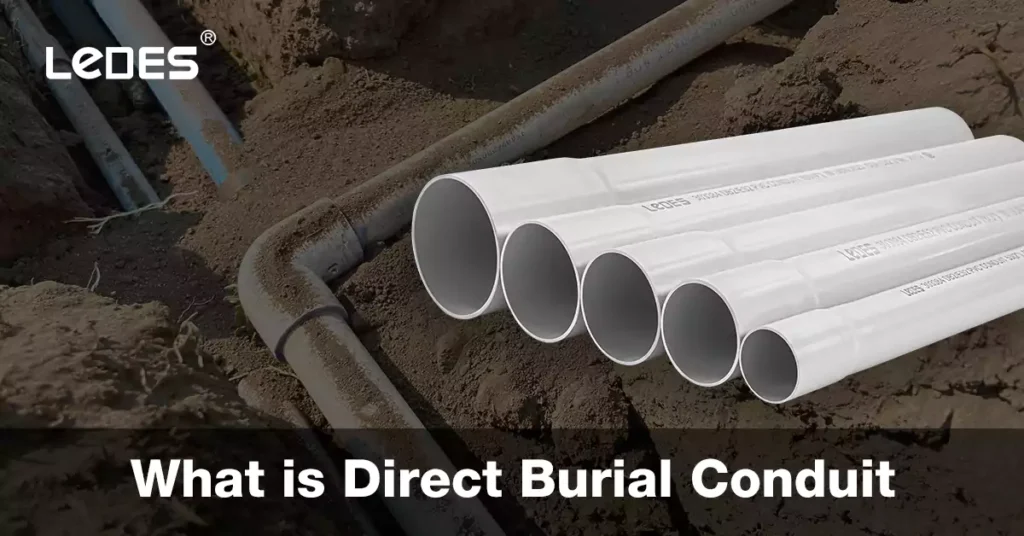
Table of Contents
Direct burial conduit refers to a type of piping or conduit system that is designed and installed underground without the need for additional protection or encasement. It is commonly used for electrical, telecommunications, or data communication applications where cables or wires need to be routed underground.
Direct burial conduit is typically made of durable materials such as high-density polyethylene (HDPE) or rigid PVC (polyvinyl chloride), which provide protection against moisture, soil acidity, and other environmental factors. The conduit is designed to resist corrosion, impact, and crushing, ensuring the integrity of the cables or wires it houses.
The “DB” in the name stands for “direct burial,” indicating its suitability for installation underground without requiring additional concrete encasement. This makes it a cost-effective and versatile option for various underground electrical applications.
There are several types of DB conduit available, each with its own specifications and advantages. Here are some of the most common used underground conduits in America and Canada.
Notes: Learn more about the details of the UL 651 standard requirement for PVC conduit in our last post if you are interested in this section.
DB60 conduit is a type of conduit specifically engineered to accommodate cables and wires in telecommunications and data networking applications. The “DB60” designation refers to its dimensions, with a standard size of 60mm in both height and width. However, it’s important to note that other sizes and variations may be available to suit specific installation requirements.
- Effortless Installation: Say goodbye to heavy concrete encasement. DB60’s direct burial capability saves you time and money, making installation a breeze.
- Superior Strength: DB60 is built to handle the pressure of underground soil and the stresses of movement, ensuring your cables stay secure.
- Cost-Effective Choice: Compared to traditional metal conduits, DB60 offers significant cost savings thanks to its ease of installation and lighter weight.
general guideline for minimum burial depths based on conduit type and location (refer to the National Electrical Code (NEC) and other industry standards for specific requirements):
- Residential areas: 18 inches(45cm)
- Commercial and industrial areas: 24 inches(60cm)
- Road crossings: 36 inches(90cm)
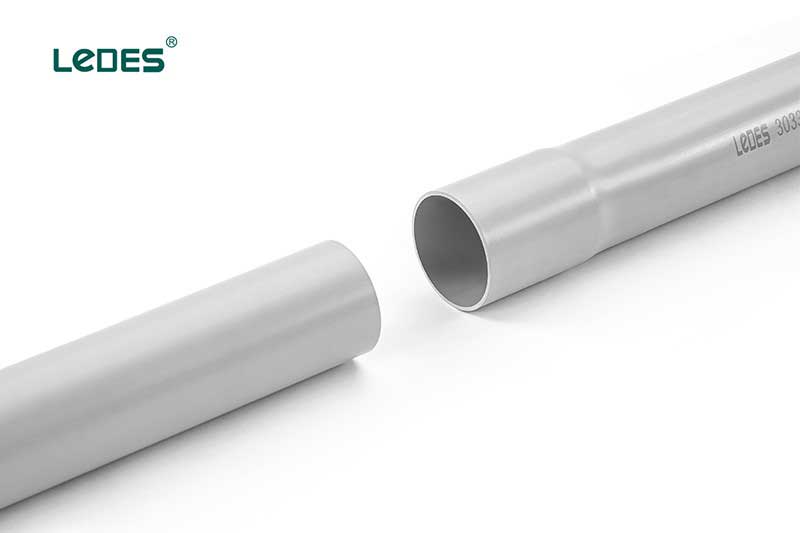
DB100 conduit is a type of PVC (polyvinyl chloride) conduit specifically designed for direct burial. It’s mainly used to protect electrical cables underground without needing extra encasement like concrete. DB100 is a lighter-duty conduit compared to heavier options like DB120, and it’s commonly used for residential, light commercial, and communication cable applications.
Cost-Effective:
DB100 is more affordable than heavier-rated conduits like DB120, making it a practical choice for projects that don’t require extreme mechanical strength.
Lightweight and Easy to Install:
Its thinner wall and lighter weight make DB100 easier to handle and faster to install, helping reduce labor time and costs.
Direct Burial Ready:
It’s manufactured specifically for underground installation without additional protection, simplifying trenching and cable laying.
Corrosion and Moisture Resistant:
Being PVC, DB100 doesn’t corrode like metal conduits and provides excellent resistance to moisture and many chemicals found in soil.
Smooth Interior:
The smooth inner surface reduces friction during cable pulling, helping prevent cable damage during installation.
While specific requirements can vary depending on local codes and project conditions, a common guideline is 18 to 24 inches (45–60 cm) from the top of the conduit to the ground surface for low-voltage and communication lines.
If installed under driveways, roadways, or where heavy equipment may cross, deeper burial (often 24 to 36 inches, sometimes with additional protection like concrete encasement) might be required.
DB120 conduit is a type of electrical conduit that is widely used for protecting and organizing electrical wires and cables. It is made from high-quality, durable materials such as polyvinyl chloride (PVC) or polyethylene (PE), which provide excellent resistance against corrosion, moisture, chemicals, and UV rays. The “DB120” designation refers to the specific schedule rating of the PVC, which indicates its wall thickness and strength.
- Durability: DB120 conduit is resistant to corrosion, chemicals, and weathering, making it ideal for long-term underground use.
- Impact resistance: The thick walls of DB120 conduit can withstand significant impact, protecting the wires inside from damage.
- Lightweight: Compared to concrete or metal conduit, DB120 is much lighter, making it easier to handle and install.
- Flexibility: DB120 conduit is available in a variety of lengths and diameters, making it easy to adapt to different project needs.
- Cost-effective: DB120 conduit is a relatively affordable option compared to other types of underground conduit.
- Residential areas: 12 inches (30 cm)
- Commercial and industrial areas: 18 inches (45 cm)
- Road crossings: 36 inches (90 cm)
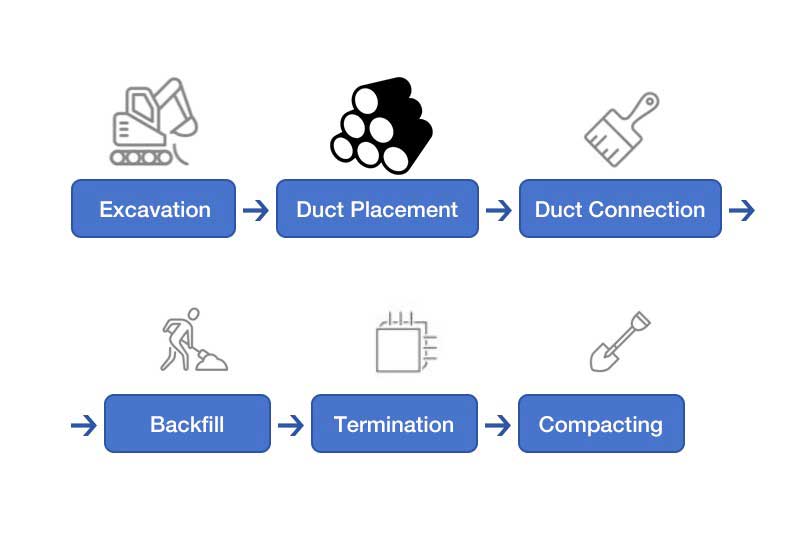
Installing DB120 conduit is a relatively straightforward process. Here are the basic steps:
- Excavate a trench: The trench should be deep enough to meet the local burial depth requirements for electrical and communication lines.
- Lay the conduit: Place the conduit in the trench, ensuring it is level and free of debris.
- Join the conduit sections: Use solvent cement or mechanical couplings to join the conduit sections together.
- Pull the wires: Pull the electrical or communication wires through the conduit.
- Backfill the trench: Backfill the trench with earth, tamping it down to eliminate air pockets.
DB120 conduit is used in a wide variety of applications, including:
- Residential and commercial underground electrical wiring
- Traffic signal and street lighting systems
- Telecommunication and data cables
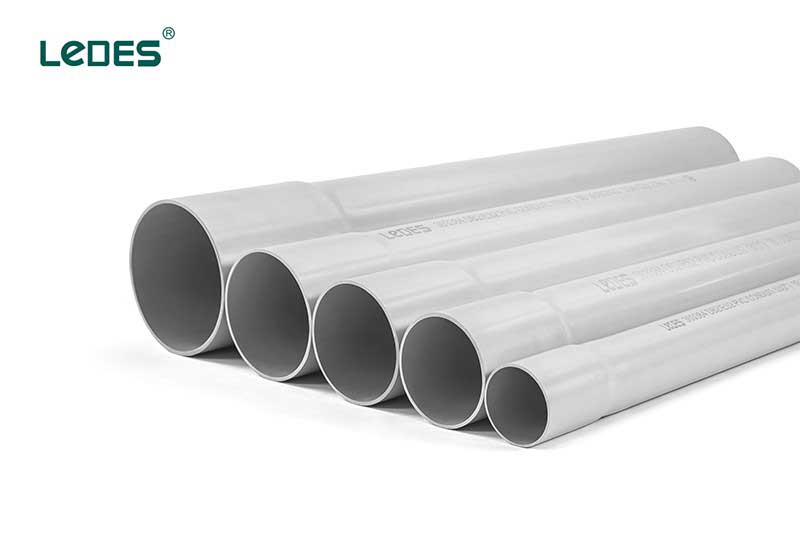
Crafted from sturdy PVC (polyvinyl chloride), these conduits are specifically designed for burial encased in concrete. This means they become an integral part of the underground infrastructure, shielding sensitive electrical cables from the harsh realities of buried life.
- Exceptional Strength: The “EB” designation signifies their exceptional impact resistance, able to withstand the pressures of shifting soil and accidental impacts. Think of them as silent guardians, keeping your electrical currents flowing uninterrupted.
- Superior Durability: Encased in concrete, these conduits form a robust and stable network, minimizing the risk of damage from ground movement and ensuring long-lasting performance.
- Lightweight: Compared to their metal counterparts, EB20/35 conduits are featherweights, making them easier to handle and install, saving time and labor costs.
- Compatibility: Available in a range of diameters and lengths, these conduits can be tailored to diverse project needs, from small residential installations to sprawling commercial complexes.
Installing EB20/35 conduit follows a straightforward process:
- Trench Warfare: Dig a trench deep enough to meet local burial depth requirements, providing ample protection for the electrical arteries within.
- Concrete Cradle: Prepare a bed of sturdy concrete to serve as a supportive and protective encasement for the conduit.
- Laying the Foundation: Carefully place the conduit sections in the trench, ensuring proper alignment and connection.
- Joining Forces: Use solvent cement or mechanical couplings to create a seamless and leak-proof conduit network.
- Concrete Cloak: Cover the conduit with the prepared concrete, creating a unified and impenetrable shield.
DB2/ES2 conduit refers to a specific type of duct used for communication purposes. It is typically a nonmetallic duct designed to house and protect communication cables, such as fiber optic cables or Ethernet cables. Ledes DB2 duct is made of PVC, certifed by CSA C22.2 No.211.1, and is commonly used in various industries, including telecommunications, networking, and data centers, to provide a conduit for the efficient and organized installation of communication cables.
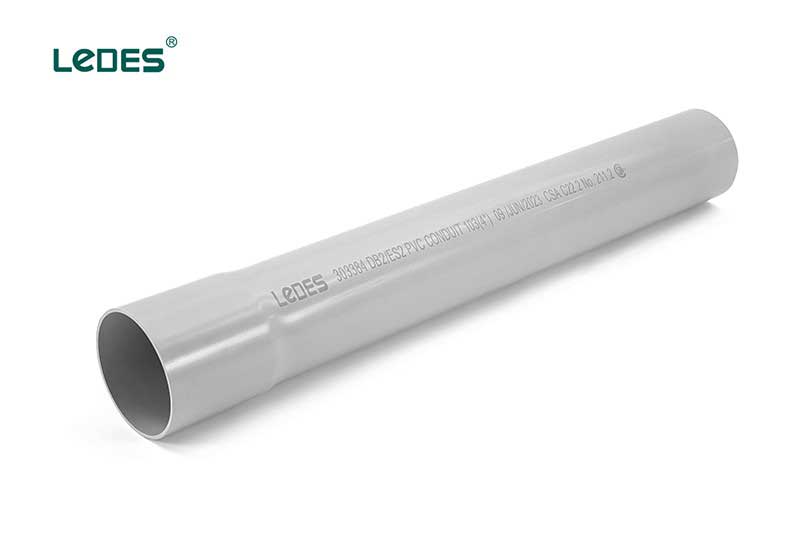
- Corrosion resistant: DB2/ES2 PVC duct made of high PVC material, its non-metallic, even exposed to naturally corrosive conditions, it won’t rust. Ensuring long-term performance in the underground world, providing safe and reliable protection for wiring systems.
- Lightweight: Its lightweight, making handling and installation easier and greatly saving time and labor costs.
- Direct burial: Its for direct burial applications and requires no additional protection when installed according to the Canadian Electrical Code(CEC).
- Easy wire pulls: DB2/ES2 has smooth interior surface reduces friction when pulling wires and cables through long runs.
DB2/ES2 PVC duct can be cut easily with a hacksaw, or use a PVC cutter for small sizes.
To join the lengths of duct or fittings, solvent cement is all that needed. PVC Solvent cement can make the joints strong and leak-proof. Easy handling and saving time.
- Trench Bottom: Dig a trench deep enough to meet local burial depth requirements, protecting the electrical lines within.
- Laying the Foundation: Carefully place DB2 duct sections in the trench, ensuring proper alignment and connection using solvent cement or mechanical couplings.
- Backfill: Once the conduit is secure, backfill the trench with earth, ensuring proper compaction to eliminate air pockets.
The depth at which DB duct should be buried can vary depending on various factors, including local regulations, specific project requirements, and the type of installation. However, there are some general guidelines to consider:
Local Regulations: Check the local building codes and regulations in your area. They often specify the minimum burial depth for different types of ducts and utilities.
Environmental Factors: Consider factors such as frost depth, soil type, and ground conditions. These factors can affect the stability and protection of the duct. In regions with freezing temperatures, it is common to bury ducts below the frost line to prevent damage.
Protection and Accessibility: The duct should be buried at a depth that provides adequate protection from external elements, such as excavation, traffic, and environmental factors. Additionally, it should be buried at a depth that allows for easy maintenance and accessibility if needed.
As a general guideline, nonmetallic communication ducts like DB ducts are often buried at a depth of 18 to 24 inches (45 to 60 centimeters). However, it is crucial to consult with local authorities and professionals familiar with the specific project and local regulations to determine the appropriate burial depth for DB duct in your specific location.
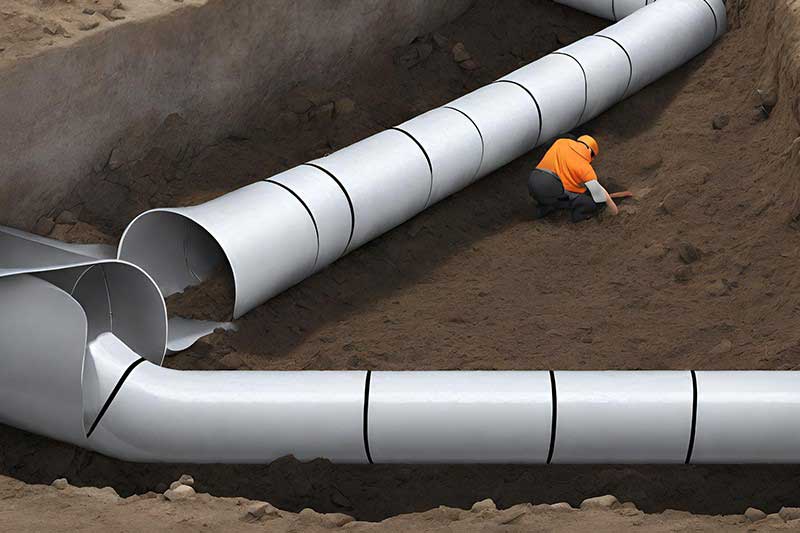
Before selecting a DB conduit for an underground project, it’s essential to understand the standards that govern its design, material, and performance. Standards ensure that conduits meet minimum safety, durability, and quality benchmarks – critical when infrastructure reliability is on the line.
In the United States, the main standards are:
- ASTM F512-19: Standard Specification for Smooth-Wall Poly(Vinyl Chloride) (PVC) Conduit and Fittings for Underground Installation.
- NEMA TC 6 & 8: Polyvinyl Chloride (PVC) Plastic Utilities Duct for Underground Installers.
In Canada, the key standard is:
- CSA C22.2 No. 211.1: Rigid types EB1 and DB2/ES2 PVC conduit.
Pro Tips: Want to learn more about the details of the CSA CC22.2 standard? Click the link to read our last post.
One of the most important standards for underground electrical conduit in the United States is ASTM F512-19. This specification defines the material, construction, and performance requirements for smooth-wall poly(vinyl chloride) (PVC) conduits and fittings used for underground installation of communication and electrical power cables.
The standard organizes conduits into five types, based on their stiffness and intended use:
Type EB-20 — Concrete encasement (lower stiffness)
Type EB-35 — Concrete encasement (higher stiffness)
Type DB-60 — Direct burial (lower stiffness)
Type DB-100 — Direct burial (higher stiffness)
Type DB-120 — Direct burial (very high stiffness)
EB types are mainly intended for installation within concrete encasement, while DB types are specifically built for burial directly in the soil, where higher strength and durability are essential.
To comply with ASTM F512-19, conduits must pass several critical tests that assess their durability and performance under underground conditions:
Conduits must be made from virgin or reworked PVC compound that meets detailed material properties such as strength, impact resistance, and chemical resistance.
The PVC material must meet specific cell classifications as defined in ASTM D1784, including:
- 12254
- 12164 (requiring a minimum tensile strength of 4000 psi or 28 MPa)
- 12264 (requiring a minimum tensile modulus of 500,000 psi)
Molded fittings must be made from PVC compounds with cell classifications of:
- 12234, or
- 13343,
also as defined under ASTM D1784.
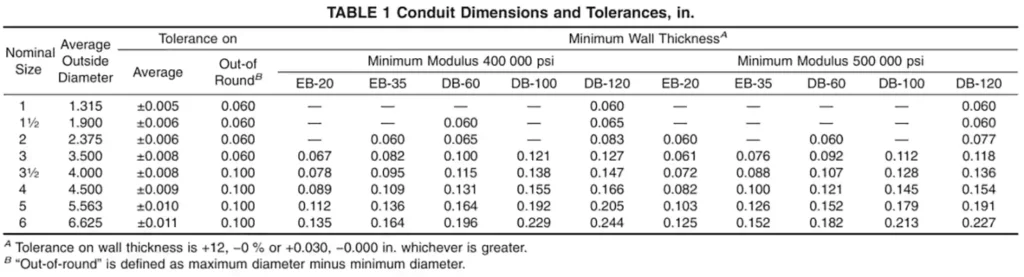
Outside diameters, wall thicknesses, and lengths must fall within tight tolerances to ensure consistent quality and compatibility with fittings.
Special dimensional requirements are defined separately for EB and DB types due to their different burial conditions.
Pipe stiffness is a critical performance characteristic for underground conduits, particularly those intended for direct burial where soil loads and external pressures are a concern.
According to ASTM F512-19:
Minimum Pipe Stiffness Values are as follow:
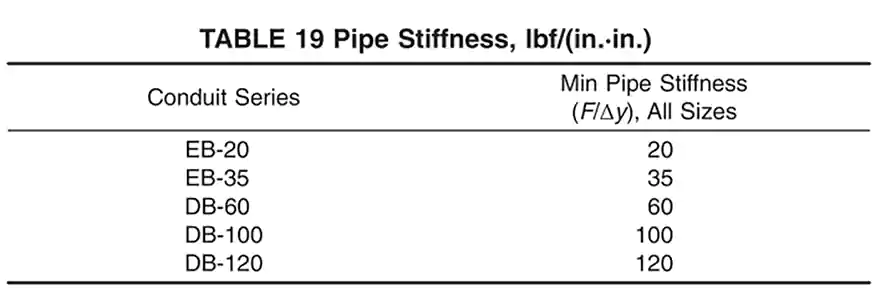
Test Method
The stiffness of the conduit is determined by a standardized parallel-plate loading test, following the procedures outlined in ASTM D2412. Here’s how the method works:
- A short length of pipe is placed horizontally between two rigid, parallel flat plates.
- The plates are brought together at a controlled rate of 0.50 ± 0.02 inches (12.5 ± 0.5 mm) per minute.
• During loading, load versus deflection (diameter change) data are recorded. - If cracking, crazing, delamination, or rupture occurs during the test, the corresponding load and deflection at the moment of failure are documented.
Impact resistance is another critical performance factor for underground PVC conduits. This is a quality control test that must be conducted at the time of manufacture to ensure consistent product reliability.
According to ASTM F512-19:
Minimum Requirements:
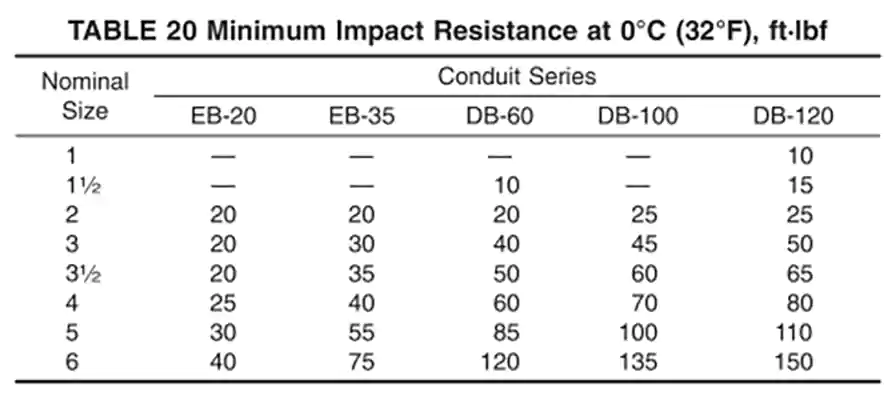
Test Method:
Impact testing is performed according to ASTM D2444, a 20-lb (9.1 kg) Tup B and a flat plate holder (Holder B) are used to apply the impact force.
Temperature Considerations:
If the test is performed at temperatures above 0°C (32°F), the specimen must be tested within 15 seconds after removal from the conditioning environment to maintain accuracy.
This impact test ensures that DB conduits can resist sudden, heavy loads without cracking or breaking, maintaining their structural integrity underground.
Ensuring a watertight connection between conduit sections is essential for underground installations, especially to prevent infiltration of moisture or soil into the electrical or communication pathways.
According to ASTM F512-19:
Requirement:
Conduit joints must not leak when subjected to pressure testing.
Test Method:
- A section of conduit is cemented to a bell (socket) following the manufacturer’s instructions, or, if no instructions are available, by using the method described in ASTM Practice D2855.
- The assembled joint must stand undisturbed for at least 6 hours to allow the solvent cement to properly cure.
- After curing, the joint is subjected to an internal water pressure of at least 25 psi (170 kPa) and maintained at this pressure for at least 1 hour.
Passing Criteria:
During the test, no leakage of water is permitted.
Bond:
A probe or point of a knife blade is used to separate the concentric layers.
It shall not be possible to separate any two layers using a probe or the point of a knife blade in such a way that the layers come apart cleanly or that the probe or blade can move freely between them.
ASTM F512-19 requires conduit products to carry clear and standardized markings to ensure easy identification, traceability, and compliance with quality expectations. Key requirements include:
Manufacturer’s Name or Trademark
PVC Cell Classification
Nominal Size and Type of Conduit
Minimum Wall Thickness
Control or Code Number
Standard Designation must be marked:
“ASTM F512” for single extrusion conduit
“ASTM F512 COEX” for coextruded conduit
Marking Frequency: At intervals not exceeding 5 feet (1.5 meters) along the conduit length.
Additional markings are allowed if the manufacturer deems them useful.
In addition to ASTM standards, another important reference for underground PVC conduit manufacturing in North America is the NEMA TC 6 & 8 standard.
This standard is published by the National Electrical Manufacturers Association (NEMA) and plays a critical role in defining the performance and quality requirements for polyvinyl chloride (PVC) conduit used in both direct burial and concrete encasement applications.
Key Points and Testing Requirements:
Conduits and fittings must be made from high-quality PVC compounds that meet minimum performance standards for strength, chemical resistance, and durability. Similar as ASTM F512-19 requirements.
Precise tolerances are set for conduit diameter, wall thickness, and socket dimensions to ensure proper fit and function in the field.
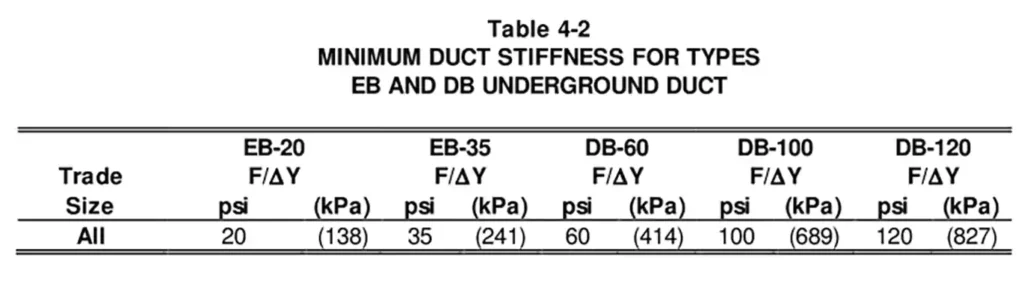
Testing procedure and requirements are the same referenced in ASTM F512-19. Measurements are take at 5% vertical deflection of the conduit’s inside diameter.
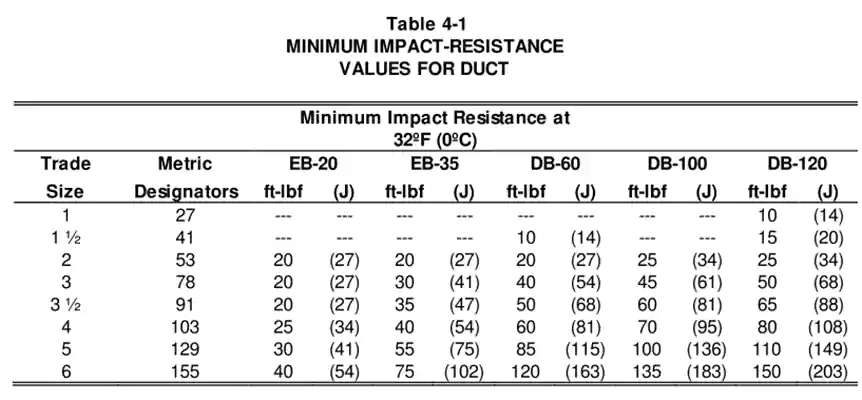
The testing method and requirements are the same with ASTM F512-19, but NAME TC 6&8 explicitly warns that UV exposure reduces impact resistance; values only valid at time of manufacture.
Same requirements as ASTM F512-19.
Manufacturer’s Name or Trademark
Standard Size Designation and Type of Conduit
PVC Cell Classification
Standard designation
Marking Frequency: Markings must be repeated at uniform intervals and appear at least every 10 feet (3.05 meters).
Additional markings that manufacturer considers necessary.
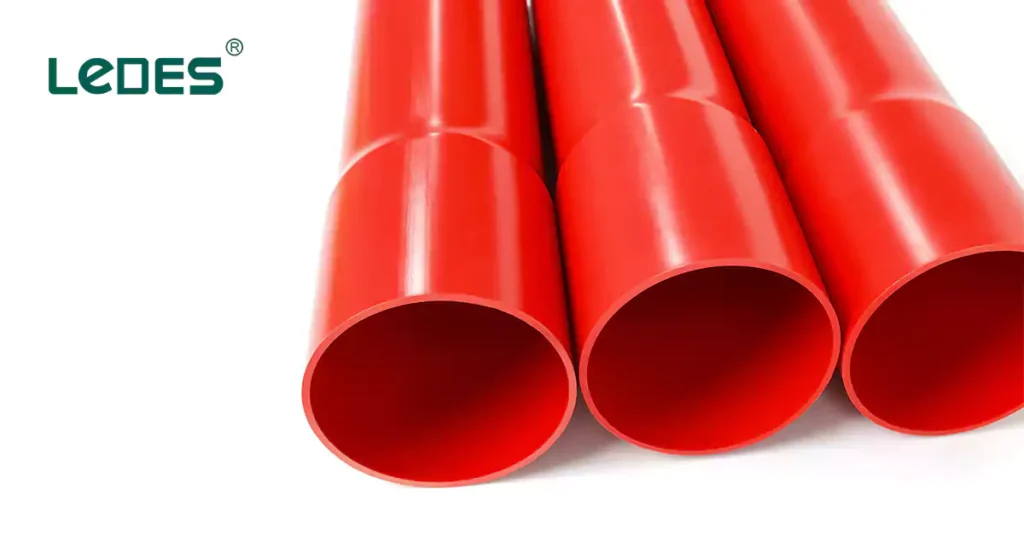
In addition to ASTM and NEMA standards, CSA C22.2 No. 211.1 is an important specification covering polyvinyl chloride (PVC) conduit intended for underground installations in Canada. CSA (Canadian Standards Association) standards ensure products meet strict safety and performance requirements suitable for Canadian environments, including extreme cold.
This standard sets the materials, construction and performance requirements for:
- Rigid PVC Conduit:
Type EB1: Intended for encasement in concrete or masonry.
Type DB2/ES2: Intended for direct burial in the ground or encasement in concrete or masonry.
- Associated Fittings:
Including straight couplings, 5° angle couplings, caps, plugs, bell-end terminators, bends, and adapters.
The conduit must be manufactured from PVC compounds that meet minimum requirements for physical and chemical properties such as tensile strength, impact resistance, and resistance to sunlight (for exposed sections). And have an ASTM D1784 cell classification of 12224.
The standards specifies the minimum wall thickness and outside diameters for different trade sizes. The requirements are different to ASTM and NEMA standards since they are different types and used in different regions.
This test verifies the toughness of the conduit material – especially under handling and installation conditions at both normal and cold temperatures.
Test Method:
A falling weight impacts the conduit placed on a specially prepared support bed.
Impact Energy and Temperatures
- At room temperature (23 °C): The impact energy applied must be 61 joules.
- At cold temperature (–18 °C): The impact energy applied must be 34 joules.
The crush resistance test evaluates the ability of PVC conduit to maintain its shape under compressive loading. This test ensures that the conduit can withstand burial or encasement pressures without permanent deformation.
Test Procedure:
- Test is performed at 23 ± 2°C (standard room temperature).
- Before loading, the vertical inside diameter of each specimen is measured and recorded.
- Each specimen is placed horizontally between two flat steel platens on a static load test bed (according to Figure 2 of CSA C22.2 No. 211.0).
The conduit is positioned so that the vertical axis (direction of measurement) is under compression. - A test mass of 90 kg, including the mass of the upper platen, is applied gradually onto the specimen. The load is maintained for 60 ± 5 seconds.
- After 60 seconds under load, remeasure the vertical inside diameter. And after 300 ± 20 seconds (5 minutes), measure the vertical inside diameter again to assess recovery.
Pass Criteria:
- During Load:
The average percentage decrease in vertical diameter shall not exceed:
12% for Type EB1 conduit
10% for Type DB2/ES2 conduit
- After Recovery:
The average percentage decrease shall not exceed 5% for both types.
The test method is same as ASTM and NEMA standards, which is performed in accordance with ASTM D2412.
Requirements:
- Type EB1 conduit must have a minimum pipe stiffness of 200 kPa at 5% deflection.
- Type DB2/ES2 conduit must have a minimum pipe stiffness of 300 kPa at 5% deflection.
Test Procedure:
- Two pieces of conduit, each 1 ± 0.1 meters long, are solvent-cemented into a standard coupling.
- After assembly, the joint must be cured for 24 hours at room temperature to ensure proper bonding.
- The entire assembly is completely filled with water, ensuring no trapped air inside.
- A gauge pressure of 35 kPa (around 5 psi) is applied inside the filled assembly.
- The pressure must be maintained continuously for 4 hours.
Acceptance Criteria:
- Throughout the 4-hour period, the joint must withstand the pressure without any rupture or leakage.
- Visual inspection is performed after the test to ensure no signs of leaking or joint separation.
Bond Strength:
- Choose eight points spaced equally around the circumference (every 45 degrees approximately).
- At each valley point, use a sharp probe or knife point. Attempt to separate the inner and outer walls manually by prying or picking.
- The conduit cannot cleanly separate the inner and outer walls at any of the eight points.
The chemical resistance requirements ensure that rigid PVC conduits maintain their mechanical and physical properties when exposed to aggressive chemical environments.
About Test:
The conduits are immersed for 7 days in the selected chemical solutions.
After immersion, the specimens must not exhibit a mass change greater then 2%.
After removing the samples from the chemical solutions, the specimens are subjected to a tensile strength at a crosshead speed of 12.7 mm/min ± 25% within 1 hour.
The average tensile strength of the chemical-exposed specimens must not differ from the average tensile strength of the control (unexposed) specimens by more than 15%.
Manufacturer’s name, trademark
Conduit type, such as DB2/ES2 PVC Conduit
Trade size
The date of manufacture
Standard: CSA C22.2 No.211.1
Item | ASTM F512-19 | NEMA TC 6 & 8 | CSA C22.2 No.211.1 |
Region | U.S. | U.S. | Canada |
Conduit Types | EB20, EB35, DB60, DB100, DB120 | EB20, EB35, DB60, DB100, DB120 | EB1, DB2/ES2 |
Impact Resistance | 20 ft-lbf at 0 °C | 20 ft-lbf at 0 °C | 61 J at 23 °C, 34 J at -18 °C |
Crush Resistance | Not specified | Not specified | 90 kg load for 60s, avg. Deformation: EB1≤12%, DB2≤10%, recovery≤5% |
Stiffness | ASTM D2412: specify min. Stiffness for each conduit type at 5% deflection | Same as ASTM F512-19 | ASTM D2412: EB1≥200 kPa, DB2≥300 kPa at 5% deflection |
Joint Tightness | Water medium, 25 psi (172 kPa) pressure for 1 hour | Water medium, 25 psi (172 kPa) pressure for 1 hour | Water medium, 35 kPa (5 psi) pressure for 4 hours |
Bond Strength | No layer separation under probe or blade | Not specified | No clean separation allowed using knife at 8 points around circumference |
Chemical Resistance | Not specified | Not specified | <2& mass change; tensile strength change <15% after 7-day immersion |
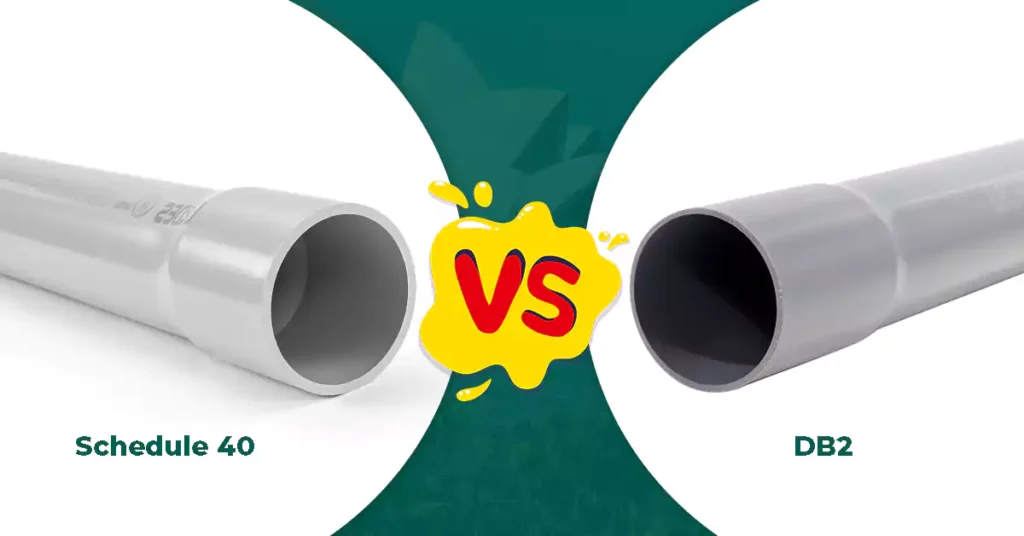
When selecting the right conduit for an electrical installation, one of the most important considerations is whether the conduit is intended for underground or above-ground applications. Two of the most common types are DB conduit (specifically DB2/ES2 for Canada or DB120 in the U.S.) and Schedule 40 PVC conduit.
While both are made from polyvinyl chloride (PVC), their designs, wall thicknesses, performance characteristics, and application scenarios differ significantly.
Feature | DB Conduit (DB2/ES2, DB120) | Schedule 40 PVC Conduit |
Primary Use | Underground installations (direct burial or concrete encasement) | Above ground installations or embedded in walls/ floors |
Standard | CSA C22.2 No.211.1 (Canada), NEMA TC 6&8 (U.S.) | UL651, NEMA TC2 |
Wall Thickness | Thinner than Schedule 40 | Thicker wall for higher mechanical protection |
Flexibility | More flexible for easier trench installation | More rigid |
Installation Method | Buried directly or encased in concrete | Surface-mounted or embedded in structures |
Crush Resistance | Designed for buried loads | Higher crush resistance due to thicker wall |
UV Resistance | Not always UV resistant (buried) | Typically UV resistant for outdoor exposure |
Impact resistant | Moderate | Higher |
Stiffness | Moderate | Higher |
Cost | More cost-effective | More expensive |
Understanding their differences can better help you to choose the right conduit type for your project, whether to choose DB conduit or above ground use conduit.
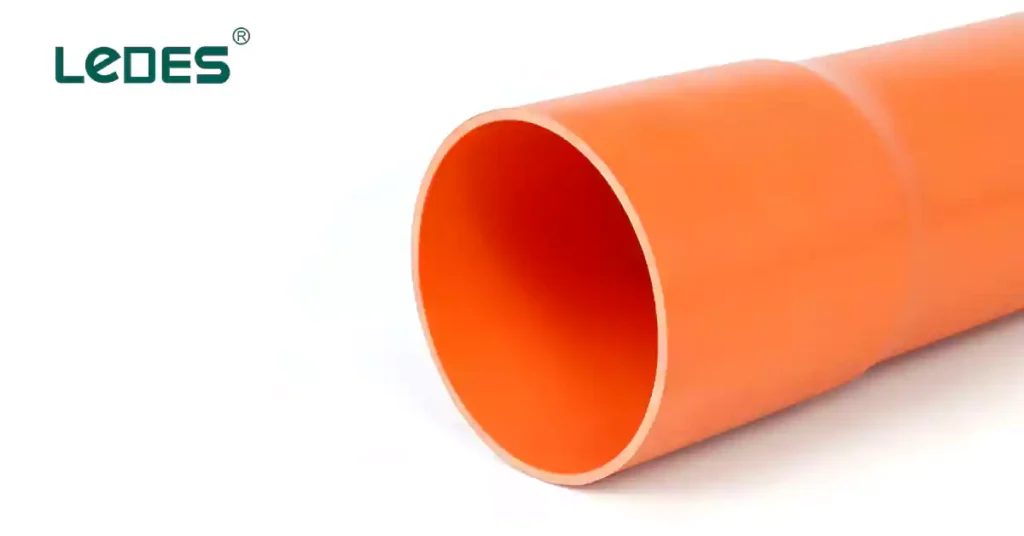
Choosing the right underground conduit starts with understanding your installation environment and matching it with the appropriate conduit type and standard. In the U.S., popular underground conduit types include EB20, EB35, DB60, DB100, DB120, Schedule 40, and Schedule 80. Each has specific strengths designed for different applications.
For concrete encased underground installations, choose the EB types.
For light-duty direct burial underground installations, such as garden lighting or residential landscape wiring, DB60 or DB100 can offer a budget-friendly solution with adequate protection. However, for most utility-grade and code-compliant electrical work, DB120 is considered the standard. It offers a balance of crush resistance, flexibility, and durability, making it suitable for use under driveways, sidewalks, or landscaped areas.
If your project requires conduits to run both underground and above ground (e.g., from underground into a building or panel), you may need to use to Schedule 40 or even Schedule 80 conduit. These rigid PVC conduits can used both underground and above-ground, and are thicker-walled, provide better UV resistance and impact protection when exposed. However, Schedule 40/80 are generally more rigid and may be harder to install in tight bends or curved runs, unlike DB conduit, which is easier to work with in trench applications.
Not all suppliers are created equal. Beyond just selling conduit, a dependable supplier should provide verified compliance with standards like CSA C22.2 No. 211.1, ASTM F512, or NEMA TC6 & 8. Look for evidence of product testing, such as impact resistance, joint tightness, stiffness, and bond integrity. Ask for certifications or test reports when necessary.
It’s also beneficial to work with a supplier that offers a complete system—conduits along with compatible fittings, adapters, elbows, and accessories—to ensure ease of assembly and reduce compatibility issues. Consider the supplier’s track record in your industry, their availability of technical support, and their responsiveness to project-specific needs. Local warehousing, fast delivery, and customization options are also key indicators of a reliable partner.
Ultimately, the best supplier is one that not only delivers high-quality products but also stands behind them with technical knowledge, compliance documentation, and after-sales support. Making the right choice will help your underground installation go smoothly and perform reliably for years to come.
When choosing between direct burial (DB) conduit and above-ground conduit systems, understanding the full cost-benefit profile is essential.
Upfront Cost: DB conduit typically has a lower initial cost than above-ground use conduit, such as Schedule 40 rigid PVC conduit
Installation Costs: DB conduit is easier to install due it’s lighter weight, making the labor costs lower. While Schedule 40 is heavier and potentially increases the installation costs.
Long – Term Costs: While DB conduit is less expensive upfront, it may require more frequent maintenance or replacements due to lower durability. Schedule 40, with its greater durability, can lead to lower long-term maintenance and replacement costs.
Direct Burial (DB) conduit plays a vital role in today’s underground electrical infrastructure, offering a reliable, durable, and code-compliant solution for protecting cables in harsh below-ground environments. Whether used in residential power distribution, commercial utilities, or infrastructure projects like EV charging stations and data centers, DB conduit stands out for its moisture resistance, long-term performance, and ability to meet stringent testing standards such as CSA C22.2 No. 211.1, ASTM F512, and NEMA TC6 & 8.
In this guide, we’ve explored the key differences between DB conduit and above-ground options like Schedule 40, breaking down everything from crush resistance and joint integrity to bond strength, chemical resistance, and cost-effectiveness. We’ve also discussed how to choose the right type of conduit and the importance of selecting a trustworthy supplier to ensure both compliance and performance.
Ultimately, DB conduit offers more than just buried protection – it delivers peace of mind. For those planning underground installations where safety, longevity, and minimal maintenance are priorities, DB conduit is a forward-thinking and cost-efficient choice.
signed for direct burial and concrete encasement, are the ideal choice for underground electrical installations. For more product information, please send us a request form or email us directly. Ledes’ professional team will help you with your questions and projects need.
Can I Use Direct Burial Cables Without a Conduit?
Yes, you can use direct burial cables without a conduit—but only if the cable is specifically rated for direct burial use. These cables are designed with robust insulation and jackets that can withstand underground conditions, including moisture, soil pressure, and temperature changes.
However, using conduit, especially DB type conduit, can provide extra mechanical protection for cables against rocks, shifting soil, and accidental digging.
What are the risks of sourcing direct burial products internationally?
Sourcing direct burial (DB) conduit products internationally can offer cost advantages, but it also comes with notable risks. Here are the key concerns:
- Product Quality
Not all direct burial conduits can meet the industry safety and performance requirements, when selecting the conduit manufacturer, make sure their products comply with the required standards and provide relevant test reports or certifications. If the conduit can’t meet the requirements, can result in costly failure and pose safety risks.
- Lead Time and Logistics
Shipping products from overseas can lead to longer lead times, especially in peak construction seasons. Unpredictable customs delays or disruptions due to geopolitical issues or port congestion. And need to pay increased freight costs.
Tips: Plan procurement schedules in advance and ensure suppliers have reliable logistics partners. Always factor in buffer stock for urgent needs.
- Communication Barriers and After-Sales Support
Cross-time zone collaboration and language differences can lead to misinterpretations or delays in communication. Technical requirements may not be fully understood, and important issues might not be addressed in a timely manner. This can become especially problematic during installation or in the event of product failure, where quick access to technical support or replacement parts is critical. In some cases, after-sales service from international suppliers may be slow, unresponsive, or not aligned with local expectations.
Tips: Choose suppliers with bilingual technical teams, clear communication channels, and a local or regional support network. Always confirm their responsiveness and support capabilities before committing to large-scale procurement.
Are there environmental considerations for direct burial installations?
Yes. Direct burial conduit systems must be designed with environmental factors in mind to ensure long-term reliability and safety. One of the primary concerns is soil composition—certain soils can be highly acidic or alkaline, which may degrade materials over time. In addition, microbial activity in the soil can contribute to corrosion, particularly in metallic components.
To mitigate these risks, conduits used for direct burial—such as PVC DB2 or HDPE conduit—are typically engineered to resist chemical attack and biological degradation. These materials are non-reactive, corrosion-resistant, and well-suited for harsh subsurface environments.
What certifications should I look for in direct burial products?
In the United States and Canada, products are expected to meet standards set by organizations like UL (Underwriters Laboratories), CSA (Canadian Standards Association), ASTM (American Society for Testing and Materials), and NEMA (National Electrical Manufacturers Association). These certifications confirm that the conduit has been rigorously tested for factors such as structural integrity, stiffness, chemical resistance, and joint tightness—qualities especially important in underground environments where long-term durability is critical.
For example, CSA C22.2 No. 211.1 covers direct burial PVC conduit in Canada, including DB2 and EB1 types, and mandates performance under various physical and chemical tests. Similarly, ASTM F512 addresses the requirements for coextruded pipe, such as uniform bond strength and resistance to layer separation. Products certified under UL standards may also carry additional marks for fire resistance or impact performance. Ensuring that your direct burial conduit carries these recognized certifications helps protect your installation from failure, reduces liability, and guarantees that you’re using a product suited for its intended underground application.
What is the disadvantage of underground cables?
While underground cables offer several advantages, there are also some disadvantages associated with their use. Here are some common disadvantages of underground cables:
- Higher Installation Cost: One of the primary drawbacks of underground cables is the higher installation cost compared to overhead cables. Excavation, trenching, and specialized equipment are required for laying the cables underground. These additional expenses can make the initial installation significantly more expensive, especially in areas with complex geographical features or urban environments where extensive underground infrastructure already exists.
- Increased Maintenance and Repair Difficulty: Maintaining and repairing underground cables is more challenging and time-consuming compared to overhead cables. Locating faults in underground cables requires specialized equipment and expertise, and accessing the cables buried beneath the ground can be cumbersome. This difficulty in fault detection and repair can lead to longer downtime and higher maintenance costs.
- Limited Accessibility: Underground cables are less accessible for maintenance and repairs. In densely populated areas or urban environments, accessing underground cables can be particularly challenging due to the presence of buildings, roads, and other infrastructure. This limited accessibility can result in delays and disruptions during maintenance and repair work, further increasing costs and causing inconvenience to service providers and customers.
What are the risks of burying underground cables without conduit?
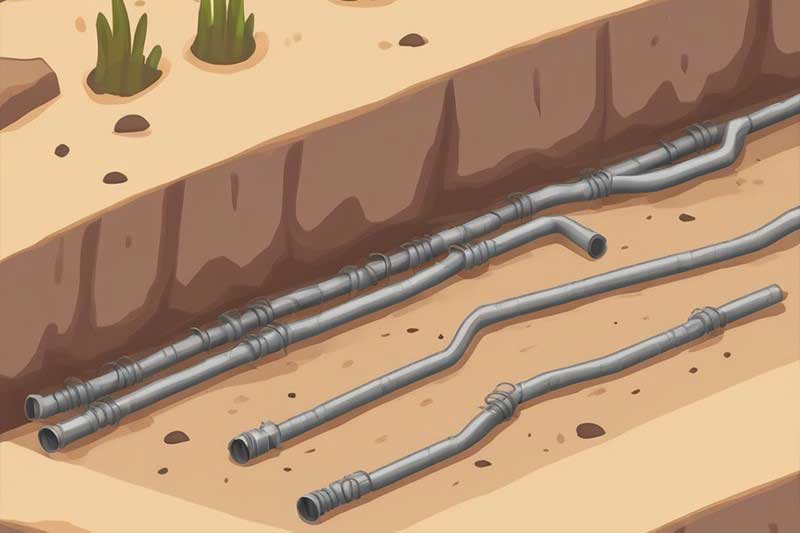
Burying underground cables without conduit can pose several risks and disadvantages. Here are some of the potential risks associated with not using conduit for underground cable installations:
- Physical Damage: Without conduit protection, underground cables are more susceptible to physical damage from external factors such as rocks, tree roots, construction activities, or accidental digging. Without a protective barrier, the cables are more exposed and vulnerable to potential impacts or compression, which can result in cable insulation damage or conductor breakage.
- Moisture and Water Ingress: Underground environments can be prone to moisture and water infiltration. Without conduit, there is a higher risk of water seepage into the cable system, which can cause insulation degradation, short circuits, and corrosion of conductors or connectors. Moisture ingress can significantly affect the performance and longevity of the cables, leading to service disruptions and costly repairs.
- Chemical Exposure: Underground locations may contain chemicals or substances that can adversely affect cable integrity and performance. Without conduit, the cables are more exposed to potential chemical exposure from soil contaminants, industrial activities, or accidental spills. Chemical interactions can result in cable degradation, insulation breakdown, and overall system failure.
- Difficulty in Cable Replacement or Upgrades: Without conduit, replacing or upgrading underground cables becomes more challenging. The absence of a dedicated pathway can make it difficult to remove and install new cables or make modifications to the existing infrastructure. This limitation can increase the complexity, time, and cost associated with future cable replacements or system upgrades.
- Lack of Cable Identification and Organization: Conduit provides a structured and organized pathway for cables, allowing for easier identification and management. Without conduit, the cables may become tangled or disorganized, making it harder to locate specific cables for maintenance, repairs, or expansions. This can lead to increased downtime and inefficiencies during troubleshooting or system upgrades.
Does a direct burial cable need a conduit?
Direct burial cables do not require a conduit for installation. They are specifically designed to be buried directly in the ground without additional protection. These cables have insulation and jackets that provide resistance to moisture, temperature variations, and physical damage. However, local electrical codes and regulations may have specific requirements, so it’s important to consult them.
While direct burial cables can be installed without conduit, using a conduit may offer additional benefits depending on the specific requirements of the project. Conduit can provide extra physical protection and make cable replacement or maintenance easier. It can also be helpful in challenging environmental conditions or for locating the cable. However, installing a conduit adds cost and complexity to the project.
Ultimately, the decision to use a conduit with direct burial cables depends on factors such as soil conditions, project requirements, and local regulations. Evaluating these aspects and consulting with a professional electrician can help determine the best approach for your specific circumstances.
What is the best conduit for direct burial?
The best conduit for direct burial is commonly recommended to be PVC (Polyvinyl Chloride) due to its durability, stability, and proven performance. PVC conduits have been extensively used and tested for underground installations. They offer several advantages, including:
Sturdiness: PVC conduits are known for their strength and ability to withstand external pressures and impacts. They provide reliable protection for the cables against physical damage from rocks, soil shifting, or other potential hazards.
Moisture Resistance: PVC is highly resistant to moisture and water ingress, making it an ideal choice for underground applications. It helps prevent water from reaching the cables, which can cause insulation degradation or short circuits.
Size Options: PVC conduits are available in various sizes, allowing for flexibility in accommodating different cable diameters or multiple cables within a single conduit. This versatility makes PVC conduits suitable for a wide range of direct burial cable installations.
Cost-Effectiveness: PVC conduits are generally more cost-effective compared to other options like metal conduits. They are less expensive to purchase and install, contributing to overall cost savings for the project.
Additionally, Fiberglass Reinforced Plastic (FRP) conduits are another option for direct burial applications. FRP conduits offer excellent durability, corrosion resistance, and high tensile strength. They are known for their non-conductive properties, making them suitable for installations where electrical grounding is a concern. FRP conduits are particularly useful in corrosive environments or areas with high moisture content.
Is PVC conduit suitable for direct burial?
According to NEC Code 352.10 Uses Permitted, PVC conduit is suitable for direct burial and underground encased in concrete. This means that PVC conduit can be directly buried in the ground without the need for additional protection, as long as it complies with the requirements specified in NEC sections 300.5 and 305.15. These sections provide guidelines for the installation of conduits in underground applications, including direct burial scenarios. Therefore, PVC conduit is considered a suitable option for direct burial installations, as per the NEC regulations.
How deep should electrical lines be buried?
The depth at which electrical lines should be buried can vary depending on several factors, including the type of electrical line, local building codes, and regulations. Here are some general guidelines:
- Residential Power Lines: In most residential applications, electrical lines, such as service entrance cables or underground feeders, are typically buried at a depth of 18 to 24 inches (45 to 60 cm). However, local codes may require deeper burial depths, so it’s essential to consult the specific regulations in your area.
- Commercial and Industrial Power Lines: For commercial or industrial installations, the burial depth of electrical lines is often greater than in residential settings. Depths can range from 24 to 36 inches (60 to 90 cm) or even deeper, depending on the type of electrical line, voltage, and local codes.
- Direct Burial Cables: Direct burial cables, designed for underground installations without conduit, generally have specific burial depth requirements specified by the manufacturer. It’s crucial to follow the manufacturer’s guidelines to ensure proper installation and performance of the cable.
- Other Factors: Besides burial depth, it’s important to consider factors such as soil type, environmental conditions, and the presence of other utilities. Some local codes may require additional depth or clearance requirements to protect electrical lines from damage caused by external factors or future excavation.