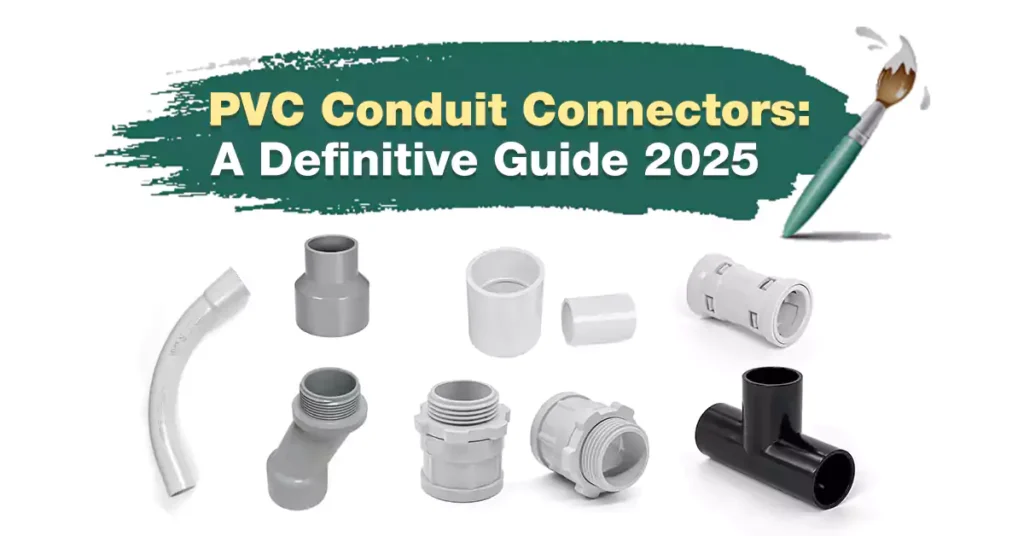
目录
PVC conduit connectors are essential components in modern electrical installations, ensuring secure and reliable connections between sections of PVC conduit. These connectors play a vital role in maintaining the integrity of the conduit system, allowing for smooth transitions between conduit lengths and facilitating proper sealing and grounding. In an era where electrical safety and efficiency are paramount, understanding the different types of PVC conduit connectors and their specific uses is crucial for professionals in the electrical industry.
Choosing the right PVC conduit connectors is not merely a matter of convenience; it is a critical step in ensuring the long-term safety and effectiveness of the electrical system. Conduit connectors help prevent potential hazards by providing a secure connection that protects electrical wiring from external elements, such as moisture, dust, and physical damage. Additionally, a properly selected connector ensures compliance with local codes and regulations, which is essential for passing inspections and ensuring that the system meets industry standards.
The wrong choice of connector can lead to issues like electrical faults, system malfunctions, and even fires. Factors such as environmental conditions, conduit type, and installation requirements should guide the selection process. In the following sections, we will explore the various types of PVC conduit connectors, their specific applications, and key considerations for selecting the right connector for your electrical projects.
What You Will Know:
After reading this article, readers will gain a clear understanding of the following:
- What PVC conduit connectors are and why they are essential in electrical installations.
- The different types of PVC conduit connectors, including straight connectors, tees, elbows, couplings, adaptors, reducer connectors, and offsets, and their specific uses in different parts of an electrical system.
- The key functions of PVC conduit connectors, including how they connect conduit, maintain system integrity, and protect the cables within.
- Related Codes and Standards for PVC connectors.
- Installation guides for PVC conduit connectors.
- How to choose the right type of connector based on the requirements of a particular electrical project, ensuring both safety and code compliance.
What are PVC Conduit Connectors?
定义
PVC conduit connectors are specialized fittings used to join and secure sections of PVC conduit in electrical installations. They are designed to create a seamless pathway for electrical wiring while ensuring that the system remains safe, durable, and compliant with industry standards. PVC conduit connectors come in various shapes and sizes to meet the diverse needs of electrical systems, whether the application involves residential, commercial, or industrial projects.
These connectors provide several essential functions, including maintaining the physical integrity of the conduit, preventing moisture and contaminants from entering the conduit system, and ensuring that electrical cables are properly protected. As a result, selecting the correct PVC conduit connector is crucial to ensuring the safety and performance of the entire system.
Key Functions of PVC Conduit Connectors
- Connecting Conduit
The primary function of PVC conduit connectors is to securely join sections of conduit, creating a continuous pathway for electrical cables. This ensures that the electrical system is intact and that the wiring is protected from external elements. - Maintaining Electrical System Integrity
PVC conduit connectors help to maintain the structural and electrical integrity of the entire conduit system. They ensure that the conduit remains secure and aligned, preventing movement or misalignment that could lead to wiring damage or safety hazards. - Protecting Cables
Conduit connectors also serve to protect the electrical cables running through the conduit from physical damage, moisture, and environmental elements. By creating a tight seal and providing a continuous, rigid pathway, they help prevent issues like short circuits, wire wear, or degradation due to environmental exposure.
7 Types of PVC Conduit Connectors
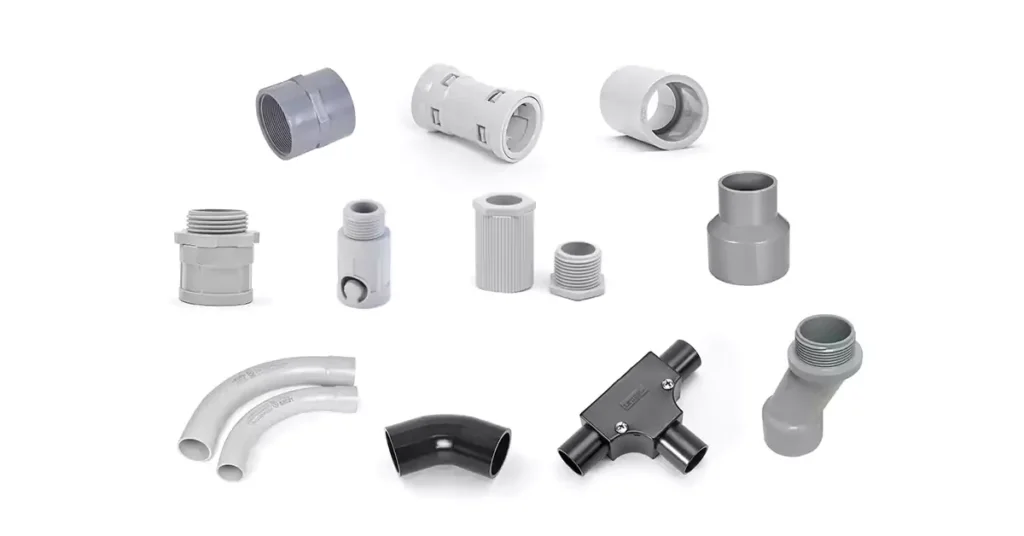
PVC conduit connectors come in a variety of types, each designed to fulfill specific functions in electrical installations. These connectors allow for directional changes, connections between different conduit sections, or transitions to different materials or sizes. Below, we’ll explore the different types of PVC conduit connectors, their purposes, benefits, and installation considerations.
Straight Connectors
Straight connectors are used to join two sections of conduit in a straight line, ensuring a continuous pathway for electrical wiring. These connectors are essential for extending conduit runs or connecting conduit to junction boxes, electrical panels, or other fittings.
好处:
Simple and straightforward connection.
Ensures a seamless flow of cables.
Provides a secure, rigid connection that maintains the conduit’s integrity.
Installation:
To install a straight connector, simply align the two ends of the conduit and slide them into the connector. Depending on the type (threaded or slip-on), the connector is either screwed in or pressed onto the conduit ends. For a tighter seal and to prevent moisture or dust from entering the conduit, it may be sealed with caulking or rubber gaskets if required by the installation standards.
Elbow Connectors
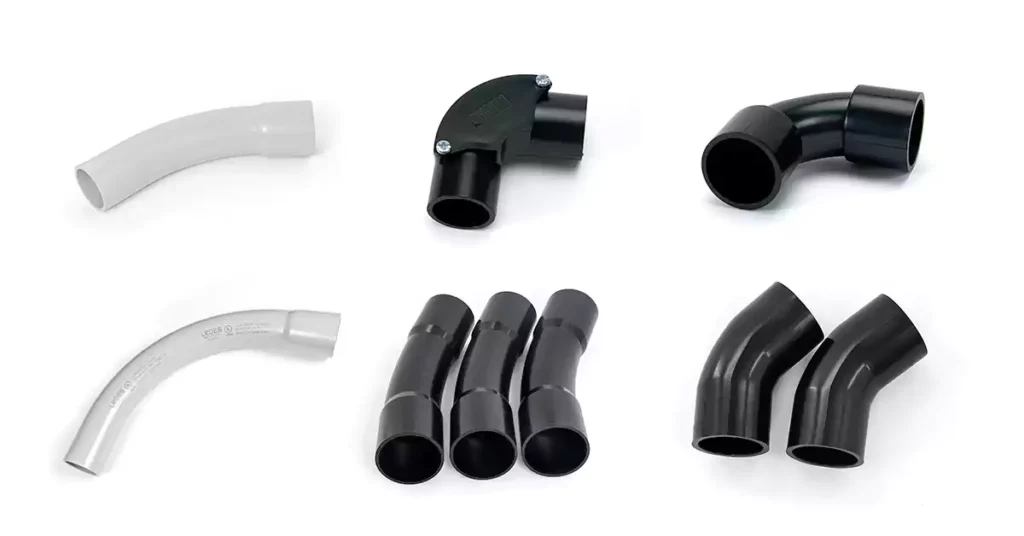
Elbow connectors are used to change the direction of conduit, typically by 90 degrees, 45 degrees or 30, 22.5 degrees, though other angles are also available. These connectors allow for routing conduit around obstacles or to alter the direction of the conduit path, providing flexibility in installations.
Elbow connectors are essential in installations where the conduit needs to navigate around corners or redirect the path of the wiring. They come in a variety of angles and materials, and the type of elbow used will depend on the installation’s layout and requirements.
Types of Elbows:
- 90-Degree Elbow: The most common type of elbow, used to make sharp turns in the conduit pathway.
- 45-Degree Elbow: Provides a more gradual angle than the 90-degree elbow, often used when less of a sharp turn is required.
- 22.5-Degree Elbow: Provide slight and gradual angle of conduit turning.
- Sweeps: These are specific types of elbows designed for smooth bends, typically used in areas where you want to minimize friction and stress on the wiring.
Tees
Conduit Tees are used when a conduit system needs to branch into multiple directions. A tee connector creates a “T” shape that allows a conduit run to split into two or more branches, commonly used when routing cables in different directions from a main conduit line.
目的:
Tees are used to branch conduit paths, ensuring that each branch maintains a secure, continuous conduit system. This is typically required in large installations with complex routing needs, such as in commercial or industrial settings.
Installation:
Tees are installed in a similar way to elbows or straight connectors. The ends of the conduit are inserted into the tee fitting, which then branches the wiring in the required directions.
Couplings
Conduit Couplings are designed to join two sections of conduit together. They are typically used to extend the length of the conduit run, or to connect conduit to junction boxes, enclosures, or other fittings. There are different types of couplings based on the kind of conduit they connect.
目的:
The primary purpose of a coupling is to securely join two sections of conduit, ensuring the system remains aligned and intact. Couplings help maintain the pathway for electrical wiring and protect it from external elements.
Types of Couplings:
- Standard Rigid Couplings: Used for connecting two sections of rigid PVC conduit.
- Expansion Couplings: These couplings allow for movement due to expansion or contraction of the conduit due to temperature changes, ensuring that the system remains intact during these shifts.
- ENT Couplings: Specifically designed for Electrical Nonmetallic Tubing (ENT), these couplings connect flexible conduit while maintaining its flexibility.
Offsets
Conduit Offsets are used when a conduit system needs to be redirected slightly, usually to avoid an obstacle or align with an electrical box knockout opening. Offsets are helpful for creating space around obstructions, ensuring the conduit doesn’t interfere with other systems or structures.
目的:
Offsets help maintain a clear and organized conduit layout, providing flexibility in routing. They also help prevent unnecessary bends in the conduit system that might cause stress on the wiring.
Installation:
To install an offset, the conduit is cut to the desired length, and the connector is attached at the necessary angle to realign the conduit with the intended path. Offsets are typically used when a simple bend or elbow is not sufficient.
Adapters
Conduit Adapters are used to connect PVC conduit to other materials (such as metal conduit) or to connect different sizes of conduit. These connectors are essential when transitioning between two different types of conduit or when the system needs to be adapted to fit a specific application.
目的:
Adapters provide a smooth and secure transition between different conduit types, ensuring that the system remains intact and that no gaps or weaknesses are introduced. They are often used in installations where conduit types need to change, such as in outdoor environments where PVC is used for the majority of the system, but metal conduit is necessary for specific sections.
Types of Adapters:
- Male Terminal Adapters: These adapters are used to connect a piece of conduit to a threaded or non-threaded box, electrical panel, or other fitting. The male end of the adaptor fits into the conduit, while the threaded or smooth exterior connects to the corresponding box or fitting. Male terminal adapters are commonly used to securely terminate conduit runs into junction boxes, electrical panels, or other enclosures.
- Female Adapters: Female adapters are the opposite of male terminal adapters, featuring a threaded or smooth interior that allows them to fit over the end of a conduit, providing a secure connection to another fitting or conduit. They are often used to connect a conduit to boxes, panels, or other fittings where a female connection is needed. Female adapters provide a stable, tight-fitting connection that helps maintain system integrity and prevent contamination.
Reducer Connectors
Reducer connectors are used when a conduit system needs to transition between different sizes of conduit. These connectors are designed to connect a larger diameter conduit to a smaller one, ensuring that the electrical cables can pass safely through the system without obstruction.
目的:
The primary purpose of reducer connectors is to provide a secure and smooth transition between two different-sized conduit sections. This ensures that the electrical wiring can flow through the conduit without any restrictions or potential damage caused by a sudden change in size.
Installation:
Reducer connectors are installed by inserting the ends of the conduit into the larger end of the connector, then securing the smaller end to the smaller conduit. These connectors provide a tight fit that prevents gaps or leaks, ensuring the system’s integrity is maintained.
7 Benefits of PVC Conduit Connectors
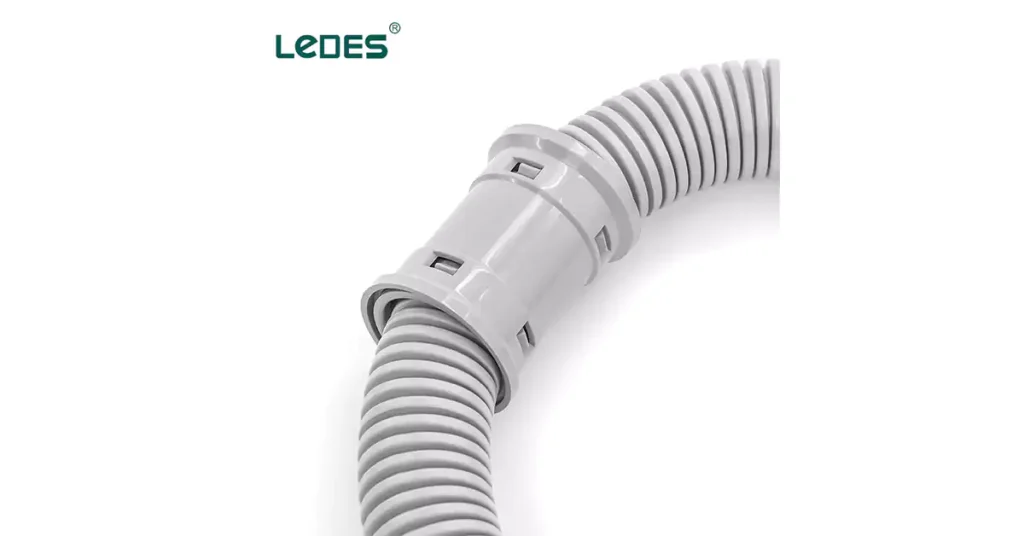
PVC conduit connectors are widely favored in electrical installations due to their numerous benefits. These fittings offer a range of advantages, including durability, resistance to corrosion, ease of installation, and more. Below are the key benefits of PVC conduit connectors, highlighting why they are a go-to choice for both professionals and DIY enthusiasts in the electrical industry.
1. Durability and Strength
Resistance to Impact, Weather, and Chemicals
PVC conduit connectors are known for their excellent durability and strength, making them highly resistant to various environmental factors. They can withstand impacts from external forces without cracking or breaking, ensuring that the conduit system remains intact even in challenging environments. Whether installed outdoors or in industrial areas, PVC connectors can endure harsh weather conditions, including extreme temperatures and UV exposure, without degrading. Additionally, PVC connectors are resistant to many common chemicals, ensuring that they maintain their integrity in industrial and commercial settings where exposure to corrosive substances is a concern.
2. Corrosion Resistance
Unlike metal connectors, which are prone to rust and corrosion over time, PVC conduit connectors do not corrode. PVC is a non-metallic material that remains unaffected by moisture, salt, or other corrosive elements that can degrade metal fittings. This makes PVC an ideal choice for applications in environments where exposure to water, chemicals, or salty air is common, such as coastal areas, industrial facilities, and outdoor installations.
3. Easy Installation
One of the biggest advantages of PVC conduit connectors is their ease of installation. PVC connectors are lightweight and require minimal effort to install compared to metal alternatives. They don’t require special tools or equipment for cutting, fitting, or joining, making them a great choice for both professionals and DIY enthusiasts. PVC connectors are typically designed for simple push-fit or threaded connections, which streamline the installation process and reduce labor time.
The ease of installation makes PVC connectors cost-effective, as they can save time and reduce labor costs on a project. This also makes them accessible to a wider range of installers, even those with minimal experience working with electrical conduit systems.
4. Electrical Insulation
PVC conduit connectors not only protect electrical cables from physical damage but also provide a layer of electrical insulation. This is critical for preventing electric shocks or short circuits caused by faulty connections or exposed wiring. PVC is a non-conductive material, which helps ensure that the electrical system remains safe for both people and equipment.
The electrical insulation provided by PVC conduit connectors adds an extra layer of safety to electrical installations, reducing the risk of electrical hazards and ensuring that the system complies with safety standards and regulations.
5. Flexible and Lightweight
PVC conduit connectors are known for being lightweight and flexible, which makes them easy to handle and transport during installation. Their lightness reduces the strain on workers when setting up large conduit systems, and the flexibility of PVC makes it easier to adjust the layout of the conduit as needed, especially in areas with obstacles or tight spaces. PVC connectors are also less prone to cracking during installation, ensuring that the integrity of the conduit system is maintained.
The flexibility and lightweight nature of PVC connectors make the entire system more versatile and easier to install in difficult or confined spaces. Installers can manipulate the conduit layout with minimal effort, allowing for more efficient installation in various environments.
6. Cost-Effectiveness
PVC conduit connectors are often more affordable than their metal counterparts, providing a cost-effective solution for both residential and commercial electrical installations. The lower material and manufacturing costs of PVC, combined with the reduced installation time, make it an attractive option for budget-conscious projects without compromising safety or performance.
7. Long-Term Reliability
PVC conduit connectors have excellent resistance to aging, maintaining their strength and functionality over time. They are not prone to fading, embrittling, or degrading under UV exposure, making them suitable for both indoor and outdoor applications. This long-term reliability ensures that the electrical system remains effective and safe throughout its lifespan.
Applications of PVC Conduit Connectors
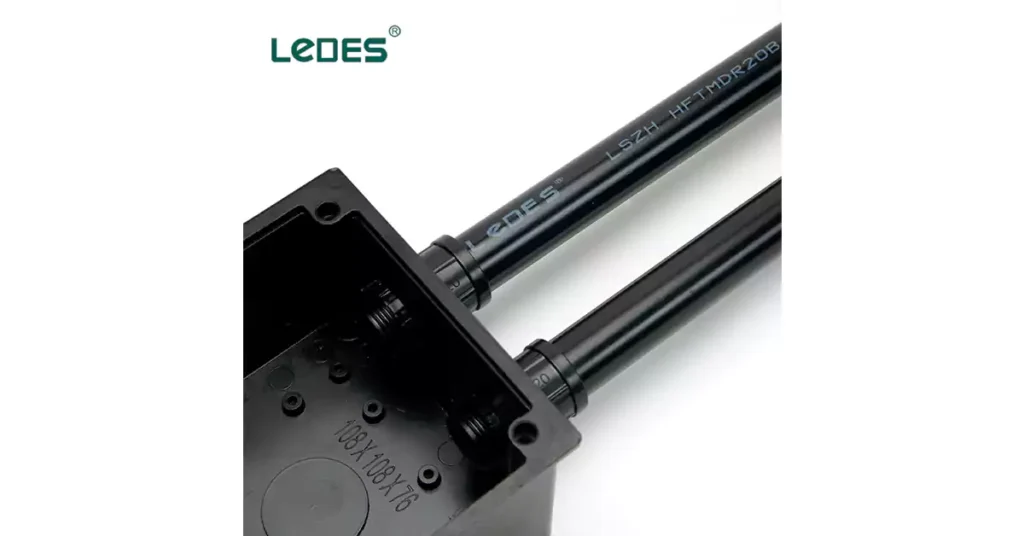
1. Electrical Wiring Systems
PVC conduit connectors are commonly used in both residential and commercial electrical wiring systems to provide a safe and reliable conduit pathway for electrical cables. In residential homes, they are used to route power to outlets, switches, and fixtures, ensuring that wiring is well-protected from physical damage. In commercial and industrial settings, PVC conduit connectors are used to link sections of conduit, ensuring that cables are securely routed between electrical panels, machinery, and other equipment.
The non-conductive nature of PVC provides added safety, preventing electrical shorts or shock hazards while maintaining the integrity of the wiring system. PVC connectors are also compliant with local electrical codes, making them a safe and effective solution for electrical installations of all sizes.
2. Outdoor Installations
PVC conduit connectors are commonly used for outdoor electrical installations, where protection from the elements is critical. Outdoor environments expose electrical wiring to weather-related challenges such as rain, snow, humidity, and extreme temperatures. PVC connectors, with their resistance to UV rays and moisture, offer long-lasting protection in these harsh conditions.
Whether it’s for powering outdoor lighting systems, security cameras, or signage, PVC conduit connectors help ensure that the wiring remains intact and safe from environmental damage. These connectors are also often used in agricultural, recreational, or remote installations where exposure to the elements is a concern.
3. Underground Wiring
PVC conduit connectors are ideal for underground wiring applications, providing a secure and durable solution for protecting electrical cables buried in the ground. Underground installations require connectors that can withstand soil pressure, moisture, and potential physical impact, all of which PVC conduit connectors are well-equipped to handle.
When used with PVC conduit, these connectors help to route electrical power or data cables to buried systems, such as outdoor lighting, irrigation systems, and underground utilities. PVC connectors ensure that the conduit system remains sealed and intact, preventing water ingress and ensuring the system’s reliability over time.
4. Industrial Applications
In industrial applications, PVC conduit connectors are frequently used in manufacturing plants, warehouses, and other heavy-duty environments to route power and control cables to machinery, equipment, and control panels. The robust construction and resistance to chemicals and physical impact make PVC conduit connectors suitable for industries like automotive, food processing, and pharmaceuticals.
These connectors not only ensure that electrical wiring is safely routed but also help prevent the buildup of static electricity and reduce the risk of electrical shocks in hazardous environments. Additionally, PVC’s lightweight nature and ease of installation make it a cost-effective choice for industrial projects where speed and efficiency are essential.
5. Construction & Infrastructure Projects
PVC conduit connectors are widely used in construction and infrastructure projects to support the installation of electrical systems within buildings, roads, bridges, and other large-scale structures. From wiring for lighting, HVAC systems, elevators, and escalators to powering heavy machinery and street lighting, PVC conduit connectors provide the necessary connections that ensure the system functions safely and efficiently.
Moreover, PVC conduit connectors help projects comply with building codes by providing secure, code-compliant electrical systems. These connectors are easy to incorporate into construction designs and meet the standards set for electrical wiring and safety.
6. Home & Building Renovations
PVC conduit connectors are a go-to choice for home and building renovations, where modifications to existing electrical systems are necessary. Whether updating outdated wiring, installing new electrical outlets, or rerouting cables to accommodate new structures, PVC conduit connectors provide an easy and efficient way to complete these tasks.
Their ease of installation is especially beneficial in renovation projects, where minimizing disruption to existing systems is key. PVC connectors are also ideal for retrofitting electrical systems in buildings that need to be upgraded to meet current safety standards.
Code Compliance for PVC Conduit Connectors
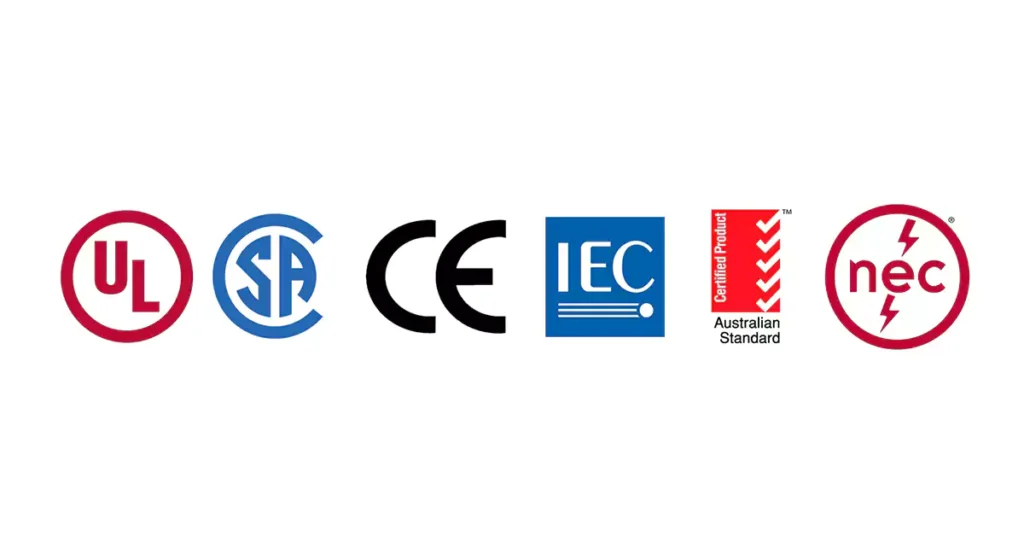
There are involved many standards and codes for fittings of connectors, follow are some common ones:
The National Electrical Code (NEC): Article 352
When selecting and installing PVC conduit connectors, it is essential to ensure compliance with the National Electrical Code (NEC). The code outlines specific regulations that govern the use of PVC fittings and connectors to ensure safe and reliable electrical installations. Below is a summary of key points regarding PVC conduit connectors as per the NEC:
Listing and Labeling Requirements
All PVC conduit connectors must be listed and labeled by a recognized testing agency (such as UL) to confirm their compliance with safety and performance standards. This ensures that connectors are designed, tested, and manufactured to meet the minimum requirements for quality, durability, and safety.
It is important to check that the connectors are properly marked with certification labels or identifying marks that indicate they meet these requirements. The labeling also ensures that the connectors are suitable for the specific environments in which they will be used (e.g., wet, corrosive, or high-temperature areas).
Approved Applications and Environments
PVC conduit connectors are approved for use in a wide range of environments, but specific guidelines govern their application:
- Dry, Damp, and Wet Locations: PVC connectors can be used in dry, damp, and wet locations, but their use must be appropriate for the conditions.
- Corrosive Environments: PVC is highly resistant to many chemicals and environmental conditions, making it suitable for use in corrosive environments, as long as the connectors are specifically approved for such applications. PVC can withstand the effects of chemicals, salt, and other harsh substances, ensuring long-term performance and protecting cables.
- Underground and Direct Burial Installations: PVC conduit and connectors are allowed for direct burial applications, provided they meet the requirements for strength and resistance to impact. In cases where PVC conduit is encased in concrete or buried underground, the connectors must be able to withstand potential abuse, such as impact and crushing, during installation and after installation.
Temperature and Physical Damage Resistance
PVC conduit connectors must be able to withstand specific environmental conditions such as extreme temperatures and physical stresses:
- 耐温性: PVC connectors must be suitable for the temperature ranges expected in the installation. For example, the connectors should be rated to perform well in temperatures commonly found in the region, and they should not be used in areas with temperatures exceeding 50°C (122°F) unless they are specifically rated for high-heat applications.
- Protection Against Physical Damage: In areas where PVC conduit is exposed to physical damage, connectors must be chosen based on their ability to resist impact and crushing forces. Schedule 80 PVC connectors are recommended for such applications, as they are more robust and can provide better protection in areas where the conduit may be subject to impact or other physical damage.
Bends and Expansion Fittings
To maintain the integrity of the conduit system, the NEC outlines guidelines for bends and expansion:
Bends: PVC conduit connectors should allow for proper bending without damaging the conduit or reducing its internal diameter. The bends should not exceed a certain number, and the radius of bends should be made with specific equipment to avoid damaging the conduit. Exceeding the number of bends or using improperly sized connectors can lead to installation difficulties or create an impedance for the conductors within the conduit.
Expansion Fittings: PVC conduit expands and contracts with temperature fluctuations. The NEC requires the use of expansion fittings to accommodate any length change of 6 mm (1/4 inch) or more in a straight run. These fittings help absorb the effects of thermal expansion and contraction, preventing stress on the conduit and connectors, and ensuring that the system remains intact and functional under varying temperature conditions.
Strength and Durability Standards
The construction of PVC connectors must meet specific strength and durability requirements:
Resistance to Moisture and Chemicals: The connectors must be resistant to moisture, chemicals, and other environmental factors that could compromise the integrity of the system. This includes being able to withstand the impact of chemicals in industrial or outdoor applications.
Flame Retardancy and Impact Resistance: For above-ground use, connectors must be flame retardant and resistant to impact and crushing. In outdoor applications, PVC connectors should be able to resist UV radiation and prevent degradation from sunlight exposure.
UL Standards for PVC Conduit Connectors
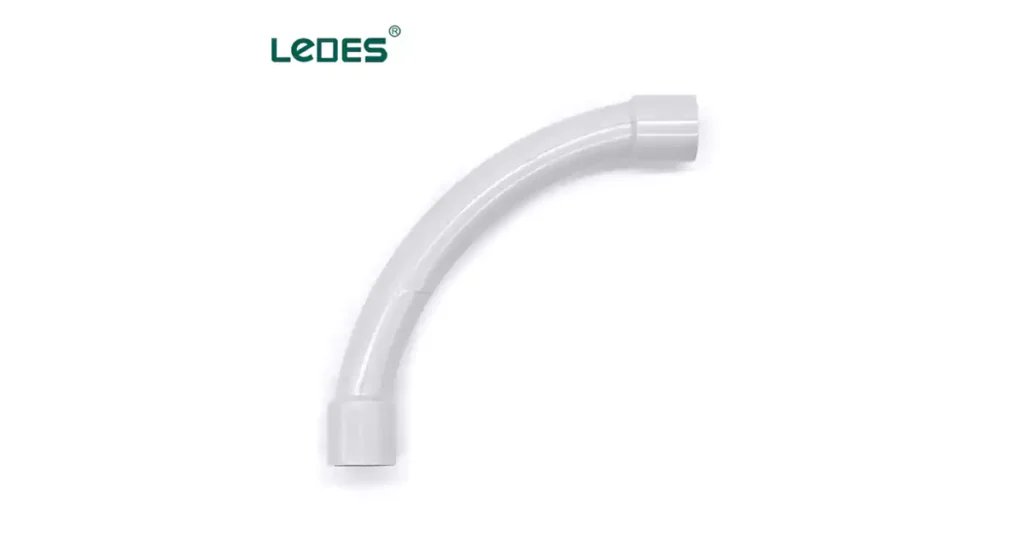
The Underwriters Laboratories (UL) is a globally recognized independent safety science organization that sets industry standards for safety, performance, and reliability. UL certifications are essential for ensuring that products meet stringent safety requirements, providing both manufacturers and end-users with confidence in the products’ quality and performance.
For PVC conduit connectors, complying with UL standards means that these connectors have been rigorously tested for various physical, chemical, and environmental stressors, ensuring that they will perform as expected in a variety of installations. This includes critical factors such as durability, fire resistance, and resistance to physical damage.
The two primary UL standards applicable to PVC conduit connectors are UL651 和 UL 1653, which detail the construction, performance, and safety requirements for conduit systems and fittings. Let’s explore these standards and their relevance to PVC connectors.
UL 651:
UL 651 specifically addresses the requirements for rigid PVC conduit and associated fittings, ensuring they are safe for electrical installations. This standard includes a broad range of specifications for connectors, such as:
(尖端: You can read our last post about UL listed PVC conduit requirements if you are interested in PVC electrical conduit parts.)
方面: The standard provides precise dimensional requirements for PVC connectors to ensure proper fitting and compatibility with PVC conduits. This is crucial for maintaining a secure and efficient electrical system without compromising its safety.
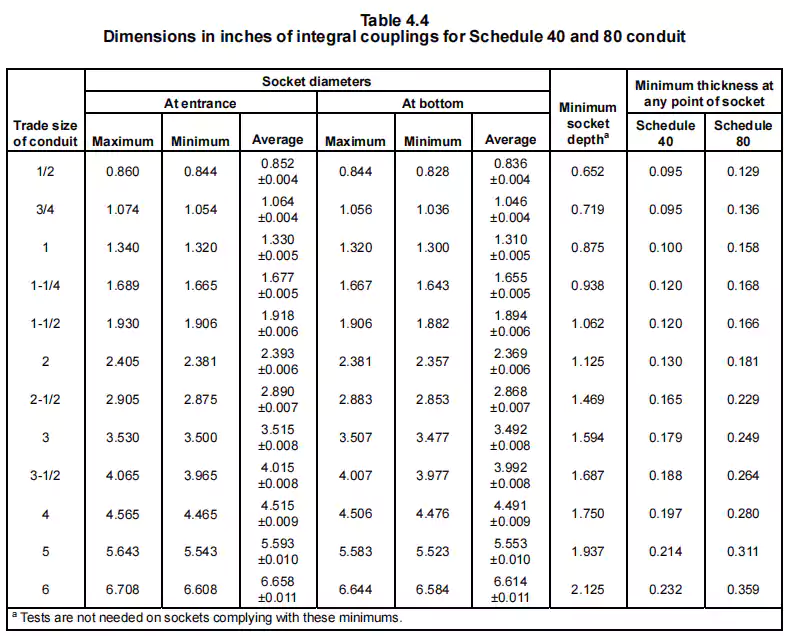
UL 651 Dimensions of Schedule 40 80 Conduit Couplings
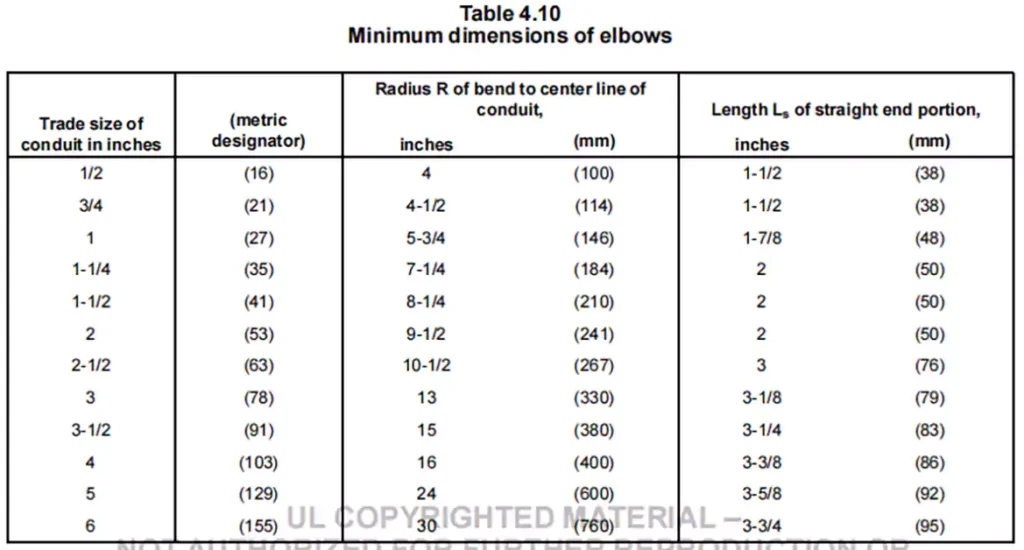
UL 651 Standard Dimensions of PVC Conduit Elbows
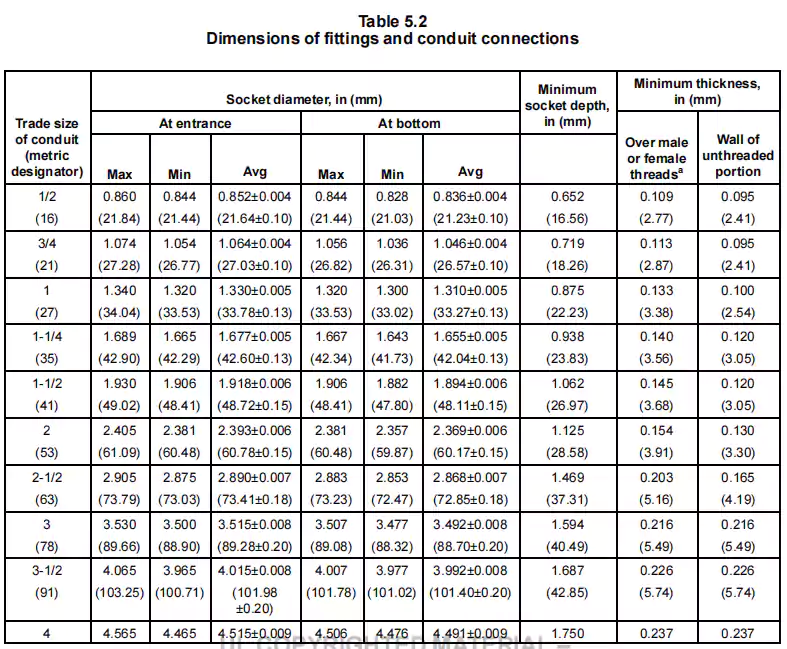
UL 651 Standard Dimensions of PVC Conduit Connections
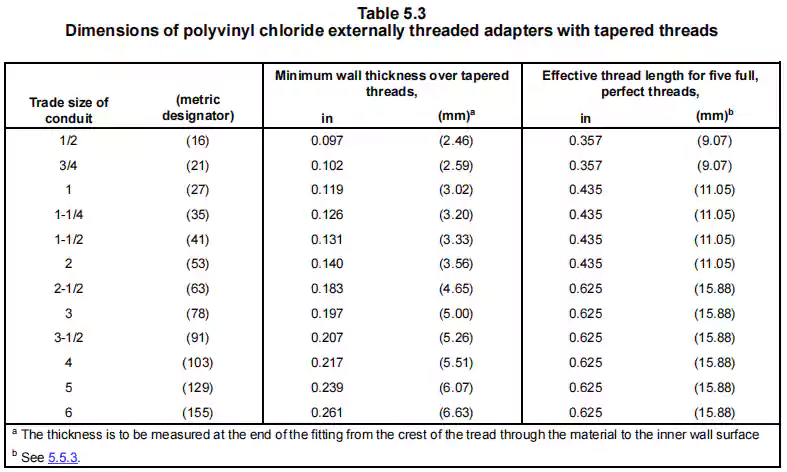
UL 651 Standard Dimensions of PVC Conduit Adapeters
Water Absorption: UL 651 tests the water absorption properties of PVC connectors, ensuring that they do not absorb excess moisture, which could potentially degrade their performance or lead to electrical hazards. This property is particularly important for outdoor and underground installations, where exposure to water is likely.
Flammability: PVC connectors are required to meet strict flammability standards. UL 651 specifies that the connectors must be fire-resistant to prevent the spread of flames in the event of a fire. This is essential for electrical safety, especially in commercial or industrial applications where high-voltage systems could be present.
Heat Distortion: Connectors are also tested for heat resistance under various temperature conditions. The heat distortion test ensures that PVC connectors do not warp, bend, or lose their shape when exposed to high temperatures, which could otherwise result in compromised conduit integrity.
Crushing and Bending Resistance: UL 651 establishes that connectors must withstand crushing and bending forces during installation and throughout their use. This is particularly relevant for underground installations or locations where physical damage is more likely.
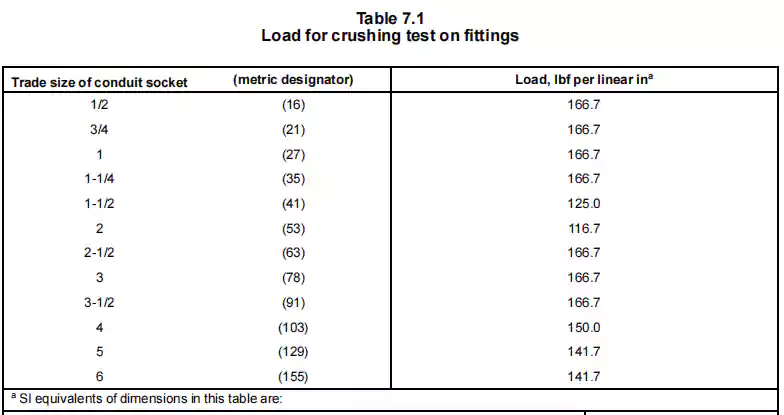
UL 651 Standard Load of Crushing Test of Conduit Fittings
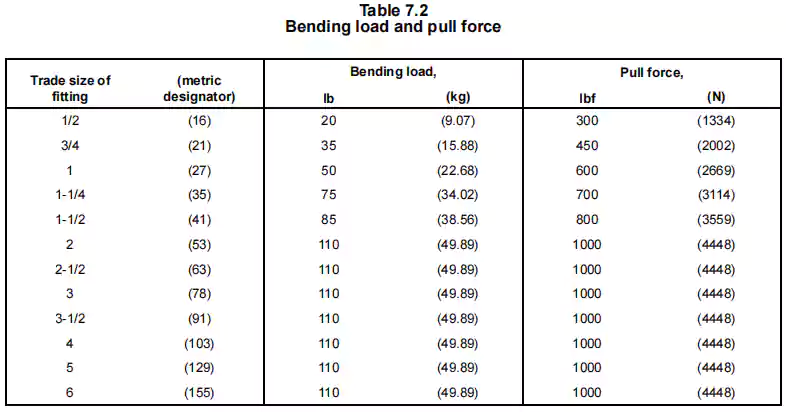
UL 651 Standard Bending Load and Pull Force Test of Conduit Fittings
Pull Test: The pull test evaluates the strength of the connection between connectors and conduits, ensuring that they remain securely in place and will not disconnect under stress or force.
Resistance to Specific Reagents: PVC connectors are tested for their ability to resist chemical exposure to various reagents, which is especially critical in corrosive environments or industries dealing with harsh chemicals.
UL 1653:
UL 1653 focuses on the performance requirements for flexible nonmetallic conduits and their connectors. While more commonly associated with flexible conduits, this standard also provides important guidelines that apply to PVC connectors:
Bending and Pull Test: UL 1653 requires connectors to pass specific bending and pull tests, ensuring they do not fail or disconnect under normal installation and operating conditions. The bending test assesses the flexibility of connectors, while the pull test ensures that the connection is secure even under tension.
Flame Resistance: Connectors are subjected to a flame test to determine how well they resist ignition and the spread of fire. UL 1653 mandates that the connectors must be flame retardant to meet safety standards, particularly in applications where fire safety is critical.
抗冲击性: The impact resistance test at minus 20 Degrees Celsius ensures that connectors can withstand physical shocks, drops, or blows without cracking or breaking. This is vital for installations where the system may be exposed to mechanical stresses, such as in industrial settings or outdoor environments.
Complying with UL 651 and UL 1653 standards ensures that PVC conduit connectors are safe, durable, and suitable for use in various environments. These standards cover critical factors such as flame resistance, impact resistance, water absorption, and chemical resistance, all of which contribute to the longevity and safety of electrical installations. UL certification is an essential mark of quality, providing confidence to both manufacturers and end-users that the connectors meet the highest industry standards for safety and performance.
(尖端: You can read our last post about ENT tubing code compliance if you are interested in ENT conduit parts.)
CSA Standards for PVC Conduit Connectors
The Canadian Standards Association (CSA) is a leading organization responsible for setting safety standards in Canada, similar to UL in the United States. For PVC conduit connectors, CSA certification ensures that products meet rigorous safety, performance, and construction requirements, providing essential protections for electrical systems in Canada. Two critical CSA standards governing PVC conduit connectors are CSA C22.2 No. 211.2 和 CSA C22.2 No. 227.1. These standards cover a variety of performance and construction specifications for PVC connectors to ensure their reliability and safety in diverse applications.
尖端: As to DB2 conduit electrical code, you can read our last post to learn more about it.
CSA C22.2 No. 211.2:
CSA C22.2 No. 211.2 applies to PVC conduit connectors, including couplings, elbows, and bends. This standard outlines the dimensions, materials, and performance criteria required for the connectors used in electrical systems in Canada. Below are the key points covered by this standard:
Dimensions and Construction: This standard provides specific dimensional requirements for PVC connectors, ensuring that the connectors are appropriately sized to fit with the conduit they are meant to connect. Proper dimensions are crucial for maintaining a secure and leak-proof connection, which is essential for safety and proper electrical function. It also covers construction requirements, ensuring the connectors are made from durable and high-quality materials that will endure over time.
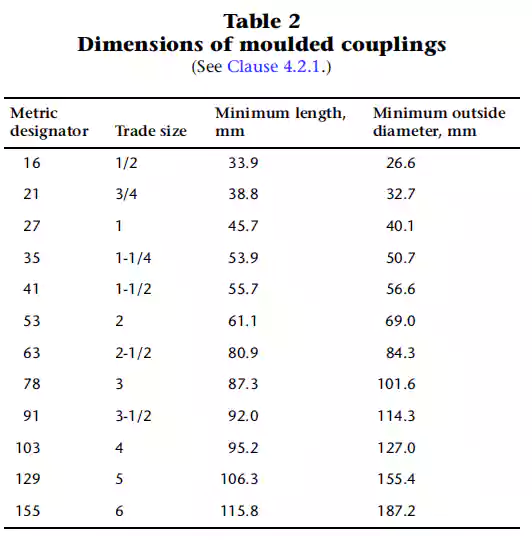
CSA C22.2 No. 211.2 Standard Dimensions Requirement of Conduit Couplings
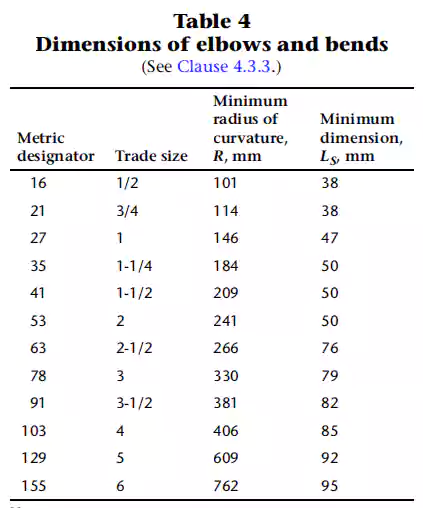
CSA C22.2 No. 211.2 Standard Dimensions Requirement of Conduit Elbows and Bends
Impact Resistance at Low Temperatures: One of the critical aspects covered by CSA C22.2 No. 211.2 is the impact resistance at low temperatures. PVC connectors must maintain their structural integrity even when exposed to cold conditions, as cold weather can cause some materials to become brittle and more prone to cracking. The standard specifies that connectors must withstand impacts at low temperatures without breaking or cracking.
耐化学性: Chemical resistance is another vital requirement. PVC connectors must be able to resist degradation or damage caused by exposure to common chemicals, including those found in industrial, commercial, and residential settings. This ensures the long-term durability of the connectors, especially in environments where chemicals are used or may come into contact with the connectors.
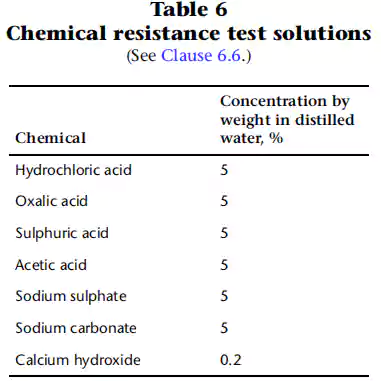
CSA C22.2 No. 211.2 Standard Chemical Resistance Test Required of Conduit Fittings
CSA C22.2 第 227.1 号:
CSA C22.2 No. 227.1 applies to flexible nonmetallic conduit and connectors, aligning closely with the UL 1653 standard. While this standard focuses on flexible conduit systems, many of its performance requirements are also applicable to rigid PVC conduit connectors in terms of safety and reliability.
CSA C22.2 No.85:
CSA C22.2 No. 85 also plays a vital role in regulating the performance of PVC conduit connectors in Canada. This standard is specifically concerned with the performance requirements for nonmetallic conduit fittings. It outlines the key criteria for ensuring that PVC connectors can withstand the demands of various environmental and physical conditions, providing a safe and reliable means of electrical wiring protection.
Key Performance Requirements
方面:
This standard specified the dimension requirements for connectors such as adapters and reducers:
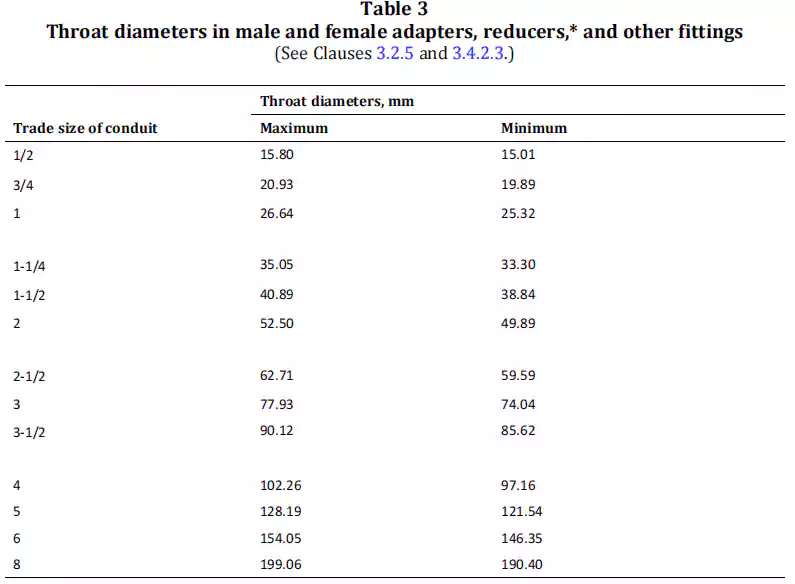
CSA C22.2 No.85 Standard Dimension Requirements for Conduit Connectors and Adapters
Water Absorption:
Water absorption is a critical factor for PVC conduit connectors, particularly for those used in outdoor or underground applications. CSA C22.2 No. 85 specifies that connectors must exhibit minimal water absorption to prevent material degradation and maintain long-term durability, especially in damp or wet environments.
Flame Resistance:
As with other CSA standards, CSA C22.2 No. 85 requires that PVC connectors are flame-resistant. The connectors must not contribute to the spread of fire in the event of an electrical fault or short circuit. This requirement ensures that PVC connectors are suitable for use in high-risk areas where fire safety is a priority.
体力:
Crushing Resistance: PVC connectors must be able to withstand physical impacts without being crushed. This is important for maintaining the structural integrity of the conduit system in areas where the connectors might be subject to mechanical stresses or accidental impacts.
Impact Resistance at Low Temperatures: PVC connectors must retain their impact resistance at low temperatures. In colder climates or regions, PVC materials can become brittle. The standard ensures that connectors are not prone to cracking or breaking when exposed to low temperatures.
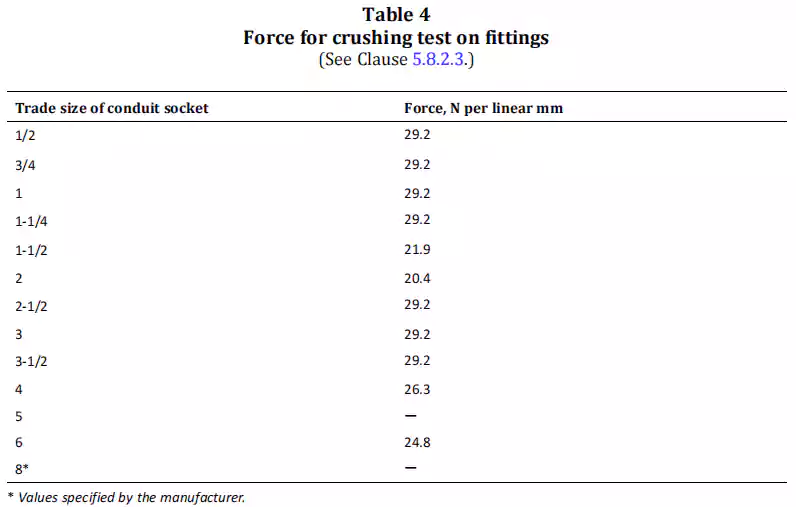
CSA C22.2 No.85 Standard Force for Crushing Test on Fittings Data Sheet
弯曲强度: Similar to CSA C22.2 No. 227.1, CSA C22.2 No. 85 requires that PVC connectors can endure bending forces without damage. This is crucial for installations where the conduit system needs to be routed around corners or tight spaces.
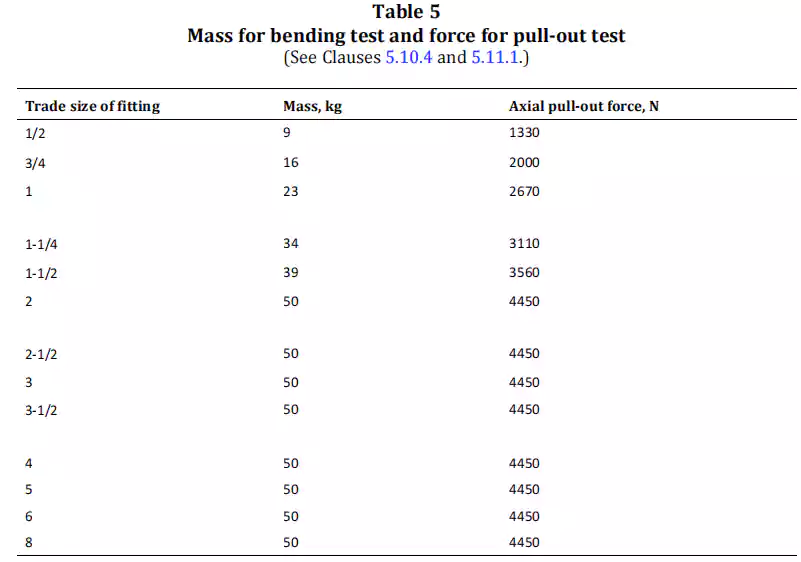
CSA C22.2 No. 85 Standard Bending Strength Test for Conduit Fittings
耐化学性:
PVC connectors must exhibit chemical resistance to ensure they are not degraded by exposure to common chemicals that may be found in the environment. This includes resistance to oils, solvents, and other corrosive agents that could damage the connectors over time.
IEC Standards for PVC Connectors
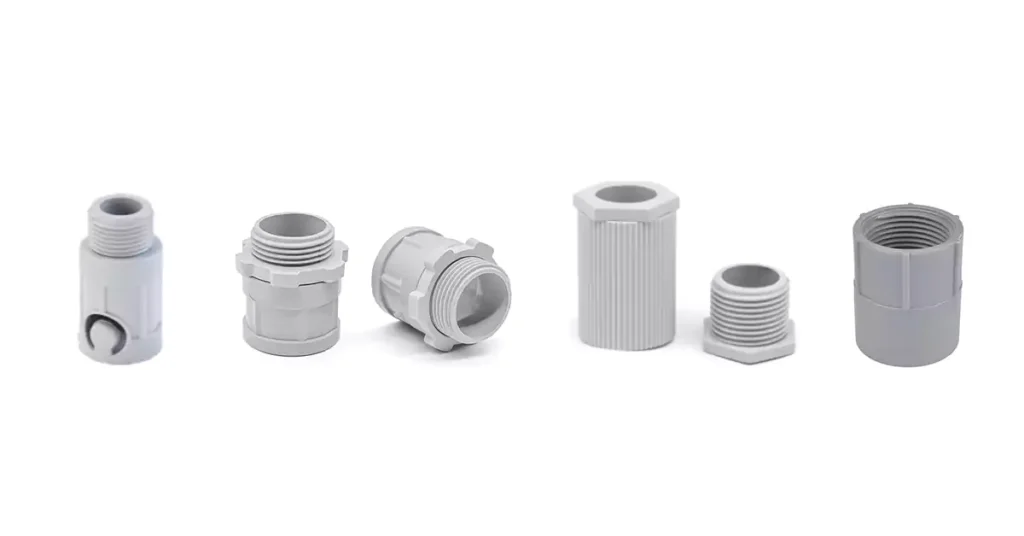
The IEC standards (IEC 61386-21, IEC 61386-23, and IEC 60423) provide essential guidelines for the design, performance, and installation of PVC conduit connectors. These standards ensure that connectors meet high safety, durability, and performance requirements in electrical installations.
- IEC 61386-21 focuses on the specific requirements for rigid PVC conduit fittings, ensuring they are resistant to physical damage, impact, and environmental stress while offering flame resistance.
- IEC 61386-23 expands on performance requirements for both rigid and flexible PVC conduit fittings, emphasizing impact resistance, temperature tolerance, and chemical durability.
- IEC 60423 covers the dimensions, construction, and overall mechanical and electrical performance of PVC connectors, ensuring they maintain integrity and provide proper insulation.
By complying with these standards, PVC connectors are guaranteed to provide safe, durable, and reliable connections in electrical systems, helping prevent electrical hazards and ensuring long-term performance. These standards also ensure that connectors are compatible internationally, supporting consistent use across global electrical installations.
Notes: To IEC standard rigid PVC conduit code, you can read our last post for more details.
AS/NZS Standards for PVC Conduit Connectors
The AS/NZS 2053 series of standards outline the key requirements for PVC conduit connectors used in electrical installations across Australia and New Zealand. These standards ensure that connectors meet specific criteria for construction, performance, and durability.
- AS/NZS 2053.1 covers general requirements for PVC conduit and fittings, including material specifications, dimensional accuracy, and electrical insulation.
- AS/NZS 2053.2 addresses the technical requirements for rigid PVC conduit connectors, emphasizing mechanical strength, flame resistance, and temperature tolerance.
- AS/NZS 2053.5 focuses on connectors used in underground installations, ensuring they are resistant to corrosion, impact, and moisture.
Together, these standards ensure that PVC conduit connectors are reliable, safe, and capable of withstanding various environmental conditions in electrical systems in Australian and New Zealand regions.
Pro Tips: The AS/NZS PVC conduit electrical code; you can read our last post for expert insights.
ETL and CETL Certification for PVC Conduit Connectors
ETL (Intertek) and CETL (Canadian ETL) are certifications that signify a product’s compliance with safety and performance standards in the United States and Canada, respectively. These certifications are recognized globally and provide assurance that the product meets stringent safety requirements, ensuring reliability in electrical installations.
The ETL Certification is issued by Intertek, an independent, globally recognized testing and certification organization. It signifies that a product has been tested and meets the applicable UL (Underwriters Laboratories) standards. ETL certified products have been evaluated for safety, performance, and compliance with regulatory requirements.
The CETL Certification is the Canadian equivalent of ETL certification, issued by Intertek. It ensures that the product complies with CSA (Canadian Standards Association) standards for safety and performance in Canada. The CETL mark is essential for products being sold and used in Canada, confirming that they have been tested to meet specific regulatory standards.
How to Choose the Right PVC Conduit Connector
Choosing the right PVC conduit connector is crucial for ensuring the safety, reliability, and long-term performance of an electrical system. With various types of connectors available, it’s important to consider several factors to select the most suitable option for your project. Here are the key aspects to consider when choosing the right PVC conduit connector:
1. Consider the Type of Application
The first step in selecting a PVC conduit connector is to identify the application requirements. Different types of connectors are suited for various purposes, understanding the specific needs of your electrical system will help determine which type of connector is required for seamless integration.
2.Check Compatibility with Conduit and Other Components
PVC conduit connectors must be compatible with the type and size of conduit being used. Always match the connector with the specific type of conduit (e.g., Schedule 40, Schedule 80, or ENT) and ensure that the sizes of the connectors match the conduit diameter. Additionally, verify that connectors will work with other components, such as boxes, elbows, and adaptors.
- Material compatibility: For example, ensure that the connector is made from the same material as the conduit, such as rigid PVC 或者 flexible PVC, to maintain system integrity.
- Size compatibility: Ensure that connectors fit correctly with the conduit and other system parts, such as junction boxes or raceways.
3. Consider the Environmental Conditions
The environmental conditions where the conduit system will be installed play a significant role in determining the right connector. PVC conduit connectors are designed for various environments, and it’s important to consider factors such as:
- 温度范围: Choose connectors rated for extreme temperatures if your installation will be exposed to heat or cold.
- Exposure to chemicals: For industrial or outdoor environments, connectors may need to withstand exposure to chemicals, oils, or corrosive elements.
- UV resistance: For outdoor or exposed installations, select connectors that are UV-resistant to prevent degradation from sunlight exposure.
Check product specifications for UV protection, weather resistance, and impact resistance for use in specific conditions.
4. Code Compliance
Ensure that the PVC conduit connectors meet relevant NEC, UL, CSA, or IEC, AS.NZS standards for safety and performance. Certified connectors guarantee compliance with industry standards for electrical insulation, fire resistance, chemical resistance, and physical durability.
5. Evaluate the Installation Process
The ease of installation is another important consideration when choosing a PVC conduit connector. Some connectors are designed for quick and easy installation, requiring no special tools, while others may require more complex procedures. Look for features such as:
- Quick-connect features: Certain connectors have snap-fit or twist-lock designs for faster installation.
- Tool-free installation: Some connectors allow for easy assembly without the need for additional tools or equipment.
- Flexibility and adjustability: Ensure that connectors allow for proper alignment, adjustment, and sealing without excessive effort.
Choosing connectors that are easy to install can save time and reduce labor costs on the job site.
6. Durability and Longevity
The durability of the PVC conduit connector is essential for ensuring long-term system performance. High-quality connectors are designed to withstand physical stress, vibration, and environmental wear. Choose connectors that are:
耐冲击: Resistant to damage caused by physical forces, ideal for areas where impact or vibration is common.
Crush-resistant: Some connectors offer increased resistance to crushing, which is important for underground installations or where conduits are exposed to heavy loads.
Flame-retardant: In areas where fire safety is a concern, select connectors that meet flame retardant standards to minimize fire risks.
7. Evaluate Cost and Quality
While cost is an important factor, it should not compromise the safety or performance of the electrical system. Opt for connectors that offer the best balance of quality and affordability. Investing in higher-quality connectors can result in long-term savings by reducing the risk of failures, replacements, and safety hazards.
Installation Guidelines for PVC Conduit Connectors
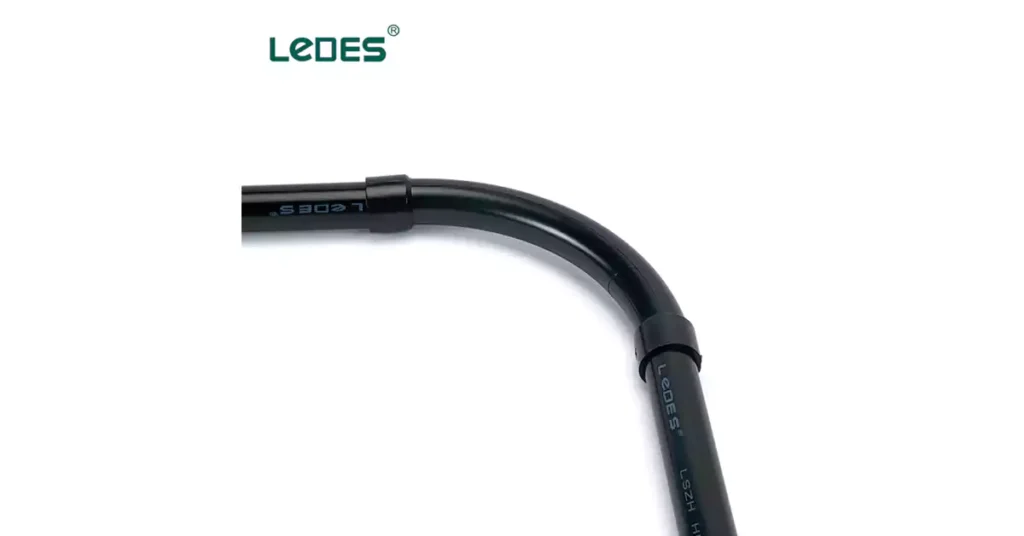
Proper installation of PVC conduit connectors is essential for ensuring a secure, durable, and code-compliant electrical system. While different types of connectors serve specific purposes, their installation processes often share common steps. This section provides a detailed guide on how to install various PVC conduit connectors effectively.
General Installation Guidelines
Regardless of the type of connector, there are some universal steps and considerations that apply to all installations:
Preparation Before Installation
- Gather the required tools and materials: Ensure you have the necessary connectors, PVC conduit, primer, PVC cement (if required), a measuring tape, and a conduit cutter.
- Check conduit and connector sizes: Verify that the connectors match the conduit diameter and type (e.g., Schedule 40, Schedule 80).
- Ensure clean and dry surfaces: Remove dirt, grease, or moisture from the conduit ends and connectors before assembly to ensure a secure fit.
- Plan the conduit layout: Before installation, map out the route, allowing for bends, offsets, and expansion fittings if necessary.
Cutting and Deburring the Conduit
- Measure and mark the conduit at the required length.
- Use a PVC pipe cutter or saw to cut the conduit cleanly.
- Deburr the edges using a file or reamer to prevent rough edges from interfering with the connection.
Securing the Connection
- Dry-fit the components to check alignment before applying adhesive or fastening.
- Apply PVC primer and cement (if applicable) to the conduit end and the inside of the connector for a strong bond.
- Push the conduit into the connector with a slight twisting motion to ensure full insertion.
- Hold the joint firmly for a few seconds to allow the cement to set.
Ensuring Proper Sealing and Support
- Use appropriate sealing methods (e.g., gaskets or O-rings) for watertight connections in wet locations.
- Allow curing time for adhesive-based connections before exposing them to mechanical stress.
- Secure the conduit system with supports at recommended intervals per NEC or local electrical codes.
Installation Guide for Connectors with Threads
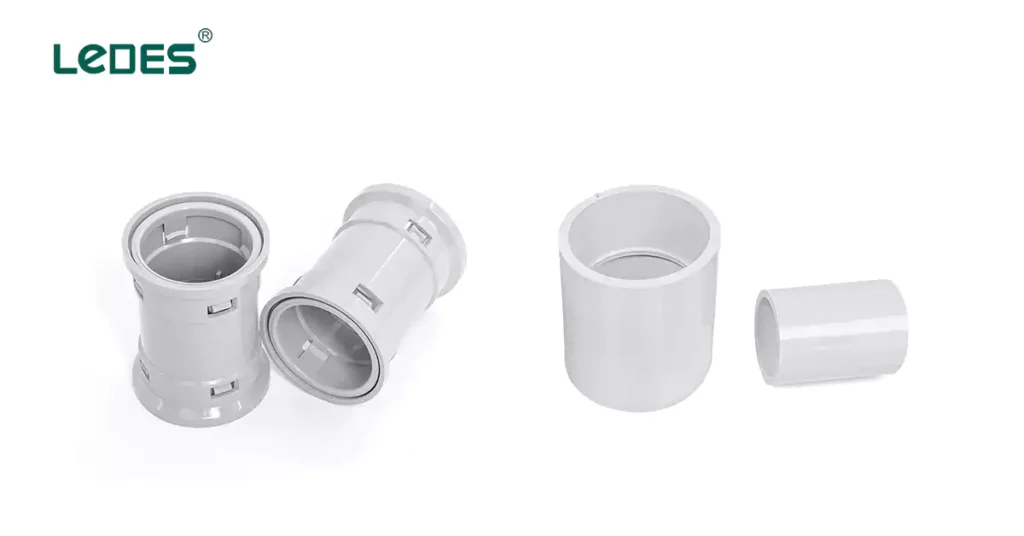
Adapters and Offsets
Connect PVC conduit to a electrical boxes, enclosures or threaded fittings.
- Apply PVC cement to the conduit side (if applicable) to connect conduit with connector, for connector that connect tubing and electrical boxes, just connect tubing tight with connector (with locking nuts on one side).
- Align the connector with knockout or electrical box opening and thread connector onto the box.
- Tighten the connection securely to avoid movement.
Installation Guide for Connectors with Locking Tabs
ENT Couplings
Due the connectors’ design, the installation for them are quite easy.
- Measure and cut the ENT conduit to the required length.
- Deburr the cut ends to remove any rough edges.
- Insert each end of the ENT conduit into the coupling until it locks into place, ensure a firm grip.
- Ensure proper alignment of the conduit run before securing it with straps or supports.
For more detailed guidelines for electrical conduit installation, check our previous article.
Maintenance and Care of PVC Connectors
Proper maintenance and care of PVC conduit connectors ensure the longevity and safety of electrical conduit systems. Regular inspection, cleaning, and timely replacement help prevent failures and maintain compliance with industry standards.
Inspection
PVC conduit connectors should be inspected at least once a year or more frequently in harsh environments (e.g., outdoor installations, high-moisture areas, or industrial settings). During inspection, look for:
- Cracks or fractures due to mechanical stress or UV exposure.
- Loosening caused by temperature fluctuations or improper installation.
- Discoloration or brittleness, which may indicate material degradation.
- Moisture intrusion, especially in sealed connections.
Routine Cleaning
Routine cleaning helps maintain the integrity of PVC conduit connectors. Follow these best practices:
- Use a soft cloth or brush to remove dirt and debris.
- Clean with mild soap and water—avoid harsh chemicals that can weaken PVC.
- For outdoor installations, rinse off accumulated dust and grime periodically.
- Ensure seals and gaskets (if applicable) are free from dirt to maintain water-tight connections.
Replacement
Connectors should be replaced when they show signs of damage, such as:
- Visible cracks, brittleness, or discoloration.
- Loose connections that cannot be securely tightened.
- Signs of overheating or electrical arcing.
- Compromised water-tight seals leading to moisture ingress.
To replace a connector safely:
- Turn off power to the conduit system.
- Carefully remove the damaged connector.
- Install a new, properly sized connector.
- Secure and test the connection before restoring power.
Common Issues and Troubleshooting
Even with proper installation and maintenance, PVC conduit connectors may encounter issues over time. Below are common problems and their solutions.
Connection Failure
Causes:
Improper solvent welding or loose snap-fit connections.
Dirt or debris preventing a proper seal.
Incorrect conduit type or size for the connector.
Solutions:
Reapply solvent cement if the bond is weak.
Ensure the connector is fully seated and locked in place.
Use the correct connector type for the conduit material.
Connector Breakage
Causes:
Excessive mechanical stress or impact.
Prolonged exposure to UV light (outdoor installations).
Low-temperature brittleness in extreme cold environments.
Solutions:
Use UV-resistant PVC connectors for outdoor use.
Choose impact-resistant connectors for high-stress areas.
Handle connectors carefully during installation to prevent cracking.
Improper Fitment
Causes:
Using a connector not rated for the conduit size.
Expansion and contraction due to temperature changes.
Manufacturing tolerances causing slight size variations.
Solutions:
Always verify connector sizing before installation.
Allow for thermal expansion by using expansion joints where necessary.
Use approved connectors from reputable manufacturers to ensure compatibility.
By implementing regular maintenance and addressing issues early, PVC conduit connectors can continue to perform safely and effectively, minimizing system failures and ensuring compliance with electrical safety standards.
Where to Buy PVC Conduit Connectors
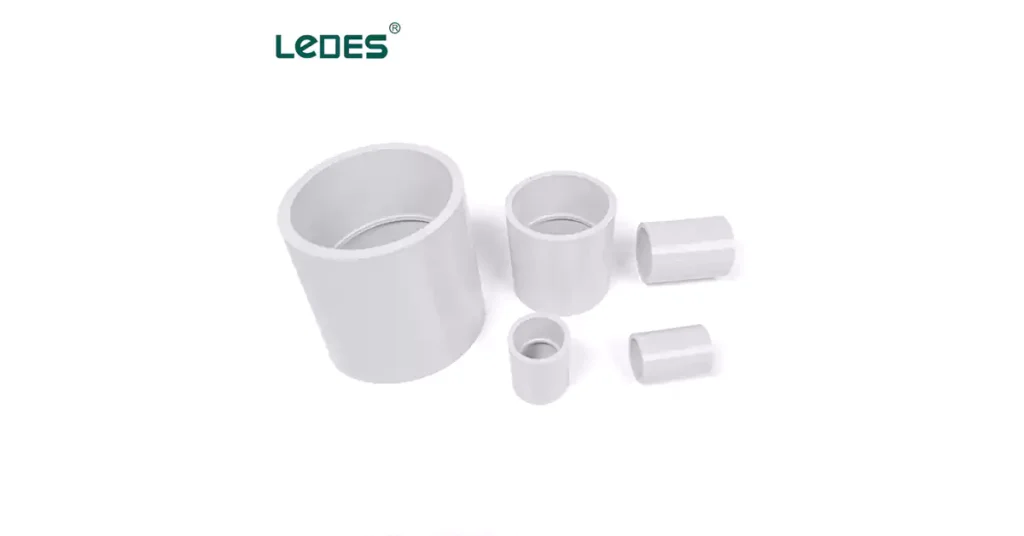
When purchasing PVC conduit connectors, selecting a reliable supplier is crucial to ensuring product quality, compliance with industry standards, and long-term performance. Several top manufacturers and suppliers provide high-quality electrical fittings, including conduit connectors, for various applications.
Top 5 PVC Conduit Connector Suppliers and Manufacturers
Cantex
A leading U.S.-based manufacturer specializing in PVC electrical conduit and fittings.
Offers a wide range of UL-listed conduit connectors, couplings, and adapters for commercial and industrial use.
Known for its durable, high-quality products that meet NEC and UL requirements.
IPEX
A major provider of thermoplastic piping and electrical solutions in North America.
Supplies PVC conduit connectors designed for residential, commercial, and industrial applications.
Offers corrosion-resistant fittings that comply with CSA and UL standards.
A global supplier with a strong focus on low-smoke, halogen-free, and solar conduit fittings.
Provides heavy-duty and UV-resistant conduit connectors for demanding environments.
Offers a full range of electrical conduit solutions, including connectors compliant with UL, CSA, and IEC standards.
JM Eagle
One of the largest manufacturers of PVC pipes and fittings in North America.
Supplies a broad range of electrical conduit and fittings, including Schedule 40 and Schedule 80 PVC conduit connectors.
Known for its high-strength, corrosion-resistant products.
Vinidex
A key supplier of plastic piping systems in Australia, offering a variety of PVC conduit solutions.
Provides AS/NZS-compliant PVC connectors for electrical installations.
Offers robust conduit solutions for both underground and above-ground applications.
What to Look for When Purchasing PVC Conduit Connectors
When selecting PVC conduit connectors, consider the following factors to ensure you get the right product for your application:
Compliance with Standards
Ensure the connectors meet UL, CSA, IEC, or AS/NZS standards, depending on regional requirements.
Look for UL-listed or CSA-certified markings for safety assurance.
Material Quality
Choose high-impact, UV-resistant, and flame-retardant connectors for outdoor and industrial environments.
Low-smoke, halogen-free options are ideal for safety-critical applications.
Compatibility
Match the connector type with your conduit (e.g., rigid PVC, ENT, or liquid-tight).
Ensure the correct size and threading for secure installation.
耐用性和耐环境性
For outdoor use, select UV-stabilized connectors that can withstand harsh weather conditions.
In chemical or high-moisture environments, look for connectors with corrosion and moisture resistance.
易于安装
Consider connectors with quick-lock mechanisms or threaded designs for easy installation.
Check for pre-lubricated or pre-assembled options to save installation time.
By selecting high-quality connectors from reputable manufacturers and considering key factors like compliance, durability, and compatibility, you can ensure a secure and long-lasting electrical conduit system.
结论
PVC conduit connectors play a crucial role in ensuring safe, efficient, and long-lasting electrical installations. By providing secure connections, protection against environmental factors, and compliance with industry standards, these connectors help maintain the integrity of conduit systems across residential, commercial, and industrial applications.
When selecting PVC conduit connectors, it’s essential to consider factors such as compliance with UL, CSA, IEC, or AS/NZS standards, durability, material quality, and ease of installation. Choosing high-quality connectors from reputable manufacturers ensures reliable performance and reduces the risk of connection failures, breakage, or improper fitment.
For installation, following best practices—such as properly securing fittings, ensuring tight connections, and conducting regular inspections—helps maintain the system’s efficiency and safety. Additionally, adhering to NEC, IEC, or local electrical codes guarantees compliance and minimizes potential hazards.
By selecting the right PVC conduit connectors, installing them correctly, and maintaining them over time, you can ensure a safe, efficient, and code-compliant electrical system for any application. Always prioritize quality and best practices to achieve long-term reliability in your conduit installations.
常见问题解答:
How do I connect a PVC conduit to an electrical box?
Connecting PVC rigid conduit to an electrical box often require a terminal male adaptor, using PVC cement to connect with one end of adaptor, and connect the thread end of adaptor to the box. The detailed installation steps can check the installation guide part of this article.
What is flexible conduit connector?
一个 柔性导管连接器 is a fitting designed to join 柔性导管 to an electrical box, enclosure, or another conduit. It helps secure and protect wiring while allowing for movement and vibration resistance.
Types of Flexible Conduit Connectors
- Snap-in Connectors – Quick and easy installation, commonly used for ENT(电气非金属管).
- Threaded Connectors – Screw-on type for liquid-tight 和 flexible metallic conduits (FMC).
- Compression Connectors – Provide a tight seal for liquid-tight flexible conduit (LFMC) to keep out moisture.
- Set-Screw Connectors – Use a small screw to clamp onto the conduit.
- Clamp Connectors – Have a clamp mechanism to hold the conduit securely.