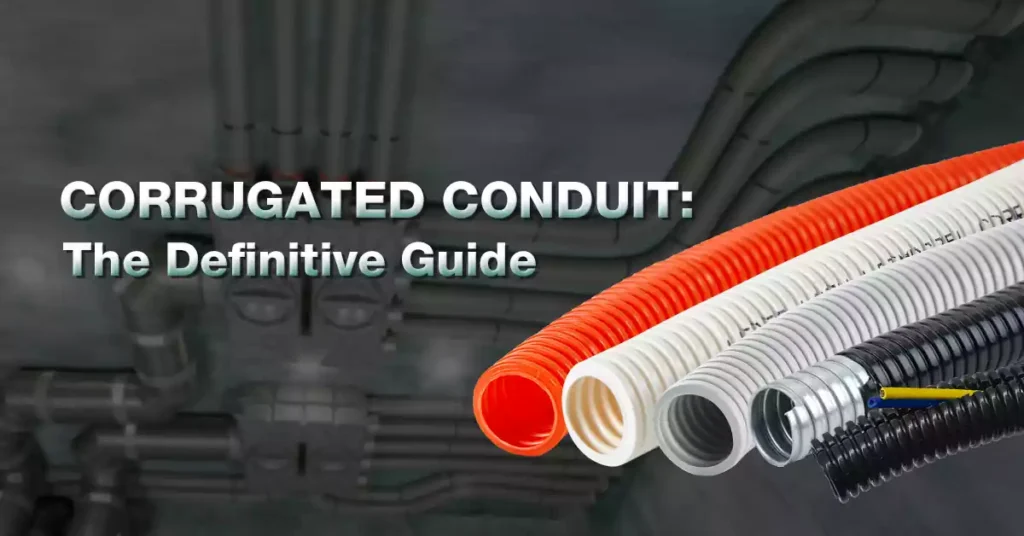
目录
在当今快速发展的技术和基础设施世界中,对可靠、适应性强、耐用的布线解决方案的需求从未如此强烈。进入 波纹管是现代电气和通信系统中用途广泛且必不可少的组件。这种柔性导管以其独特的肋状设计和灵活性而闻名,在保护电缆方面发挥着关键作用,同时适用于各种应用。
从住宅建筑、商业建筑中的导管到电信网络中的通信导管,再到快速发展的电动汽车 (EV) 行业中的电动汽车 (EV) 导管,波纹管已成为需要坚固而灵活的线路保护的项目的首选解决方案。它通常用于电气系统、地下电缆和工业自动化,可保护电线免受环境危害、物理损坏甚至电磁干扰。
波纹管不仅仅适用于传统的电气安装。它在电动汽车充电站、智能电网基础设施和光纤数据网络中的作用凸显了其对尖端技术和新兴行业的适应性。无论您是工程师、承包商还是 DIY 爱好者,了解这种多功能管道对于在项目中做出明智的选择都至关重要。
在本指南中,我们将探索您需要了解的有关波纹管的所有信息,从其基本特性和各种应用到选择和安装正确类型的技巧。最后,您将全面了解这一不可或缺的工具及其在当今电气和通信领域的关键作用。
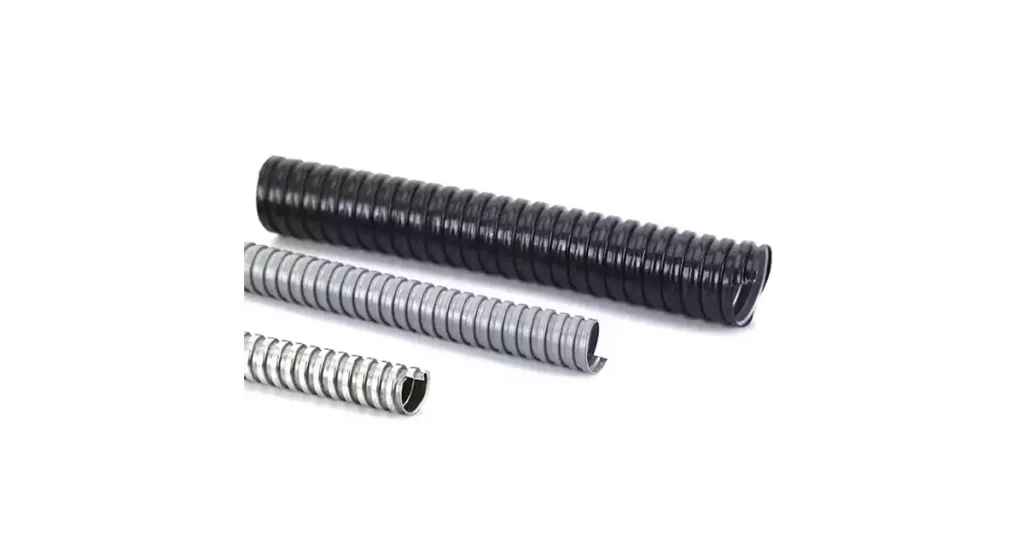
波纹管,也称为柔性管或柔性管,是一种专门设计的保护管,具有肋状波纹外部,可增强柔韧性和强度。这种导管通常由 PVC(聚氯乙烯)、HDPE(高密度聚乙烯)甚至铝和不锈钢等金属制成,可实现适应性和耐用性的平衡。
肋状结构允许导管弯曲和伸缩而不会损害其完整性,使其成为穿过狭窄或不规则空间的理想选择。此外,波纹导管有金属和非金属选项,适合各种应用和环境。
波纹管对于保护电线和电缆免受物理损坏、潮湿和环境危害至关重要,同时保持复杂安装所需的灵活性。以下是这种导管类型的主要目的和用途:
电缆保护: 保护电线和电缆免受物理冲击、振动以及紫外线照射、水侵入和化学腐蚀等环境条件的影响。
复杂路由的灵活性: 非常适合需要弯曲或穿过狭小空间的安装,无需多个配件或接头。
环境安全: 确保电气和通信系统保持绝缘和安全,降低触电或短路的风险。
易于维护和升级: 简化电缆更换或升级,因为导管可以轻松接触内部电线而不会损坏周围的基础设施。
波纹管以其独特的灵活性、耐用性和保护性而闻名,使其成为各种电气应用的多功能解决方案。波纹管最显着的特点是其 罗纹设计,可提供出色的机械保护,防止撞击、磨损和外部压力。这种肋条增强了其抵抗挤压和其他形式损坏的能力,确保在具有挑战性的环境中长期使用。
波纹管的一个突出特点是其 灵活性,可轻松安装在狭窄或密闭空间、拐角处或不平坦的表面上。这种灵活性还减少了对额外配件的需求,使安装更快、更经济。 轻的 波纹管的特性进一步减少了安装工作量和人工成本,使其成为大型项目的理想选择。
除了这些基本的材料优势外,波纹管的一些变体还包括 阻燃 或者 防火 特性,进一步提高了安全性,特别是在存在火灾隐患的环境中。这些防火版本可以帮助防止火势蔓延,为工业或商业环境提供额外的保护。
波纹管也有各种尺寸和颜色,可根据项目的具体要求进行定制。其用途广泛,涵盖从建筑和汽车到电信和制造业等各个行业,表明其应用范围广泛,在电线保护中发挥着重要作用。
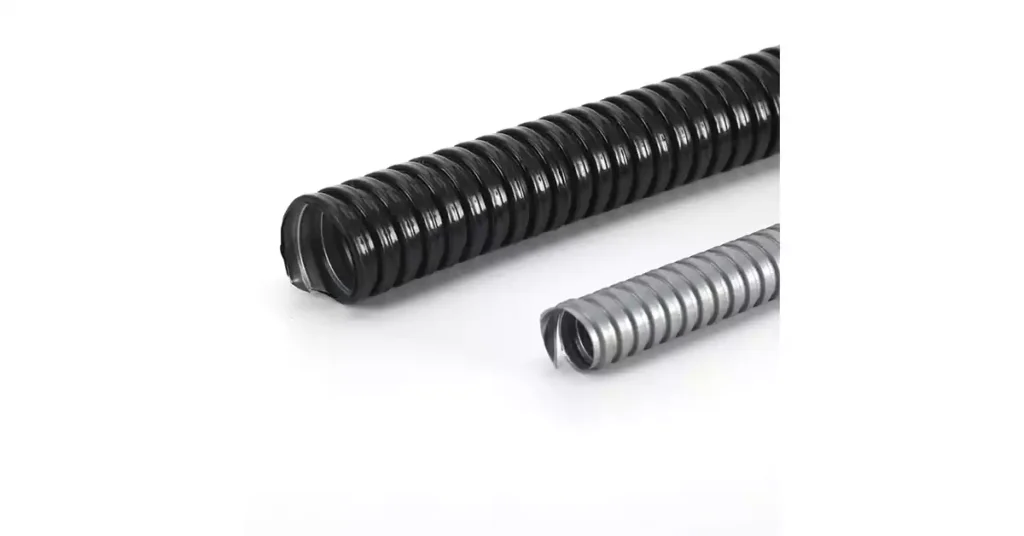
波纹管有多种类型,根据设计目的、材料和应用场景进行分类。每种类型都可满足特定的安装要求,确保布线系统获得最佳性能和保护。
- 标准波纹管
标准波纹管是最常见的类型,旨在为电缆和电线提供基本保护。它具有高度灵活性、重量轻,适用于住宅布线、商业安装和轻工业用途等通用应用。 - 超柔波纹管
Super-Flex 波纹管采用增强型肋状设计,具有更大的灵活性和弯曲半径。这种类型非常适合具有复杂布线要求的安装,例如汽车布线、机器人和狭小空间。 - 分体波纹管
分体波纹管 专为快速简便的安装而设计,无需拉动电缆即可插入。分体式设计方便改装或更换现有系统中的电缆,常用于汽车维修、数据中心改造和临时布线设置。
- PVC波纹管
PVC波纹管 它重量轻、经济高效,并且具有很强的防潮和防化学品性能。它广泛用于住宅和商业设施,在这些设施中,耐用性和经济性是关键考虑因素。 - HDPE波纹管
HDPE(高密度聚乙烯)波纹管具有出色的柔韧性和抗冲击性。其坚固性使其适用于地下安装、室外布线和恶劣环境。 - 聚丙烯(PP)波纹管
PP 波纹管具有出色的耐高温和耐化学腐蚀性能,非常适合需要担心热暴露的汽车和工业应用。 - 聚氨酯(PU)波纹管
PU 导管具有出色的灵活性、耐磨性和耐用性,适用于需要频繁移动或暴露于振动的应用,例如机器人和机械。 - 聚酰胺/尼龙波纹管
聚酰胺(尼龙)导管非常耐用,具有很强的耐磨性、耐化学性和抗紫外线性。它们通常用于汽车布线、重型机械和户外安装等要求严格的应用。 - 金属波纹管
金属导管由钢或铝制成,因其强度和电磁干扰 (EMI) 屏蔽能力而备受推崇。它们用于需要强大机械保护的工业环境中。 - 低烟无卤(LSZH)波纹管
LSZH 导管 最大限度地减少火灾时的有毒气体排放和烟雾,确保数据中心、医院和运输系统等封闭空间的安全。
波纹管是现代电气和通信设备中用途广泛且必不可少的组件。其独特的设计和材料特性使其适用于从住宅项目到大型工业设施的广泛应用。本节深入探讨波纹管的功能和特性,整合 UL 1653、CSA C22.2 NO.227.1、AS/NZS 2053.5 和 IEC 61386-23 等关键认证,以强调其符合行业标准。它还探讨了这些标准所需的主要测试,并介绍了关键的应用场景。
波纹管的一大特色是其出色的柔韧性。得益于肋状设计,这些管子可以轻松绕过狭窄的角落、穿过狭窄的空间并适应不平坦的表面。这种适应性在需要复杂电缆布线的环境中至关重要,例如:
汽车系统: 导管必须安装在复杂的发动机舱内。
工业机械: 确保狭小空间内的无缝电缆管理。
住宅布线: 简化墙壁或天花板后面的安装。
螺旋或肋状结构增强了可弯曲性,同时保持了耐用性,使其成为涉及频繁移动或振动的应用的理想选择。例如,Ledes 柔性 PVC 管电气波纹导管可确保平稳弯曲和一致的电缆完整性。
波纹管经过精心设计,可承受恶劣条件。PVC、聚乙烯和尼龙等材料可抵御:
紫外线辐射: 对于户外安装来说必不可少。
水分和化学物质: 使其成为地下布线和工业环境的理想选择。
极端温度: 允许在从寒冷的冬天到高热机械的区域使用。
AS/NZS 2053.5 和 UL 1653 等标准确认了这些导管在各种环境压力下的耐用性和安全性。Ledes PVC 波纹导管等产品在极端温度和户外条件下具有耐用性,符合 UL 1653 等严格的标准,可抵抗物理损坏和环境退化
防火性是许多应用中的一个重要考虑因素,波纹管通常采用阻燃材料以最大限度地降低火灾危险。低烟无卤 (LSZH) 变体进一步减少了有毒烟雾排放,使其成为以下应用中不可或缺的:
医院和学校: 乘客安全至关重要。
公共交通系统: 地铁和公交车线路安装。
Ledes 电气非金属管和波纹管符合 CSA C22.2 No.227.1 和 IEC 61383 标准,其中包括可燃性测试,确保导管抵抗点火并限制火焰蔓延,从而在易燃环境中提供增强的安全性。
通讯配线
波纹管通常用于保护精密的光纤和通信电缆。其柔韧性和抗环境损害能力可确保电信网络中可靠的数据传输。
电动汽车充电站
电动汽车充电系统的动态特性要求导管能够承受频繁弯曲、天气暴露和潜在的化学品泄漏。专为电动汽车应用设计的波纹导管符合 UL 1653 等标准的严格机械和热测试,确保持久的性能。
建筑和基础设施
波纹管重量轻且易于安装,广泛应用于建筑布线系统。它们能够保护电缆免受物理损坏、紫外线照射和火灾危害,是住宅和商业建筑项目的理想选择。
工业系统
在工厂和仓库中,波纹管可组织和保护线路免受振动、化学物质和机械冲击。符合抗冲击和抗压测试,确保它们在苛刻的环境中可靠地运行。
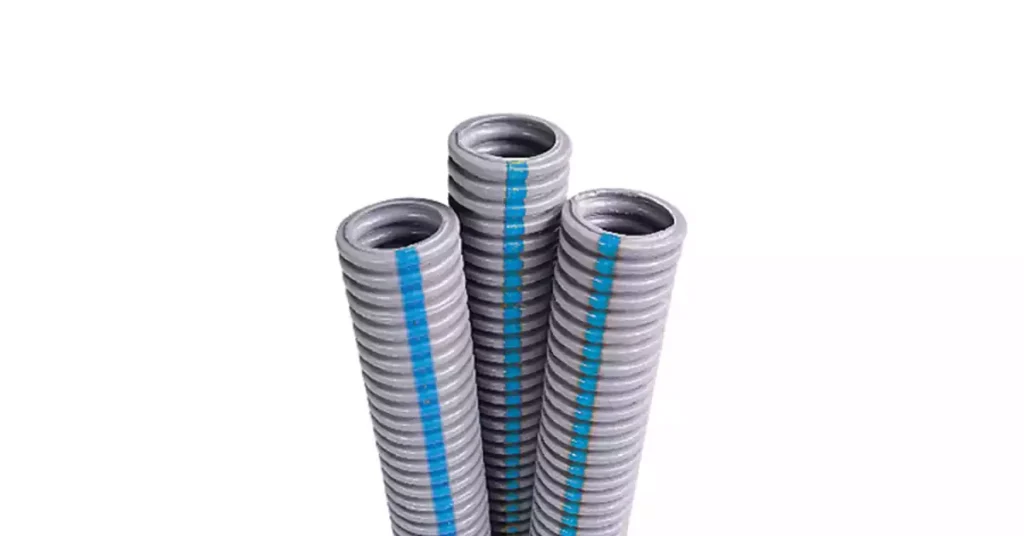
波纹管与任何其他电气安装材料一样,必须遵守当地规范和标准,以确保安全、性能和合规性。这些规范对于定义导管在各种应用中必须满足的技术规格、安装实践和安全措施至关重要。在本节中,我们将介绍一些管理波纹管和柔性导管使用的常见规范,以及它们如何影响其在实际项目中的应用。
在美国,国家电气规范 (NEC) 制定了电气安装的标准,包括柔性导管的使用。 《国家经济法》第 352 条 涵盖刚性非金属导管(包括 PVC 和波纹管变体)。它规定了这些材料应如何用于电线、其物理特性和安装要求。
NEC 第 348 条还管理柔性金属导管 (FMC),确保电气装置中使用的柔性导管符合耐用性、安全性和接地标准。
UL 1653 是专门适用于柔性塑料导管的标准。它详细说明了柔性和波纹导管必须经过的耐火性、环境适用性和性能测试,以确保在各种环境下安全使用。例如,UL 1653 侧重于耐磨性、耐化学品性和耐热性,确保导管能够安全地发挥其预期的电气保护作用。
在加拿大, CSA C22.2 NO.227.1标准 管理柔性非金属导管系统。该标准涉及波纹导管在各种应用中的材料、结构和性能,特别关注耐环境性、防火性能和机械耐久性。
CSA 标准得到加拿大各地认可,旨在与全球安全和性能要求紧密结合。
AS/NZS 2053.5 标准 概述了澳大利亚和新西兰非金属柔性导管的使用。其中包括住宅、商业和工业用途的柔性和波纹导管的设计、建造和安装指南。该标准确保材料适合当地气候条件,例如极端温度和紫外线照射,并符合安全法规。
IEC 61386-23 标准 得到国际广泛认可,规范柔性和波纹塑料导管系统的使用。它规定了波纹导管的性能和测试标准,包括其抗冲击性、火焰蔓延性和环境因素。该标准确保导管适合全球工业、商业和住宅应用。
在为任何电气安装选择波纹管时,务必确保其符合当地相关规范和标准。这不仅包括导管的物理特性,还包括与之相关的安装实践和安全措施。
通过遵守这些标准,您可以确保导管适合其预期用途,无论是布线用于建筑物内的配电还是保护室外环境中的通信线路。
ENT(电气非金属管) 是美国和加拿大市场广泛使用的柔性导管类型,它是一种柔性、轻质的导管,用于保护和布线住宅和商业应用中的电线。ENT 由耐用的热塑性材料制成,具有出色的防潮、防腐蚀和防物理损坏能力,使其成为灵活性和保护性至关重要的环境的理想解决方案。ENT 广泛用于干式墙、混凝土和空间狭小的区域,在这些区域可以轻松弯曲和安装,无需特殊工具。
ENT 的主要优势之一是其非金属结构,有助于防止导电并降低短路风险,使其成为各种电气系统的安全选择。此外,它的设计与各种配件和附件兼容,为安装提供了灵活性。ENT 还符合相关 UL(保险商实验室)、NEC(国家电气规范)标准、CSA(加拿大标准协会)和 CEC(加拿大电气规范)标准,确保其在电气布线系统中的可靠性和安全性。
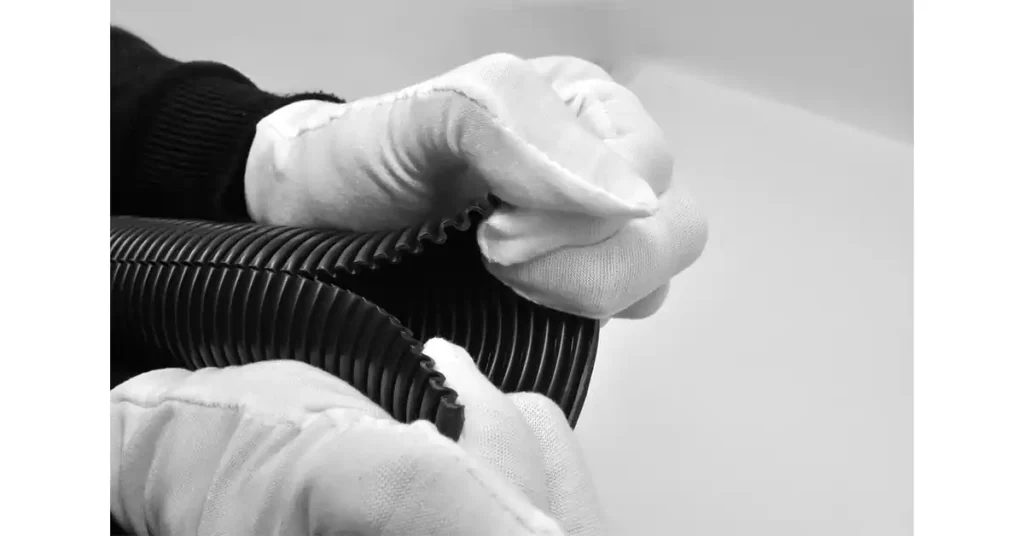
波纹管或柔性导管的颜色编码是电气系统设计的一个重要方面,它提供了导管用途的视觉识别,并简化了维护、故障排除和符合安全标准的过程。虽然具体的颜色代码可能因地区、行业或应用而异,但全球普遍采用某些通用做法来标准化导管识别并确保系统安全。
美国国家电气规范 (NEC) 和其他国际标准(例如 IEC(国际电工委员会)制定的标准)可能会提供颜色编码方面的指导,尽管当地法规和特定行业需求有时会影响这些做法。许多电气组织建议使用一种系统,其中导管的颜色表示其功能、电压水平或应用类型。
黑色的: 通常用于一般电线和低压应用。它是住宅、商业和工业环境中使用的柔性导管最常见的颜色之一。
灰色的: 通常用于非金属室内应用,特别是住宅建筑中的布线和照明系统。它还可用于需要灵活性的环境,例如电气管道。
黄色的: 常用于高压电缆导管。它是一种表示谨慎的颜色,用于警告潜在的危险情况,这就是为什么它用于高功率应用,包括工业机械和一些商业设施。
橙子: 高压或特殊应用:橙色通常用于识别高压电路或特定类型的电缆,尤其是在工业环境中。它是一种类似于黄色的警告色,但通常用于指示需要特别注意的电路,例如应急电源系统、照明控制电路或受特殊监管要求约束的电路。 数据和通信电缆: 在某些情况下,橙色可用于数据电缆或电信管道,表示管道包含关键或专用线路。
红色的: 通常用于识别具有特定功能的电路,例如紧急电路或火灾报警系统。它还可用于高压线路,以将其与其他电路区分开来。
蓝色的: 通常用于低压电路或通信电缆,例如用于网络、电信或控制系统的电缆。
绿色/绿色带黄色条纹: 这种颜色通常用于接地导体。它代表安全,并帮助工人轻松识别电气系统中的接地线。
白色的: 常用于中性导体,通常用于标准电气系统。白色编码的导管有助于确保中性线与火线或地线轻松区分。
尖端: 要了解颜色代码信息,请阅读我们上一篇文章“PVC 导管颜色代码指南'。
彩色编码导管在各种应用中都必不可少,可确保电气安全和系统组织。一些主要用途包括:
识别和可追溯性: 帮助工人快速识别特定电路,特别是在复杂或大型安装中,减少错误并提高安全性。
遵守: 确保符合当地电气规范,帮助满足不同地区的安全和标准的法律要求。
维护和故障排除: 通过轻松追踪电线并根据颜色编码的导管了解其功能,简化了维护和维修。
标准化: 确保整个项目使用的颜色代码一致。根据行业或当地代码标准化颜色将确保系统上的每个人都能轻松理解布线设置。
清晰的标签: 除了颜色编码外,还应在关键点添加标签,以进一步明确电线和导管的功能。
培训和意识: 应教育电气承包商、维修工人和其他人员了解颜色编码的重要性以及如何识别不同导管类型以尽量减少错误。
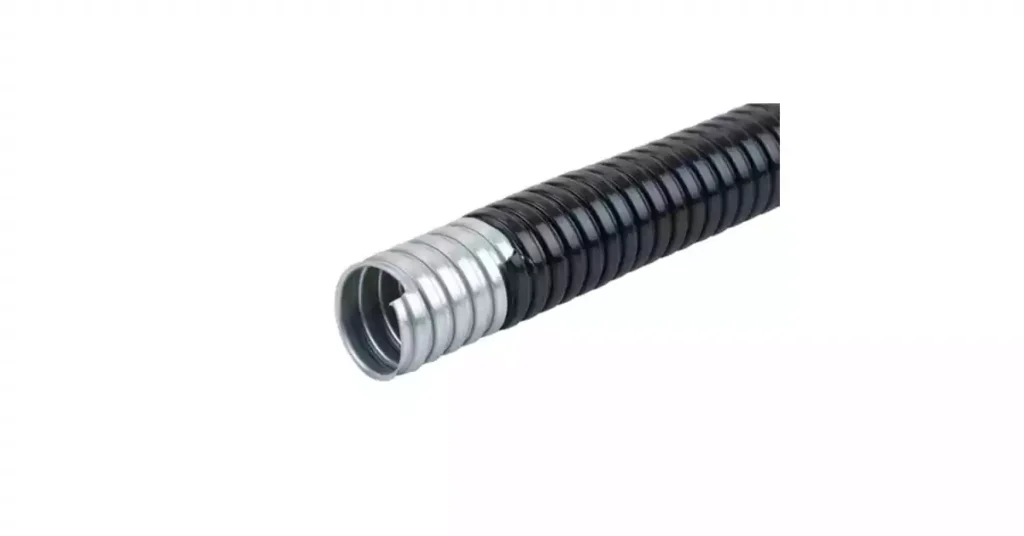
成本效益
波纹管是一种经济实惠的电线保护解决方案。其轻巧的设计有助于降低运输成本,而其灵活性则最大限度地减少了安装过程中对额外配件的需求。这种成本效益对于大型项目尤其有利,例如住宅或工业安装,因为材料和人工成本会迅速增加。正如行业专家指出的那样,“波纹管以刚性金属管成本的一小部分提供强大的保护。”
跨行业多功能性
波纹管用途广泛,适用于各种行业,包括建筑、汽车、工业,甚至 DIY 项目。其灵活性和耐用性使其能够适应静态和动态环境。例如,分体式波纹管通常用于汽车应用中,以保护线束免受磨损和损坏,尤其是在引擎盖下的狭小空间中。这种适应性确保波纹管可以处理广泛的应用,从保护建筑物中的电线到屏蔽工业机器中的电缆。
预防环境危害
波纹管的主要优势之一是它能够提供针对环境危害的保护。由 PVC 和聚乙烯等材料制成的波纹管具有防潮、防紫外线和防化学品的能力,可确保室外和地下安装的长期性能。例如,PVC 波纹管因其耐腐蚀性而在地下布线中特别有效。这种保护可确保您的电气系统即使在恶劣的环境中也能保持安全和正常运转,例如在恶劣天气条件下的区域或容易受到水和化学品影响的地下安装中。
简化安装流程
波纹管的肋状和柔性设计简化了安装过程。无需额外的工具或配件,即可轻松穿过狭小空间、拐角或不平坦的表面。这种易用性可以节省时间和劳动力,使波纹管成为专业人士和 DIY 爱好者的实用选择。此外,尼龙波纹管等材料不仅耐用,而且重量轻,进一步减少了安装工作量和时间。安装简便还有助于最大限度地降低安装过程中出错的风险,使其成为快速项目的有效解决方案。
机械强度低于刚性金属导管
虽然波纹管经久耐用,但它们的机械强度不如 RMC 或 IMC(中间金属管)等刚性金属管。在人流量大的区域或物理损坏风险较高的环境中,波纹管可能无法提供相同级别的外力保护。
耐火性有限
与金属导管相比,大多数由塑料材料制成的波纹导管的耐火性有限。虽然某些类型的波纹 PVC 导管具有阻燃性,但它们可能不符合某些高风险环境(例如商业厨房或工业厂房)所需的更高耐火性标准。
不适合极端温度
由标准塑料材料制成的波纹管在极低温度下会变脆或失去柔韧性,在极高温度环境下可能会变形或降解。虽然有特殊的耐高温波纹管可供选择,但它们价格更昂贵,使用范围也较有限。
选择合适的波纹管有 6 个技巧,
选择合适的波纹管的第一步是全面评估项目的具体需求。不同的环境和应用需要不同的功能,了解这些要求将有助于您缩小最佳选择范围。
- 项目环境 首先考虑一下导管的安装环境。您是在住宅、工业还是户外环境中工作?每种情况对导管都有不同的挑战和要求:
- 居住环境: 此类项目通常优先考虑安装的简易性、成本效益和美观性。住宅环境中的波纹管通常安装在墙壁、天花板和地板上,这些地方的灵活性和绕过障碍物的能力很重要。
- 工业环境: 在工业应用中,导管必须具有高耐用性、耐化学性以及承受恶劣条件(例如,暴露于极端温度、剧烈物理冲击和腐蚀性物质)的能力。
- 户外安装: 户外项目需要具有高抗紫外线性能的导管,以防止因长时间暴露在阳光下而导致的降解,同时还需要对雨雪等环境因素提供强有力的保护。
需要保护的电缆类型将显著影响您的导管选择。例如,电源线、通信电缆或数据线都有特定要求。如果您需要频繁接触线路,分体波纹导管可能是一个不错的选择。这种类型的导管可以轻松打开和关闭,而无需拆除整个线路,使其成为需要定期接触、维护或更换电缆的应用的理想选择。分体导管在灵活性和易维护性是关键考虑因素的情况下特别有用。
选择波纹管时,合适的尺寸至关重要。为了确保波纹管既实用又安全,您必须考虑电缆的直径,并确保管道有足够的空间进行正确的布线。电缆过于拥挤会导致电气系统过热、损坏或故障。足够的空间可以散热,并降低电缆受到物理压力而损坏的风险。
测量电缆直径,然后选择可提供额外空间的导管尺寸,以确保电缆可以在导管内自由移动而不会受到挤压或限制。此外,确定安装所需的导管长度。确保导管足够长,可以覆盖整个布线长度,而不会出现不必要的多余部分,从而导致浪费。
波纹管的材料对其性能起着关键作用。大多数波纹管由 PVC、聚乙烯或其他耐用热塑性塑料制成,每种材料都有自己的特点:
PVC 波纹管以其耐化学性、灵活性和价格实惠而闻名,使其成为住宅和商业应用的热门选择。
在高冲击条件、紫外线辐射或极端温度下的安装可能需要聚乙烯或其他高性能材料。对于室外或地下安装,聚乙烯通常是首选,因为它耐用且耐环境因素。
确保您选择的波纹管符合必要的当地、国家或国际标准和规范。例如,在美国,国家电气规范 (NEC) 提供了导管使用指南,包括材料规格、安装方法和耐火等级。遵守这些标准可确保导管系统的安全性、可靠性和长期性能。
最后,评估项目的预算。虽然波纹管通常比刚性金属替代品更实惠,但价格会根据材料、尺寸和特殊功能(如抗紫外线或耐化学性)而有所不同。对于成本敏感的项目,请确保所选导管提供必要的功能且不超过预算限制。
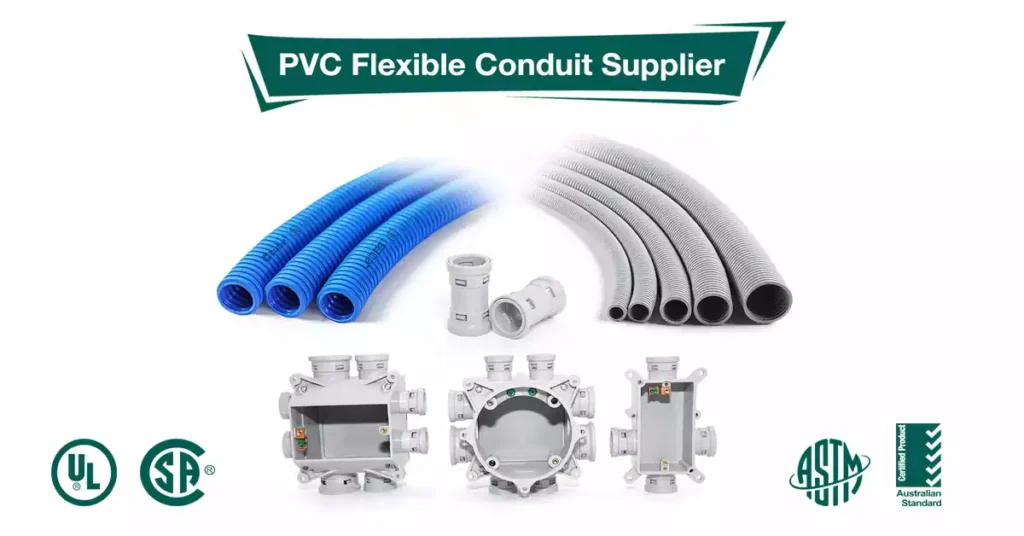
选择正确的 波纹管供应商 需求对于确保产品的质量、性能和及时交付至关重要。无论是住宅、工业还是大型商业安装,合适的供应商都会对项目的成功产生重大影响。以下是选择波纹管供应商时需要考虑的关键因素:
选择供应商时,首先也是最重要的考虑因素是他们提供的波纹管的质量。寻找提供符合或超过行业标准的产品的供应商。供应商应提供产品文档或测试报告以验证是否符合这些标准。质量保证可确保导管在预期应用中可靠地运行,为电缆和布线系统提供持久保护。
根据环境条件、机械应力和柔韧性需求,不同项目需要不同的材料。可靠的供应商应提供各种材料,例如:
PVC: 由于其价格便宜且耐化学性,通常用于一般住宅和商业应用。
聚乙烯: 由于其耐用性和抗紫外线能力,非常适合户外和地下安装。
尼龙: 为工业应用提供卓越的机械强度和耐磨性。
此外,提供定制解决方案(例如特定颜色、尺寸或分离式波纹管)的供应商可以帮助根据您的项目需求定制导管,确保最佳性能和更高效的安装。
信誉良好的供应商应提供各种导管产品,以满足各种行业和安装要求。确保他们提供不同类型的波纹导管,包括:
标准波纹管 适合一般用途。
软管 对于灵活性至关重要的应用。
分体波纹管 方便连接电缆。
重型波纹管 适用于高压力环境。
检查供应商是否能完成大订单或持续提供库存以满足您的时间表。及时提供产品对于避免项目延误至关重要,因此应优先考虑库存充足或交货时间短的供应商。
好的供应商不仅是供应商,也是您项目成功的合作伙伴。他们应该提供出色的客户服务和技术支持,以帮助您做出明智的决策。寻找符合以下条件的供应商:
拥有知识渊博的员工,他们可以根据您的项目要求提供选择最佳导管的技术建议。
提供安装指导或最佳实践建议。
能够及时响应询问并能够处理售后支持或问题。
如果您正在进行专业或复杂的安装,技术支持会特别有用,而拥有一个可以信赖的供应商提供建议可以避免代价高昂的错误。
波纹管(刚性或柔性)
导管配件(接头、弯头、适配器)
导管带/夹
管道切割机或锯子(用于刚性导管)
电工胶带或导管胶带(如果需要)
卷尺
钻头(如果安装到墙壁或天花板)
螺丝刀
- 规划路线:
确定导管安装路径,考虑长度、障碍物和弯道等因素。确保考虑导管尺寸,避免干扰其他系统。
- 测量并切割:
测量导管所需的长度。使用切管机或锯子将导管切割成合适的尺寸。如果使用柔性波纹导管,可以使用剪刀或锋利的刀进行切割。
- 安装导管带:
使用导管带或夹子将导管沿着所需路径固定。这些应以固定的间隔放置,通常刚性导管每 3-4 英尺放置一个,柔性导管每 18 英寸放置一个。
确保导管得到适当支撑,以防止下垂或损坏。
- 弯曲导管:
如果需要,弯曲导管以遵循所需的路径。柔性波纹导管更容易手动弯曲,而刚性导管可能需要弯头配件或其他连接器才能进行急转弯。
- 加入部分:
使用接头或适配器连接导管各部分。如有必要,使用 90 度弯头、三通或弯头等配件来改变导管的方向。
确保所有连接牢固且正确对齐。
- 密封和保护:
根据安装情况,密封导管末端以保护电线免受灰尘、水或其他环境因素的影响。
对于室外安装,请确保导管正确密封,以防止水进入。
- 测试和检查:
安装后,测试系统(如适用)以确保功能正常。检查是否有任何松动的配件、下垂的部分或可能需要纠正的潜在问题。
在处理任何电线管或电线之前,务必确保电源已关闭。
佩戴手套和安全眼镜等防护装备。
使用适当的工具以避免损坏导管或造成伤害。
遵循这些步骤将有助于确保波纹管的安全且合规的安装。
总之,波纹管是一种多功能、经济高效且可靠的解决方案,可用于保护各种应用中的电线,从住宅和商业设施到工业和汽车环境。波纹管具有灵活性、耐用性和易于安装的特点,可提供出色的保护,防止潮湿、紫外线和化学物质等环境危害。然而,与任何材料一样,它们也有局限性,特别是在高压力或重载环境中。
为您的项目选择合适的波纹管需要仔细考虑材料类型、环境条件和安装需求等因素。通过评估项目的具体要求(无论是简单的住宅设置还是复杂的工业应用),您可以选择最合适的导管,以确保最佳性能、安全性和成本效益。
最终,波纹管为保护电线提供了一种灵活、可靠且经济实惠的选择,使其成为许多行业和应用的首选。有了合适的产品和供应商,您可以确保您的电气安装安全、耐用且高效。