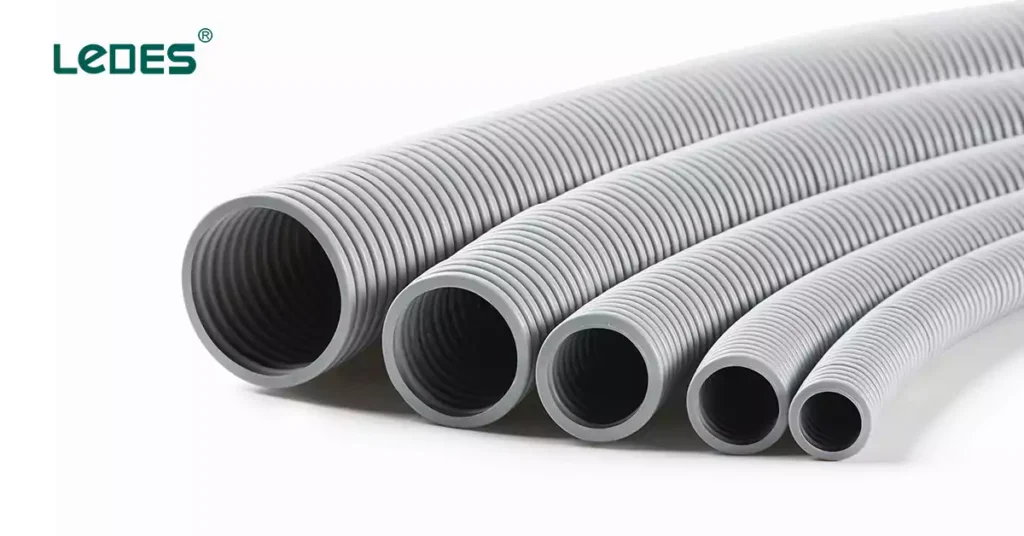
Flexible and lightweight, designed for installations requiring bending or movement, such as in telecommunications or automotive wiring.
Polyethylene (PE) Conduit:
Known for its flexibility and chemical resistance, often used in fibre optic networks and underground communication systems.
Liquid-Tight Non-Metallic Conduit (LTNMC):
A specialized insulating conduit with water-tight properties, used in wet or corrosive environments.
Composite conduits combine multiple materials to offer enhanced properties. Common types include:
Aluminum-Plastic Composite Conduit:
Combines lightweight aluminum for strength with a plastic outer layer for corrosion resistance, often used in outdoor environments.
Steel-PVC Composite Conduit:
A steel conduit lined or coated with PVC for added electrical insulation and chemical resistance. Ideal for industrial settings with corrosive exposures.
Fiberglass Reinforced Plastic (FRP) Conduit:
Provides excellent corrosion resistance, lightweight construction, and strength, used in chemical plants and marine applications.
FRC conduits are highly durable and primarily used in heavy-duty infrastructure applications. Types include:
Prestressed Concrete Conduits:
Manufactured with pre-tensioned steel reinforcement for added strength, used in tunnels, bridges, and highways.
Centrifugally Cast Concrete Conduits:
Made using spinning techniques for uniform strength and density, often used in underground applications requiring extreme compressive strength.
Polymer Concrete Conduits:
A blend of resin and aggregate, offering improved chemical resistance and lighter weight compared to traditional concrete conduits, used in industrial and energy projects.
Distinguishing between heavy-duty and medium-duty conduits is crucial for ensuring safety, regulatory compliance, and long-term performance across a variety of installations. Different applications, environmental conditions, and regional standards necessitate the careful selection of conduit duty levels. Here are the primary reasons why this distinction matters:
Different countries and regions enforce unique standards and requirements for conduit usage based on their environmental conditions and infrastructure needs.
Urban vs. Rural Settings: Urban areas often have dense underground utility networks requiring heavy-duty conduits to handle traffic loads and minimize risk of damage. In rural settings, medium-duty conduits may suffice due to lighter loads.
Industry-Specific Applications: Sectors like renewable energy, rail infrastructure, and heavy manufacturing demand heavy-duty conduits for enhanced mechanical protection, whereas commercial and residential buildings typically rely on medium-duty solutions.
Conduits must protect wiring and cables from environmental threats, and the duty classification determines their ability to withstand these challenges.
Harsh Conditions: Heavy-duty conduits are better suited for environments exposed to heavy soil pressure, water immersion, or corrosive chemicals.
Controlled Environments: Medium-duty conduits provide adequate protection in less demanding conditions, such as indoor installations or sheltered outdoor areas.
The type of conduit directly impacts its ability to withstand mechanical loads.
Heavy Loads: Underground installations in high-traffic areas, such as highways or industrial zones, demand the compressive strength of heavy-duty conduits.
Moderate Loads: Areas with lower traffic or mechanical stresses can utilize medium-duty conduits, reducing costs without compromising performance.
Compliance with AS/NZS 2053.1 and other standards ensures that installations are safe and fit for purpose. Each duty classification has specific guidelines that must be followed for mechanical strength, impact resistance, and durability.
Avoiding Over-Specification: Using heavy-duty conduits in low-stress environments can unnecessarily increase costs.
Preventing Under-Specification: Medium-duty or light-duty conduits used in high-stress areas risk failure, potentially causing system outages or safety hazards.
Selecting the appropriate conduit duty helps balance performance and budget.
Heavy-Duty for Critical Areas: Investing in heavy-duty conduits for critical installations ensures long-term reliability and reduced maintenance costs.
Medium-Duty for General Use: For less demanding applications, medium-duty conduits offer cost-effective solutions without over-engineering the system.
When selecting conduit for electrical installations, understanding the differences between heavy-duty and medium-duty conduit is essential for ensuring the right performance and durability. The key differences in size, color, thickness, performance, weight, price, application scenarios, and marking are based on the standards outlined in AS/NZS 2053.1, AS/NZS 2053.2, and AS/NZS 2053.5. This section compares these two types of conduit, helping you determine which is the best fit for your needs.
There are Rigid Plain Conduit and Corrugated Conduit, both available in light, medium and heavy-duty and other types, each with specific size and thickness requirements. Below is an overview of the dimensions according to AS/NZS 2053.1, AS/NZS 2053.2, and AS/NZS 2053.5.
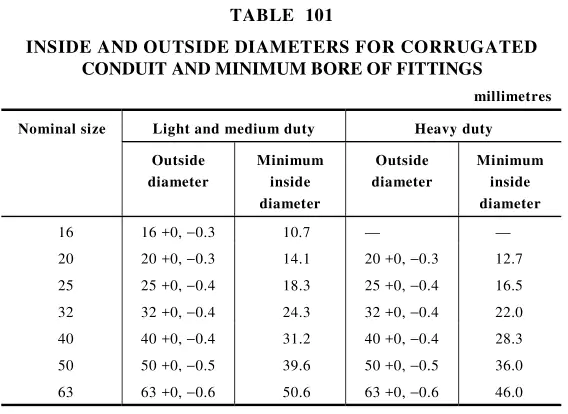
Corrugated Conduit Dimensions (AS/NZS 2053.5)
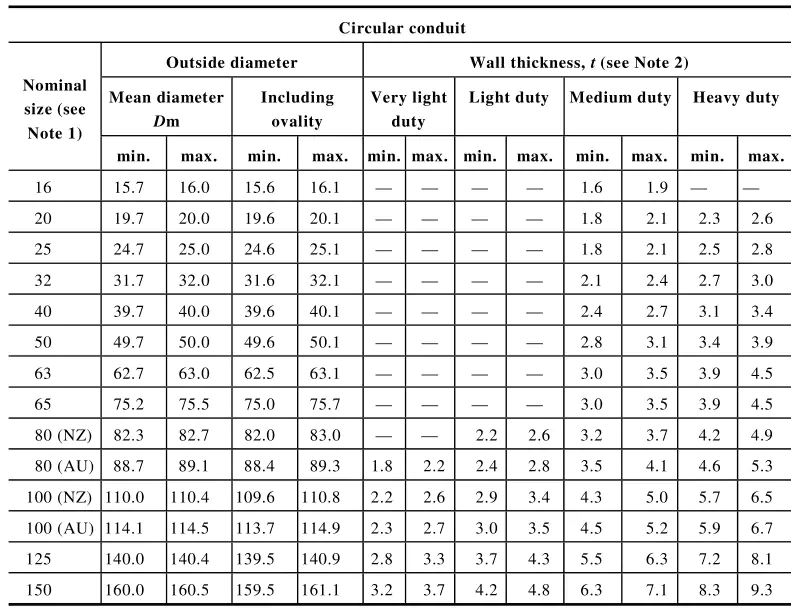
Rigid Plain Conduit Dimensions (AS/NZS 2053.2 TABLE 101)
Heavy Duty Conduit:
Heavy-duty conduits are typically orange in color, as specified in AS/NZS 2053.1. The bright orange color makes them easily identifiable, which is important for safety and compliance in power installations, both for low voltage (LV) and high voltage (HV) systems. The color also helps differentiate power-related conduits from those used for telecommunications.
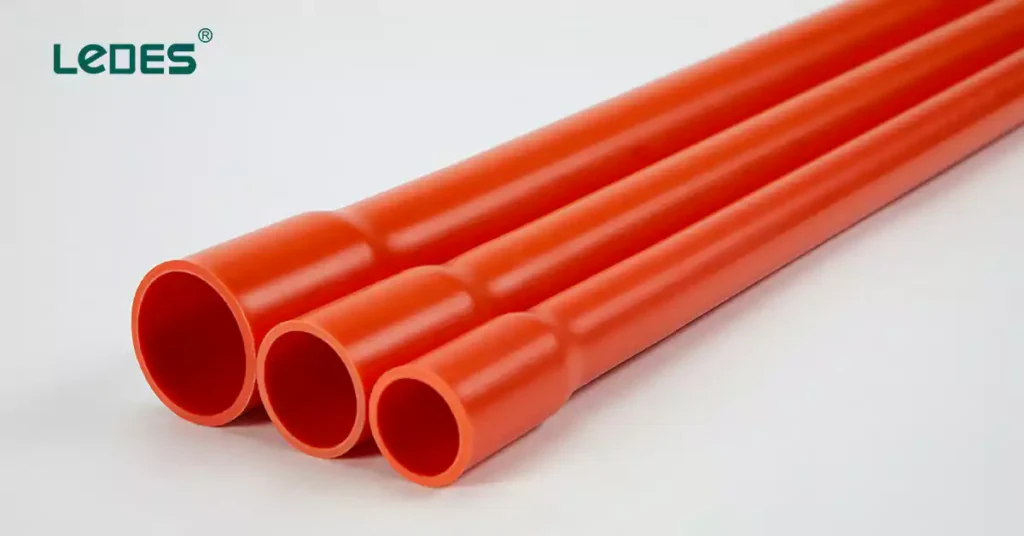
Medium Duty Conduit:
Medium-duty conduits are often grey or white, depending on the application. Grey is the standard for electrical installations in commercial or residential environments, while white is commonly used for telecommunications and fiber optic cables. These colors help identify the conduit’s purpose and ensure safe handling during installation and maintenance.
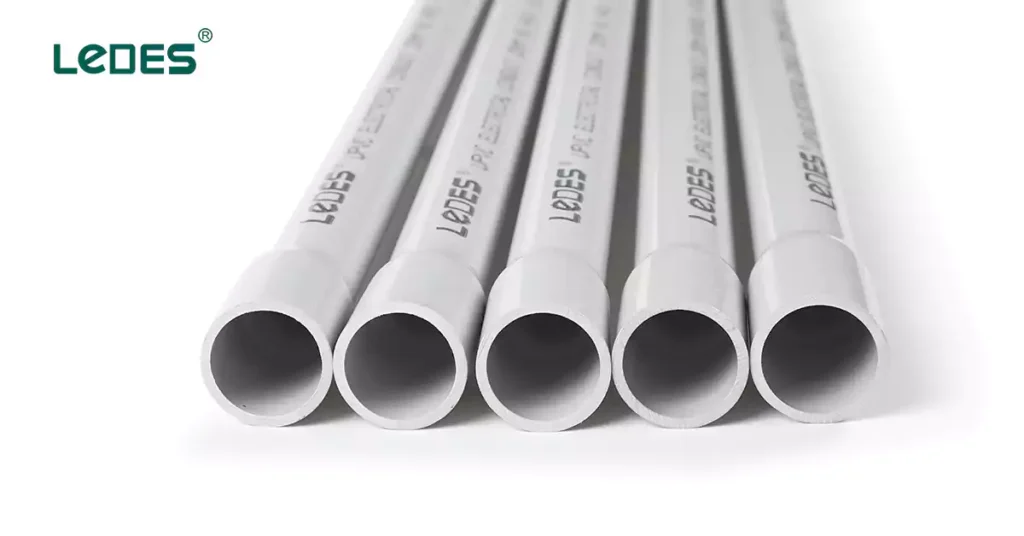
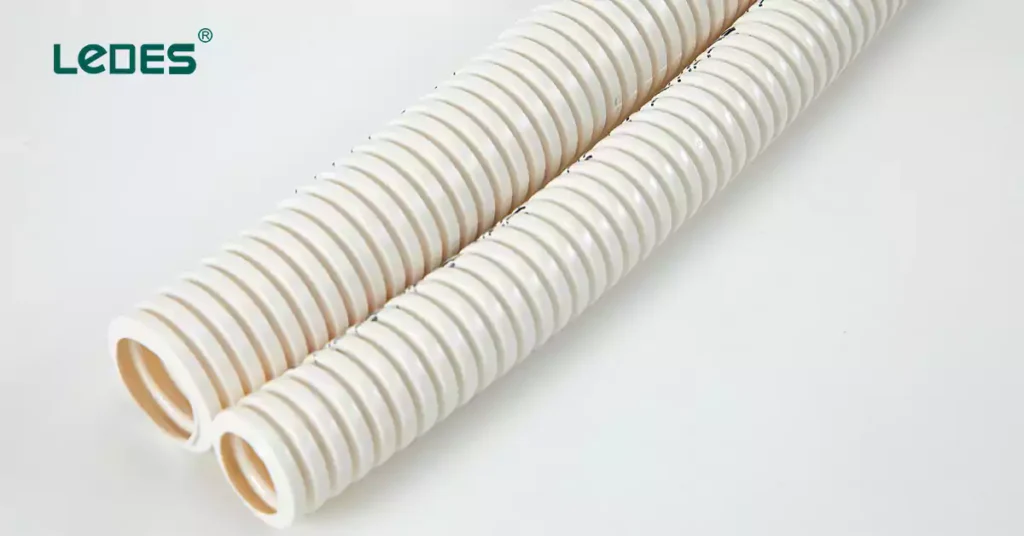
In distinguishing heavy-duty and medium-duty conduits, their performance under stress is crucial. The AS/NZS 2053.1 standard provides clear guidelines for evaluating conduit performance, particularly in terms of compression resistance, impact strength, and collapse resistance. These tests ensure conduits can withstand the mechanical stresses they may encounter during installation and operation.
- 压缩试验
The compression test assesses a conduit’s ability to resist deformation under load. According to AS/NZS 2053.1, conduits are subjected to a uniform load distributed over a defined area. This test ensures the conduit can maintain its shape and protect enclosed cables when exposed to external forces.
Compression Strength Criteria in AS/NZS 2053.1
导管 | Test Load (N) | Deformation Limit |
HD Rigid Conduit | 1250 N | ≤ 10% deformation |
MD Rigid Conduit | 750 N | ≤ 10% deformation |
HD Corrugated Conduit | 1250 N | ≤ 25% deformation |
MD Corrugated Conduit | 750 N | ≤ 25% deformation |
- Impact Test
The impact test evaluates a conduit’s ability to withstand sudden mechanical shocks, such as drops, collisions, or accidental strikes. And the conduit should show no cracks or disintegration when subjected to the following weight and height. This test is crucial for ensuring the conduit’s integrity during handling and installation.
Hammer Weight and Fall Height in AS/NZS 2053.1
Conduit Duty | Weight of the hammer kg | Fall height mm |
中等的 | 2.0 | 100±1 |
重的 | 2.0 | 300±1 |
- Collapse Test
The collapse test is a critical evaluation method outlined in AS/NZS 2053 standards to ensure conduits maintain their structural integrity under mechanical and environmental stresses. This test assesses whether a conduit can retain its internal diameter and functional shape when exposed to bending forces and prolonged high temperatures.
The process begins by bending the conduit test piece at room temperature through a specific angle, typically 90°, using a bending device with a standardized radius.
验收标准: The gauge must pass through the conduit without obstruction or excessive deformation.
Rigid Conduit: According to AS/NZS 2053.2, only conduits of diameter less than 32mm and medium, or light duty conduit should be tested for collapse, heavy duty conduits do not need to be tested. When tested with a bending device, the conduit should pass the diameter check.
Corrugated Conduit: All sizes are applicable. (AS/NZS 2053.5)
Heavy Duty Conduit:
Due to their thicker walls and stronger materials, heavy-duty conduits are heavier than their medium-duty counterparts. This added weight provides greater mechanical protection, but it also means that heavy-duty conduits can be more difficult to handle and install, particularly for large-scale projects. The added weight is a trade-off for their durability and strength in harsh environments.
Medium Duty Conduit:
Medium-duty conduits are lighter in comparison, making them easier to handle and install, especially in areas where heavy-duty conduit would be overkill. The lighter weight makes them ideal for residential wiring, office installations, and other non-heavy-duty applications.
Heavy Duty Conduit:
Heavy-duty conduits are generally more expensive than medium-duty conduits due to their higher material costs, thicker walls, and enhanced performance features. While the upfront cost is higher, these conduits provide long-term value in environments where durability and reliability are critical. For example, in power transmission systems, where conduit failure could lead to costly repairs and safety hazards, the higher price of heavy-duty conduit is justified.
Medium Duty Conduit:
Medium-duty conduits are more cost-effective than heavy-duty options, making them an ideal choice for general-purpose applications such as residential, light commercial, and telecommunications installations. The lower cost is a significant factor when the conduit’s mechanical protection needs are less stringent.
Heavy Duty Conduit:
Heavy-duty conduits are designed for high-stress applications and environments where external forces are significant. Typical uses include:
Underground Power Installations: In areas with heavy traffic, such as roads or industrial zones.
Heavy Industrial Environments: Where impact and compression resistance are vital.
Renewable Energy Projects: Such as solar farms or wind turbines, where conduit must withstand harsh weather and environmental conditions.
High-Voltage Systems: Used in both low-voltage (LV) and high-voltage (HV) electrical installations.
Medium Duty Conduit:
Medium-duty conduits are suited for low to moderate stress environments. Common applications include:
住宅布线: Used for general electrical wiring in homes and buildings.
Commercial Installations: Ideal for wiring in offices, shopping centers, and schools.
Telecommunication and Fiber Optic Installations: Used for the protection of telecommunications cables in controlled environments.
The AS/NZS 2053 standards outline precise marking requirements for all conduit types, ensuring clear identification of their specifications and intended use. Key marking components:
- Manufacturer Identification
- 公称尺寸
- Application Designation: The word “ELECTRICAL” must be included
- Duty Classification: Clearly marked with “ MEDIUM DUTY (MD)” or “HEAVY DUTY (HD)
- Special Properties (Optional): Such as Halogen-Free (HF) and UV protection “T”
- 温度范围
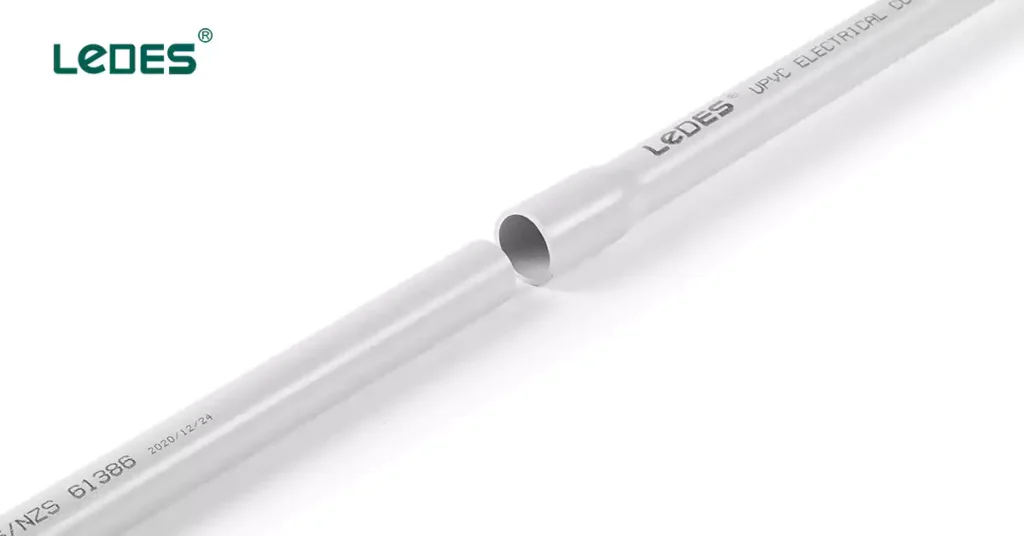
PVC conduit is a popular choice for electrical installations due to its unique properties and advantages compared to metal conduits. Its lightweight nature, durability, and versatility make it a go-to option for residential, commercial, and industrial applications. Below are the key benefits of PVC conduit:
PVC conduits are more affordable than metal conduits due to lower material and manufacturing costs. Additionally, their lightweight nature reduces labor expenses, making them highly economical for large-scale projects.
Unlike metal conduits, PVC is inherently resistant to corrosion, making it ideal for humid or underground environments where moisture could deteriorate metal over time.
PVC conduits are significantly lighter than metal conduits, facilitating easier transportation and installation. This benefit reduces installation time and labor efforts, particularly in overhead or complex layouts.
PVC is a non-conductive material, providing built-in insulation for cables. This eliminates the need for additional grounding, unlike metal conduits, which require grounding to prevent electrical hazards.
Available in various types, sizes, and duty classifications (light, medium, and heavy-duty), PVC conduits can be customized to suit different environments, including underground, outdoor, and even solar installations.
PVC conduits are self-extinguishing, meaning they do not propagate flames, enhancing safety in case of a fire.
PVC Vs. Metal Conduit
特征 | PVC 导管 | Metal Conduit |
成本 | 低的 | 高的 |
耐腐蚀 | 出色的 | Prone to rust unless treated/coated |
重量 | 轻的 | 重的 |
Electrical Insulation | Built-in | Requires additional grounding |
易于安装 | Easy | Labor-intensive |
防火性能 | 自熄性 | Conductive, may require extra measures |
Strength | Relatively lower than Metal | 高的 |
The standards AS/NZS 2053 and IEC 61386 are both internationally recognized frameworks governing the design, testing, and application of electrical conduits. While they share similarities in ensuring safety and performance, the standards diverge in structure, scope, and testing requirements due to regional priorities and regulatory needs.
AS/NZS 2053
- Region: Australia and New Zealand.
- Scope: Focuses on rigid and flexible conduits for electrical applications, tailored to local environmental and industry requirements.
- Primary Concerns: Durability, UV resistance, and performance under extreme Australian and New Zealand conditions, including temperature fluctuations and heavy mechanical loads.
IEC 61386
- Region: European Union and internationally.
- Scope: Covers conduit systems for cable management in diverse settings, from industrial to residential.
- Primary Concerns: Comprehensive classification based on mechanical and electrical characteristics, emphasizing uniformity across European markets.
These two has similar requirements for conduits, they both divided the conduit into same 5 classifications: Very Light, Light, Medium, Heavy, Very Heavy. The test forces for their mechanical performance also the same. But there some differences in certain testing conditions, acceptance criteria etc. And part of the test items also different, here are the comparison of some key tests:
Tests | AS/NZS 2053 | IEC 61386 | ||
Conditions | 验收标准 | Conditions | 验收标准 | |
压缩 | Test pieces should be conditioned at 20 ±1°C for at least 10 h | OD difference≤ 10% for rigid conduit; OD difference≤ 25% for corrugated conduit;
| test at (23 ± 2) ºC | OD difference≤25%, 60s after removing force |
Impact | Condition temperatures are specified by manufacturer. | No signs of disintegration or cracks at least 9 of 12 test pieces | Condition temperatures are specified in Table 1 of the standard for 2 hours. | No signs of disintegration or cracks at least 9 of 12 test pieces |
坍塌 | Condition temperatures are specified by manufacturer. | The gauge must pass through the conduit without obstruction or excessive deformation.
| Rigid conduit should condition according to Table of IEC 61386-1; Flexible conduit is not applicable for this test. | Should be possible to pass the appropriate gauge. |
抗拉强度 | Not specified | Not specified | Subject to the tensile force in Table 6 of IEC 61386-1 at 23℃ | No damage visible to normal or corrected vision without magnification |
Suspended Load | Not specified | Not specified | Subject to suspended load in Table 7 and maintained at temperatures of Table 2 | No cracks visible to normal or corrected vision without magnification |
Understanding these differences ensures proper conduit selection based on region-specific requirements, enhancing performance and compliance with local regulations.
Selecting the right conduit type is crucial for ensuring reliable performance, safety, and compliance. When deciding between classifications such as light, medium, and heavy-duty conduits (both rigid and corrugated), it’s essential to consider several key factors.
If you need a more comprehensive guide to PVC conduit, including a buying guide, click here to read the ultimate guide to PVC conduit.
The type of conduit you choose should align with the specific load requirements of your project:
Light Duty: Ideal for indoor installations with low mechanical stress, such as residential wiring.
Medium Duty: Suited for moderate-stress applications like commercial and light industrial setups.
Heavy Duty: Required for high-impact scenarios, such as outdoor installations, underground cabling, and infrastructure projects.
Environmental factors such as temperature extremes, and moisture greatly influence the choice of conduit:
Rigid Conduits: Perform well in stable environments like underground or embedded walls.
Corrugated Conduits: Flexible options for dynamic setups, and tight bends.
Conduit diameter and wall thickness must match the cables and application scenario:
Light-duty conduits are thinner and lighter, suited for smaller cables and less demanding environments.
Medium and heavy-duty conduits feature greater wall thickness and are available in larger diameters to handle higher loads and more extensive cable installations.
Consider the mechanical properties of the conduit:
Compression and Impact Strength: Heavy-duty conduits are built to endure higher compression and impact forces compared to medium or light-duty types.
Thermal Resistance: Conduits should resist deformation or failure under high or low temperatures, especially in outdoor or industrial applications.
Ensure you’re using a compliant product and adherence to required standards such as AS/NZS 2053, IEC 61383, EN 61386.
Cost considerations are essential, especially for large-scale projects:
Light-duty conduits are more cost-effective but may require replacement sooner in demanding conditions.
Heavy-duty conduits are an investment, providing long-term durability and lower maintenance costs.
Projects like solar installations require conduits with specific features:
UV Resistance: For outdoor use.
Flexibility: Corrugated solar conduits work well in dynamic environments.
Temperature Tolerance: Important for renewable energy setups exposed to extreme weather.
Ledes offers a complete range of rigid and corrugated conduits that comply with AS/NZS 2053 standards, ensuring they meet the demands of various applications.
Types available:
HD/MD Rigid Conduit, MD Communication Rigid Conduit
HD/MD Corrugated Conduit, MD Communication Corrugated Conduit
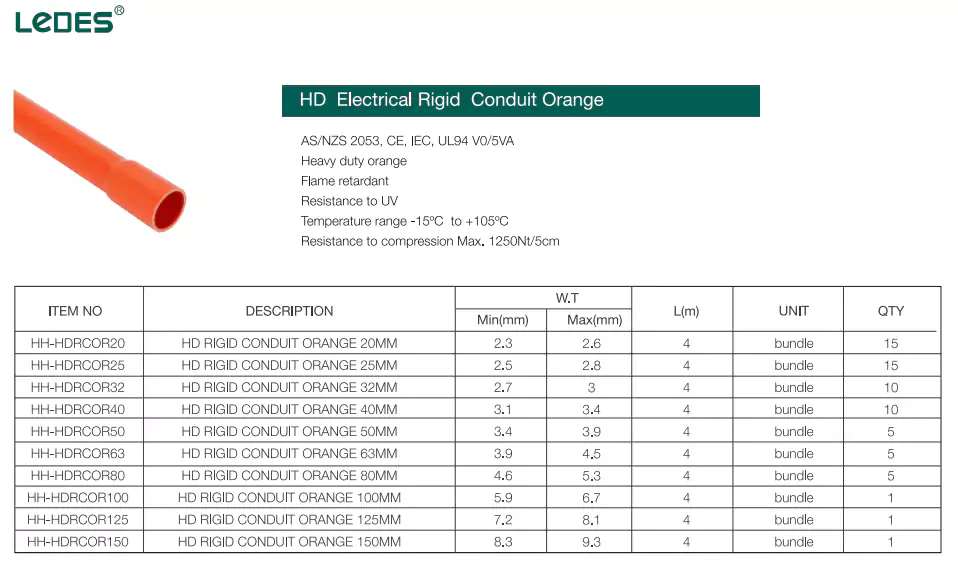
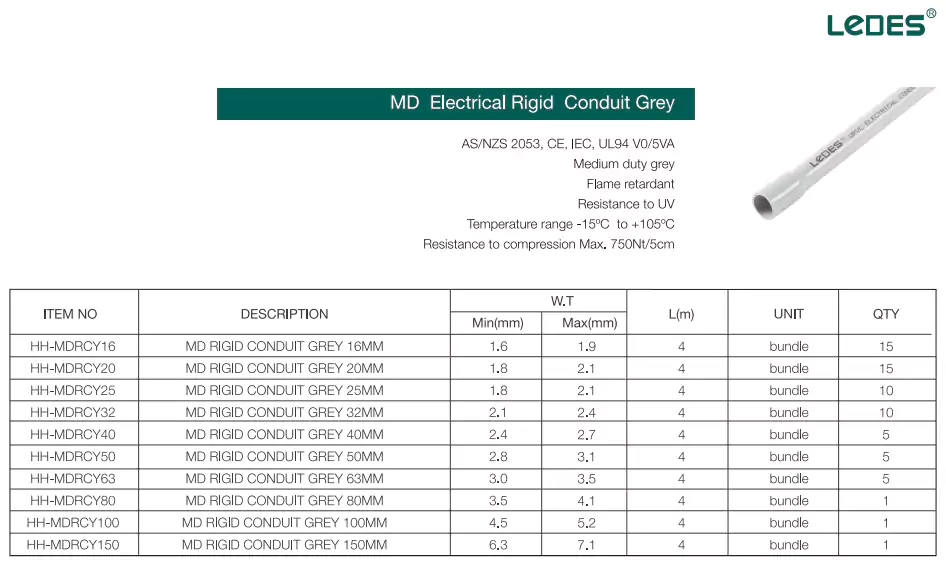
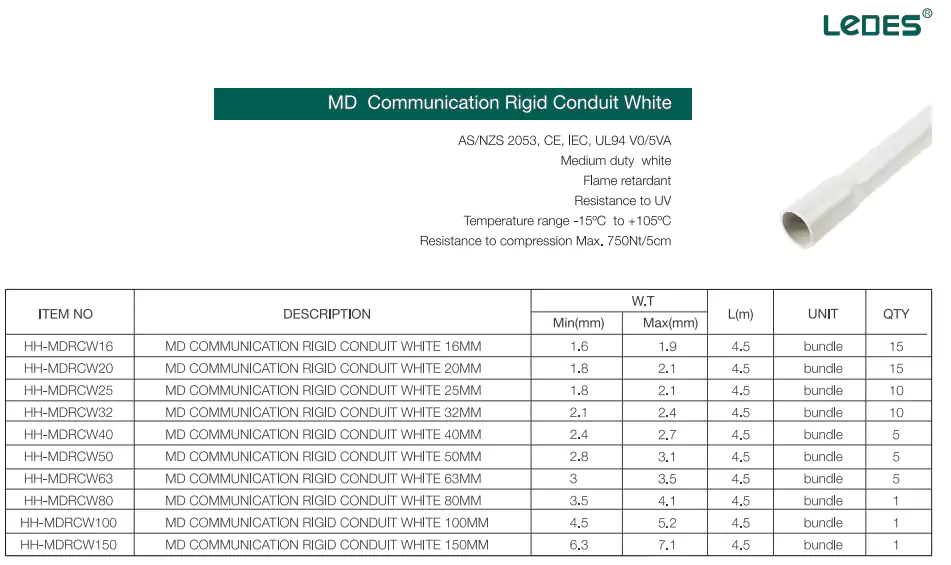
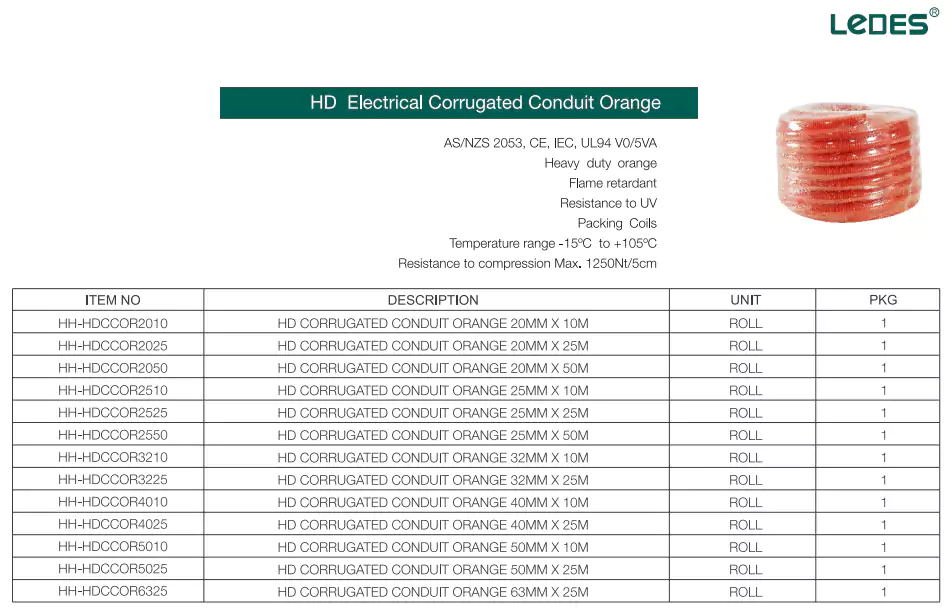
Ledes AS series conduits are designed for Australian and New Zealand market, they are stand out for their:
- Versatility: Available in light, medium, and heavy-duty classifications for both rigid and corrugated types.
- 耐用性: Engineered for high-impact resistance and long-lasting performance.
Beside the AS/NZS series conduit, Ledes provides solar conduits specially for Photovoltaic installations. They are also comply to AS/NZS 2053 standard, and meet IEC, CE standards. Their excellent UV resistant property make them a popular choice for many solar projects. Here are the specifications of Ledes Solar Conduit:
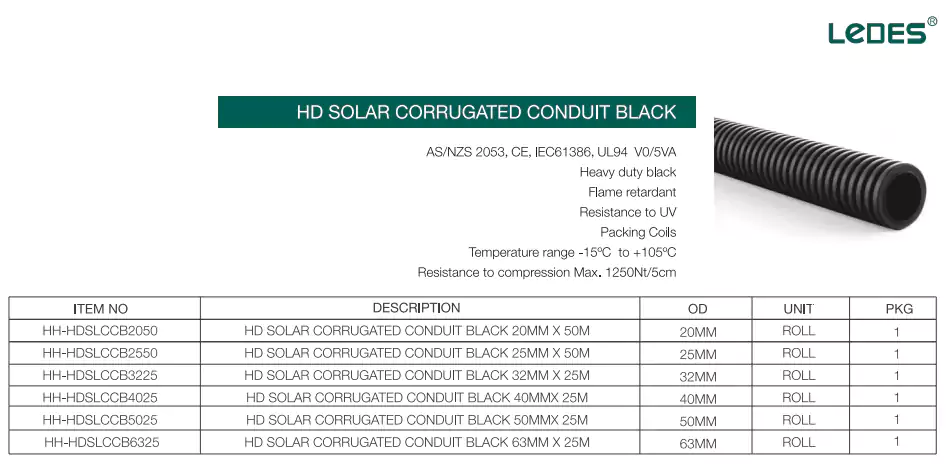
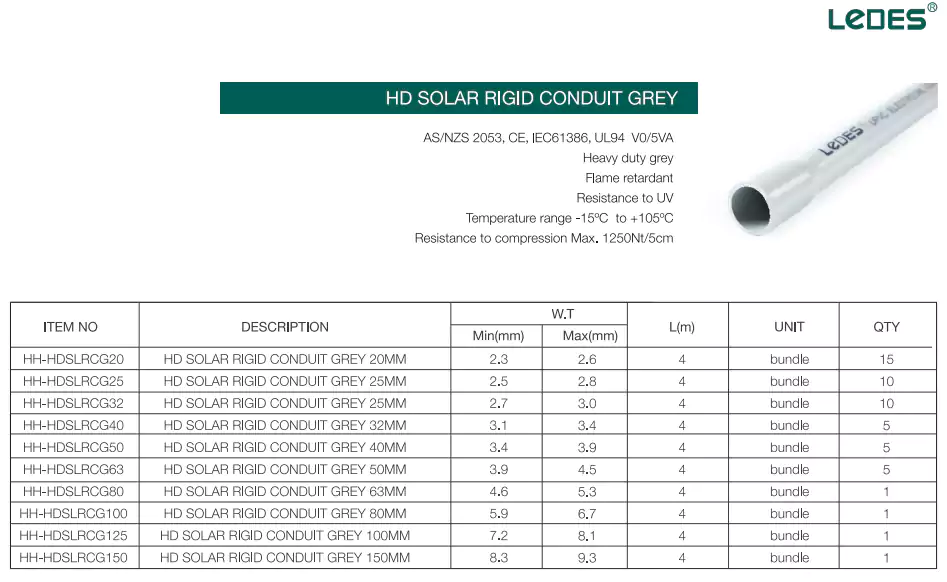
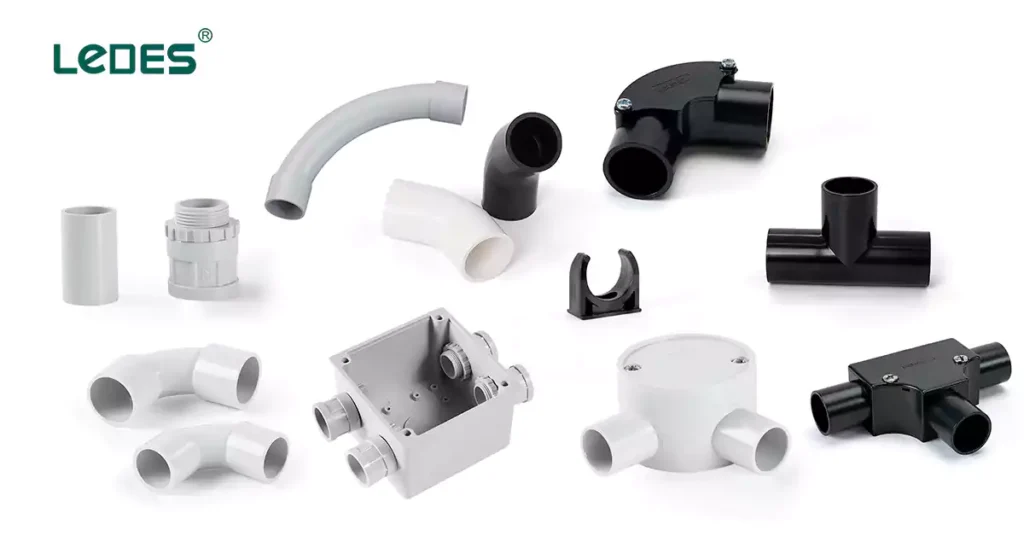
Conduit systems are incomplete without the right fittings, which ensure seamless connections, secure installations, and optimal performance. Fittings come in various shapes, sizes, and types, tailored to specific conduit applications. Here are some fittings that Ledes offers:
Sweep Bend: A long, smooth curve ideal for protecting cables from sharp bends.
Standard Bend: A general-purpose bend for standard applications.
Solid Elbow: A small, 90 degree elbow that offers robust connections in fixed-angle scenarios.
90-Degree Elbow: Designed for sharp turns at right angles, maintaining conduit integrity and cable protection.
45-Degree Elbow: Used for less acute angles, providing a smoother path for wiring.
Inspection Elbow: Includes a removable cover, allowing for easy access to cables for maintenance or inspection.
Coupling: Joins rigid conduits end-to-end for extended runs.
Plain-to-Screw Adapter: Converts plain-end conduits into threaded ones.
Corrugated-to-Screw Adapter: Links corrugated conduits to threaded connections, ensuring secure and flexible transitions.
可适应盒子: A versatile enclosure suitable for a variety of installations.
接线盒: Facilitates connections between multiple conduits, ensuring neat and safe cable management.
Standard Tee: Enables simple three-way connections.
Inspection Tee: Comes with a removable cover for easy cable access and maintenance.
U Clips: U clips are fasteners used to secure conduits to walls, ceilings, or other surfaces.
Solar Conduit Fittings
For solar conduit systems, fittings must withstand harsh outdoor conditions:
抗紫外线: Fittings like solar couplings, elbows, and adapters are treated for long-term exposure to sunlight.
Weatherproofing: Designed to endure temperature fluctuations, rain, and dust in renewable energy applications.
Ledes offers a comprehensive range of fittings designed for solar applications. These include:
- UV-resistant elbows, bends, and couplings.
- Solar-grade junction boxes and adaptable boxes for secure and durable connections.
- Terminal adapters and inspection fittings tailored for solar setups.
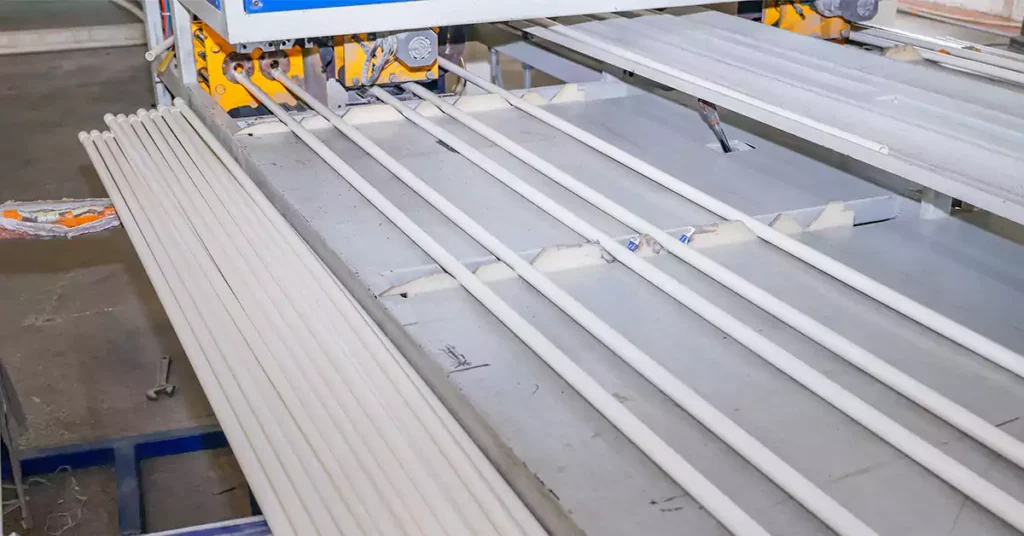
Are there any benefits to using black-colored PVC pipes?
Yes, black-colored PVC pipes offer several advantages:
抗紫外线: Black PVC pipes are often treated with additives like carbon black, making them highly resistant to UV radiation and suitable for outdoor applications.
耐用性: These pipes are more resistant to fading, cracking, and degradation caused by prolonged exposure to sunlight.
Aesthetic Appeal: Black-colored pipes are visually unobtrusive in certain settings, such as outdoor or landscaping applications.
What is the difference between PVC and LSZH conduit?
材质成分: PVC (Polyvinyl Chloride) conduits are made from a robust plastic material, whereas LSZH (Low Smoke Zero Halogen) conduits are formulated to emit minimal smoke and no harmful halogen gases during a fire.
应用: PVC conduits are widely used for general electrical installations, while LSZH conduits are ideal for enclosed or high-risk areas like data centers, transportation hubs, and tunnels.
Fire Safety: LSZH conduits are preferred where fire safety is critical, as they reduce toxic emissions and enhance visibility for evacuation during a fire.
What is the meaning of communication conduit?
Communication conduit refers to a protective pathway specifically designed to house and safeguard communication cables, such as fiber optic, telephone, or data cables.
应用: These conduits are used in telecom networks, internet infrastructure, and structured cabling systems.
标准: In regions like Australia, communication conduits comply with medium-duty or heavy-duty standards, typically marked white for identification.
Can you glue black PVC to white PVC?
Yes, you can glue black PVC to white PVC, provided they are of the same material type (e.g., both are PVC). To do so:
Use the Right Adhesive: PVC cement, specifically formulated for joining PVC materials, is recommended.
Surface Preparation: Ensure both surfaces are clean and dry before applying the adhesive.
Application: Apply primer and cement according to the manufacturer’s instructions for a secure bond.
Compatibility: Verify that the black PVC pipe is not a CPVC (Chlorinated PVC) pipe, as CPVC may require a different adhesive.
Choosing the right type of conduit is a critical decision that affects the safety, efficiency, and longevity of electrical and communication systems. This article has explored the differences between heavy-duty and medium-duty conduits, as well as the benefits of using PVC over metal alternatives. It also provided insights into important standards like AS/NZS 2053 and EN 61386, common fittings, and the factors to consider when selecting the most suitable conduit for your project.
Understanding the distinctions in material, application, and performance is essential for meeting specific installation requirements. Whether it’s for a residential, commercial, or solar project, ensuring compliance with industry standards is key to delivering high-quality and durable solutions.
Ledes provides a wide range of conduits for different applications, if you have any questions, contact us at any time.