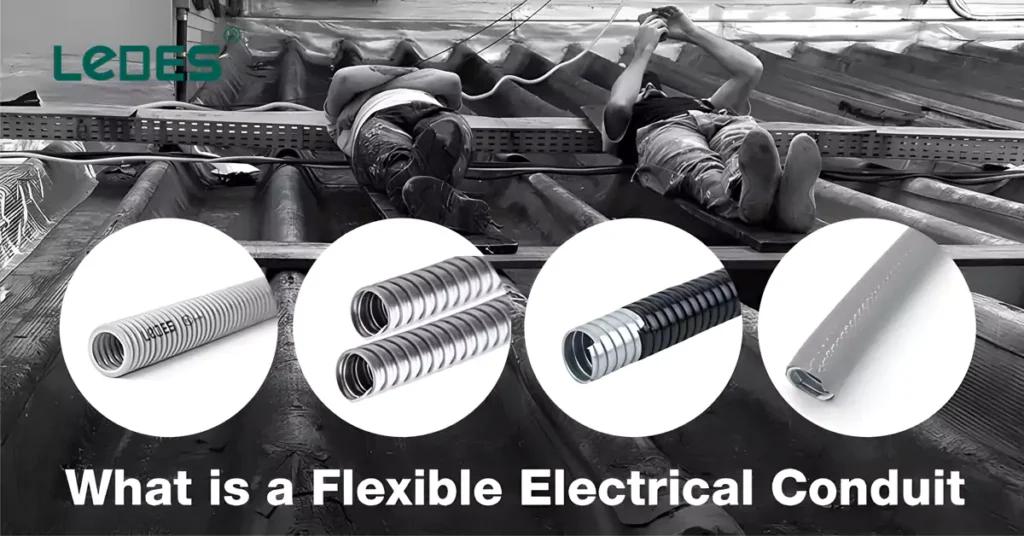
Table of Contents
Flexible conduit, also known as flexible tubing or flexible conduit pipe, is a type of protective conduit used for routing and protecting electrical wires, cables, and other types of conductors. It is typically made of a durable and pliable material, such as plastic or metal, that allows it to bend and flex without breaking or damaging the wires inside. Flexible conduit is designed to provide flexibility and ease of installation in applications where rigid conduit may be impractical or difficult to use.
What are the two types of flexible conduit?
Like the rigid conduit, flexible conduit comes in two types, metal and non-metal, both of which can be subdivided into different types, so let’s get start.
Electrical Nonmetallic Tubing (ENT)
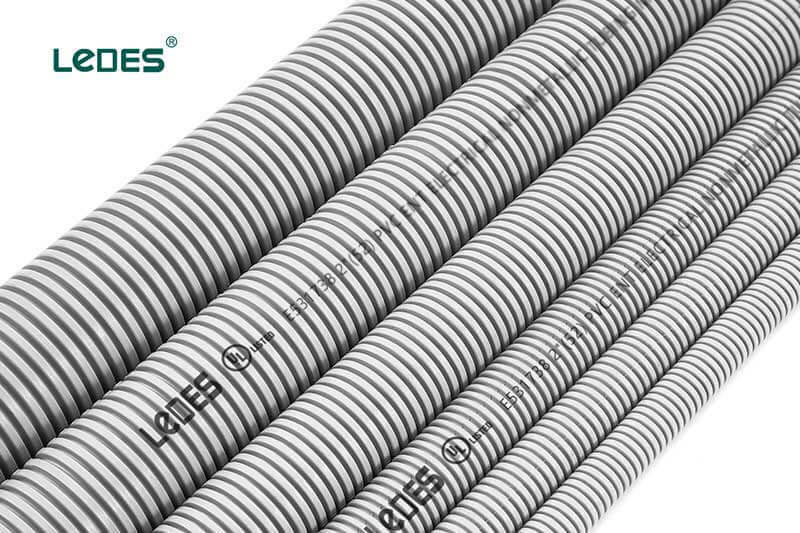
Electrical Nonmetallic Tubing (ENT) is the most commonly used plastic flexible conduit type. It is a type of pliable raceway used for the installation of electrical conductors. It is a thin-walled, corrugated tubing with a circular cross-section and is designed to be moisture-resistant and flame retardant.
ENT is composed of a nonmetallic material that offers resistance against moisture and chemical atmospheres, ensuring the protection of the electrical wiring. The raceway is pliable, which means it can be easily bent by hand with a reasonable amount of force, without requiring additional assistance or tools. However, it’s important to note that while the tubing itself is flexible, the associated fittings and connectors may not possess the same level of pliability.
Unlike threaded conduits, ENT features a corrugated shape, which eliminates the need for threading. While the tubing itself is not threaded, there are fittings available specifically designed for ENT installations that allow for secure connections. These fittings and connectors are integral or associated with the ENT raceway, ensuring a reliable and safe electrical installation.
Sizes of ENT Conduit
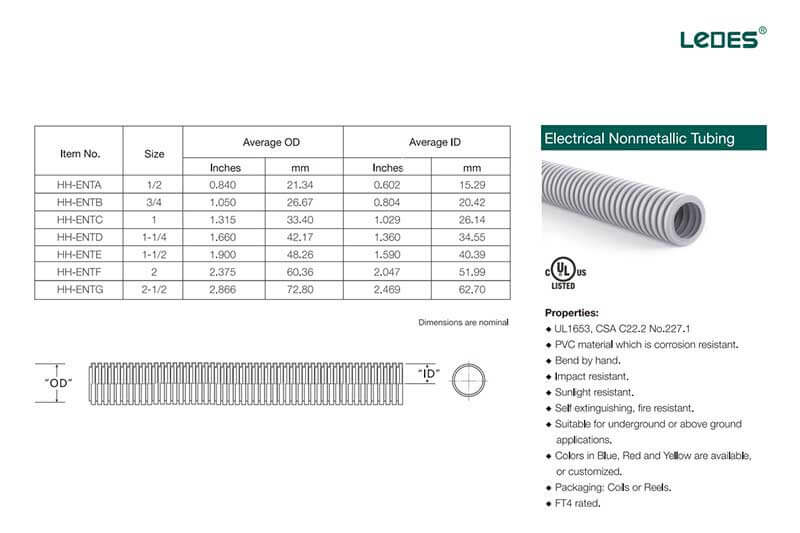
According to UL and CSA standards, Electrical Nonmetallic Tubing (ENT) conduit is available in sizes ranging from 1/2 inch to 1/2-2 inch, with the 1/2-2 inch size being specific to Canada only.
In addition to the standard specifications of inner diameter (ID) and outer diameter (OD), UL and CSA have stringent requirements for the performance of ENT conduit. For example, in the Vertical Flame Test, the following description applies:
When subjected to the test in Clause 7.2, Sample of ENT shall not burn for more than 10s. Flaming or glowing particles shall not fall from the specimen at anytime during the test.Not more than 25% of the extended portion of the indicator flag shall be burned.
Compliance Codes and Standards
All ENT conduit products sold in North America must comply with UL1653 and CSA C22.2 No. 227.1 standards to ensure electrical construction and project safety. CSA C22.2 No. 227.1 offers the optional FT4 fire rating, and Ledes is proud to have obtained certification for all the mentioned standards.
Using products that do not meet these specifications can pose significant risks during construction and usage. UL and CSA have carefully considered the performance and safety of Electrical Nonmetallic Tubing in their relevant standards. For example, the impact resistance test in UL1653 requires that no more than 20% of the test samples exhibit damage or cracks. Imagine the consequences of installing non-compliant products underground, where a quality issue could lead to ENT conduit breakage, exposing wires and potentially causing a series of safety accidents, resulting in severe losses.
For PVC Corrugated conduit sold in Australia and the European Union, compliance with AS/NZS 2053.5:2001 and IEC61386 standards is mandatory. These standards cover physical performance and various additional testing requirements. Ledes also offers compliant products for these regions.
Flexible PVC Electrical Conduit Pros:
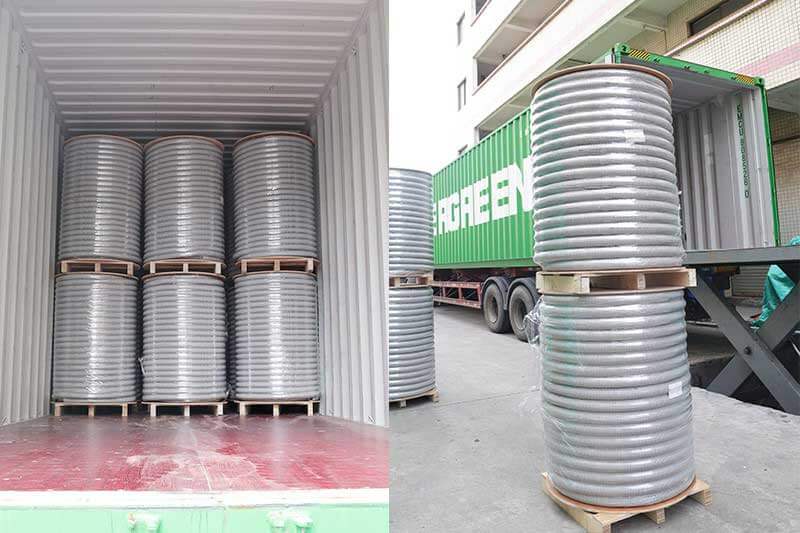
- Flexibility: ENT is designed for convenient installation, offering excellent flexibility that can accommodate various construction needs, especially in situations with corners, obstacles, or limited space. It significantly saves construction time and improves efficiency.
- Lightweight: ENT is typically made of PVC material, which is lighter in weight compared to metal materials. This makes it easier to transport and reduces labor consumption during cutting and installation. It is the preferred choice for builders and contractors.
- Fire Rating: As mentioned earlier, ENT conduit undergoes the UL1653 Vertical Flame Test, ensuring that it does not burn for more than 10 seconds and does not release flaming or glowing particles during the test. Additionally, no more than 25% of the extended portion of the indicator flag should be burned. This outstanding fire resistance ensures construction and usage safety.
- Concrete Tight: Ledes offers optimized formulations and processes for concrete and underground environments, making quick and easy fixes possible with its quick-connect fittings. It ensures efficient and reliable installations.
- Corrosion Resistance: Plastic materials used in ENT do not rust, eliminating concerns about rusting even when buried for long periods. In addition, ENT undergoes relevant UL tests that consider factors such as antimicrobial properties and water absorption rates. This makes it suitable for both residential and commercial construction projects.
- Safety: ENT’s plastic material provides excellent insulation, significantly enhancing safety. It prevents electrical hazards and ensures a high level of protection.
Overall, ENT conduit offers flexibility, lightweight construction, excellent fire resistance, concrete tightness, corrosion resistance, and enhanced safety due to its insulation properties.
Flexible PVC Electrical Conduit Cons:
- Rigidity: ENT, being made of PVC or plastic, is not as rigid as metal flexible conduit. In certain extreme usage environments, this may pose some challenges.
- Sunlight Resistance: PVC or plastic materials used in ENT can undergo aging when exposed to direct sunlight for extended periods. In this aspect, metal flexible conduit offers better performance.
- Durability: Metal conduits, under normal circumstances without incidents like rusting, have a longer theoretical lifespan. Although current ENT plastic conduits also have a lifespan of over 100 years.
It’s important to consider these cons when choosing flexible electrical conduits, as they may have specific implications depending on the application and environment in which they are used.
Flexible Metal Conduit
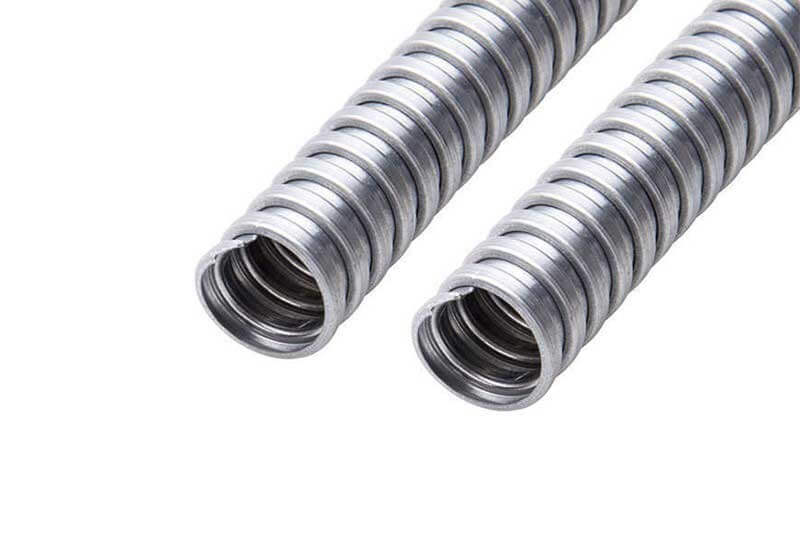
Metal flexible conduit has several commonly used types, here are some introdcution for them.
Flexible metal conduit (FMC)
Flexible metal conduit (FMC), also known as greenfield or flex, is a type of conduit made by coiling a ribbed strip of aluminum or steel into a hollow tube. It provides a flexible solution for routing and protecting electrical wires in areas where installing rigid non-flexible conduits like EMT (Electrical Metallic Tubing) would be impractical. FMC offers the strength of a metal conduit while allowing for easy bending and flexing without maintaining a permanent shape.
Advantages of FMC Conduit:
- Durability: FMC conduit is made of metal, typically steel or aluminum, and most FMC conduits have effective rust prevention measures in place. They are designed to be strong, with high hardness and excellent impact resistance. Thin-walled conduit variants are commonly used, ensuring long-lasting durability once installed.
- Flexibility: Despite being made of metal, FMC conduit can be easily bent and flexed due to its unique manufacturing process. This flexibility greatly facilitates tasks such as wire pulling during construction, reducing installation difficulties.
- Rust Resistance: As mentioned earlier, FMC manufacturers incorporate rust prevention coatings during production. This significantly reduces the likelihood of rust formation, ensuring long-term use of FMC conduits.
- EMI/RFI Shielding: FMC’s metal structure provides electromagnetic interference (EMI) and radio frequency interference (RFI) shielding properties, making it suitable for installations where electromagnetic compatibility is a concern. However, the applicability of this feature may vary depending on the construction project, so careful consideration is necessary during selection.
Disadvantages of FMC Conduit:
- Weight: Due to its metal composition, usually steel or aluminum, FMC conduit is heavier compared to plastic conduit materials. This increased weight can add extra costs and considerations during installation and construction.
- Decline in Rust Resistance over Time: While FMC conduits come with rust prevention coatings, these coatings may deteriorate over time, leading to decreased rust resistance. Gradually, this may result in rust formation.
Applications of FMC Conduit:
Residential and Commercial Buildings: FMC conduit, like ENT, is suitable for both residential and commercial construction. Its primary purpose is to protect cables and wiring from damage in building structures.
Outdoor Installations: FMC conduit’s superior resistance to direct sunlight makes it a good choice for outdoor applications. It can be used for outdoor lighting, signage, surveillance systems, solar power systems, and more.
Machinery and Equipment: FMC conduit’s flexibility makes it ideal for cable protection in machinery and equipment. It can withstand the harsh environments typically found in industrial settings, ensuring the longevity of the cables.
Industrial Construction: Considering the demands of industrial construction and environments, FMC conduit can meet the higher requirements for wiring and conduit systems in facilities such as factories. It ensures the safety of internal wiring in these demanding applications.
Flexible metallic tubing (FMT)

Flexible metallic tubing (FMT), FMT is described in a separate article of the US National Electrical Code (NEC) and is considered a raceway rather than a conduit. FMT is circular in cross-section, flexible, metallic, and liquidtight without a nonmetallic jacket. It is available in smaller trade sizes (1/2″ and 3/4″) compared to the wider range of trade sizes for FMC (1/2″ to 4″).
Therefore, FMT conduit shares similar characteristics and features with FMC conduit, and further details will not be reiterated here.
Liquidtight Flexible Metal Conduit (LFMC)
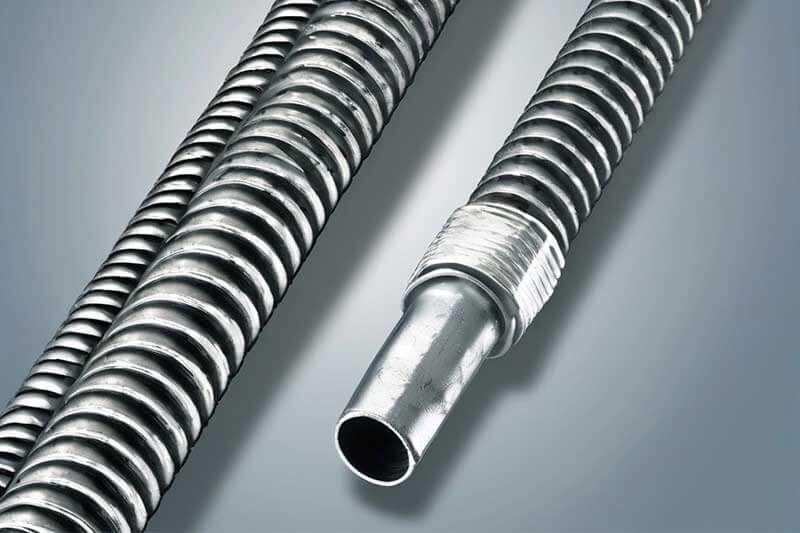
Liquidtight Flexible Metal Conduit (LFMC), it is a metallic flexible conduit coated with a waterproof plastic layer, offering enhanced protection against moisture. It shares a similar interior design with FMC.
Advantages of LFMC Conduit:
- Durability: LFMC conduit is highly durable, making it suitable for applications that require protection against mechanical damage. Its plastic coating provides excellent resistance to rust, chemicals, and moisture, making it ideal for harsh environments.
- Waterproof: LFMC conduit exhibits good waterproof properties due to the low water absorption characteristics of PVC or plastic materials. This makes it suitable for underground installations in damp conditions.
- Flexibility: Like FMC, LFMC conduit is flexible, allowing it to be easily bent and maneuvered. This flexibility enables installation in tight spaces and corners where rigid conduits may be impractical.
- EMI/RFI Shielding: LFMC conduit, similar to FMC, utilizes galvanized steel, aluminum, or brass as its core material. This gives it electromagnetic interference (EMI) and radio frequency interference (RFI) shielding capabilities, making it suitable for special applications.
- Sunlight Resistant: The plastic coating on LFMC conduit is typically designed to be sunlight resistant, and the metal core itself provides good protection against direct sunlight.
Disadvantages of LFMC Conduit:
- Higher Weight: LFMC conduit is heavier due to the metal core and the additional plastic coating. This can result in increased transportation costs and may require additional considerations during installation.
- Larger Outer Diameter: The dual-layer structure of LFMC conduit (metal + PVC) increases the wall thickness and, consequently, the outer diameter. This needs to be taken into account during construction planning to avoid installation issues.
- Reduced Flexibility: The limited bending capability of LFMC conduit is due to the constraints of the plastic coating and its tight bond with the metal core. This is an important consideration during purchasing and installation processes.
Applications of LFMC Conduit:
Residential and Commercial Buildings: LFMC conduit can be used in various settings, including shopping malls, residential buildings, and other commercial structures. It is particularly suitable for areas prone to moisture, such as sewer lines, kitchens, and damp environments where cable protection is essential.
Aboveground Installation: LFMC conduit’s excellent resistance to direct sunlight makes it suitable for aboveground installations. It provides enhanced protection for cables exposed to sunlight, ensuring their longevity and performance.
Machinery and Equipment: LFMC conduit’s dual-layer protection (metal core + plastic coating) makes it well-suited for machinery and equipment in industrial settings. These environments often involve harsh conditions, such as oil or dust exposure, where LFMC conduit can provide superior cable protection.
Liquid Tight Flexible Non-Metallic Conduit (LFNC)
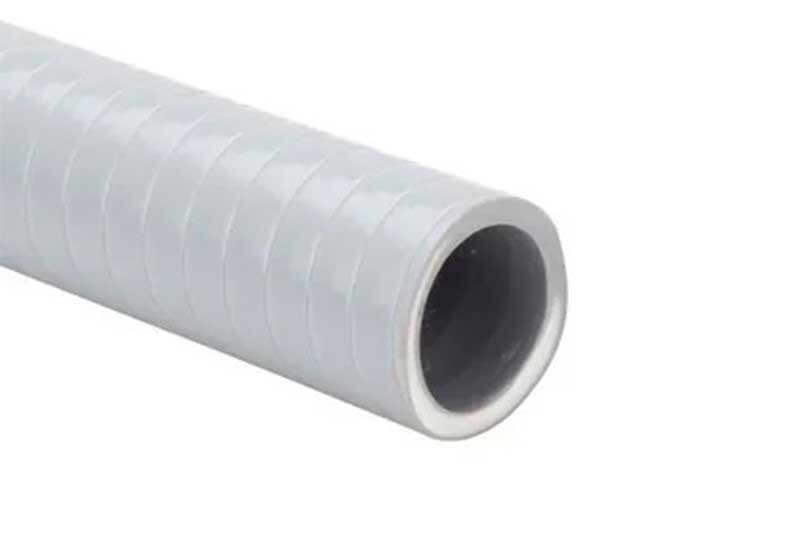
Liquid Tight Flexible Non-Metallic Conduit (LFNC), also known as FNMC, encompasses various types of non-metallic tubing that are flame-resistant and designed for electrical applications. These conduits feature either smooth or corrugated interior surfaces and may incorporate integral reinforcement within the conduit wall. They are specifically designed with a waterproof jacket to provide protection against water.
LFNC is a flexible conduit system that serves the purpose of enclosing and safeguarding electrical cables and wiring from moisture, liquids, abrasions, and external elements. Unlike traditional rigid metal conduits, LFNC is made from non-metallic materials like PVC (polyvinyl chloride) or thermoplastic rubber. This composition allows for enhanced flexibility while maintaining resistance to liquids. LFNC can be easily bent, twisted, and routed in various directions without compromising the integrity of the enclosed cables.
Advantages of LFNC Conduit:
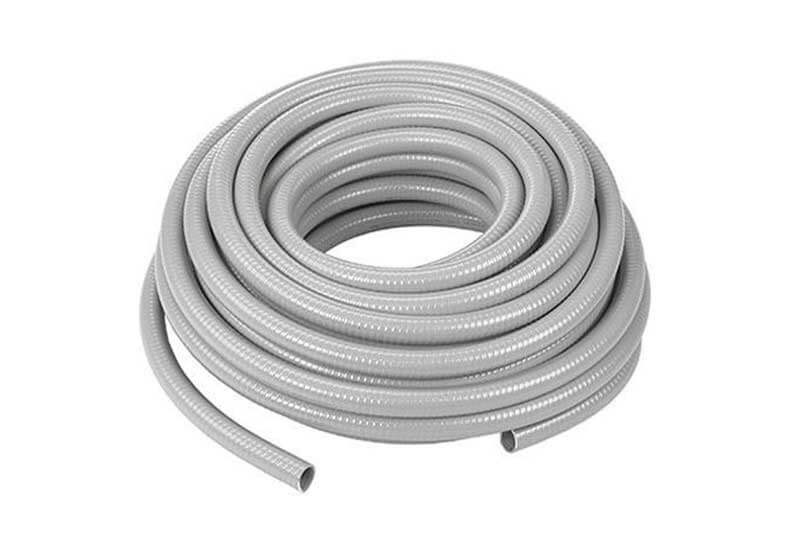
- Flexibility: LFNC conduit, being a flexible tubing, offers the ability to bend and maneuver easily. Unlike LFMC conduit, it contains minimal or no metal components, making it relatively easier to bend without compromising its integrity.
- Lightweight: Despite incorporating reinforcement in some variants, LFNC conduits are lighter compared to steel conduits like FMC. This can result in cost savings during transportation and installation.
- Cost-effective: Due to the lower cost of raw materials, LFNC conduits are generally more affordable compared to FMC or LFMC conduits. This can help reduce project budgets without compromising cable protection capabilities. However, this factor should be considered in conjunction with specific project requirements.
- Waterproof: LFNC conduit exhibits good waterproof properties due to the low water absorption characteristics of plastic materials. This makes it suitable for underground installations in damp conditions.
- Corrosion Resistance: LFNC conduits, being non-metallic, eliminate the risk of corrosion commonly associated with metal conduits. This is particularly advantageous in installations where the conduit may be exposed to corrosive substances.
- UV & Sunlight Resistance: Some LFNC products are formulated with UV and sunlight resistance properties, providing protection against prolonged exposure to UV rays and direct sunlight.
Disadvantages of LFNC Conduit:
- Durability: As LFNC conduit is non-metallic, it may have lower physical strength and impact resistance compared to FMC or LFMC conduits. In theory, it may be less durable.
- Weight: While lighter than metal conduits, LFNC conduit is heavier than ENT (Electrical Nonmetallic Tubing) conduits. Its flexibility performance also does not match that of ENT conduits.
Applications of LNFC Conduit:
Residential and Commercial Buildings: LNFC conduit can be used in various settings, including shopping malls, residential buildings, and other commercial structures. It is particularly suitable for areas prone to moisture, such as sewer lines, kitchens, and damp environments where cable protection is essential.
Outdoor Installation. LFNC conduits have excellent resistance to direct sunlight and enhanced strength, so they can be used in scenarios with higher requirements, such as outdoor street lighting systems, security systems, and hydraulic irrigation system cable protection scenarios.
Industry or Chemicals Location. Because LFNC is resistant to chemical corrosion, it can be used for cable protection under harsh working conditions, such as cable protection for large mechanical equipment, chemical plants, etc.
How to install Flexible Metal Conduit?
Installing Flexible Metal Conduit (FMC) involves several steps to ensure a secure and proper installation. Here’s a general guide on how to install FMC:
- Gather the necessary tools and materials: You’ll need FMC, connectors, a conduit cutter, a utility knife, a screwdriver, and appropriate fasteners.
- Plan the conduit route: Determine the path where the FMC will be installed, taking into account any obstacles, bends, or corners. Ensure compliance with local electrical codes and regulations.
- Measure and cut the FMC: Measure the required length of FMC for each section of the conduit route. Use a conduit cutter to cut the FMC to the appropriate size. Ensure the cut ends are smooth and free from burrs.
- Install connectors: Attach appropriate connectors to each end of the FMC. Connectors can be compression-type or set-screw type, depending on the specific FMC system being used. Follow the manufacturer’s instructions for proper installation.
- Secure the connectors: Fasten the connectors tightly to the FMC using a screwdriver or other suitable tool. Ensure a secure connection that prevents the conduit from detaching.
- Mount the FMC: Securely fasten the FMC to the desired surface using appropriate fasteners, such as straps or clamps. Ensure that the conduit is adequately supported at regular intervals to prevent sagging.
- Make bends and turns: If necessary, use a conduit bender or conduit vise to create bends and turns in the FMC. Follow the bending instructions provided by the manufacturer and avoid exceeding the bending radius limits.
- Connect to electrical devices: Attach the FMC to electrical boxes, junction boxes, or other electrical devices using appropriate connectors. Ensure proper grounding connections as required by electrical codes.
- Secure cables within the FMC: Place the electrical cables or wires inside the FMC and secure them using appropriate cable ties or clamps. This helps to prevent movement and protect the cables within the conduit.
- Verify the installation: Inspect the FMC installation to ensure it meets all applicable electrical codes and regulations. Check for proper support, secure connections, and correct routing.
It’s essential to consult local electrical codes and regulations and follow the manufacturer’s instructions for the specific FMC system being installed. If you are unsure about any aspect of the installation process, it is recommended to consult a licensed electrician for assistance.
How to choose the right flexible conduit?
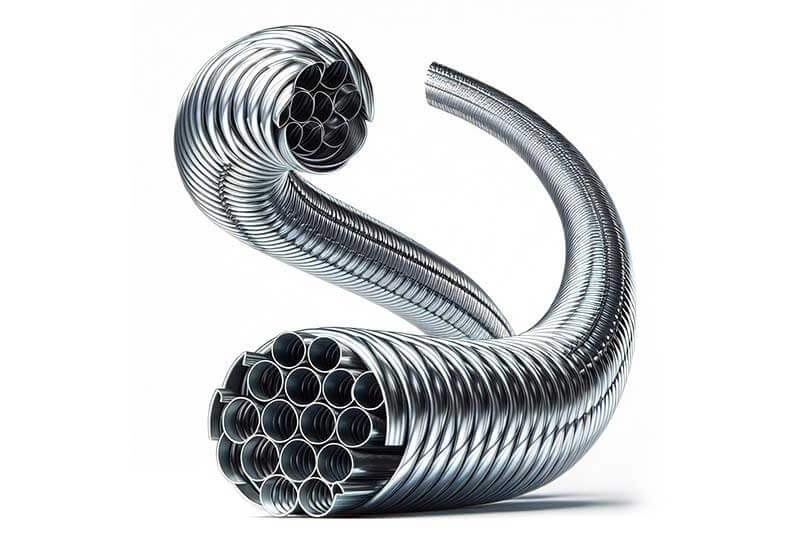
When selecting the appropriate corrugated conduit product, it is wise to consider the following five common factors:
- Requirement: Evaluate the basic needs of your project or application based on the environment. Will the conduit be buried in a typical residential building or exposed to outdoor conditions for an extended period? Will it be used in a consistently damp location? By considering the advantages and disadvantages of various corrugated conduit products mentioned earlier, you can make an informed choice. If you are a project contractor or distributor, feel free to contact us for more purchasing advice.
- Budget: Choose a product that suits your project within your budget. This ensures that you meet the project requirements while minimizing procurement costs. Additionally, when considering the budget, it is important to include transportation and installation costs. For example, as mentioned earlier, metal conduits are heavier, resulting in increased transportation and installation expenses. Therefore, these costs should be factored into the overall budget.
- Local Code: Once you have determined the material and type of conduit, it is essential to understand the local requirements and regulations for such conduits. Purchasing corrugated conduit products that comply with local standards is crucial. Non-compliant products will not pass inspection. For example, if you are using ENT conduit in North America, you must purchase products that comply with UL1653 and CSA C22.2 No. 227.1 standards to meet local installation requirements and avoid additional costs.
- Size & Quantity: Determine the number of wires or cables that need to be accommodated within a single conduit, as well as the estimated length and quantity required for your installation needs. This helps you stay within your budget and save costs.
- Brand: Different types of conduits are associated with different brands. Purchasing products from reputable brands may come at a slightly higher price, but the difference in quality is significant. Well-known brands have their products certified according to local standards. Choosing unknown or generic products may lead to quality issues that result in losses far exceeding the value of the products themselves. If local brand prices seem too high or you require large quantities, you can also consider purchasing directly from manufacturers such as Ledes. As a manufacturer, Ledes offers competitive prices as there are no brand intermediaries. With over 14 years of experience in exporting, serving thousands of customers, we can ensure timely delivery of your order once specifications and requirements are confirmed. If you would like to consult us regarding product-related inquiries, please click here to send us an email.
Can a flexible conduit be buried?
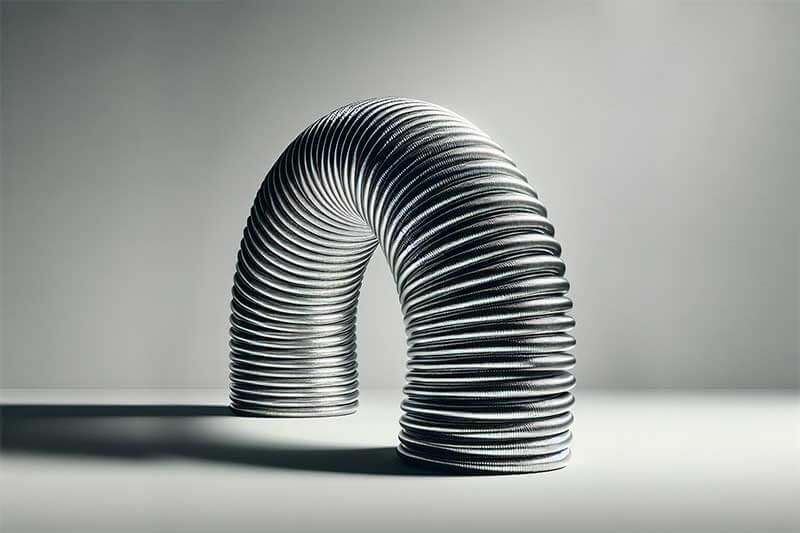
Yes, certain types of flexible conduit can be buried. In North America, the NEC (National Electrical Code) provides guidelines for the permissible uses of different types of conduits.
For ENT (Electrical Nonmetallic Tubing) conduit, according to NEC Article 362.10 Uses Permitted, the 6th provision states:
“Encased in poured concrete or embedded in a concrete slab on grade where ENT is placed on sand or approved screenings, provided fittings identified for this purpose are used for connections.”
For LFNC (Liquidtight Flexible Nonmetallic Conduit) conduit, according to NEC Article 356.10 Uses Permitted, the 4th provision states:
“For direct burial where listed and marked for the purpose.”
To determine whether the specific flexible conduit you are purchasing can be buried, it is necessary to consult the relevant local permit documents and adhere to local regulations.
Which is better, plastic or metal conduit?
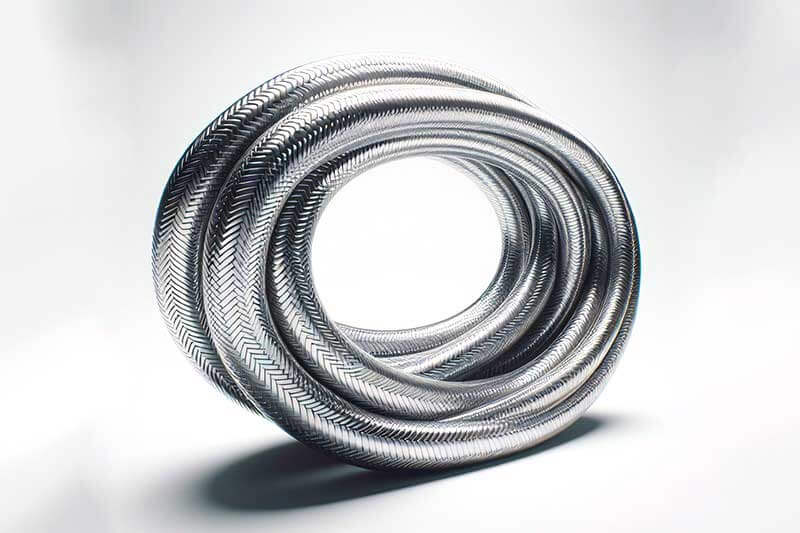
There is no definitive answer to whether plastic or metal conduit is better. It depends on which one is more suitable for your specific needs, as they each have their own advantages and disadvantages.
Advantages and disadvantages of metal conduit:
Metal conduit is often the preferred and more traditional choice for homeowners in their electrical systems. It has a long lifespan and is generally the most durable option. Metal conduits are typically made of copper, brass, cast iron, or steel. The main advantage of metal conduit is its higher hardness and longer theoretical lifespan. However, metal conduit is heavier, resulting in higher transportation and installation costs, and it can be prone to rusting, leading to increased maintenance expenses. Manufacturers have come up with solutions to address the rusting issue, such as surface coatings or the use of liquidtight flexible metal conduit (LFMC) that has a plastic coating, usually made of PVC. However, these solutions increase the weight and diameter of the metal conduit.
Advantages and disadvantages of plastic conduit:
The main advantage of plastic conduit is its lightweight nature and resistance to rust, overcoming the drawbacks of metal conduit. The reduced weight translates to cost savings in transportation and installation, and it is easier to cut, connect, and bend. With advancements in technology, plastic conduit has also improved in terms of heat resistance, corrosion resistance, and other properties, making it suitable for most residential and commercial building needs. The main drawback of plastic conduit is that it is not as hard as metal conduit, so it may be prone to damage in certain extreme situations. Additionally, plastic conduit may not have the same heat resistance and UV resistance as metal conduit, potentially leading to accelerated aging and the risk of breakage if used in such environments over a long period.
Therefore, based on the above comparison, it is evident that plastic and metal conduits have their own advantages and disadvantages, and they complement each other. Choosing the appropriate material based on your specific needs or project requirements is the wise choice.
How do you run a conduit around corners?
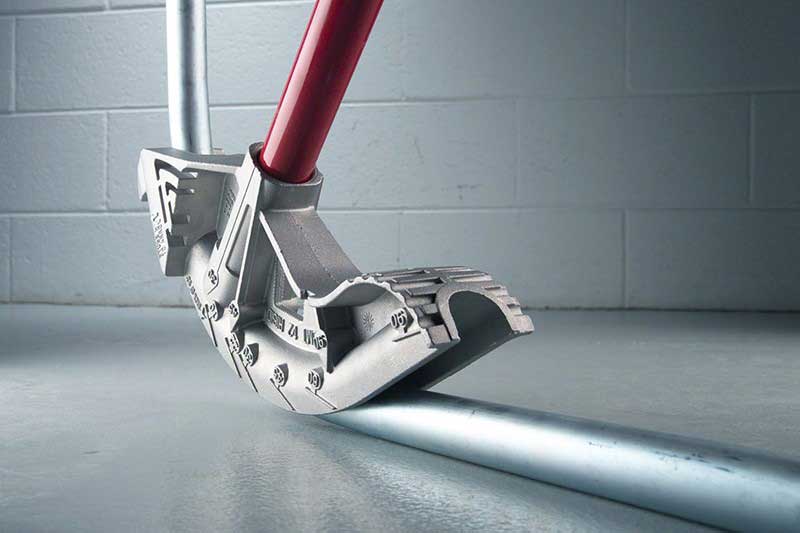
- Conduit Bending: Regardless of whether it’s metal or plastic conduit, you can use tools to bend the conduit to the desired angle. The specific process may vary depending on the conduit material, but generally, a conduit bender or a bending tool is used to achieve the desired bend angle.
- Use Conduit Fittings: Conduit fittings such as bends or elbows are designed to provide smooth corner transitions without damaging the conduit. In North America, for example, standard conduit elbow fittings are available in various angles such as 22.5°, 45°, 90°, etc. You can select the appropriate fitting based on your conduit size and connect it to achieve the desired corner angle.
It’s important to note that if you’re using PVC conduit, you must use specialized PVC glue or adhesive to ensure a secure connection that won’t come apart.
- Use PVC Flex Conduit: If the corner angle is not too sharp, using flexible PVC conduit can be a convenient option. PVC flex conduit is made of plastic and can be easily bent by hand without the need for specialized bending tools. This makes the installation process more convenient, especially for smaller angle bends.
When can you use flexible conduit?
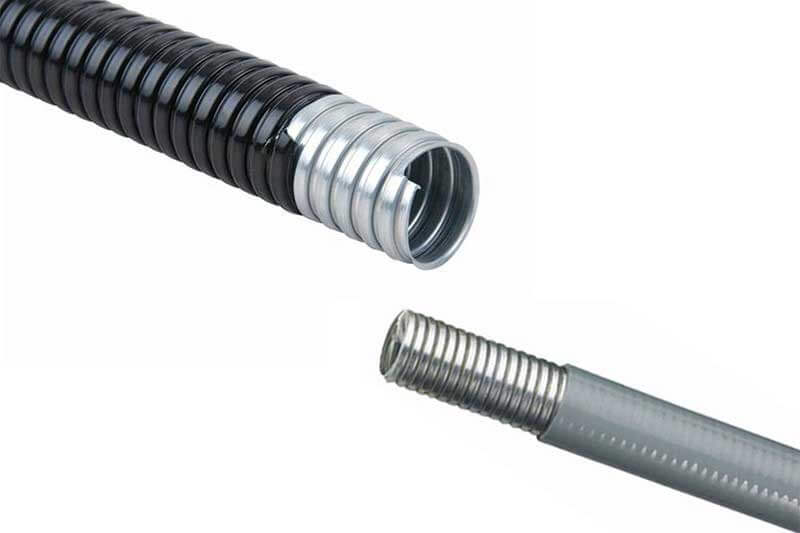
According to the NEC (National Electrical Code) guidelines, flexible conduits can be used in various situations. Here are the general applications:
ENT (Electrical Nonmetallic Tubing) and LFNC (Liquidtight Flexible Nonmetallic Conduit): These conduits are suitable for being encased in poured concrete, buried underground, or used in ceilings and suspended installations. They can also be used on the ground, such as for solar power systems or outdoor installations, as plastic conduits have good UV and sunlight resistance.
FMC (Flexible Metal Conduit): FMC is suitable for use in dry environments because it has a lower resistance to rust. It can be used for various applications where flexibility is required, such as in mechanical equipment, high-temperature environments, and ground installations like solar energy systems or outdoor installations. However, in environments with significant dust or oil/gas presence, it’s important to use the liquid-tight series of conduits to ensure safety.
LFMC (Liquidtight Flexible Metal Conduit) and LFNC (Liquidtight Flexible Nonmetallic Conduit): These conduits are designed for use in wet locations, as they provide good water resistance. They can be used in environments where moisture is present, ensuring protection against water ingress. LFMC and LFNC conduits are suitable for applications requiring flexibility.
Is flexible conduit watertight?
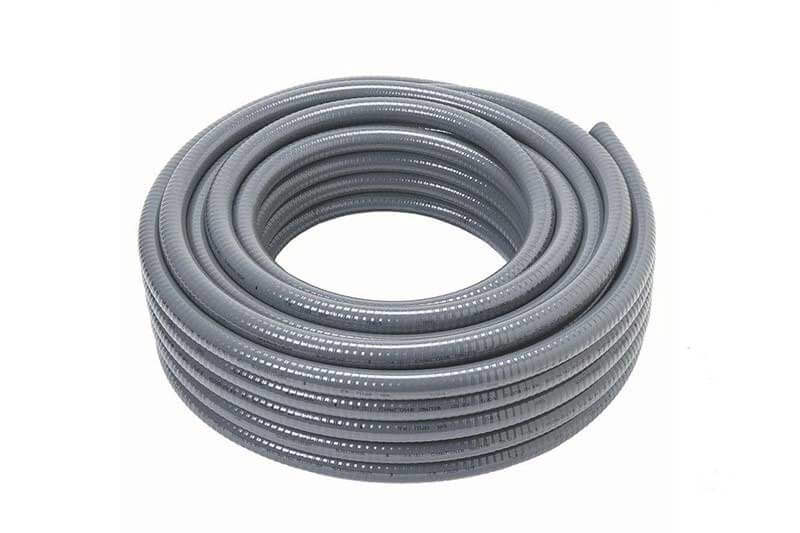
Not all flexible conduits are watertight. In general, FMC (Flexible Metal Conduit) and ENT (Electrical Nonmetallic Tubing) are not designed to be watertight. For watertight applications, conduits with a “liquid tight” designation, such as LFMC (Liquidtight Flexible Metal Conduit) and LFNC (Liquidtight Flexible Nonmetallic Conduit), should be used.
It’s important to understand that FMC and ENT conduits do not have built-in waterproofing features, including their connections. ENT, being made of plastic, has low water absorption properties, so it can tolerate small amounts of water without significant issues. FMC, on the other hand, is made of metal and relies on a thin coating, which doesn’t provide substantial waterproofing.
Conduits from the liquid tight series, on the other hand, have reinforced plastic outer layers and waterproof connections, making them suitable for use in wet environments, ensuring the safety of your cables.
Conclusion
Flexible electrical conduit provides a versatile solution for various electrical installations and plays a vital role in a wide range of applications. Their importance lies in their ability to provide flexibility, protection, and versatility to electrical wiring systems.
These conduits are extensively used in residential, commercial, and industrial settings.
They are indispensable in applications such as concrete encasement, burial underground, ceiling and suspended installations, as well as outdoor installations like solar power systems. The flexibility of these conduits allows for easy installation around obstacles, making them ideal for complex wiring setups.
If you have any further questions or require assistance with flexible electrical conduits, please feel free to reach out to us via email or summit a form. We are here to help you meet your electrical conduit needs.