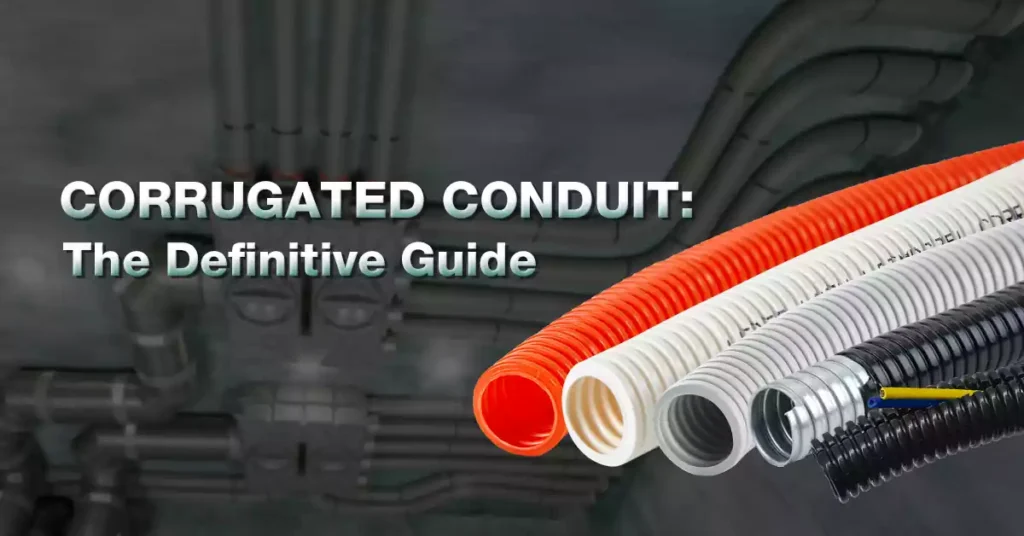
目录
In today’s fast-paced world of technology and infrastructure, the need for reliable, adaptable, and durable wiring solutions has never been greater. Enter 波纹管, a versatile and essential component in modern electrical and communication systems. Known for its unique ribbed design and flexibility, this type of flexible conduit plays a critical role in safeguarding cables while accommodating a wide range of applications.
From conduits in residential buildings, commercial buildings to communication conduits in telecommunications networks and electric vehicle (EV) conduits in the rapidly growing EV industry, corrugated conduit has become a go-to solution for projects requiring robust yet flexible wiring protection. It is commonly used in electrical systems, underground cabling, and industrial automation, where it protects wires from environmental hazards, physical damage, and even electromagnetic interference.
Corrugated conduit isn’t just for traditional electrical installations. Its role in EV charging stations, smart grid infrastructure, and fiber-optic data networks underscores its adaptability to cutting-edge technologies and emerging industries. Whether you’re an engineer, contractor, or DIY enthusiast, understanding this versatile tubing is crucial for making informed choices in your projects.
In this guide, we’ll explore everything you need to know about corrugated conduit, from its fundamental characteristics and various applications to tips for selecting and installing the right type. By the end, you’ll have a comprehensive understanding of this indispensable tool and its pivotal role in today’s electrical and communication landscapes.
Definition and Purposes of Corrugated Conduit
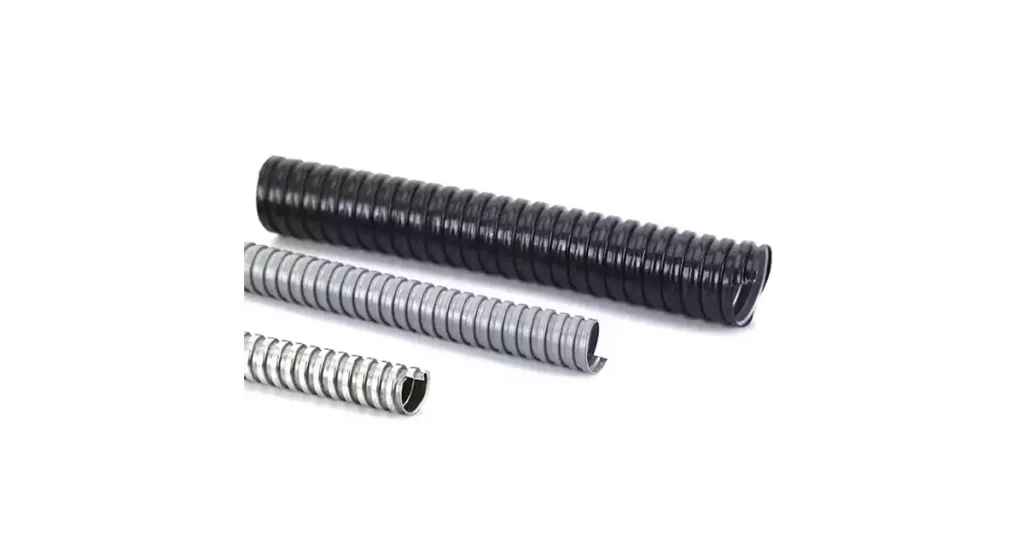
What is Corrugated Conduit?
Corrugated conduit, also referred to as flexible conduit or flexible tubing, is a specially designed protective tubing with a ribbed, corrugated exterior that enhances flexibility and strength. Typically made from materials such as PVC (polyvinyl chloride), HDPE (high-density polyethylene), or even metals like aluminum and stainless steel, this conduit type offers a balance of adaptability and durability.
The ribbed structure allows the conduit to bend and flex without compromising its integrity, making it ideal for routing through tight or irregular spaces. Additionally, corrugated conduit is available in metallic and non-metallic options to suit a variety of applications and environments.
Primary Purposes and Uses
Corrugated conduits are essential in protecting wires and cables from physical damage, moisture, and environmental hazards while maintaining the flexibility needed for complex installations. Below are the key purposes and uses of this conduit type:
Cable Protection: Shields wires and cables from physical impacts, vibrations, and environmental conditions such as UV exposure, water ingress, and chemical corrosion.
Flexibility for Complex Routing: Ideal for installations requiring bending or navigating through confined spaces without the need for multiple fittings or joints.
Environmental Safety: Ensures that electrical and communication systems remain insulated and safe, reducing risks of electrical shocks or short circuits.
Ease of Maintenance and Upgrades: Simplifies cable replacements or upgrades, as the conduit allows easy access to internal wires without damaging surrounding infrastructure.
Key Characteristics of Corrugated Conduit
Corrugated conduit is known for its unique combination of flexibility, durability, and protection, making it a versatile solution for various electrical applications. The most distinctive feature of corrugated conduit is its ribbed design, which provides excellent mechanical protection against impacts, abrasion, and external pressures. This ribbing enhances its ability to resist crushing and other forms of damage, ensuring long-term performance in challenging environments.
One of the standout features of corrugated conduit is its flexibility, which allows for easy installation in tight or confined spaces, around corners, or across uneven surfaces. This flexibility also reduces the need for additional fittings, making installation faster and more cost-effective. The lightweight nature of corrugated conduit further reduces installation effort and labor costs, making it an ideal choice for large-scale projects.
In addition to these basic material advantages, some variants of corrugated conduit include flame-retardant 或者 fire-resistant properties, further enhancing safety, particularly in environments where fire hazards are a concern. These fire-resistant versions can help prevent the spread of fire, providing an extra layer of protection in industrial or commercial settings.
Corrugated conduit is also available in various sizes and colors, which allows for customization based on the specific requirements of the project. Its versatility across industries—from construction and automotive to telecommunications and manufacturing—demonstrates its broad application range and essential role in electrical wiring protection.
Types of Corrugated Conduits
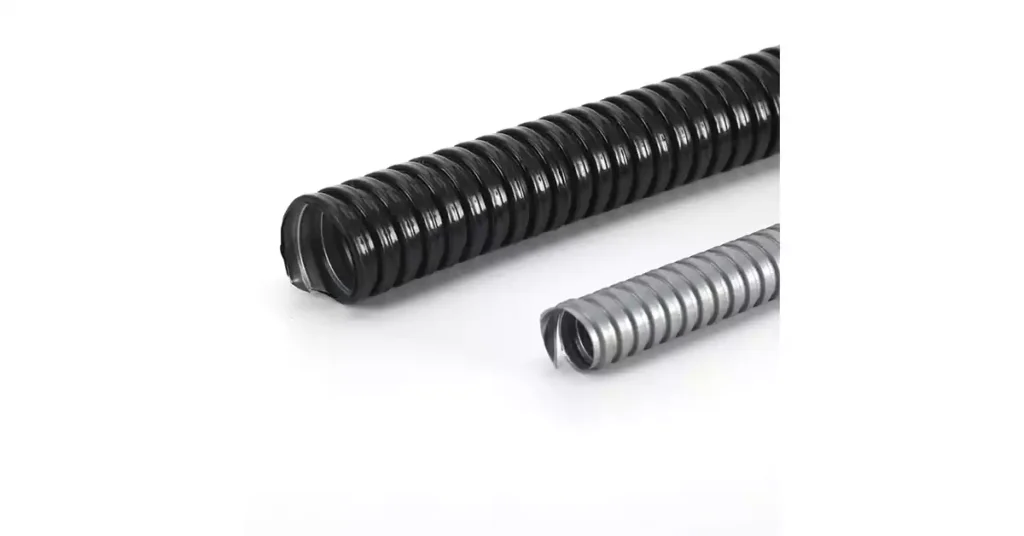
Corrugated conduits are available in various types, categorized based on design purpose, materials, and application scenarios. Each type caters to specific installation requirements, ensuring optimal performance and protection for wiring systems.
1. Types by Design Purpose
- Standard Corrugated Conduit
Standard corrugated conduit is the most common type, designed to provide basic protection for cables and wiring. It is highly flexible, lightweight, and suitable for general-purpose applications such as residential wiring, commercial installations, and light industrial use. - Super-Flex Corrugated Conduit
Super-Flex corrugated conduit features an enhanced ribbed design for greater flexibility and bend radius. This type is ideal for installations with complex routing requirements, such as automotive wiring, robotics, and tight spaces. - Split Corrugated Conduit
Split corrugated conduit is designed for quick and easy installation, allowing cables to be inserted without the need to pull them through. The split design makes it convenient for retrofitting or replacing cables in existing systems, commonly used in automotive repairs, data center retrofits, and temporary wiring setups.
2. Types by Materials
- PVC波纹管
PVC corrugated conduit is lightweight, cost-effective, and highly resistant to moisture and chemicals. It is widely used in residential and commercial installations where durability and affordability are key considerations. - HDPE Corrugated Conduit
HDPE (High-Density Polyethylene) corrugated conduit offers superior flexibility and impact resistance. Its robustness makes it suitable for underground installations, outdoor wiring, and harsh environments. - Polypropylene (PP) Corrugated Conduit
PP corrugated conduit provides excellent resistance to high temperatures and chemicals, making it suitable for automotive and industrial applications where heat exposure is a concern. - Polyurethane (PU) Corrugated Conduit
PU conduits offer exceptional flexibility, abrasion resistance, and durability, making them suitable for applications requiring frequent movement or exposure to vibration, such as robotics and machinery. - Polyamide / Nylon Corrugated Conduit
Polyamide (Nylon) conduits are extremely durable, offering high resistance to wear, chemicals, and UV exposure. They are often used in demanding applications like automotive wiring, heavy machinery, and outdoor installations. - Metallic Corrugated Conduit
Made from steel or aluminum, metallic conduits are prized for their strength and electromagnetic interference (EMI) shielding capabilities. They are used in industrial settings where robust mechanical protection is essential. - Low Smoke Halogen-Free (LSZH) Corrugated Conduit
LSZH 导管 minimize toxic gas emissions and smoke during a fire, ensuring safety in enclosed spaces like data centers, hospitals, and transportation systems.
3. Types by Application Scenarios
- Light-Duty Corrugated Conduit
Light-duty conduits are intended for environments with minimal mechanical stress, such as indoor residential wiring or cable management in offices. - Medium-Duty Corrugated Conduit
Medium-duty conduits offer a balance between strength and flexibility, making them suitable for commercial and light industrial uses. These conduits are commonly used where moderate environmental and mechanical protection is required. - Heavy-Duty Corrugated Conduit
Heavy-duty conduits are built for maximum durability, providing excellent resistance to environmental stress, impacts, and mechanical forces. These are ideal for outdoor installations, electric vehicle wiring, photovoltaic systems, and other demanding applications.
Tips: To learn the differences between the two, read our last post, ‘Medium Duty Vs. Heavy Duty Conduit.’
Applications and Features of Corrugated Conduits
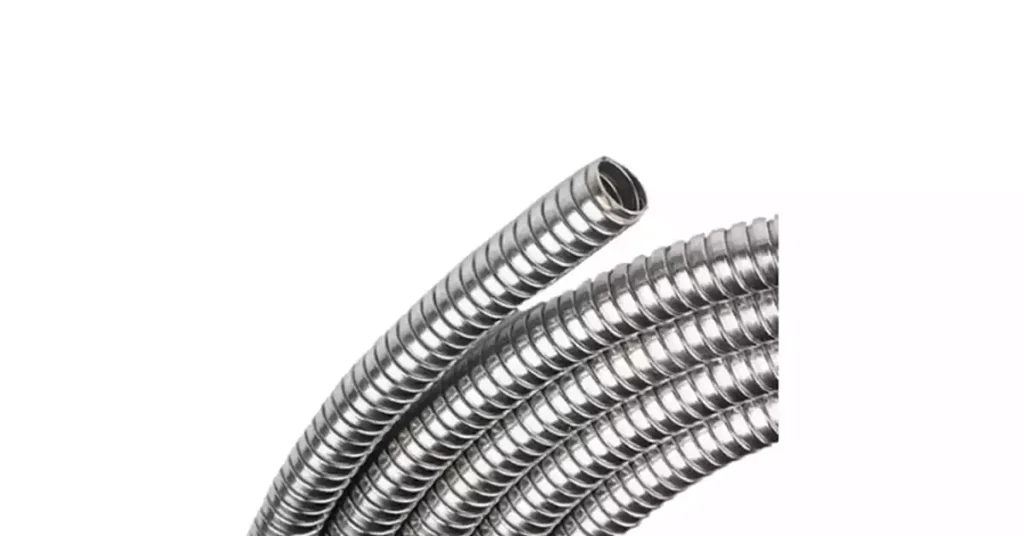
Corrugated conduits are a versatile and essential component in modern electrical and communication installations. Their unique design and material properties make them suitable for a wide range of applications, from residential projects to large-scale industrial setups. This section delves into the features and characteristics of corrugated conduits, integrating key certifications like UL 1653, CSA C22.2 NO.227.1, AS/NZS 2053.5, and IEC 61386-23 to highlight their compliance with industry standards. It also explores the main tests these standards require and introduces critical application scenarios.
Flexibility and Versatility
One of the defining features of corrugated conduits is their exceptional flexibility. Thanks to their ribbed design, these conduits can bend around tight corners, navigate narrow spaces, and accommodate uneven surfaces with ease. This adaptability is vital in environments requiring intricate cable routing, such as:
Automotive Systems: Where conduits must fit within complex engine compartments.
Industrial Machinery: Ensuring seamless cable management in tight spaces.
住宅布线: Simplifying installations behind walls or ceilings.
The spiral or ribbed structure enhances bendability while maintaining durability, making them ideal for applications involving frequent movement or vibration. For instance, Ledes Flexible PVC Pipe Electrical Corrugated Conduit ensures smooth bending and consistent cable integrity.
Durability and Environmental Resistance
Corrugated conduits are engineered to endure harsh conditions. Materials like PVC, polyethylene, and nylon offer resilience against:
UV Radiation: Essential for outdoor installations.
Moisture and Chemicals: Making them ideal for underground wiring and industrial environments.
Temperature Extremes: Allowing use in areas ranging from freezing winters to high-heat machinery.
Standards such as AS/NZS 2053.5 and UL 1653 confirm these conduits’ durability and safety under various environmental stresses. Products like Ledes PVC Corrugated Conduit offer durability in extreme temperatures and outdoor conditions, meeting stringent standards such as UL 1653 for resistance to physical damage and environmental degradation
Fire Safety and Flame Retardancy
Fire resistance is a critical consideration in many applications, and corrugated conduits often feature flame-retardant materials to minimize fire hazards. Low Smoke Zero Halogen (LSZH) variants further reduce toxic smoke emissions, making them indispensable for:
Hospitals and Schools: Where occupant safety is paramount.
Public Transport Systems: Subway and bus wiring installations.
Ledes electrical nonmetallic tubing and corrugated conduits comply with CSA C22.2 No.227.1 and IEC 61383 standards that include flammability tests, ensure conduits resist ignition and limit flame spread, providing enhanced safety in fire-prone environments.
Some Specific Application Scenarios
Communication Wiring
Corrugated conduits are commonly used to protect delicate fiber-optic and communication cables. Their flexibility and ability to shield against environmental damage ensure reliable data transmission in telecommunication networks.
Electric Vehicle Charging Station
The dynamic nature of EV charging systems demands conduits that can withstand frequent bending, weather exposure, and potential chemical spills. Corrugated conduits designed for EV applications meet stringent mechanical and thermal tests under standards like UL 1653, ensuring long-lasting performance.
Construction and Infrastructure
Lightweight and easy to install, corrugated conduits are widely used in building wiring systems. Their ability to protect cables against physical damage, UV exposure, and fire hazards makes them an ideal choice for both residential and commercial construction projects.
Industrial Systems
In factories and warehouses, corrugated conduits organize and protect wiring from vibrations, chemicals, and mechanical impacts. Compliance with impact and crush resistance tests, ensure they perform reliably in demanding environments.
Local Codes for Corrugated Flexible Conduits
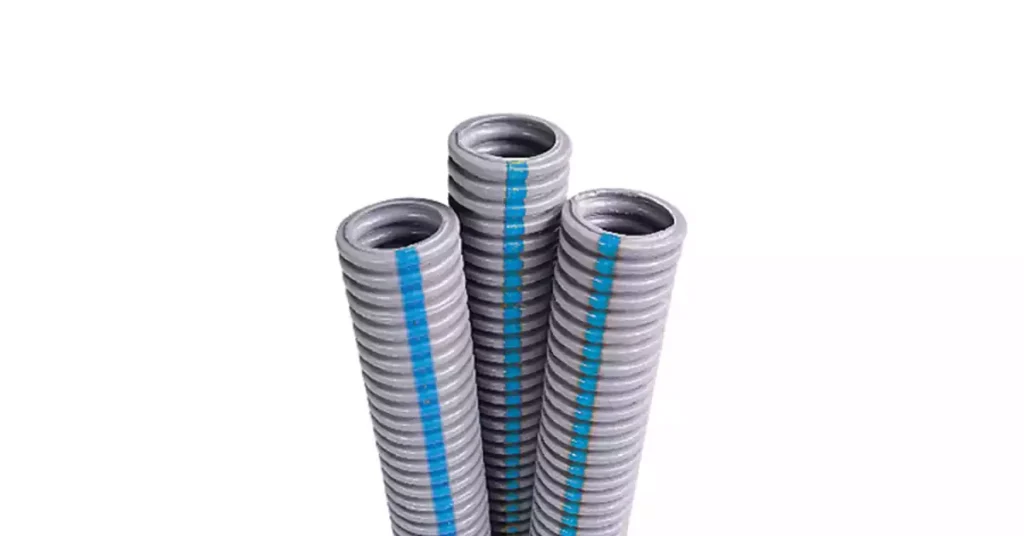
Corrugated conduits, like any other electrical installation material, must adhere to local codes and standards to ensure safety, performance, and compliance. These codes are essential in defining the technical specifications, installation practices, and safety measures that conduits must meet for various applications. In this section, we will cover some of the common codes governing the use of corrugated and flexible conduits, and how they impact their application in real-world projects.
NEC (National Electrical Code) – USA
In the United States, the National Electrical Code (NEC) sets the standard for electrical installations, including the use of flexible conduits. Section 352 of the NEC covers Rigid Nonmetallic Conduit (which includes PVC and corrugated variants). It specifies how these materials should be used for electrical wiring, their physical properties, and installation requirements.
The NEC Article 348 also governs flexible metal conduits (FMC), ensuring that flexible conduits used in electrical installations meet durability, safety, and grounding standards.
UL (Underwriters Laboratories) – USA
UL 1653 is the standard that applies specifically to flexible plastic conduit. It details the fire resistance, environmental suitability, and performance tests that flexible and corrugated conduits must undergo to ensure safe use in various settings. For example, UL 1653 focuses on resistance to abrasion, chemicals, and exposure to heat, ensuring the conduit is safe for its intended electrical protection role.
CSA (Canadian Standards Association) – Canada
In Canada, the CSA C22.2 NO.227.1 standard governs flexible non-metallic conduit systems. This standard addresses the materials, construction, and performance of corrugated conduit for use in various applications, with a particular focus on environmental resistance, fire performance, and mechanical durability.
CSA standards are recognized across Canada and are designed to align closely with global requirements for safety and performance.
AS/NZS (Australia/New Zealand) – Australia and New Zealand
The AS/NZS 2053.5 standard outlines the use of non-metallic flexible conduit in Australia and New Zealand. This includes guidelines for the design, construction, and installation of flexible and corrugated conduits for residential, commercial, and industrial applications. The standard ensures that materials are suitable for the local climate conditions, such as extreme temperatures and UV exposure, and comply with safety regulations.
IEC (International Electrotechnical Commission) – International
The IEC 61386-23 standard is widely recognized internationally and governs the use of flexible and corrugated plastic conduit systems. It sets out the performance and testing criteria for corrugated conduits, including their resistance to impact, flame spread, and environmental factors. This standard ensures that the conduit is suitable for global use in industrial, commercial, and residential applications.
When selecting corrugated conduit for any electrical installation, it is crucial to ensure that it complies with the relevant local codes and standards. This includes not only the physical properties of the conduit but also the installation practices and safety measures associated with it.
By adhering to these standards, you ensure that the conduit is suitable for its intended use, whether it’s routing cables for power distribution in buildings or protecting communication lines in an outdoor environment.
电气非金属管 (ENT)
ENT (Electrical Nonmetallic Tubing) is a widely used flexible conduit types in American and Canadian markets, it is a flexible, lightweight conduit used for protecting and routing electrical wiring in both residential and commercial applications. Made from durable thermoplastic materials, ENT offers excellent resistance to moisture, corrosion, and physical damage, making it an ideal solution for environments where flexibility and protection are paramount. ENT is widely used in drywall, concrete, and areas with tight spaces, where it can be easily bent and installed without requiring special tools.
One of ENT’s key advantages is its nonmetallic construction, which helps prevent electrical conductivity and reduces the risk of short circuits, making it a safe choice for a variety of electrical systems. Additionally, it is designed to be compatible with a wide range of fittings and accessories, providing flexibility in installations. ENT also offers compliance with relevant UL (Underwriters Laboratories), NEC (National Electrical Code) standards, CSA (Canadian Standards Association) and CEC (Canadian Electrical Code) ensuring its reliability and safety for electrical wiring systems.
Color Code of Corrugated Conduits
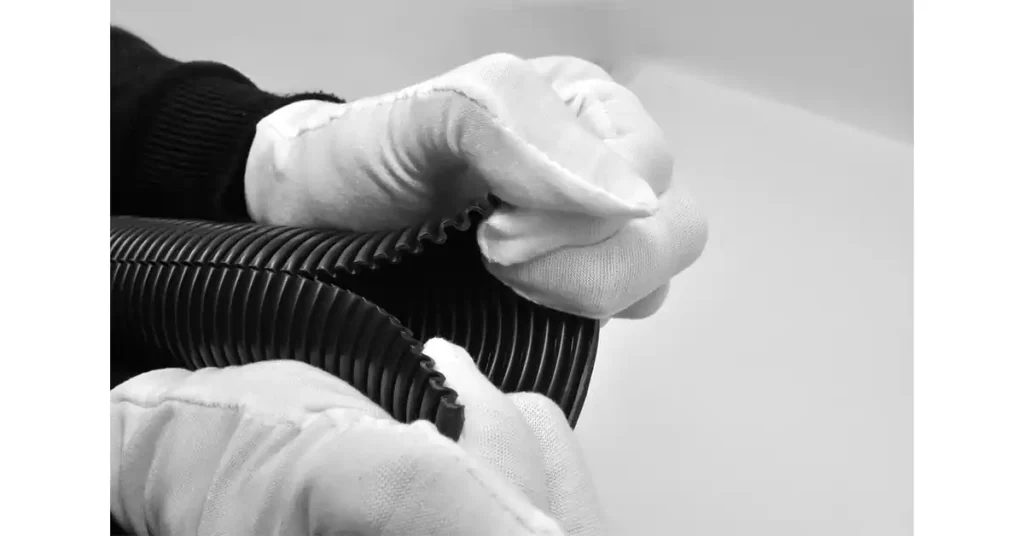
The color coding of corrugated or flexible conduits is an essential aspect of electrical system design, providing visual identification of the conduit’s purpose and simplifying maintenance, troubleshooting, and compliance with safety standards. While the specific color code can vary by region, industry, or application, certain general practices are commonly adopted worldwide to standardize conduit identification and ensure system safety.
The National Electrical Code (NEC) and other international standards, such as those set by IEC (International Electrotechnical Commission), may provide guidance on color coding, although local regulations and specific industry needs can sometimes influence these practices. Many electrical organizations suggest using a system where the color of the conduit indicates its function, voltage level, or application type.
Common Color Code Practices
Black: Typically used for general electrical wiring and low-voltage applications. It is one of the most common colors for flexible conduits used in residential, commercial, and industrial settings.
Gray: Often used for nonmetallic, indoor applications, particularly in residential buildings for wiring and lighting systems. It can also be used in environments where flexibility is needed, such as in electrical raceways.
Yellow: Frequently used for conduit carrying high-voltage cables. It is a color that indicates caution, serving as a warning of potentially hazardous conditions, which is why it is used for high-power applications, including industrial machinery and some commercial installations.
Orange: High Voltage or Specialized Applications: Orange is often used to identify high-voltage circuits or specific types of cables, particularly in industrial settings. It serves as a warning color similar to yellow but is often used to indicate circuits that require special attention, such as emergency power systems, lighting control circuits, or circuits subject to unique regulatory requirements. Data and Communication Cables: In some cases, orange can be used for data cables or telecommunication conduits, signaling that the conduit contains critical or specialized wiring.
Red: Commonly used to identify circuits with specific functions, such as emergency circuits or fire alarm systems. It may also be used for high-voltage wiring to distinguish it from other circuits.
Blue: Often used for low-voltage circuits or communication cables, such as those for networking, telecommunication, or control systems.
Green/Green with Yellow Stripes: This color is typically reserved for grounding or earthing conductors. It signifies safety and helps workers easily identify ground wires in electrical systems.
White: Commonly used for neutral conductors, typically in standard electrical systems. White color-coded conduits help to ensure that neutral wires are easily distinguishable from live or ground wires.
尖端: To learn the color code information, read our last post, ‘The Guide of Color Code of PVC Conduit.’
Applications of Color-Coded Conduits
Color-coded conduits are essential in various applications to ensure electrical safety and system organization. Some of the key uses include:
Identification and Traceability: Helps workers identify specific circuits quickly, especially in complex or large installations, reducing errors and improving safety.
Compliance: Ensures compliance with local electrical codes, helping to meet legal requirements for safety and standards in different regions.
Maintenance and Troubleshooting: Simplifies maintenance and repairs by making it easy to trace wires and understand their function based on their color-coded conduit.
Best Practices for Implementation
Standardization: Ensure consistent use of the color code across the entire project. Standardizing colors according to the industry or local codes will ensure everyone working on the system can easily understand the wiring setup.
Clear Labeling: Along with color coding, labels should be added at key points to further clarify the function of the wiring and conduit.
Training and Awareness: Electrical contractors, maintenance workers, and other personnel should be educated on the importance of color coding and how to identify different conduit types to minimize errors.
Corrugated Conduits: Pros and Cons
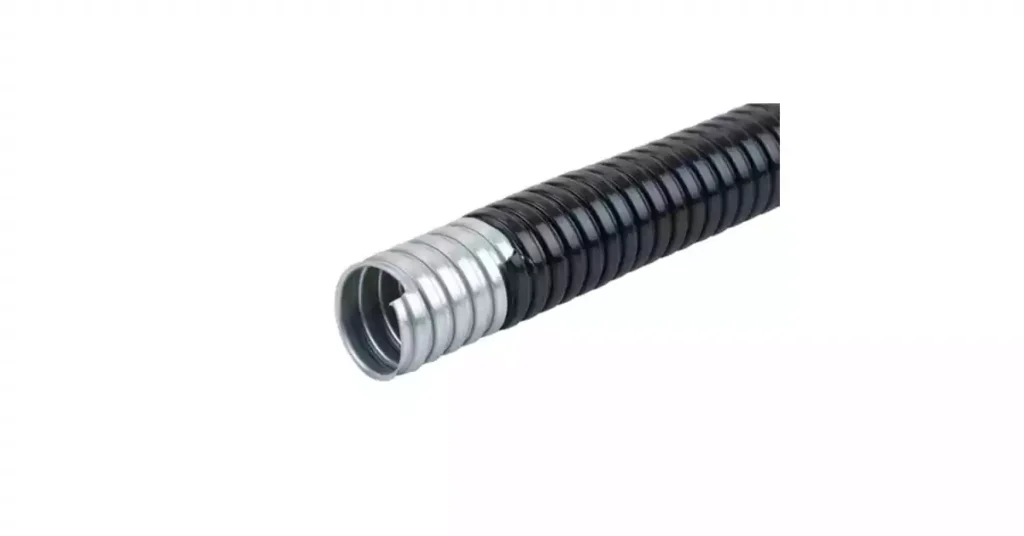
Pros of Corrugated Conduits
成本效益
Corrugated conduits provide an affordable solution for protecting electrical wiring. Their lightweight design helps reduce transportation costs, while their flexibility minimizes the need for additional fittings during installation. This cost-effectiveness is particularly beneficial for large-scale projects, such as residential or industrial installations, where materials and labor costs can quickly add up. As industry experts note, “Corrugated conduit provides robust protection at a fraction of the cost of rigid metal conduits.”
Versatility Across Industries
Corrugated conduit is highly versatile, suitable for use in various industries, including construction, automotive, industrial, and even DIY projects. Its flexibility and durability make it adaptable to both static and dynamic environments. For example, split corrugated conduit is commonly used in automotive applications to protect wiring harnesses from abrasion and damage, especially in tight spaces under the hood. This adaptability ensures that corrugated conduit can handle a wide range of applications, from protecting electrical wiring in buildings to shielding cables in industrial machines.
Protection Against Environmental Hazards
One of the key advantages of corrugated conduit is its ability to provide protection against environmental hazards. Corrugated conduits made from materials such as PVC and polyethylene offer resistance to moisture, UV rays, and chemicals, ensuring long-lasting performance in both outdoor and underground installations. For instance, PVC corrugated conduits are particularly effective in underground wiring because of their resistance to corrosion. This protection ensures that your electrical systems remain safe and functional even in challenging environments, such as in areas exposed to harsh weather conditions or underground installations prone to water and chemical exposure.
Simplified Installation Process
The ribbed and flexible design of corrugated conduit simplifies the installation process. The conduit can be easily routed through tight spaces, around corners, or over uneven surfaces without the need for additional tools or fittings. This ease of use can save both time and labor, making corrugated conduits a practical choice for both professionals and DIY enthusiasts. Additionally, materials like nylon-based corrugated conduits are not only durable but also lightweight, further reducing installation effort and time. The ease of installation also helps minimize the risk of errors during setup, making it an efficient solution for quick projects.
Cons of Corrugated Conduits
Lower Mechanical Strength than Rigid Metal Conduits
While corrugated conduits are durable, they do not offer the same level of mechanical strength as rigid metal conduits like RMC or IMC (intermediate metal conduit). In high-traffic areas or environments where there is a higher risk of physical damage, corrugated conduits may not provide the same level of protection against external forces.
Limited Fire Resistance
Most corrugated conduits made from plastic materials have limited fire resistance compared to metal conduits. While some types of corrugated PVC conduits are flame-retardant, they may not meet the higher fire resistance standards required for certain high-risk environments, such as commercial kitchens or industrial plants.
Not Suitable for Extreme Temperatures
Corrugated conduits made from standard plastic materials can become brittle or lose their flexibility in extremely low temperatures, and they may deform or degrade in very high-temperature environments. Special high-temperature rated corrugated conduits are available, but they can be more expensive and less widely used.
How to Choose the Right Corrugated Conduit
There are 6 tips to choose the right corrugated conduit,
Assessing Your Specific Needs
The first step in choosing the right corrugated conduit is to thoroughly assess the specific needs of your project. Different environments and applications require different features, and understanding these requirements will help you narrow down the best options.
- Project Environment Start by considering the environment in which the conduit will be installed. Are you working in a residential, industrial, or outdoor setting? Each scenario comes with distinct challenges and requirements for the conduit:
- Residential settings: Projects here often prioritize ease of installation, cost-effectiveness, and aesthetic appeal. Corrugated conduits in residential environments are typically installed in walls, ceilings, and floors, where flexibility and the ability to maneuver around obstacles are important.
- Industrial environments: In industrial applications, the conduit must offer high durability, resistance to chemicals, and the ability to withstand harsh conditions such as exposure to extreme temperatures, heavy physical impacts, and corrosive substances.
- Outdoor installations: Outdoor projects require conduits with high UV resistance to prevent degradation from prolonged exposure to sunlight, as well as robust protection against environmental elements such as rain and snow.
Type of Cables to Be Protected
The type of cables that need to be protected will significantly influence your conduit choice. For example, power cables, communication cables, or data cables all have specific requirements. If you expect frequent access to the wiring, split corrugated conduit might be a good option. This type of conduit allows easy opening and closing without removing the entire run, making it an ideal choice for applications where cables need to be regularly accessed, maintained, or replaced. Split conduits are particularly beneficial in scenarios where flexibility and ease of maintenance are key considerations.
Size and Length of the Conduit
Proper sizing is critical when choosing corrugated conduit. To ensure the conduit is both functional and safe, you must consider the diameter of the cables and ensure that the conduit offers enough space for proper routing. Overcrowding cables can lead to overheating, damage, or failure of the electrical system. Adequate space allows for heat dissipation and reduces the risk of damage from physical stress on the cables.
Measure the cable diameter, then choose a conduit size that offers a little extra room to ensure the cable can move freely within the conduit without being squeezed or constricted. Additionally, determine the length of the conduit required for the installation. Make sure the conduit is long enough to cover the entire length of the wiring run without unnecessary excess that could lead to waste.
Conduit Material and Durability
The material of the corrugated conduit plays a key role in its performance. Most corrugated conduits are made from either PVC, polyethylene, or other durable thermoplastics, each with its own set of characteristics:
PVC corrugated conduits are known for their chemical resistance, flexibility, and affordability, making them a popular choice for residential and commercial applications.
Polyethylene or other high-performance materials might be required for installations in environments exposed to high-impact conditions, UV radiation, or extreme temperatures. For outdoor or underground installations, polyethylene is often preferred for its durability and resistance to environmental elements.
Compliance with Standards and Codes
Ensure the corrugated conduit you choose meets the necessary local, national, or international standards and codes. For example, in the U.S., the National Electrical Code (NEC) provides guidelines for conduit usage, including material specifications, installation methods, and fire resistance ratings. Compliance with these standards ensures the safety, reliability, and long-term performance of the conduit system.
Budget Considerations
Finally, assess your budget for the project. While corrugated conduits are often more affordable than rigid metal alternatives, prices can vary based on the material, size, and specialized features like UV resistance or chemical resistance. For cost-sensitive projects, ensure that the chosen conduit offers the necessary features without exceeding budget constraints.
How to Choose a Corrugated Conduit Supplier
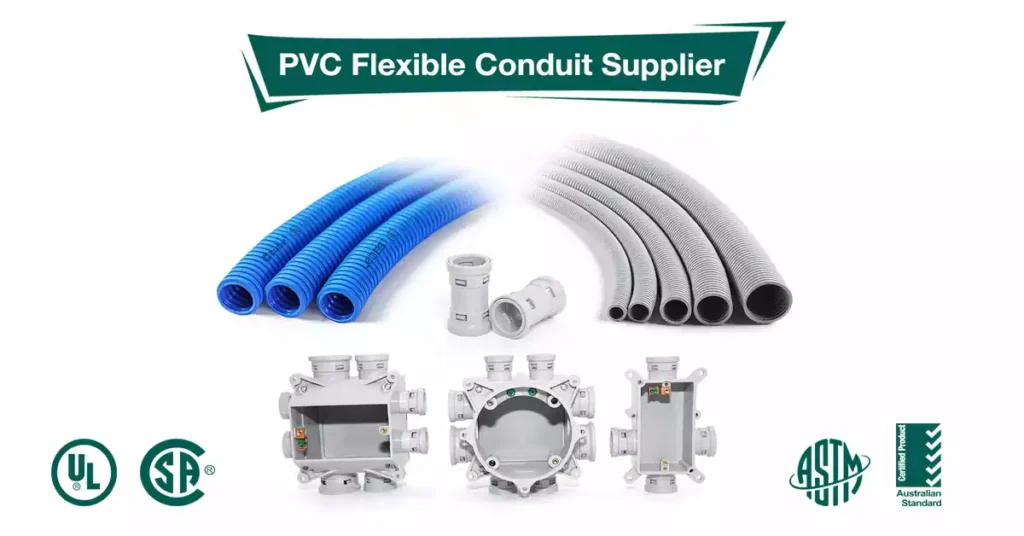
Selecting the right supplier for your corrugated conduit needs is crucial to ensure the quality, performance, and timely delivery of your products. The right supplier can significantly impact the success of your project, whether it’s a residential, industrial, or large-scale commercial installation. Here are key factors to consider when choosing a corrugated conduit supplier:
1. Quality and Compliance with Industry Standards
The first and most important consideration when choosing a supplier is the quality of the corrugated conduit they provide. Look for suppliers who offer products that meet or exceed industry standards. Suppliers should provide product documentation or test reports to verify compliance with these standards. Quality assurance ensures that the conduit will perform reliably in its intended application, providing long-lasting protection for cables and wiring systems.
2. Material Options and Customization
Different projects require different materials based on environmental conditions, mechanical stress, and flexibility needs. A reliable supplier should offer a variety of materials such as:
PVC: Commonly used for general residential and commercial applications due to its affordability and chemical resistance.
Polyethylene: Ideal for outdoor and underground installations due to its durability and UV resistance.
Nylon: Offers superior mechanical strength and wear resistance for industrial applications.
Additionally, a supplier who provides customized solutions—such as specific colors, sizes, or split corrugated conduit—can help tailor the conduit to your project’s needs, ensuring optimal performance and a more efficient installation.
3. Product Range and Availability
A reputable supplier should offer a wide range of conduit products that cater to various industries and installation requirements. Make sure they carry different types of corrugated conduit, including:
Standard corrugated conduit for general-purpose use.
Flexible conduit for applications where flexibility is key.
Split corrugated conduit for easy access to cables.
Heavy-duty corrugated conduit for high-stress environments.
Check if the supplier can fulfill large orders or provide stock consistently to meet your timeline. Timely availability of products is essential to avoid delays in your project, so suppliers who maintain a well-stocked inventory or have fast lead times should be a priority.
4. Customer Service and Technical Support
A good supplier is not only a vendor but a partner in your project’s success. They should offer excellent customer service and technical support to help you make informed decisions. Look for suppliers who:
Have knowledgeable staff who can provide technical advice on selecting the best conduit based on your project’s requirements.
Offer installation guidance or recommendations on best practices.
Are responsive to inquiries and capable of handling post-purchase support or issues.
Technical support can be especially helpful if you’re working on specialized or complex installations, and having a supplier that you can rely on for advice can prevent costly mistakes.
How to Install Corrugated Conduits?
Materials and Tools Needed:
Corrugated conduit (rigid or flexible)
Conduit fittings (couplings, elbows, adapters)
Conduit straps/clamps
Pipe cutters or saw (for rigid conduit)
Electrical tape or conduit tape (if needed)
Measuring tape
Drill (if mounting to a wall or ceiling)
Screwdriver
Installation Steps:
- Plan the Route:
Identify the path where the conduit will be installed, considering factors like the length, obstacles, and bends. Ensure you account for the size of the conduit to avoid interference with other systems.
- Measure and Cut:
Measure the required length of the conduit. Use a pipe cutter or saw to cut the conduit to size. If using flexible corrugated conduit, you can use scissors or a sharp knife for cutting.
- Install Conduit Straps:
Secure the conduit along the desired path using conduit straps or clamps. These should be placed at regular intervals, typically every 3-4 feet for rigid conduit and about 18 inches for flexible conduit.
Ensure the conduit is properly supported to prevent sagging or damage.
- Bend the Conduit:
If necessary, bend the conduit to follow the desired path. Flexible corrugated conduit is easier to bend manually, while rigid types might need elbow fittings or other connectors for sharp turns.
- Join Sections:
Connect sections of conduit using couplings or adapters. If necessary, use fittings like 90-degree bends, tees, or elbows to change the direction of the conduit.
Ensure all connections are secure and properly aligned.
- Seal and Protect:
Depending on the installation, seal the ends of the conduit to protect the wiring from dust, water, or other environmental factors.
For outdoor installations, make sure the conduit is properly sealed to prevent water ingress.
- Test and Inspect:
After installation, test the system (if applicable) to ensure functionality. Inspect for any loose fittings, sagging sections, or potential issues that may need correction.
Safety Tips:
Always ensure power is off before handling any electrical conduit or wiring.
Wear protective gear such as gloves and safety glasses.
Use proper tools to avoid damaging the conduit or causing injury.
Following these steps will help ensure a secure and compliant installation of corrugated conduit.
结论
In conclusion, corrugated conduits are a versatile, cost-effective, and reliable solution for protecting electrical wiring in a wide range of applications, from residential and commercial installations to industrial and automotive environments. With their flexibility, durability, and ease of installation, corrugated conduits offer excellent protection against environmental hazards such as moisture, UV rays, and chemicals. However, like any material, they do have limitations, particularly in high-stress or heavy-duty environments.
Choosing the right corrugated conduit for your project requires careful consideration of factors like material type, environmental conditions, and installation needs. By assessing the specific requirements of your project—whether it’s a simple residential setup or a complex industrial application—you can select the most appropriate conduit to ensure optimal performance, safety, and cost-effectiveness.
Ultimately, corrugated conduits provide a flexible, reliable, and affordable option for protecting electrical wiring, making them a preferred choice for many industries and applications. With the right product and supplier, you can ensure your electrical installations are safe, durable, and efficient.