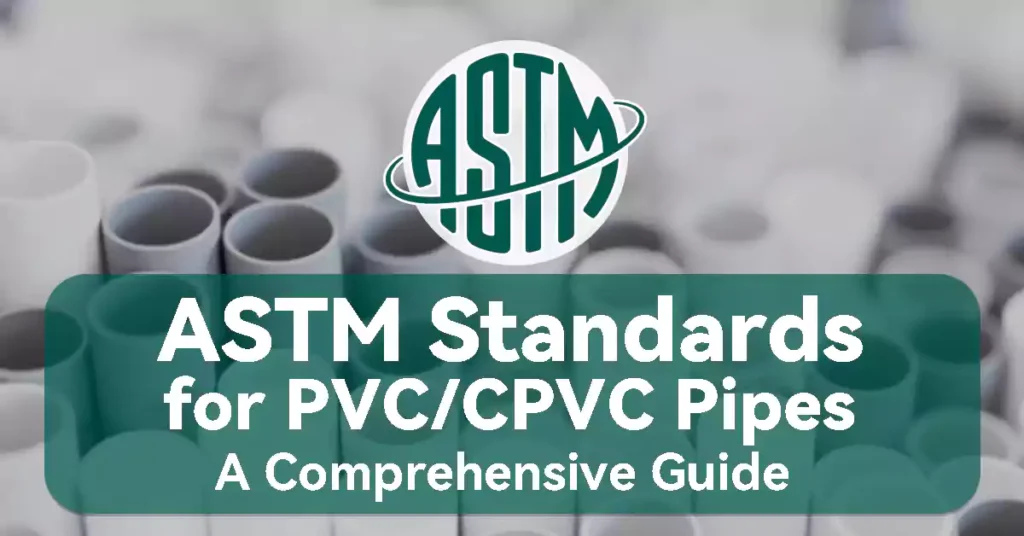
Índice
Polyvinyl Chloride (PVC) and Chlorinated Polyvinyl Chloride (CPVC) pipes and conduits are widely used in various industries due to their durability, chemical resistance, and cost-effectiveness. To ensure the quality and performance of these materials, the American Society for Testing and Materials (ASTM) has established a series of standards. These standards are crucial for manufacturers, engineers, and contractors to adhere to industry best practices and regulatory requirements.
In this comprehensive guide, we will explore the key ASTM standards applicable to PVC and CPVC pipes and conduits, their significance, and how they contribute to the safety and efficiency of piping systems.
The American Society for Testing and Materials (ASTM), now known as ASTM International, is a globally recognized organization that develops and publishes voluntary consensus standards. Founded in 1898, ASTM’s mission is to improve product quality, enhance safety, and facilitate trade through the standardization of materials, products, systems, and services.
For PVC and CPVC pipes, ASTM standards cover aspects such as material composition, physical properties, performance criteria, and testing methodologies. These standards help ensure consistency, reliability, and compatibility across different applications and environments.
Several ASTM standards apply specifically to PVC and CPVC pipes. Understanding these standards is essential for engineers, contractors, and quality control personnel to select the appropriate piping materials for their projects. Some of the most commonly referenced ASTM standards include
ASTM D1784 – 20: Standard Classification System and Basis for Specification for Rigid Poly(Vinyl Chloride) (PVC) Compounds and Chlorinated Poly(Vinyl Chloride) (CPVC) Compounds
ASTM D1784 – 11: Standard Specification for Rigid Poly(Vinyl Chloride) (PVC) Compounds and
Chlorinated Poly(Vinyl Chloride) (CPVC) Compounds
ASTM D2665: Standard Specification for Poly(Vinyl Chloride) (PVC) Plastic Drain, Waste, and Vent
Pipe and Fittings
ASTM E662 – 17a: Standard Test Method for Specific Optical Density of Smoke Generated by Solid
Materiais
ASTM F442/F442M-23: Standard Specification for Chlorinated Poly(Vinyl Chloride) (CPVC) Plastic Pipe (SDR–PR)
ASTM F512 – 12: Standard Specification for Smooth-Wall Poly(Vinyl Chloride) (PVC) Conduit and
Fittings for Underground Installation
ASTM D1785 – 21: Standard Specification for Poly(Vinyl Chloride) (PVC) Plastic Pipe, Schedules 40, 80, and 120
Each standard addresses specific aspects of pipe manufacturing and performance, ensuring compliance with safety and regulatory requirements. In the following sections, we will delve into the specific ASTM standards applicable to PVC and CPVC pipes, highlighting their scope and relevance.
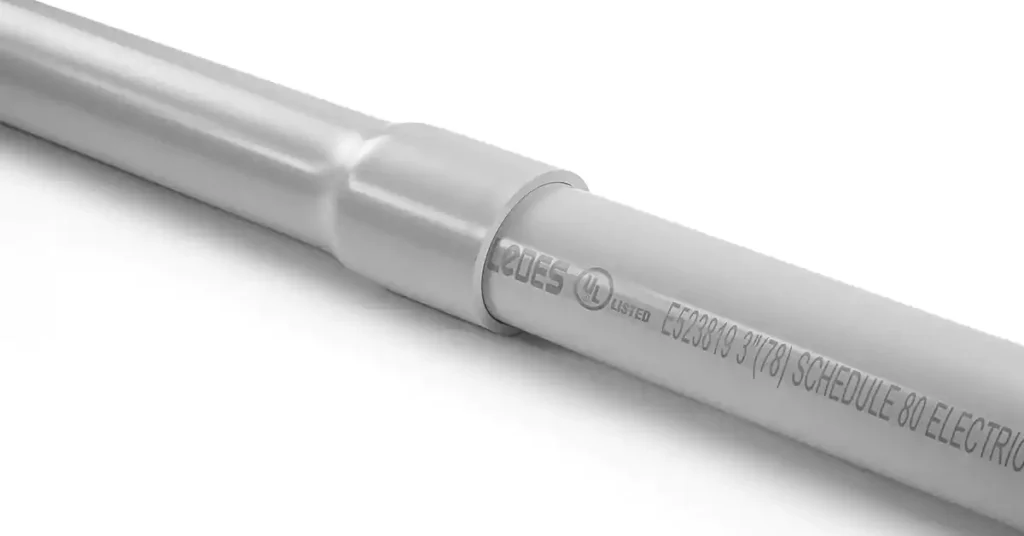
ASTM D1784 is the standard specification that covers the classification system and physical properties requirements for rigid PVC and CPVC compounds used in the production of pipes, conduits and fittings. It serves as the foundation for material selection, quality control, and performance evaluation in various applications.
The primary purpose of ASTM D1784 is to establish a uniform classification system for rigid PVC and CPVC compounds. This standard ensures that the materials used in manufacturing meet specific quality, strength, and durability requirements, enabling consistent performance across different applications.
ASTM D1784 classifies PVC and CPVC compounds based on their physical properties, including:
- Base resin
- Impact resistance (lzod)
- Tensile strength & Modulus of elasticity in tension
- Deflection temperature under load
- Flammability
These properties are defined in Table 1 of the standard, where each class of material is represented by a unique cell classification code, such as 12454. This code sequentially represents the resin type, impact strength, tensile strength, modulus of elasticity, and heat deflection temperature rating.
PVC and CPVC compounds under ASTM D1784 typically consist of:
Base resin: At least 80% vinyl chloride (PVC) or chlorinated vinyl chloride (CPVC)
Lubricants: To aid in processing and prevent surface defects
Stabilizers: To enhance thermal and UV resistance
Fillers: Sometimes added to improve mechanical properties or reduce costs
ASTM D1784 specifies different material properties that must be met for a compound to qualify under the standard.
For PVC Compounds:
Impact Strength (Izod): ≥ 34.7 J/m (0.65 ft-lbf/in.) (ASTM D256)
Resistência à tracção: ≥ 48.3 MPa (7000 psi) (ASTM D638)
Modulus of Elasticity in Tension: ≥ 2758 MPa (400,000 psi)
Heat Deflection Temperature (HDT): ≥ 70°C (158°F) under a load of 1.82 MPa (ASTM D648)
For CPVC Compounds:
Impact Strength (Izod): ≥ 34.7 J/m (0.65 ft-lbf/in.) (ASTM D256)
Resistência à tracção: ≥ 48.3 MPa (7000 psi) (ASTM D638)
Modulus of Elasticity: ≥ 2758 MPa (400,000 psi) (ASTM D638)
Heat Deflection Temperature: ≥ 50°C (122°F) after annealing for 24 hours
Resistência à chama: Burning extent ≤ 25 mm, extinguishing within 10 seconds (ASTM D635)
To ensure proper handling and traceability, ASTM D1784 specifies that PVC/CPVC materials should be commercially packaged with detailed labeling, including:
Material name and grade
Manufacturer’s name
Batch and lot number
Quantity
Shipping information
Contract or order reference
Proper packaging and labeling help in maintaining product integrity and ensuring compliance with industry standards.
The compounds classified under ASTM D1784 are used in the manufacturing of various extruded and molded products, including:
Extruded pipes (for water supply, drainage, and industrial applications)
Injection-molded fittings (used for pressure and non-pressure piping systems)
Pressure-rated piping systems (requiring additional long-term stress considerations)
For high-temperature CPVC applications, Grade 10/11 is typically used due to its superior heat resistance and long-term performance in hot water or industrial chemical environments.
ASTM D1784 serves as the foundation for PVC and CPVC material classification, ensuring that products meet mechanical, thermal, and chemical performance requirements.
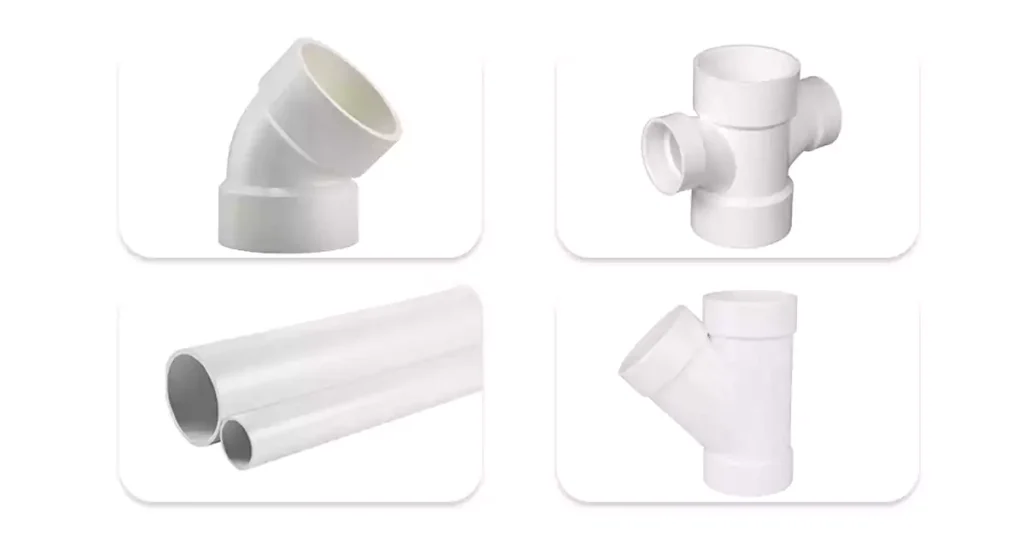
ASTM D2665 is a widely recognized standard that specifies the requirements for Poly(Vinyl Chloride) (PVC) plastic drain, waste, and vent (DWV) pipes and fittings. This standard ensures that PVC DWV piping systems meet stringent material, dimensional, and mechanical property requirements to ensure long-term performance, safety, and durability in sanitary drainage applications.
PVC pipes and fittings manufactured under ASTM D2665 are primarily used for gravity-fed sanitary drainage, waste disposal, and venting applications in both residential and commercial plumbing systems. The standard provides essential guidelines for material composition, physical properties, impact resistance, and pipe stiffness to ensure high reliability in DWV systems.
Measurement Method: All dimensions, including outside diameter (OD), wall thickness, and length, must be determined following ASTM D2122.
Standard Lengths: Pipes are typically manufactured in lengths of 10 ft (3.05 m) and 20 ft (6.10 m), with an allowable tolerance of +1.0 in.
Outside Diameter and Wall Thickness: The OD and wall thickness must conform to the specifications detailed in Table 2 of ASTM D2665.
Acessórios: Drain, waste, and vent fittings should comply with ASTM F1866 to ensure proper fit and function within the piping system.
Pipe stiffness (PS) is a key performance criterion for PVC DWV piping systems, ensuring resistance to deformation under load. The pipe stiffness is determined using ASTM D2412, which measures the pipe’s ability to withstand 5% deflection without structural failure.
Minimum stiffness values for different pipe diameters are provided in Table 3 of ASTM D2665, ensuring structural integrity in buried and above-ground applications.
Testing Method: Impact resistance is determined using ASTM D2444, which involves a falling weight impact test (Tup C).
Critérios de aceitação: Typically, 9 out of 10 specimens must pass without showing signs of cracking or splitting.
Fittings Impact Strength: Individual fittings, especially at parting lines, must withstand a minimum force of 750 lbf/ft (11 kN/m) without any visible fractures, as specified in section 6.3.2 of ASTM D2665.
ASTM D2665 encompasses various fittings essential for DWV systems, including:
Standard Fittings: Elbows, tees, wyes, and couplings that conform to ASTM D3311, ensuring standardized dimensions and configurations.
Short-Length Pipes: Short sections of DWV pipes that comply with ASTM F2135, suitable for specific installation requirements.
Threaded Fittings: Components with threads that must meet the specifications of ASTM F1498 to ensure proper sealing and mechanical strength.
To ensure consistent product quality, manufacturers must perform regular testing and adhere to the specified requirements. This includes calculating the Lower Confidence Limit (LCL) for pipe stiffness to ensure that 99% of all manufactured pipes meet or exceed the required stiffness values, providing additional quality assurance and reliability.
By adhering to ASTM D2665, manufacturers and plumbing professionals can ensure that PVC DWV piping systems are reliable, durable, and suitable for their intended applications, thereby safeguarding public health and infrastructure integrity.
ASTM E662-17 is a standard test method designed to evaluate the smoke generation and optical density characteristics of solid materials under both pyrolytic (non-combustion) and flaming (combustion) conditions. The main objective is to quantify how much the material attenuates light by producing smoke, which is reported as a specific optical density (Ds).
The primary objective of ASTM E662-17 is to measure how much smoke a material generates under specified exposure conditions. This is crucial for evaluating materials in environments where smoke density can impact visibility and evacuation during a fire. However, it is important to note that:
- The test results provide specific optical density (Ds) values that are applicable only to the tested sample in its given form and thickness.
- The method does not account for toxicological effects of the smoke or its physiological impact on human vision.
- The test does not predict smoke behavior in real-world fire conditions, where factors such as ventilation, combustion dynamics, and multi-material interactions influence smoke production.
The test is conducted inside a closed smoke density chamber where a material sample is exposed to a controlled heat source. Smoke accumulation is measured using a photometric system that tracks light attenuation over time, allowing for the calculation of the specific optical density (Ds). The test includes two conditions:
The sample is exposed to a 2.5 W/cm² radiant heat flux without direct flame application.
This condition simulates scenarios where materials generate smoke due to heat exposure without ignition.
The same 2.5 W/cm² heat flux is applied, but with the addition of a six-tube burner that introduces a direct flame to ignite the material.
This setup evaluates the smoke production when the material is actively burning.
The smoke generated under both conditions is analyzed through a photometric system that measures light transmission through the chamber. The reduction in light intensity is used to calculate the specific optical density.
The specific optical density (Ds) is determined using the following formula:
Ds=G⋅{log(100/T)+F}
Where:
Ds = Specific optical density
G = Geometric factor (typically 132)
T = Percentage of light transmitted through the smoke
F = A correction factor accounting for the initial light transmission conditions
This equation expresses how much the smoke reduces visibility by measuring the logarithmic decrease in light transmission.
- The results are expressed as specific optical density (Ds) values, indicating the concentration of smoke in the chamber.
- Samples must be uniform in composition, and their thickness should not exceed 1 inch (25.4 mm).
- If a sample exhibits self-ignition or any unexpected combustion behavior, additional testing is required to ensure data reliability.
- The values obtained are not inherent properties of the material and may vary under different fire conditions.
ASTM E662-17 plays a crucial role in assessing materials for applications where smoke production is a concern, such as:
- Building materials (e.g., wall panels, flooring, insulation).
- Electrical conduit and piping systems, where smoke density can affect fire safety compliance.
- Transportation sectors, including aircraft, railways, and automotive industries, where reduced visibility due to smoke can impact passenger safety.
By adhering to this standard, manufacturers, designers, and regulatory bodies can better evaluate and compare materials based on their smoke generation potential, leading to safer product development and improved fire safety standards.
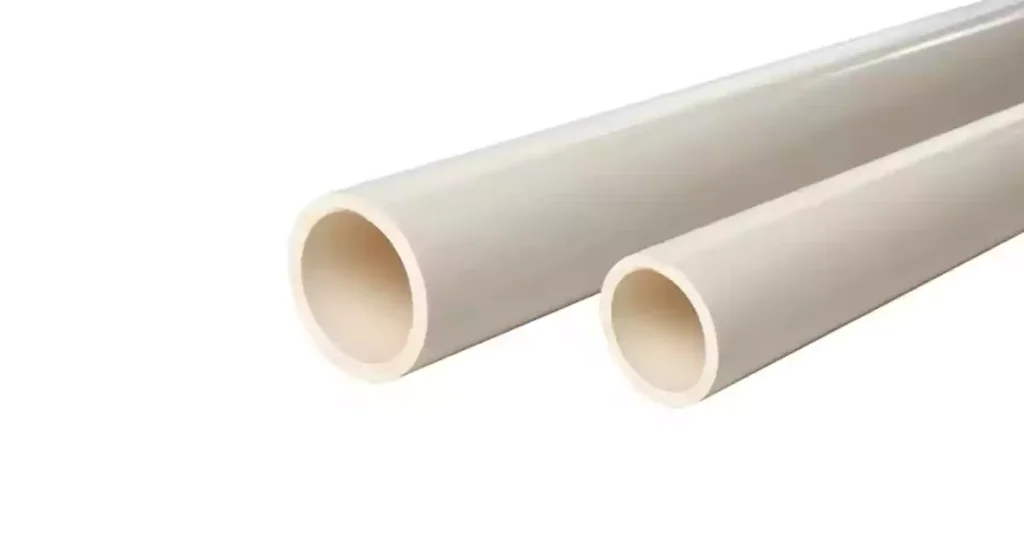
ASTM F442/F442M-23 is a standard specification that defines the requirements for Chlorinated Polyvinyl Chloride (CPVC) plastic pipes used in pressurized water distribution systems. This standard establishes material properties, dimensions, classification, and performance criteria to ensure the structural integrity and long-term reliability of CPVC piping under varying temperature and pressure conditions.
The primary objective of ASTM F442/F442M-23 is to specify the dimensions, material properties, and pressure ratings of CPVC pipes used for water distribution. It ensures that CPVC pipes are manufactured to meet consistent quality standards for hydrostatic strength, durability, and chemical resistance, making them suitable for both hot and cold water applications in residential, commercial, and industrial settings.
Pipes covered by ASTM F442/F442M-23 are manufactured from chlorinated poly(vinyl chloride) (CPVC) compound, formulated to provide enhanced temperature resistance, corrosion resistance, and chemical compatibility compared to conventional PVC pipes.
The standard classifies CPVC pipes based on two key rating systems:
- Standard Dimension Ratio (SDR-PR System): Pipes are categorized based on a fixed ratio of outside diameter to wall thickness (SDR) and a corresponding pressure rating (PR).
- Class System: Pipes are assigned a specific pressure class, indicating their ability to withstand internal pressure at a defined temperature.
Covers six Standard Dimension Ratios (SDR):
SDR: 11, 13.5, 17, 21, 26, and 32.5.
SDR, calculated as the ratio of outer diameter to minimum wall thickness (rounded to 0.5), directly correlates with pressure ratings, enabling uniform performance across all nominal pipe sizes. Lower SDR values (e.g., SDR11) indicate thicker walls for higher-pressure applications, while higher SDRs (e.g., SDR32.5) suit lower-pressure environments. Hydrostatic design stresses, derived from long-term testing, further classify pipes based on their pressure-bearing capabilities at 73°F (23°C) and 180°F (82°C).
The CPVC compounds used in these pipes must comply with ASTM D1784, ensuring the material meets strict mechanical and physical properties. Additionally, the hydrostatic design basis (HDB) and hydrostatic design stress (HDS) values are determined according to ASTM D2837, with the following key properties:
HDB at 73 °F (23 °C): 4000 psi (28 MPa)
HDB at 180 °F (82 °C): 1000 psi (7.0 MPa) or 1250 psi (8.6 MPa)
Each CPVC pipe is designated with a material code that includes the ASTM type and grade, followed by the design stress values at 73°F (23°C) and 180°F (82°C), expressed in units of 100 psi (0.7 MPa). The complete material code consists of four letters and six numerical figures for proper identification and classification.
Material designation codes (e.g., CPVC 4120-05 or CPVC 4120-06) reflect design stresses at both temperatures.
Rework material must be clean and meet all specification requirements.
The standard mandates stringent testing to validate pipe quality:
- Dimensional Tolerances:
Outside Diameter (OD): Conforms to Table 1 (per ASTM D2122), with tolerances for out-of-roundness applicable pre-shipment.
Espessura da parede: Conforms to Table 2 (per ASTM D2122), with a maximum thickness variation of 12%.
- Pressure Testing:
Sustained Pressure Test: Six specimens withstand 1,000 hours at pressures. Failure of two specimens results in rejection.
Burst Pressure Test: Five specimens are pressurized to failure within 60–70 seconds, with minimum thresholds.
Accelerated Regression Test (Optional): An alternative to sustained/burst tests, this method uses regression analysis (per ASTM D2837) to project 100,000-hour hydrostatic strength.
Lower confidence limit (LCL) exceeds 15% of extrapolated LTHS.
Statistical parameters (M ≤ 0 or slope b ≥ 0) indicate unreliable projections.
Flattening Test: Three specimens compressed to 40% of their diameter must show no cracks or breaks.
Legible, permanent markings spaced ≤5 ft (1.5 m) include:
Nominal Pipe Size (e.g., NPS 2 or NPS 50).
Material code (e.g., CPVC4120-05).
SDR (e.g., SDR13.5).
Pressure ratings at 73°F and 180°F (e.g., “400 psi at 73°F, 100 psi at 180°F”).
ASTM designation (F442, F442M, or F442/F442M).
Manufacturer’s name/trademark and production code.
Potable water pipes: Evaluator laboratory’s seal/mark.
CPVC pipes must meet strict performance and quality criteria as outlined in ASTM F442/F442M-23. This includes compliance with:
- Minimum hydrostatic design stress requirements to ensure long-term pressure resistance.
- Wall thickness and dimensional tolerances for uniformity and reliability.
- Material purity and consistency to guarantee high performance in demanding applications.
Manufacturers producing CPVC pipes under this standard must conduct regular quality control checks to maintain compliance, ensuring that every batch meets the specified standards.
The standard explicitly excludes pipes for venting combustion gases. Its primary focus is water supply systems, where CPVC’s corrosion resistance, thermal stability, and cost-effectiveness make it ideal for residential, commercial, and industrial use.
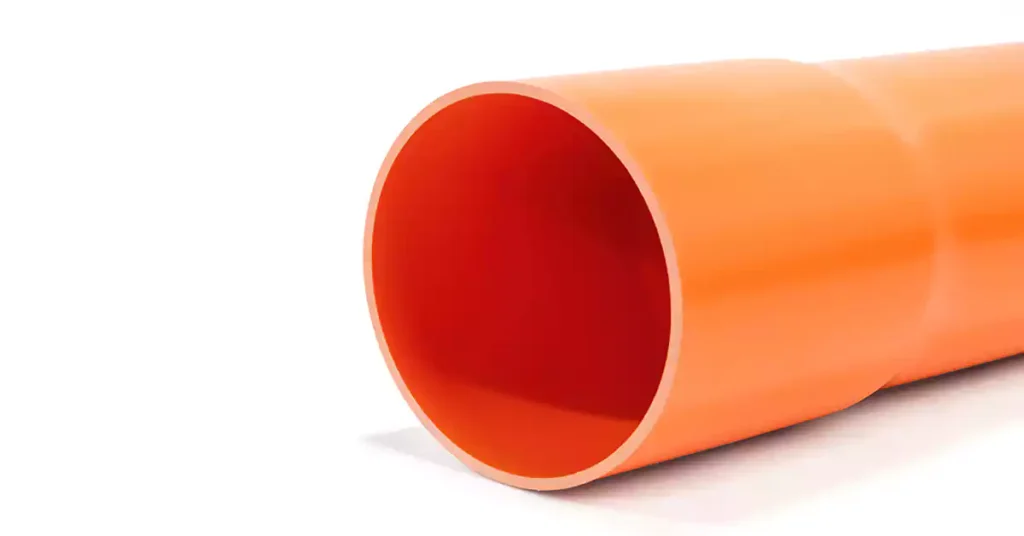
ASTM F512-12 is a standard specification that defines the requirements for smooth-wall polyvinyl chloride (PVC) conduit and fittings designed for underground applications, primarily in electrical and communication systems. The standard categorizes conduits into two main types based on their intended installation method: Encased Burial (EB) conduit, which requires concrete encasement for structural support, and Direct Burial (DB) conduit, which can be buried directly in the ground without additional reinforcement. The primary purpose of this standard is to ensure uniformity in conduit performance, durability, and compatibility while providing protection for electrical and communication cables in underground environments.
The conduits and fittings covered under ASTM F512-12 are manufactured from rigid polyvinyl chloride (PVC), complying with ASTM D1784 material specifications. The acceptable PVC cell classifications include 12254-A/B and 12164-B5, ensuring high durability, mechanical strength, and resistance to environmental stressors. Additionally, the specification allows for both single-wall conduit and coextruded honeycomb-core conduit designs, with conduit joints available in either integral bell or separate coupling configurations.
ASTM F512-12 classifies conduits into five types based on pipe stiffness and intended burial method:
EB-20 – Designed for encasement in concrete.
EB-35 – Designed for encasement in concrete with higher stiffness than EB-20.
DB-60 – Designed for direct burial without concrete encasement.
DB-100 – Designed for direct burial, offering greater stiffness than DB-60.
DB-120 – Designed for direct burial, providing the highest stiffness among DB conduits.
Additionally, the specification covers molded and fabricated fittings that are compatible with all conduit types listed above.
The standard specifies conduit dimensions and tolerances, including wall thickness, socket depths, and length requirements. These dimensions are determined in accordance with ASTM D2122 test methods.
- Conduit lengths are typically supplied in 20 ft (6.1 m) or 25 ft (7.6 m) sections, unless otherwise agreed upon by the manufacturer and purchaser.
- Integral bells and socket dimensions follow two primary fitment systems:
- Interference Fit System, following ASTM D2466 specifications.
- Clearance Fit System, with tolerances defined within ASTM F512-12.
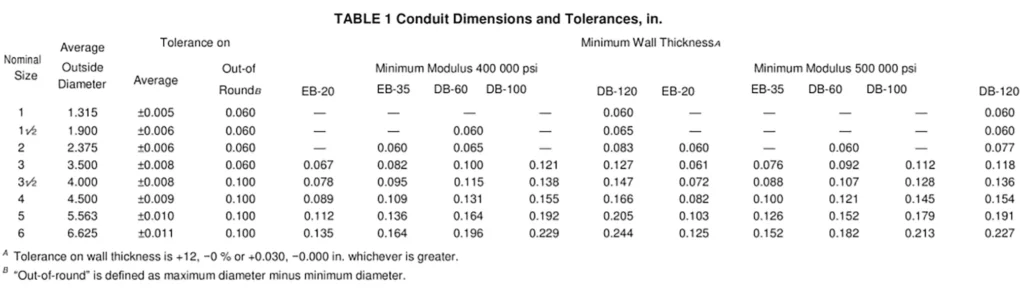
To ensure compliance with performance requirements, conduits and fittings undergo a series of standardized tests:
Validates fusion integrity by exposing specimens to acetone, ensuring no surface deterioration or laminations.
Measures conduit stiffness at 5% deflection. The required minimum stiffness values are:
EB-20: ≥ 20 psi
EB-35: ≥ 35 psi
DB-60: ≥ 60 psi
DB-100: ≥ 100 psi
DB-120: ≥ 120 psi
Evaluates the conduit’s ability to withstand mechanical impact using Type A or Type B impact hammers. Conduits must pass impact testing with a minimum acceptable pass rate (e.g., 17 out of 20 samples meeting requirements).
Requisitos: Assesses toughness at 0°C (32°F) using a Type A or B tup (hammer). For example, a batch passes if 17 out of 20 specimens withstand the specified impact energy without cracking.
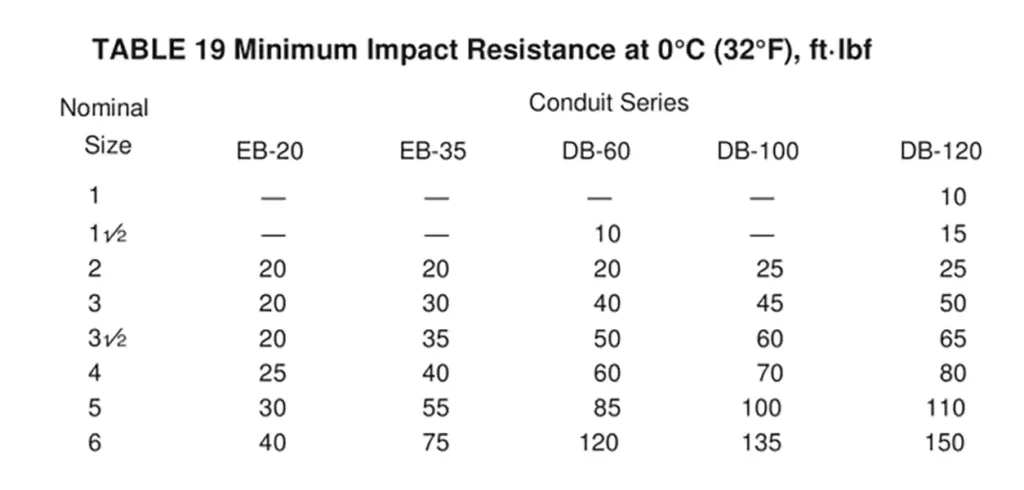
Conduits and fittings manufactured under ASTM F512-12 must meet the following quality and performance criteria:
Homogeneity: The material must be free of visible cracks, holes, foreign inclusions, or other defects that could compromise performance.
Uniformity: Conduits should be consistent in color, opacity, density, and mechanical properties to maintain product integrity.
Wall Thickness Compliance: The wall thickness of integral bells and sweeps must meet the minimum specifications to ensure structural reliability.
To ensure traceability and compliance, conduits and fittings must be clearly marked with essential information at intervals of 5 ft (1.5 m) or less. The markings include:
Manufacturer’s name or trademark
PVC cell classification (e.g., PVC 12254-A, PVC 12254-B, PVC 12164-B)
Conduit size and type (e.g., DB-60, EB-35)
Minimum wall thickness
Control number or batch code
ASTM designation (ASTM F512 for single extrusion; ASTM F512 COEX for coextruded products)
Additionally, sweeps and bends should be marked with their bend radius and angle (e.g., 18″ R – 30°), while fittings should be labeled with size, material type (PVC), and the ASTM F512 designation. If space constraints prevent direct marking on fittings, the required information should be included on the packaging.
ASTM F512-12 is pivotal in underground infrastructure for electrical and communication networks, offering solutions that balance flexibility, strength, and corrosion resistance. Its dual focus on concrete-encased and direct-burial applications ensures adaptability to diverse installation environments, from urban utility corridors to industrial sites. By enforcing stringent material and testing protocols, the standard mitigates risks of premature failure, ensuring conduits meet the demands of modern buried infrastructure systems.
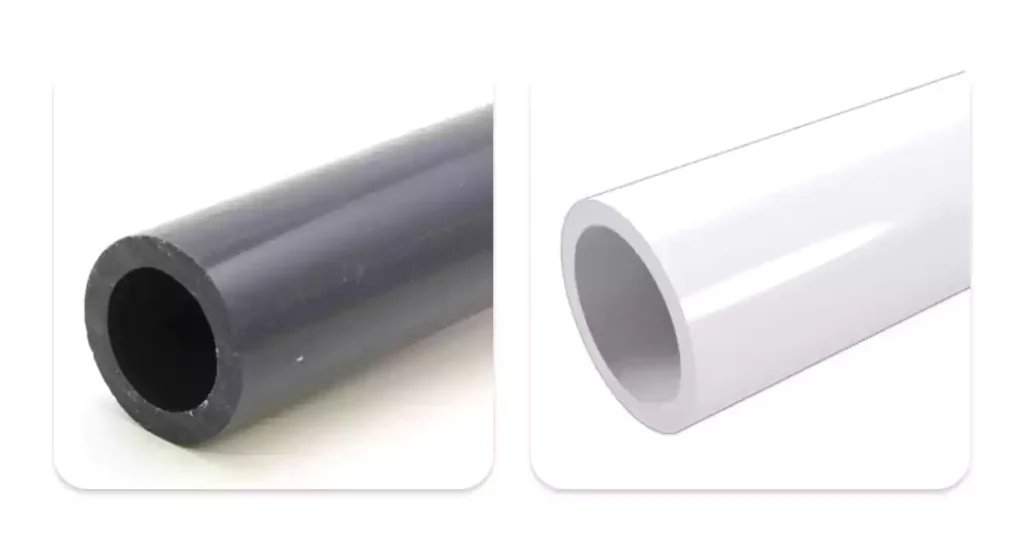
ASTM D1785-21 is a standard specification that defines the requirements for poly(vinyl chloride) (PVC) plastic pipes manufactured in Schedule 40, 80, and 120 wall thicknesses. This specification applies to pressure-rated pipes intended primarily for the conveyance of fluids, including potable water, in various plumbing and industrial applications. The standard provides guidelines for material composition, classification, dimensional tolerances, hydrostatic pressure ratings, and performance testing to ensure the quality, safety, and durability of PVC pipes used in fluid transportation systems.
This specification establishes six types/grades of PVC pipes, categorized based on hydrostatic design stress and long-term performance testing. It also aligns with ASTM D1784, which sets the material classification requirements for PVC compounds used in the manufacturing of these pipes.
ASTM D1785-21 classifies PVC pipes based on their type, grade, and hydrostatic design stress, ensuring consistent performance across different applications. This specification covers pipes produced in Schedule 40, 80, and 120 wall thicknesses, with each pipe clearly marked according to one of six designated type/grade/stress classifications.
Schedule 40: Standard-weight pipe for moderate-pressure applications.
Schedule 80: Heavy-duty pipe for higher-pressure systems.
Schedule 120: Extra-heavy pipe for specialized high-stress environments.
A key aspect of this classification is the hydrostatic design stress (HDS), which determines the long-term pressure-bearing capability of the pipe. These stresses are established through rigorous long-term testing, ensuring that the pipes can withstand sustained internal pressures without failure. The classification framework helps in selecting the appropriate pipe for different pressure applications, particularly in water distribution and industrial systems.
ASTM D1785-21 specifies that PVC pipes must be made from poly(vinyl chloride) (PVC) plastics with well-defined physical and chemical properties. The materials used must meet the standards set in ASTM D1784, specifically PVC 12454 or PVC 14333, ensuring durability, strength, and chemical resistance.
For potable water applications, the pipe must be tested and certified to meet NSF/ANSI Standard 14, ensuring it is safe for drinking water use. Pipes that pass this certification must display the appropriate approval mark.
Manufacturers can also use clean rework PVC material, but only from their own production process, and the final product must fully comply with ASTM D1785-21 requirements. This ensures consistent quality and performance across all PVC pipes.
The dimensional and tolerance requirements for PVC pipes are specified in Tables 1 and 2 of the standard. These dimensions are verified according to ASTM D2122, ensuring compliance with strict manufacturing tolerances. Key aspects include:
Outer diameter, wall thickness, and tolerances – ensuring pipes meet the required size specifications.
Out-of-roundness tolerances – applicable before shipment to ensure proper fit during installation.
To ensure durability and safety, ASTM D1785-21 mandates several critical tests for PVC pipes:
Pipes must withstand hydrostatic pressure for 1,000 hours at their designated stress level without failure (such as bursting or leaking).
Pipes must endure a short-term hydrostatic pressure test at four times the rated pressure for 60-70 seconds without failure.
Pipe specimens (minimum 2 inches long) are compressed between two parallel plates until they reach 40% of their original diameter or until the walls touch.
The specimen must not crack, split, or break under this pressure.
- Tests are conducted in a controlled laboratory environment at 73°F ± 4°F (23°C ± 2°C) with 50% ± 10% relative humidity, unless otherwise specified.
- For impact testing, specimens are conditioned at 32-35°F (0-1.6°C) for at least 30 minutes before testing.
These stringent testing procedures ensure that PVC pipes meet performance expectations for high-pressure applications.
To ensure traceability and compliance, ASTM D1785-21 requires all pipes to be clearly marked with the following information at intervals not exceeding 5 feet (1.5 meters):
Nominal pipe size (e.g., 2 inches (50 mm))
PVC material designation code (e.g., PVC 1120)
Schedule and pressure rating (e.g., Schedule 40, 200 psi)
ASTM designation and year (e.g., ASTM D1785-21)
Manufacturer’s name or trademark
Production code (identifying date, shift, plant, and extruder used in manufacturing)
Marking for potable water use (if applicable)
Manufacturers must ensure that markings remain legible after installation and inspection.
PVC pipes are regulated by multiple ASTM standards, depending on their intended application. The table below summarizes key differences:
6 Different ASTM Standard Comparing Chart
Padrões | Core Content | Key Tests | Applicable Pipe Types | Special Requirements |
ASTM D1784-20/11 | PVC and CPVC material classification | Izod impact, tensile strength, heat deflection | Extruded/injection-molded pipes & fittings. | Pressure pipes require HDB evaluation |
ASTM D1785-21 | PVC pressure pipes for pressurized water systems | Sustained pressure, burst pressure, flattening test | Schedule 40, 80, 120 pipes | Production code traceability; integral bell joints. |
ASTM D2665 | DWV (Drain, Waste, and Vent) pipe performance | Pipe stiffness, impact test | DWV pipes, elbows, tees | Threads must meet ASTM F1498 |
ASTM F442/F442M -23 | CPVC pressure pipe | Sustained burst /pressure, flattening test | SDR series pipes | Prohibits pneumatic testing |
ASTM E662-17 | Smoke density testing | Optical attenuation | Solid materials | Sample thickness ≤ 1 inch |
ASTM E512-12 | Smooth-wall PVC conduit for underground installation | Acetone immersion, Pipe stiffness, Impact | EB/DB conduit types | Material must meet 12254-A/B grade |
In summary, ASTM standards for PVC and CPVC pipes, all play a critical role in ensuring the reliability, safety, and performance of these piping systems across a variety of applications. From defining the material specifications and classifications to setting rigorous testing requirements, these standards ensure that PVC and CPVC pipes meet the necessary strength, durability, and chemical resistance criteria for use in water distribution, electrical conduit, and industrial systems.
By adhering to these established guidelines, manufacturers can produce pipes that perform consistently under pressure and environmental stress, while also complying with important safety and health regulations, such as those for potable water. The comprehensive requirements for materials, manufacturing processes, and pressure ratings outlined in these standards provide a clear framework for achieving high-quality pipe products.
Ultimately, understanding and following ASTM standards is essential for anyone involved in the design, manufacturing, and installation of PVC and CPVC piping systems, ensuring that the final products meet the highest performance and safety standards.
Contact our expert today if you still have any questions about ASTM standards or related; we will reply to you within 24 hours.
ASTM D1784 – 11: Standard Specification for Rigid Poly(Vinyl Chloride) (PVC) Compounds and
Chlorinated Poly(Vinyl Chloride) (CPVC) Compounds
ASTM D2665: Standard Specification for Poly(Vinyl Chloride) (PVC) Plastic Drain, Waste, and Vent
ASTM E662 – 17a: Standard Test Method for Specific Optical Density of Smoke Generated by Solid
ASTM F512 – 12: Standard Specification for Smooth-Wall Poly(Vinyl Chloride) (PVC) Conduit and