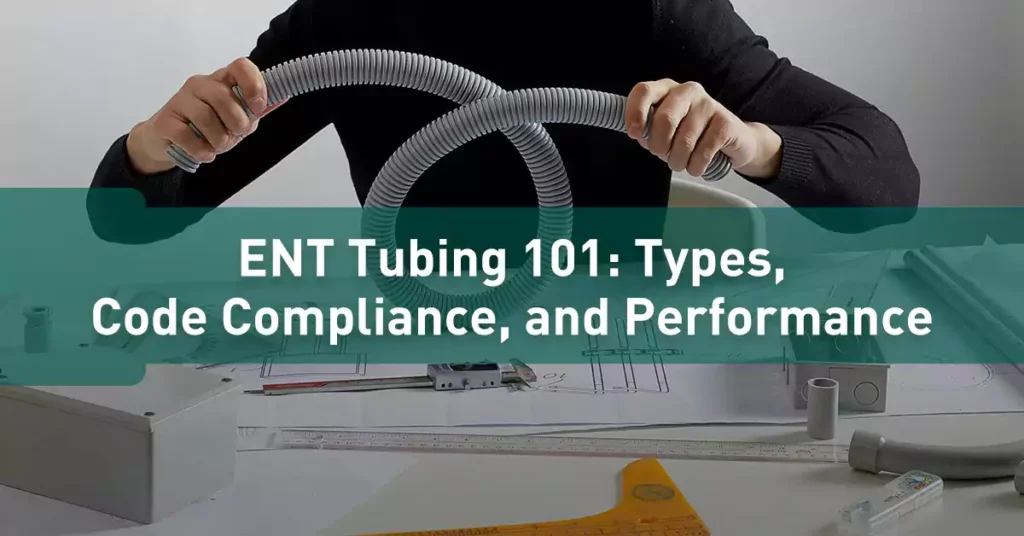
目录
In electrical installation systems, conduits play a crucial role in protecting and routing electrical wiring, ensuring safety and performance across various applications. Among the many types of conduits available, Electrical Nonmetallic Tubing (ENT) stands out for its flexibility and ease of use. ENT tubing has become a popular choice in residential, commercial, and even industrial projects due to its lightweight nature and durability.
This article delves into the essential aspects of ENT tubing, providing a comprehensive overview that includes its definition, key standards, and performance requirements. By exploring the UL and AS standards that govern ENT tubing, comparing these standards, and examining the advantages and disadvantages, this article will equip you with valuable knowledge. You’ll also learn about ENT’s applications, installation guidelines, and fittings, as well as receive insights into how this type of tubing integrates with emerging technologies like renewable energy and automotive conduit systems. Finally, the article discusses current trends and future innovations in the field, ensuring you have a thorough understanding of ENT tubing’s role in modern electrical infrastructure.
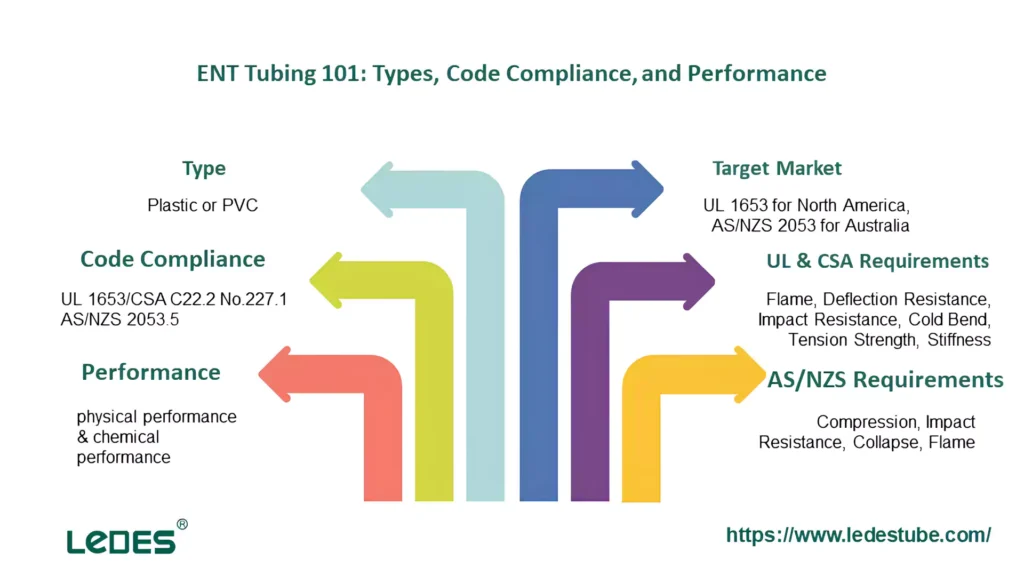
在您的网站上分享此图片
电气非金属管 (ENT) is a flexible, lightweight conduit used to protect and route electrical wires in both residential and commercial applications. Made from polyvinyl chloride (PVC) or other flame-retardant plastics, ENT is designed to be easily bendable and is resistant to impact, moisture, and chemical exposure. ENT is primarily utilized in environments where a rigid conduit would be cumbersome or challenging to install, offering an adaptable solution for routing electrical conductors through walls, ceilings, and floors.
There are many types of nonmetallic tubing for using in different countries and regions, in this article we will mainly introduce two standards tubing, and get to know the specific safety and performance criteria requirements that they must meet outlined in various national and international standards.
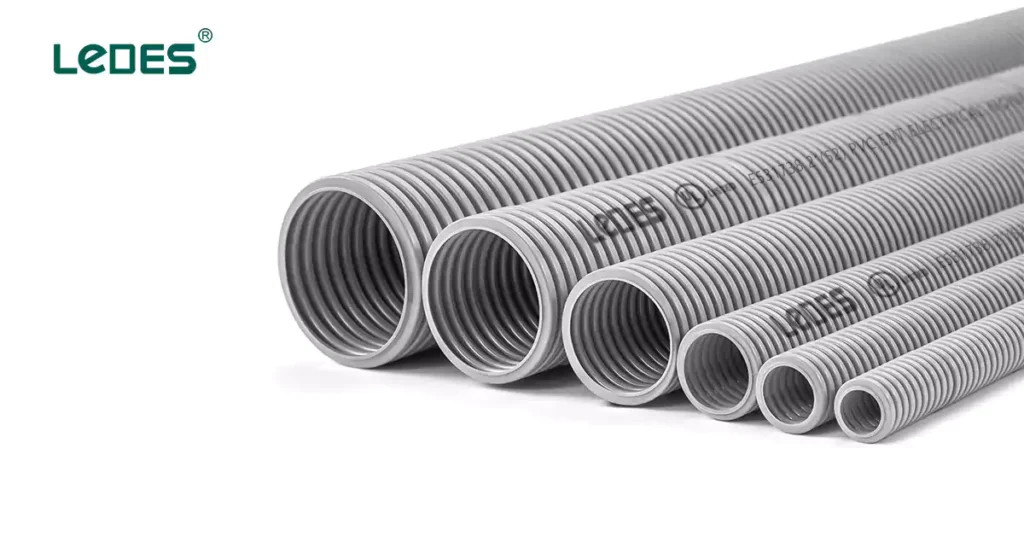
For ENT, the United States and Canada share the same standard, UL 1653/CSA C22.2 No.227.1, these two standards share the same requirements for ENT conduit, just some certain tests are slightly different, this standard outlines the safety and performance requirements for electrical nonmetallic tubing. UL-certified ENT must adhere to the National Electrical Code (NEC) Article 362, which specifies installation guidelines and limitations to ensure safe use in building construction.
If you would like to learn more about UL/CSA standard ENT conduit, you can read our last post on the ENT conduit guide for the USA and Canada.
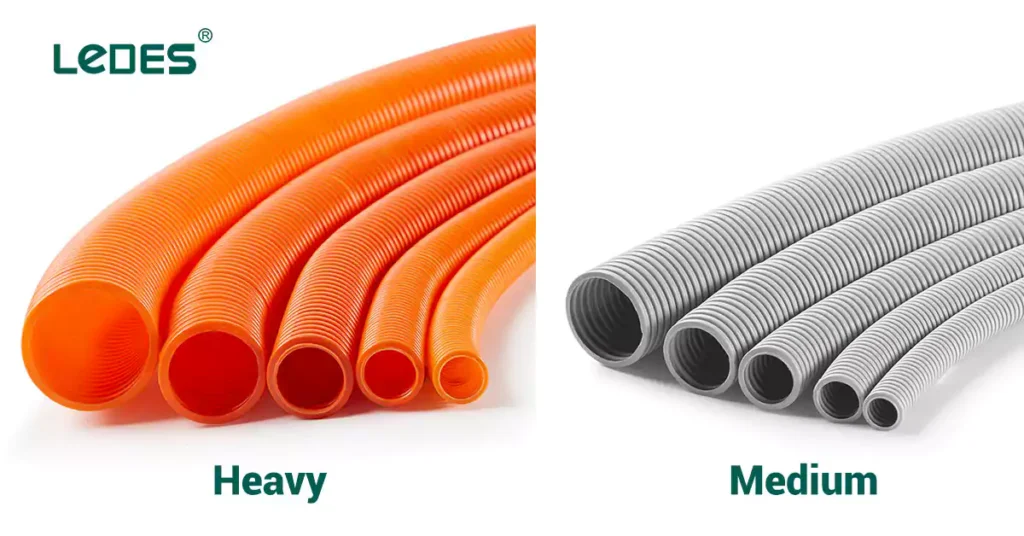
The AS/NZS 2053.5 standard is used in Australia and New Zealand for non-metallic conduits and fittings. Different from the ENT in UL1653, in order to meet different needs, in the AS/NZS standard corrugated conduit are divided into several grades according to different application scenarios, such as light, medium, heavy, etc., and their various performance strengths are also different. This standard includes requirements for thermal properties, mechanical strength, and resistance to environmental factors.
UL1653 has specified all the dimension and performance requirements for ENT, here are some most important aspects you should know:
There are two tests of flaming in UL1653, FT4 test is optional, but it is favored by most people that if the ENT conduit passed FT4 test. Here are some information for these two tests:
- Vertical Flame Test (500 W burner): In clause 7.2, UL1653, the vertical flame test assesses the conduit’s performance when subjected to direct flame exposure under controlled conditions. This test is conducted by positioning a sample of the conduit vertically and applying a 500-watt flame at the base for a specific duration. The primary objective is to observe whether the flame self-extinguishes after the source is removed and to ensure that the flame spread does not exceed specified limits.
- Flame Test in Cable Trays (FT4): The FT4 flame test is specified in clause 7.3, and the test method is according to CSA C22.2. No.211.0. The test simulates conditions found in cable trays, where wiring and conduits are often grouped closely together. This test assesses whether the conduit can prevent flames from spreading across bundles of cables and conduits under fire exposure. The setup involves placing conduit samples in a cable tray configuration and applying a substantial flame source to test flame spread under more challenging conditions.
The requirements for this test are stringent. The test determines whether the tubing can resist flame spread when exposed to high-intensity flames for a set period, and it must meet criteria for self-extinguishing and limited char length. Passing the FT4 test signifies that the ENT tubing provides reliable fire resistance in scenarios where multiple cables and conduits are present, reducing the risk of fire escalation in complex electrical systems.
Deflection resistance is a critical parameter that ensures the durability and mechanical stability of Electrical Nonmetallic Tubing (ENT) under compressive forces. Clause 7.5 of the UL 1653 standard outlines the specific procedures and conditions for testing ENT’s resistance to deflection, providing assurance that the tubing can withstand external loads without significant deformation or structural failure.
General Requirements (Clause 7.5.1):
- The test requires six samples of each trade size of ENT tubing, with each sample cut to a length of 150 ± 3 mm (6 ± 1/8 inches).
- Each sample is subjected to a specific load, varying by trade size:
16 (1/2) trade size: 4448 N (1000 lbf)
21 (3/4) trade size: 3470 N (780 lbf)
27 (1) trade size: 3380 N (760 lbf)
35 (1-1/4) and larger trade sizes: 1779 N (400 lbf)
- Canadian Specific Requirement: For the 63 (2-1/2) trade size, six samples are subjected to a load of 1334 N (300 lbf). This requirement is specific to Canada and does not apply in the United States.
Testing Procedure (Clause 7.5.3)
The procedure for testing deflection resistance is as follows:
- Initial Measurement: Measure and record the inside diameter of the ENT sample.
- 定位: Place the sample between the platens of the compression machine, aligning the inside diameter perpendicularly to the platens.
- 加载应用程序: Operate the machine until the specified load for the trade size is applied.
- Measurement During Load: Stop the machine, remeasure the inside diameter, and calculate the percentage decrease in the diameter.
- 观察: Monitor the sample for any signs of buckling during the test.
- Post-Test Examination: After releasing the load, remove the sample and inspect it for any cracking or damage.
The impact resistance of Electrical Tubing is an essential performance characteristic, particularly for installations where physical force or environmental conditions may challenge the integrity of the conduit. The UL 1653 standard outlines specific tests to assess the impact resistance of ENT, ensuring that it can withstand mechanical stress without significant damage. The impact test is detailed in clause 7.6 of UL 1653, which provides clear guidelines for how samples are prepared, tested, and evaluated.
General Requirements:
- ENT samples must be tested under controlled conditions at a temperature of -20 ± 1°C (-4 ± 1.8°F). This low-temperature requirement simulates conditions where the conduit might be exposed to cold environments, ensuring it maintains its structural properties in such scenarios.
- The impact test applies an energy force of 2.7 Joules (2.0 ft-lbf) to each sample to evaluate its resistance to breakage or deformation.
- Each test sample must be cut perpendicular to its longitudinal axis, with a required length of 150 ± 6 mm (6 ± 1/4 inches) to standardize testing.
- No more than two out of ten samples tested shall show cracks, chips, or ruptures on the inside or outside of the sample.
The ability of ENT to pass these stringent impact tests supports its use in both standard and challenging applications, confirming that it remains functional and effective even under conditions that may induce mechanical stress.
The cold bend test is an essential evaluation to confirm that Electrical Nonmetallic Tubing (ENT) can maintain its flexibility and structural integrity when bent at low temperatures, simulating harsh environmental conditions. This ensures that the conduit will not crack, chip, or rupture when exposed to bending stress in cold climates. The UL 1653 standard specifies the cold bend test under clause 7.7, detailing procedures and requirements for conducting this test.
Clause 7.7 – Test Description:
- The cold bend test requires six samples of each trade size of ENT tubing to be tested. These samples must be conditioned to simulate real-world cold temperature exposure.
- Each sample is bent 360° around a mandrel with a specified radius, which varies depending on the trade size of the ENT. The mandrel radius specifications are listed in Table 2 of UL 1653, ensuring standardized testing for various tubing sizes.
- Before bending, both the samples and the mandrel are conditioned at a temperature of -20 ± 1°C (-4 ± 1.8°F) for 4 hours. This conditioning ensures that the material reaches and maintains a uniform low temperature throughout the testing period.
- The bending process is conducted while the samples and the mandrel are still at this low temperature, ensuring the test accurately reflects the tubing’s performance under cold environmental conditions.
Test Requirements: During the test, the samples must be bent smoothly around the mandrel without causing damage. Specifically, no sample should crack, chip, or rupture during or after the bending process.
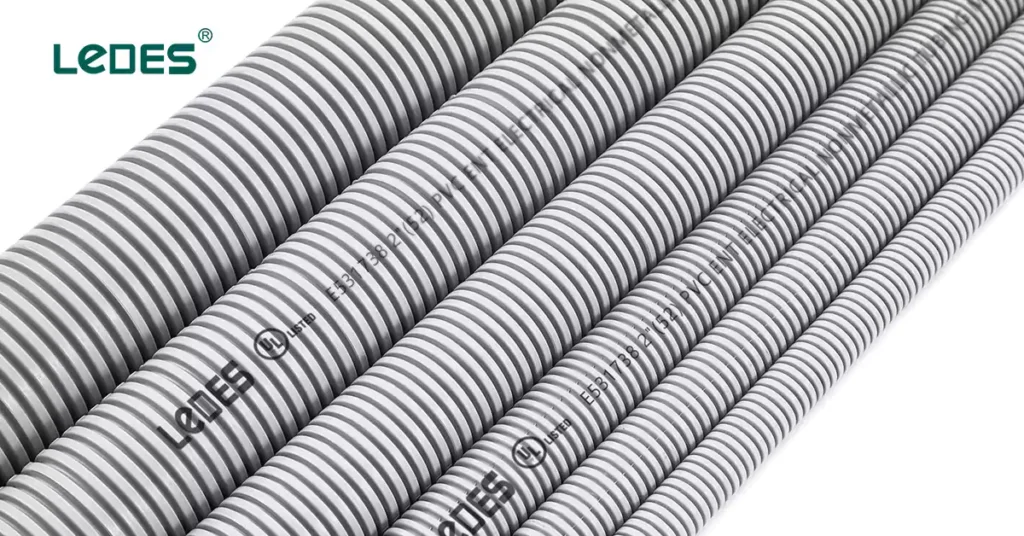
The tension test outlined in clause 7.8 of UL 1653 evaluates the ability of Electrical Nonmetallic Tubing (ENT) to withstand axial forces without breaking. This test ensures that the tubing can endure mechanical tension stresses that may occur during installation or in service without compromising its structural integrity.
Testing Application:
- For smaller trade sizes, 16 (1/2) and 21 (3/4), a 90 kg (200 lb) mass is attached to one end of the conduit to create a tension force of 889 N (200 lbf). The mass is lifted off the floor by pulling on the opposite end, and the load is maintained for 1 minute.
- For larger trade sizes, 27 (1) and above, a 135 kg (300 lb) mass is used, creating a tension force of 1,334 N (300 lbf), with the same one-minute hold requirement.
Performance Criteria
The ENT tubing must withstand the applied tension force for 1 minute without breaking or showing significant structural damage. This demonstrates the conduit’s ability to handle tensile stresses during handling, installation, or use.
The stiffness of Electrical Nonmetallic Tubing (ENT) is an important property that reflects its ability to resist deformation under load. This characteristic is essential for ensuring the conduit maintains its structural integrity when installed, especially in underground applications where external forces, such as soil pressure, are present. The stiffness requirement is particularly significant in Canada and is outlined in clause 5.10 of UL 1653.
要求:
- In Canada, ENT must meet a minimum pipe stiffness of 300 kPa at 5% deflection. This requirement is tested in accordance with ASTM D 2412, which specifies the standard method for determining the stiffness of plastic pipes by measuring the force needed to cause a specified deflection of the conduit.
- In the United States, this stiffness requirement does not apply. While ENT used in U.S. applications must still meet other performance and safety criteria set forth in UL 1653 and the National Electrical Code (NEC), a specific stiffness value for direct burial is not mandated.
Compression test is to ensure that the tubing can withstand applied mechanical pressure while maintaining structural integrity. It helps verify the conduit’s capability to endure external loads without compromising its protective function over electrical wiring.
Test Requirements:
According to AS/NZS 2053.5 and AS/NZS 2053.1, the 波纹软管 should comply with follow requirements:
- General Objective: The conduit must demonstrate resistance to compression by not undergoing excessive deformation when subjected to a specified force.
- Deformation Limit: The critical requirement for passing this test is that the difference between the initial outside diameter of the conduit and the diameter measured while the force is still applied must not exceed 25%. This ensures the conduit retains adequate mechanical properties under stress and does not deform beyond an acceptable threshold.
导管 | Compression force (N) |
非常轻 | 125 |
光 | 320 |
中等的 | 750 |
重的 | 1250 |
Very Heavy | 4000 |
The AS/NZS 2053.1 standard outlines a specific set of impact test requirements that assess the ability of the nonmetallic corrugated conduit to withstand mechanical impacts without compromising their structural integrity.
Apparatus and Test Pieces
Conditioning Chambers: Two chambers that can maintain the conduit’s maximum and minimum service temperatures with a ±2°C tolerance. These chambers are used to simulate extreme temperature conditions before impact testing.
Impact Test Apparatus: Includes a base with a steel plate and a hammer set to specified weights and fall heights.
Sponge Rubber Pad: A 40 mm thick pad under the apparatus to absorb shock.
The test is conducted on 12 lengths of conduit, each 200 mm long, or on 12 assembled fittings that include all components as they would be used in real-life applications.
Procedure for Impact Testing
- Conditioning the test piece at the maximum service temperature for 240 hours in Chamber 1.
- Transferring the test piece to Chamber 2, where it is conditioned at the minimum service temperature for at least 2 hours or until it matches the chamber’s air temperature.
- Placing the test piece on the steel base and applying the intermediate steel piece.
- Dropping a hammer of specified weight and height to simulate impact.
The weakest part of fittings is targeted for testing, but impacts are avoided within 5 mm of any socket mouth.
Mechanical property | Weight of the hammer kg | Fall height mm |
非常轻 | 0.5 | 100 ±1 |
光 | 1.0 | 100 ±1 |
中等的 | 2.0 | 100 ±1 |
重的 | 2.0 | 300 ±1 |
很重 | 6.8 | 300 ±1 |
验收标准
At least 9 out of 12 test pieces must show no signs of cracking or disintegration when visually inspected with normal or corrected vision, without magnification.
Meeting these stringent criteria ensures that nonmetallic corrugated conduits provide consistent performance and durability, maintaining their protective qualities under mechanical stress.
The collapse test is a crucial evaluation in the AS/NZS 2053 series, which confirms that the metallic tubing can withstand environmental stress without compromising its internal diameter or structural form.
管道塌陷测试程序
- 弯曲样品:
在室温下使用指定的弯曲装置小心地将 ENT 管弯曲至 90°。
- 保护样本:
使用四条带子将弯管固定到刚性支架上,如标准图所示。
取出用于弯曲管子的所有工具。
- 加热样品:
将带有管子的支架放入温控室中。
将腔室保持在制造商建议的最高温度 (±2°C) 下 24 小时。
- 检查样本:
将带有管子的支架从腔室中取出。
测量内径以确保其符合标准的最低要求。
验收标准
如果 AS/NZS 2053 系列相关部分中概述的量规能够成功穿过导管,则 ENT 样品通过了塌陷测试。这证明管道保持了其形状和内部间隙,确认了其在热应力下的弹性。
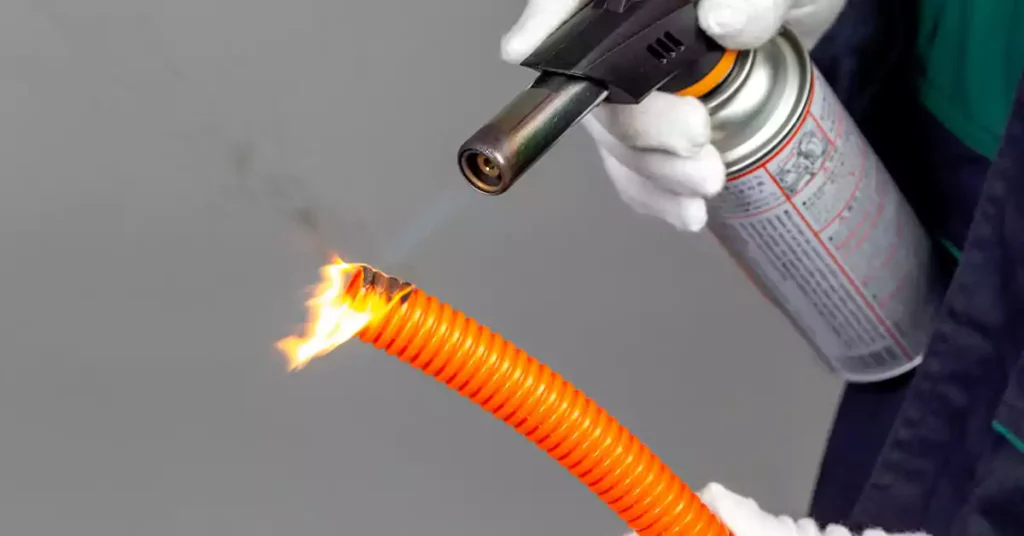
波纹管必须具有足够的抗火焰蔓延能力,才能被视为不抗火焰蔓延,如 AS/NZS 2053.5 和 AS/NZS 2053.1 所规定的那样。阻燃性测试涉及以下要点:
火焰应用:
- 将 1 kW 火焰以 45° 角施加到样品上,放置在距离样品 100 ±10 毫米的位置,并瞄准下夹具上方 100 ±5 毫米的位置。
- 火焰维持60±1秒,然后移开。
测试标准:
- 此项测试针对三个样品进行。
- 如果样品没有点燃或者在火焰移除后 30 秒内燃烧停止,则表示样品通过。
- 样品在距夹具 50 毫米的范围内不应出现烧焦或燃烧现象。
- 样品下方的薄纸点燃表明失败。
遵守:
为了符合要求,波纹管样品在火焰移除后不得出现持续燃烧,夹具附近不得出现烧焦现象。熔化材料的存在并不构成不合格,除非导致样品本身燃烧或烧焦。
用于柔性非金属导管比较的两个主要基准是电气非金属管 (ENT) 的 UL(保险商实验室)标准和管理澳大利亚和新西兰使用的非金属波纹导管的 AS/NZS 2053.5。虽然这两种导管类型的基本用途都是保护电线,但它们在尺寸、强度和性能方面都经过量身定制,以满足各自标准规定的不同要求。
比较 UL 标准电气非金属管和 AS/NZS 2053.5 非金属波纹管时,在以下方面会出现明显区别:
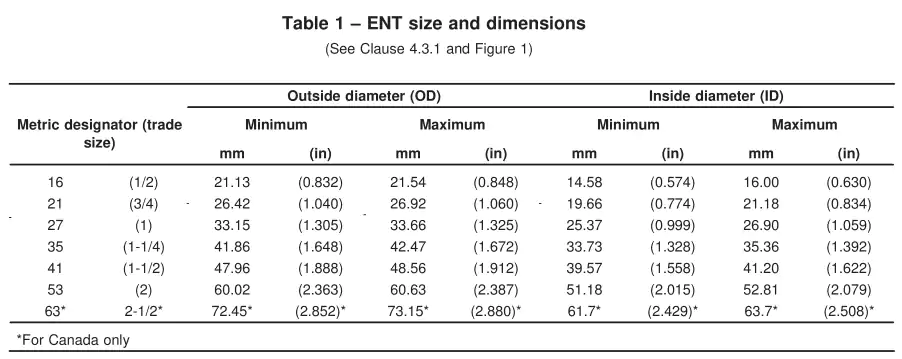
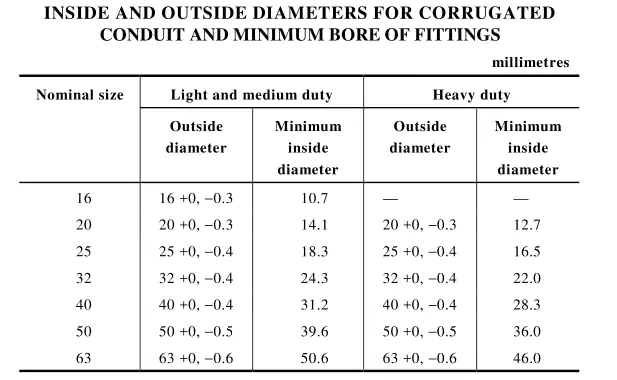
可以看出,虽然它们由相同的材料制成,并且名称几乎相同,但尺寸差异却很大。即使尺寸接近,但考虑到公差,它们几乎完全不同。
抗挤压和冲击性能:
UL 耳鼻喉科: 概述了具有特定负载阈值的严格抗压测试,以确保导管可以承受压力而不会发生永久变形。
AS/NZS 2053.5 灵活: 采用适用于不同环境下使用的导管的冲击测试,特别关注温度弹性和压缩后的恢复。
方面 | UL1653 | AS/NZS 2053 |
测试温度 | -20 ± 1°C (-4 ± 1.8°F) | 最高和最低使用温度 |
样本 | 长度150±6毫米,垂直切割 | 200 毫米长,12 个样品 |
冲击能量 | 2.7 Joules (2.0 ft-lbf) | 可变(0.5 千克至 6.8 千克锤子) |
调节时间 | 至少 4 小时 | 最高温度下 240 小时,最低温度下 2 小时以上 |
样本数量 | 10 个样品 | 12 个样品 |
验收标准 | 10 个中最多有 2 个会显示损坏 | 12 项中至少有 9 项必须通过 |
检查方法 | 目视,无需放大 | 目视,无需放大 |
UL 耳鼻喉科: 包括UL 94阻燃性测试等测试,以确保管道符合消防安全规定。
AS/NZS 2053.5: 指定耐火性测试,重点关注自熄性,以最大限度地降低火焰蔓延的风险。
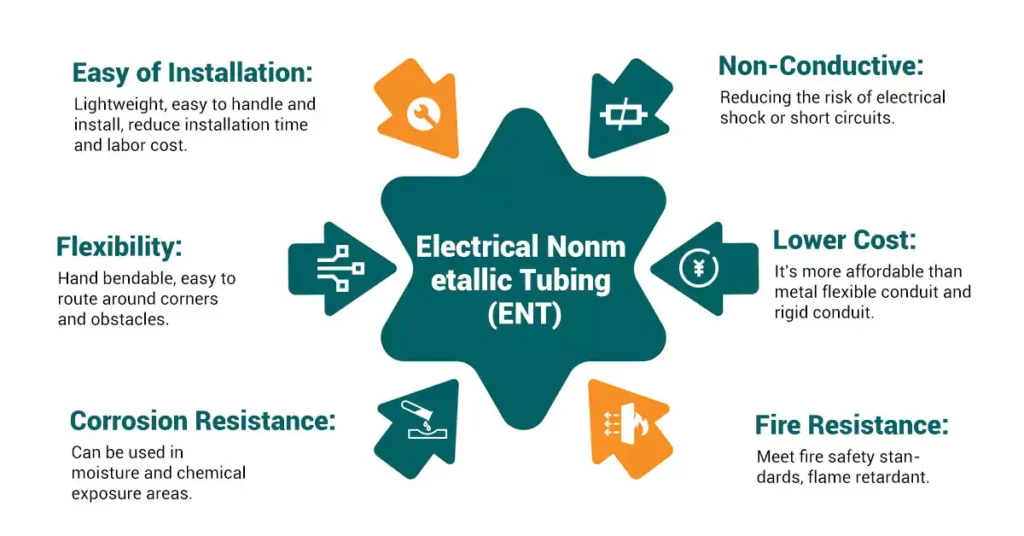
重量轻且易于安装:
ENT 比金属导管轻得多,因此易于搬运和安装。这可以减少人工成本和安装时间,尤其是在大型项目中。
- 灵活性:
其固有的灵活性使 ENT 能够绕过障碍物,而无需复杂的配件或接头,从而简化了安装过程并降低了材料成本。
- 耐腐蚀性:
ENT 具有很强的耐腐蚀性,使其成为地下室和沿海地区等容易受到潮湿或化学物质影响的环境的绝佳选择。
- 非导电特性:
作为非金属导管,ENT 不导电,可降低电线损坏时发生触电或短路的风险,从而提供更安全的选择。
- 降低成本:
ENT 通常比刚性金属导管 (RMC) 或中间金属导管 (IMC) 更实惠,使其成为标准电气安装的经济解决方案。
- 防火性:
ENT 在经过适当评级后可以满足消防安全标准,并具有阻燃性能,可在发生火灾时增强安全性。
机械强度较低:
ENT 不像金属导管那样坚固,因此不太适合需要高机械强度的应用,例如可能受到重冲击或压缩的区域。
- 有限的温度耐受性:
ENT 在高温或低温下性能可能会下降。除非专门为此类条件设计,否则在极冷环境下,ENT 会变脆,在高温下会变形。
- 紫外线敏感度:
除非使用紫外线稳定剂处理,否则 ENT 可能会在阳光直射下随时间而降解。这限制了其在没有额外保护措施的情况下在户外安装中的使用。
- 不适合某些环境:
在一些存在火灾隐患或接触可能降解塑料的化学物质的高压力或工业应用中,ENT 可能无法满足必要的安全性和耐用性标准。
- 支持和安装要求:
ENT 必须在整个长度范围内得到适当支撑,以防止随着时间的推移而下垂或损坏。这会增加安装的复杂性,尤其是在需要长距离运行的情况下。
电气非金属管材为许多电气安装需求提供了灵活、经济高效且耐腐蚀的解决方案。然而,必须考虑其局限性,特别是在机械强度和环境暴露方面,以确保其适用于特定应用。了解这些优缺点有助于做出明智的决定,确定何时何地在电气项目中使用 ENT。
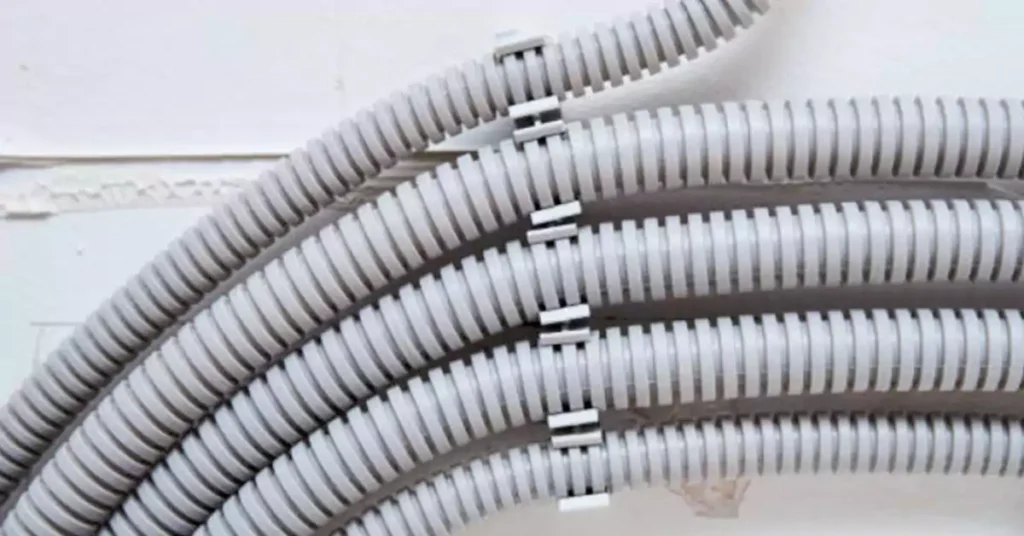
安装非金属电气管道需要仔细规划和执行,以确保电线得到适当的保护和功能。国家电气管道委员会 (NEC) 已概述了 ENT 的安装指南,该过程通常很简单,涉及一系列准备和安装步骤。以下是一般安装步骤:
安装 ENT 导管共有 8 个步骤:
- 规划安装路径: 识别并标记导管的路线。
- 切割管道: 使用导管切割器或细齿锯测量并将 ENT 切割至所需长度。
- 去掉末端毛刺: 将切割端的粗糙边缘打磨光滑,以防止损坏电线。
- 连接配件和联轴器: 连接配件以连接 ENT 段并确保连接牢固。
- 定位并固定 ENT: 将管道沿着计划的路径放置,并定期用夹子或支架固定。
- 拉电线: 使用鱼带将电线拉过 ENT,确保没有急剧弯曲或扭结。
- 连接到电气箱: 将 ENT 牢固地连接到电气箱和外壳。
- 检查并完成安装: 进行最后检查,检查是否有适当的支撑、安全的配件以及是否符合电气规范。
安装前您需要了解6件事:
支撑和间距: 确保 ENT 得到定期支撑,通常间隔不超过 3 英尺,以防止管道下垂或受力。
避免急弯: 避免过度弯曲管道,否则会限制电线移动并造成损坏。必要时使用专为转弯设计的接头。
温度考虑因素: 请勿将 ENT 安装在低于其额定最低温度的地方,或在没有适当热保护的情况下暴露在极热环境中的区域。
紫外线照射: 对于室外安装,请确认管道符合紫外线照射等级或采取额外的保护措施,例如将其放在盖子下。
正确固定配件: 使用经批准的配件和连接器将 ENT 固定到配电箱或接线端子上。连接不当的配件可能会导致导管断开和电气危险。
验证代码合规性: 始终确保安装符合当地电气规范要求,其中可能指定有关导管放置、电线容量和连接方法的额外指导原则。
通过遵循这些安装步骤和注意事项,电工和安装人员可以实现符合安全和性能标准的安全可靠的 ENT 安装。
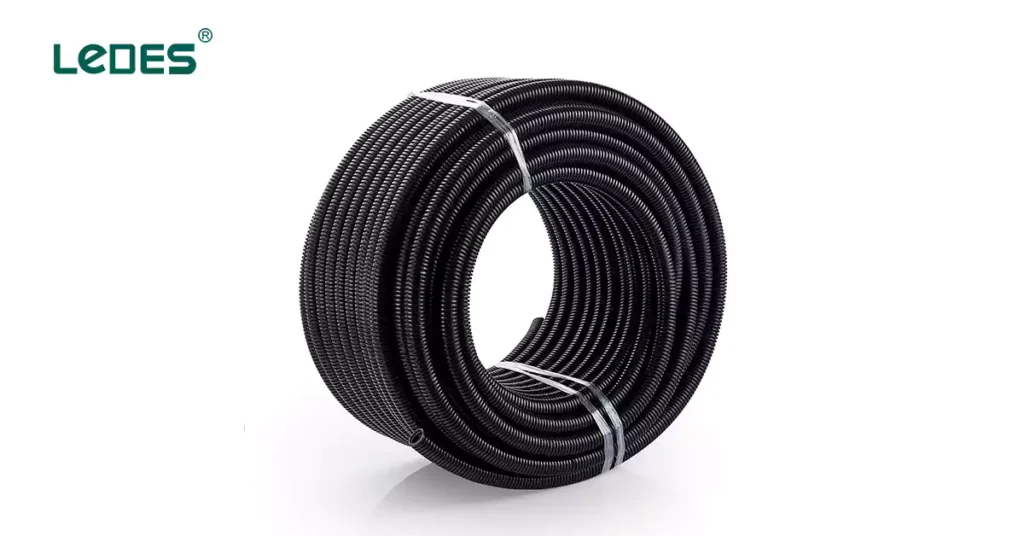
购买电气非金属管材有6个技巧,
- 了解应用程序:
室内或室外使用:确保 ENT 适合安装环境,例如干燥、潮湿或室外空间。
电线容量:根据需要保护的电线数量选择合适的尺寸。
- 检查材质和等级:
塑料的质量:寻找由坚固耐用、能够耐火和耐化学品的塑料制成的 ENT。
标准合规性:确保产品符合 UL(美国)或 AS/NZS(澳大利亚/新西兰)等行业标准。
- 考虑灵活性和安装:
选择足够灵活以绕过障碍物但仍然坚固的 ENT。
确保使用标准工具可以轻松切割和操作。
- 寻找耐用性:
Impact Resistance: Choose tubing that won’t easily crack or dent.
UV Protection: For outdoor use, make sure it’s protected against sun damage.
- Balance Cost and Quality:
Don’t just go for the cheapest option. Higher-quality ENT often lasts longer and performs better, which can save money over time.
- Check Compatibility:
Make sure the ENT can be used with standard fittings and connectors.
The future of Electrical Nonmetallic Tubing (ENT) is set to expand into areas that support sustainability and smart technologies. Here are some key trends:
- Renewable Energy Systems
ENT is expected to play a bigger role in renewable energy installations, such as solar and wind power systems. These setups often require flexible, non-corrosive conduits that can withstand various weather conditions. ENT’s lightweight and corrosion-resistant properties make it ideal for routing cables in solar farms and wind turbine installations, contributing to cleaner energy infrastructure.
- Green Building Construction
As construction shifts towards greener practices, ENT will be increasingly used in eco-friendly buildings. Sustainable buildings aim to reduce environmental impact and improve energy efficiency, and ENT fits well in these designs due to its recyclable material options and lower overall environmental footprint compared to metal conduits.
- Smart Homes and IoT Integration
ENT is likely to see more use in smart home systems where extensive wiring is needed for sensors, automation controls, and IoT devices. Its flexibility and ease of installation make it a practical choice for accommodating complex wiring setups in homes that incorporate smart technologies.
- Electric Vehicle (EV) Infrastructure
With the growth of electric vehicle charging stations, ENT can serve as a conduit solution for routing power and data cables. Its adaptability and durability help support both indoor and outdoor charging stations, facilitating the expansion of EV infrastructure that is crucial for sustainable transportation.
- Smart Grids and Power Management Systems
ENT’s role may expand in the development of smart grids, which require extensive wiring for data communication and power distribution. These systems rely on real-time data to optimize energy use and improve reliability. ENT’s potential integration with monitoring technologies could help improve the efficiency and manageability of such smart power systems.

The use of Electrical Nonmetallic Tubing (ENT) and other conduits in the electric vehicle (EV) and automotive industries is a rapidly growing area, as these industries adopt more advanced electrical systems. Here’s a closer look at how ENT and similar conduits are being used and their future potential:
- Electric Vehicle (EV) Charging Infrastructure
With the increase in electric vehicle adoption, EV charging stations are becoming more widespread, requiring robust and flexible conduit solutions. ENT and other conduits are used for:
电缆保护: ENT is ideal for protecting charging cables from physical damage and environmental factors. The tubing ensures the safe routing of cables from the power supply to the charging point.
户外耐久性: ENT’s weather-resistant qualities make it suitable for both indoor and outdoor installations, as charging stations often need to withstand harsh environmental conditions such as rain, snow, and UV exposure.
Data and Power Cable Management: For advanced charging stations with smart capabilities (e.g., energy monitoring, payment systems), ENT can protect both the power and data cables that are required for the system to function efficiently.
- Electric Vehicle Wiring Systems
Electric vehicles require extensive electrical wiring for various systems, including the battery management system, motors, charging systems, and sensors. Conduits like ENT are used to:
Cable Routing: ENT is used to route wires in the car’s body, ensuring that sensitive wiring is protected from physical stress, moisture, and temperature fluctuations.
灵活性: The flexibility of ENT allows it to be installed in tight spaces within EVs, such as around motors, batteries, and other critical components. This flexibility helps streamline the assembly process and ensure safety.
Thermal Protection: ENT’s resistance to heat makes it suitable for managing the heat generated by power cables or components in high-performance EVs.
- Automotive Manufacturing
In the automotive industry, conduit systems are essential for organizing and protecting cables that power vehicle electronics. ENT and other conduits help in:
Protection During Manufacturing: ENT protects wiring from potential damage during the manufacturing process, including paint application, mechanical assembly, and other stages.
Flexible Wiring: For complex wiring systems in modern vehicles, ENT’s flexibility allows it to be easily routed through different sections of the vehicle, providing protection against abrasion, cuts, and environmental exposure.
- Battery Storage Systems
As more companies develop energy storage systems for EVs and other renewable energy projects, ENT can play a role in ensuring that the battery systems are properly wired and shielded. ENT is used to route electrical wiring from the batteries to various components, ensuring that these systems remain safe, reliable, and efficient.
- Smart Vehicles and Autonomous Cars
With the development of smart vehicles and autonomous driving technology, the need for reliable and durable electrical systems has skyrocketed. ENT plays a role in:
Data Cable Protection: Autonomous vehicles rely heavily on sensors, cameras, and other connected systems that generate vast amounts of data. ENT can protect the data cables that carry signals from these systems to the vehicle’s central processing units.
Low-Voltage Wiring: As vehicles become more automated and include systems for driver assistance, comfort, and entertainment, ENT is used to protect low-voltage wiring that powers these systems.
Understanding the fundamentals of Electrical Nonmetallic Tubing (ENT) is essential for industry professionals seeking reliable, flexible, and efficient solutions for electrical installations. ENT tubing serves a critical role in both residential and commercial applications due to its lightweight nature, ease of installation, and adaptability.
In this overview, we explored the main types of ENT, their respective uses, and the performance attributes that make them suitable for various environments. Compliance with codes such as UL 1653 and AS/NZS 2053 underscores the importance of meeting stringent safety and performance standards, ensuring that ENT remains a dependable choice even under challenging conditions.
Staying informed on the latest standards and advancements ensures that electrical professionals can leverage the full benefits of ENT tubing, optimizing both safety and efficiency in their projects. And evaluate the project needs before you choose the tubing types, making sure you choose the right one and comply with your local codes.