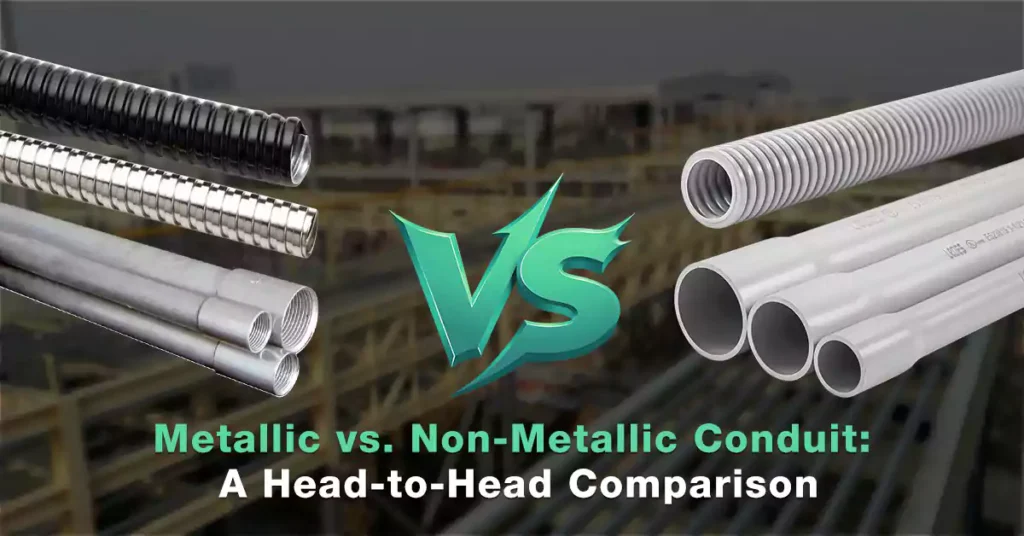
목차
Electrical conduit is an essential component in any electrical installation, providing a safe and organized pathway for electrical wiring. It protects wires from physical damage, environmental hazards, and electrical interference, ensuring the safety and longevity of the electrical system. There are several types of electrical conduit materials available, with the two most commonly used categories being metallic conduit and 비금속 도관.
Electrical Metallic Tubing (EMT) and Rigid Metal Conduit (RMC), while non-metallic conduit typically includes Polyvinyl Chloride (PVC) and Underground Feeder (UF) conduit. Each type has its unique characteristics, benefits, and limitations, which makes choosing the right material for your specific needs a critical decision in any electrical installation.
In this post, we aim to provide a comprehensive comparison between metallic and non-metallic conduit, helping readers make an informed choice based on factors such as durability, cost, ease of installation, and environmental conditions. Whether you’re installing a flexible conduit for a dynamic setup or opting for a more rigid option like PVC conduit for long-term durability, understanding the differences between these two conduit types will ensure that you choose the best solution for your wiring needs.
When considering electrical conduit options, it is important to understand the basic classifications of materials that make up these conduits. Metallic conduit is typically made from metal alloys such as steel or aluminum, providing a sturdy and durable option for wiring protection. On the other hand, non-metallic conduit is generally made from plastic polymers, such as PVC or HDPE, which are lighter and more flexible.
To better understand the differences, let’s first define and classify the two main categories of conduit types: metallic and non-metallic.
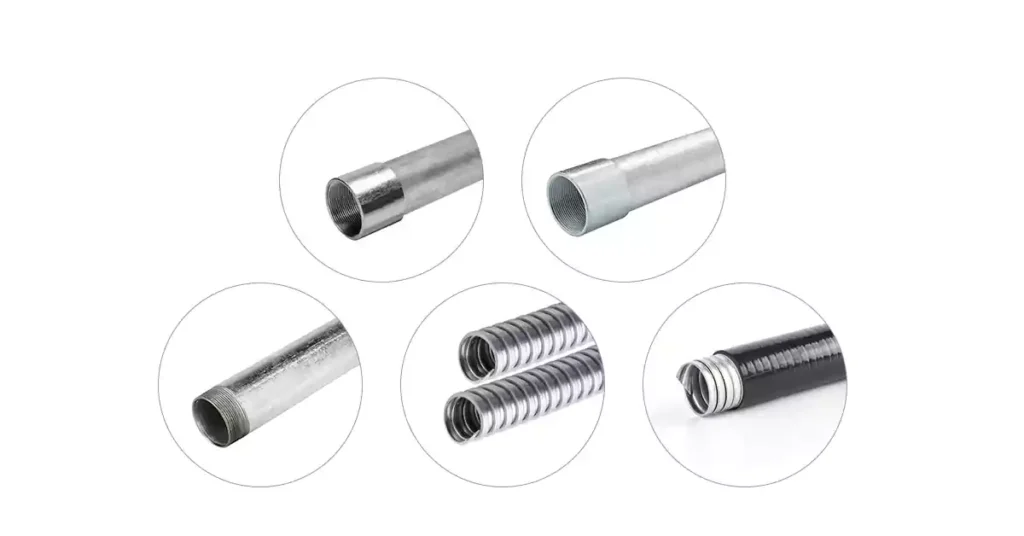
Metallic conduit includes any type of conduit made from metal, primarily designed to provide superior protection against physical damage and corrosion. These conduits are ideal for environments where high-impact protection is needed. They are commonly used in industrial settings or outdoor environments where heavy-duty protection is required.
강성 금속 도관(RMC): RMC is a heavy-duty, thick-walled conduit made of galvanized steel or aluminum. It is the most durable type of metallic conduit, providing robust protection against impact, moisture, and physical damage.
중간 금속 도관(IMC): IMC is similar to RMC but with a thinner wall, making it lighter and easier to handle while still providing robust protection. It is made of galvanized steel or aluminum.
전기 금속 튜브(EMT): EMT is a thinner-walled, lightweight metallic conduit made from galvanized steel. It is also known as “thin-wall conduit” and is easy to bend, making it a popular choice for electrical wiring installations in residential and commercial buildings.
유연 금속 도관(FMC): FMC is a flexible, spiral-wound metal conduit that allows for easy installation in areas requiring movement or frequent adjustments. It is typically made from steel and can be used to route wiring through tight spaces.
Liquid-tight Flexible Metal Conduit (LFMC): LFMC is a flexible conduit that combines the benefits of flexibility with additional protection from moisture and liquids. It consists of a metal tube with a non-metallic inner coating to make it watertight.
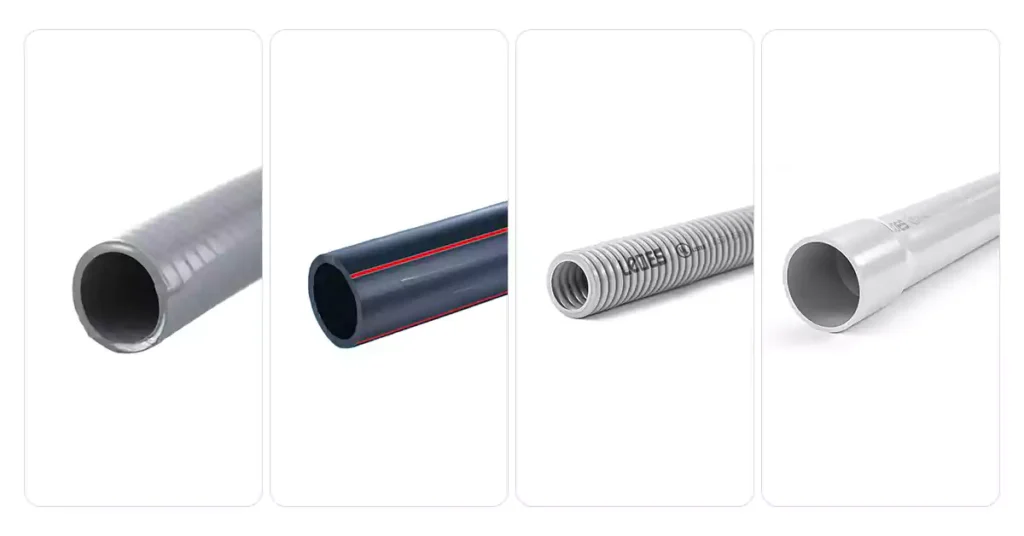
Non-metallic conduit, as the name suggests, is made from non-metallic materials, most commonly PVC. These conduits are more lightweight, easy to install, and highly resistant to corrosion, making them a popular choice for many residential and commercial installations.
Polyvinyl Chloride (PVC) Conduit: PVC electrical conduit is one of the most widely used types of non-metallic conduit. It is resistant to moisture, corrosion, and impacts, making it an excellent choice for both indoor and outdoor installations.
High-Density Polyethylene (HDPE) Conduit: HDPE conduit is made from a tough, flexible plastic that is ideal for use in underground installations. It is highly resistant to corrosion, abrasion, and chemicals.
Electrical Nonmetallic Tubing (ENT): ENT conduit is a flexible, non-metallic tubing commonly used in indoor environments, such as residential and commercial buildings, where flexibility and ease of installation are key considerations.
Liquid-tight Flexible Nonmetallic Conduit (LFNC): LFNC is a flexible, non-metallic conduit designed to protect wires from moisture, chemicals, and other environmental hazards. It consists of a spiral wound plastic core with an outer jacket for additional protection.
Summary Table: Metallic vs. Non-Metallic Conduit
Characteristic | Metallic Conduit | Non-metallic Conduit |
재료 | Steel, Aluminum | PVC, Polyethylene |
유형 | RMC, EMT, FMC, IMC, LFMC | PVC, ENT, HDPE, LFNC |
Weight | Heavier | Lighter |
Corrosion Resistance | Less resistant (unless galvanized) | Highly resistant |
Flexibility | Rigid, except FMC, LFMC | Flexible (except Rigid PVC) |
Durability | 높은 | 보통의 |
Grounding Capabilities | Provides grounding (except EMT) | May require additional grounding (PVC, ENT) |
Temperature Resistance | High (ideal for extreme conditions) | 보통의 |
Ease of Installation | More challenging (RMC, IMC are heavy, EMT requires specialized tools) | Easier to install, especially flexible types (ENT, LFNC) |
Cost | Higher (especially RMC, IMC, LFMC) | Lower (especially PVC, ENT) |
Use Case | Heavy-duty (industrial, commercial, outdoor) | Light to moderate duty (residential, commercial, underground) |
To better understand each type of conduits’ characteristics, pros and cons, here is the comparison table.
Pros and Cons of Conduit Types
Conduit Types | Advantages | Disadvantages |
RMC | High impact resistance, moisture-resistant, grounding | Heavy, difficult to install, expensive |
EMT | Lightweight, easy to install, cost-effective | Less impact protection, no grounding unless bonded |
FMC | Flexible, easy to install in tight spaces | Less protective, less durable |
IMC | Lighter than RMC, provides excellent protection | Less strong than RMC, lacks full grounding |
LFMC | Water-resistant, flexible, impact-resistant | More expensive, less impact protection than RMC/IMC |
PVC Rigid | More expensive, less impact protection than RMC/IMC | Less impact-resistant, temperature sensitive |
이비인후과 | Very flexible, easy to install, cost-effective | Less durable, less protective |
HDPE | Highly durable, resistant to chemicals, flexible | Expensive, requires specialized tools |
LFNC | Flexible, water-resistant, chemical-resistant | Less impact-resistant, more expensive than PVC |
In summary, both metallic and non-metallic conduits have their advantages and disadvantages, depending on the specific needs of your electrical installation. Metallic conduit offers superior durability, fire resistance, and grounding capabilities, making it ideal for high-risk or industrial environments. On the other hand, non-metallic conduit is more affordable, lightweight, and easier to install, making it perfect for residential or commercial applications where cost and ease of installation are primary considerations.
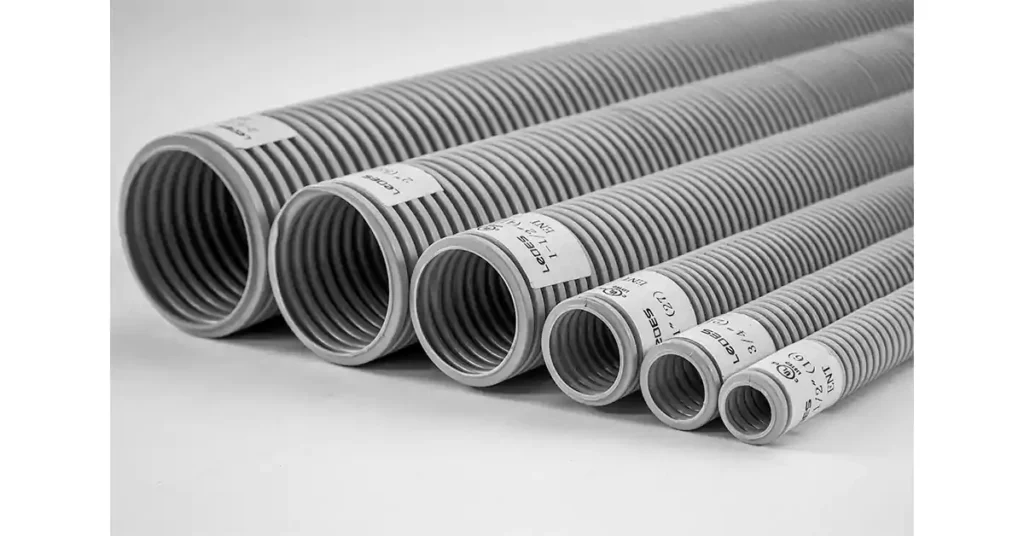
When selecting electrical conduit for wiring installations, understanding the similarities and differences between metallic and non-metallic types is crucial. These conduit materials vary in terms of construction, durability, flexibility, and their ideal use cases. While both offer protection for electrical conductors, they cater to different environmental conditions and application needs.
- Primary Function: Protection
Both metallic and non-metallic conduits serve the same primary purpose: to protect electrical wires and cables from physical damage, moisture, dust, chemicals, and other hazards. They help ensure the safe operation of electrical systems by providing an enclosed pathway for wiring.
- Compliance with Electrical Codes
Both types of conduits must comply with national and international standards to guarantee safety and performance. In the United States, for example, the National Electrical Code (NEC) sets the guidelines for their installation, specifying how each type should be used depending on the application and environment. Similarly, other countries have their own standards (e.g., IEC, AS/NZS) to regulate conduit usage. The IEC 61386 standard is global standard for electrical PVC conduit, and the AS/NZS 2053 standard for PVC conduit and works in Australia & New Zealand.
- Versatility in Use
Both metallic and non-metallic conduits are used in various applications, ranging from residential and commercial to industrial and outdoor installations. The choice between them often depends on factors like location, environmental conditions, and budget, rather than a fundamental difference in purpose.
- Standard Sizing
Regardless of the material, both types of conduit come in standard sizes, which ensures that they can be used interchangeably with wiring systems of various sizes. This consistency makes installation easier and more standardized across different projects.
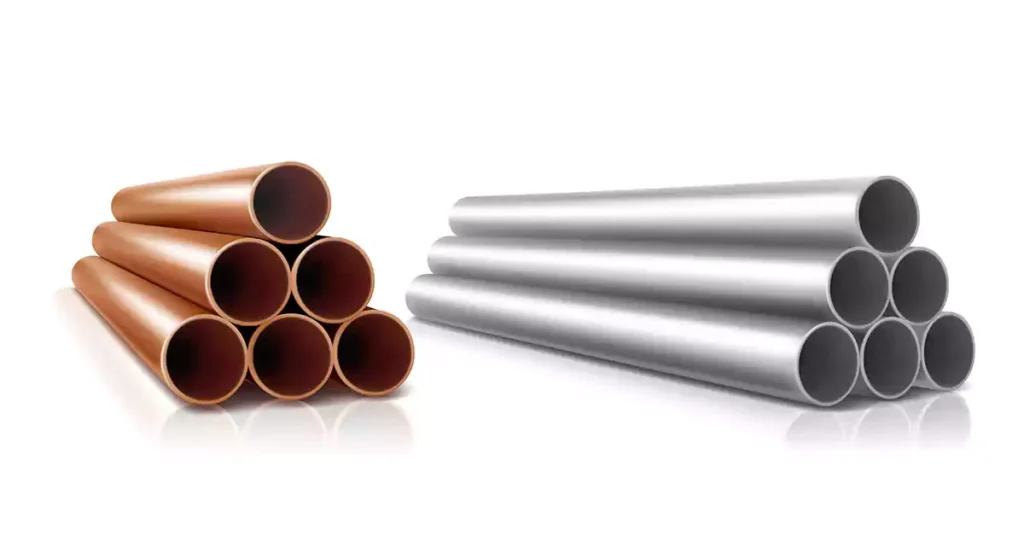
- Material Composition
The most obvious difference between metallic and non-metallic conduits lies in their material composition.
- Metallic conduits are typically made from materials like steel, aluminum, and copper-coated steel. Examples include Rigid Metal Conduit (RMC), Electrical Metallic Tubing (EMT), and Intermediate Metal Conduit (IMC).
- Non-metallic conduits, on the other hand, are made from plastic materials such as PVC (Polyvinyl Chloride), HDPE (High-Density Polyethylene), and Flexible Non-Metallic Conduit (LFNC).
- Flexibility and Installation Ease
- Metallic conduits are available in both rigid forms (e.g., RMC and IMC) and flexible forms (e.g., Flexible Metal Conduit – FMC and Liquid-tight Flexible Metal Conduit – LFMC). While the rigid types offer excellent protection, they can be more challenging to install, requiring specialized tools for cutting, bending, and connecting. The flexible metallic options, however, offer some flexibility but are still heavier and more difficult to work with than their non-metallic counterparts.
- Non-metallic conduits, such as PVC, ENT (Electrical Nonmetallic Tubing), and HDPE, tend to be lighter and easier to handle, making installation quicker and more straightforward. Many non-metallic conduits, like ENT and LFNC, are flexible, offering easy installation in areas that require frequent bending or movement. These are often preferred in residential and commercial environments due to their ease of use.
- Corrosion and Impact Resistance
- Metallic conduits generally offer high resistance to physical damage and can withstand significant impact. However, they can be prone to corrosion unless galvanized or coated. RMC and IMC are often used in outdoor or industrial settings where the conduit may be exposed to moisture, chemicals, or extreme conditions.
- Non-metallic conduits are naturally resistant to corrosion, making them ideal for environments where moisture or chemicals are a concern. PVC and HDPE are corrosion-resistant and do not need special coatings like metallic conduits. However, non-metallic conduits like PVC tend to be more susceptible to impact damage, especially when compared to rigid metallic options.
- Grounding Capabilities
- Metallic conduits, particularly RMC and IMC, provide natural grounding for electrical systems due to their conductive properties. EMT requires grounding through bonding, making the installation a bit more complex.
- Non-metallic conduits do not conduct electricity and therefore cannot provide grounding by themselves. If grounding is necessary, additional grounding conductors or bonding conductors must be installed within the conduit.
- Cost Considerations
- Metallic conduits are typically more expensive, particularly in the case of RMC, IMC, and LFMC. The higher material cost is also compounded by the need for specialized tools to install rigid metallic conduit.
- Non-metallic conduits, especially PVC, are generally much more affordable. They are cost-effective for large-scale installations, particularly in residential and light commercial projects.
- Temperature Resistance
- Metallic conduits are generally more temperature-resistant and can handle extreme heat and cold better than non-metallic types. This makes them ideal for applications in areas that experience high heat or sub-zero temperatures.
- Non-metallic conduits such as PVC and ENT have a more limited temperature range and may degrade under high heat or cold, though HDPE performs better in colder climates.
- Fire Resistance
- Metallic conduits inherently have better fire-resistance due to the nature of the materials used (steel, aluminum), offering additional protection against fire hazards.
- Non-metallic conduits, particularly PVC, have a flammability rating. While PVC is flame retardant, it can still catch fire under extreme conditions and may release toxic fumes if ignited.
- Moisture Resistance
- Metallic conduits like LFMC and RMC are effective at sealing out moisture, making them suitable for wet or humid environments, although some metallic types need additional treatments or coatings to enhance water resistance.
- Non-metallic conduits such as PVC and HDPE provide excellent moisture resistance and are commonly used in underground and outdoor applications. LFNC is another non-metallic option that offers good moisture protection.
When selecting the appropriate type of conduit for an electrical installation, it’s essential to consider the specific application requirements, including environmental factors, safety standards, and project budget. Different conduits—whether metallic or non-metallic—have distinct advantages that make them more suitable for particular use cases.
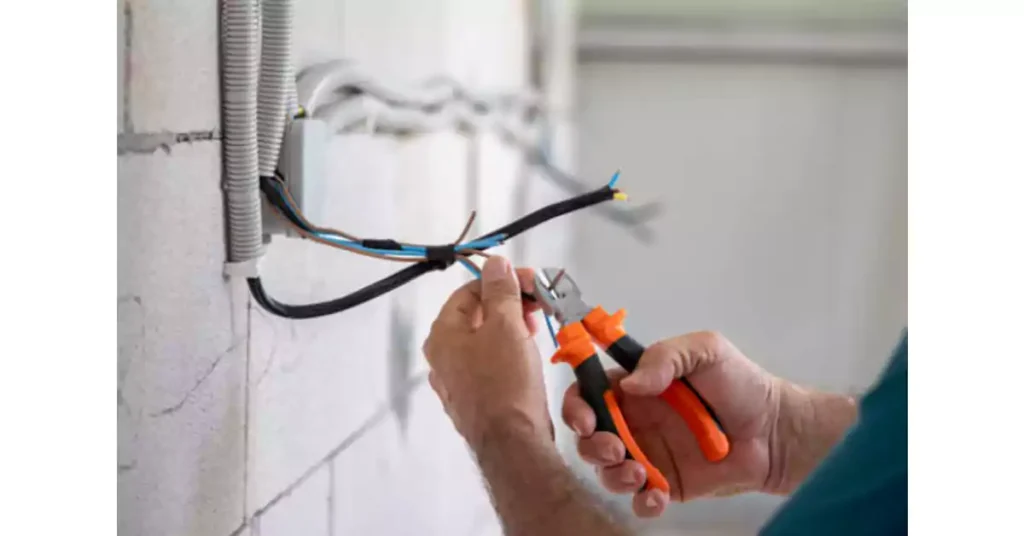
In residential and commercial electrical installations, non-metallic conduits like PVC and ENT are widely used. These materials are favored for their affordability, ease of installation, and excellent corrosion resistance, especially in environments where moisture or exposure to chemicals might be a concern. PVC conduit is often used for underground wiring, offering both protection and cost-effectiveness. ENT (Electrical Nonmetallic Tubing), which is flexible and easy to install, is commonly used for interior wiring in walls and ceilings, where quick and efficient installations are important.
On the other hand, metallic conduits like EMT (Electrical Metallic Tubing) and RMC (Rigid Metal Conduit) are preferred for installations that demand higher durability and mechanical protection. EMT is often used for indoor applications where the conduit needs to be more robust and resistant to physical damage, while RMC provides superior protection in outdoor settings or where extra protection from the environment is necessary.
In industrial environments, where systems face more demanding conditions such as exposure to chemicals, extreme temperatures, and physical impacts, metallic conduits are typically the go-to choice. RMC, IMC (Intermediate Metal Conduit), and LFMC (Liquid-tight Flexible Metal Conduit) offer excellent mechanical strength, corrosion resistance, and the ability to endure heavy-duty environments. For instance, LFMC is commonly used for installations exposed to water or moisture, such as in factories, manufacturing plants, or outdoor installations where flexibility is required, but protection from the elements is paramount.
Non-metallic conduits like HDPE (High-Density Polyethylene) and PVC are also used extensively in industrial settings, particularly for underground installations or buried cables. HDPE is especially beneficial for its resistance to corrosion, chemical resistance, and long-term durability, making it ideal for protecting wiring in environments where conditions are harsh, such as in telecommunications or utilities.
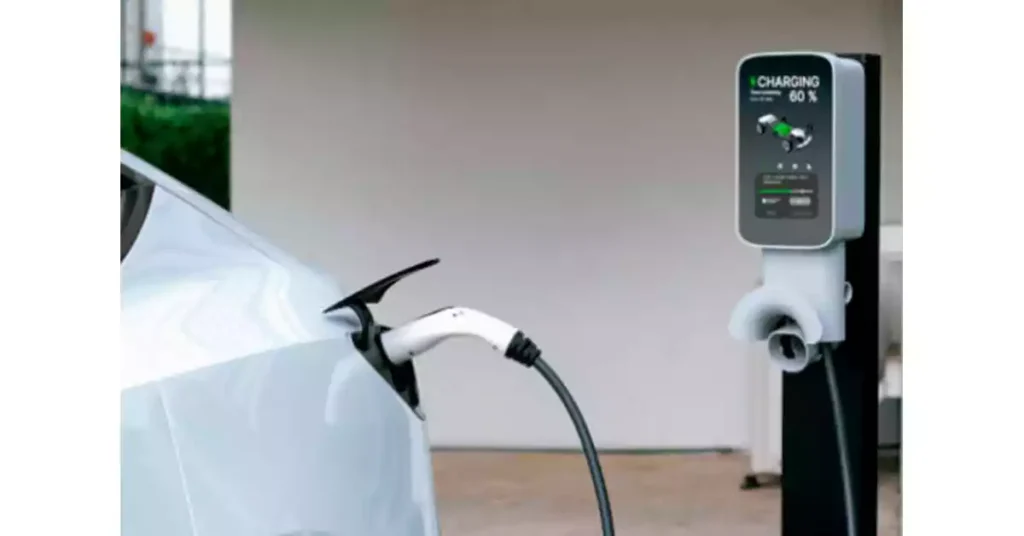
The rapid growth of electric vehicle (EV) charging infrastructure has created new demands for safe, reliable, and durable wiring systems. Both metallic and non-metallic conduits play crucial roles in protecting the wiring systems in EV charging stations.
팁: In our last post, we shared insights into the applications of electrical conduits in EV Charging Stations. If you are interested, you can check out this article.
- Metallic conduits like EMT and RMC are used for indoor and outdoor installations where wiring needs to be protected from physical damage. EMT is ideal for commercial and residential charging stations, providing an efficient, low-cost option for protecting the electrical wiring. In areas exposed to harsh weather or physical impact, RMC is the go-to choice for heavy-duty protection.
- Non-metallic conduits like PVC and LFNC (Liquid-tight Flexible Non-Metallic Conduit) are often used for underground wiring and connections exposed to the elements. PVC is ideal for underground installations, while LFNC is particularly useful for wet environments, offering both flexibility and moisture resistance.
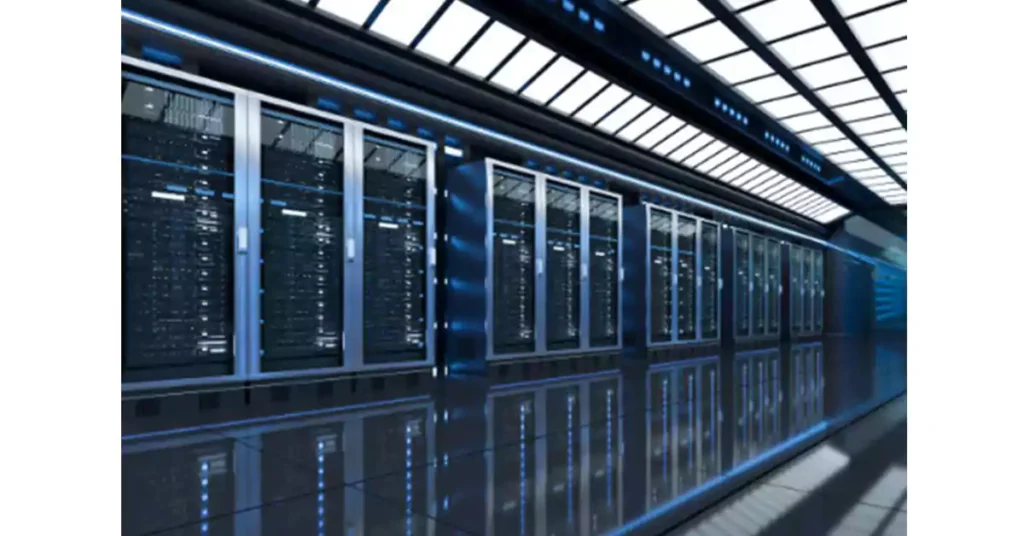
Data centers require specialized electrical conduit systems to ensure that high-performance wiring for power and data transmission remains safe, secure, and organized. The sensitive nature of data processing means these systems need to be shielded from interference, physical damage, and fire hazards.
- Metallic conduits like EMT, IMC, and RMC are used to safeguard electrical cables in data centers. EMT and IMC are favored for their ability to protect against electromagnetic interference (EMI), a crucial requirement for data centers housing sensitive equipment. RMC is often used for external or heavy-duty applications where extra protection is required.
- Non-metallic conduits, such as PVC and HDPE, are also used in data centers, especially for underground installations or in subfloor spaces where flexibility and ease of installation are key considerations. PVC conduits are often used for power distribution, while HDPE is suitable for long-lasting, corrosion-resistant protection in outdoor or subterranean installations.
The rise of solar energy systems has added another dimension to the conduit industry. The need to protect solar panel wiring, which is often located in outdoor environments and subject to harsh weather, makes conduit a critical component of the system. For more details, read this post to learn everything about solar conduit.
- Metallic conduits like RMC and IMC are commonly used in solar power installations, particularly for connecting solar arrays to inverters and power distribution systems. These conduits offer excellent protection against mechanical damage, UV radiation, and extreme weather conditions. LFMC is also used in solar systems where flexibility is needed for connections between solar panels and the main power system.
- Non-metallic conduits like PVC and LSZH (Low Smoke Zero Halogen) are used in residential solar installations due to their ease of installation, affordability, and resistance to UV exposure. PVC provides corrosion resistance and is suitable for underground wiring or areas where ease of installation and cost-effectiveness are important. LSZH conduits, which release minimal smoke and toxic gases during a fire, are preferred in applications where fire safety is a concern, such as residential or commercial solar systems.
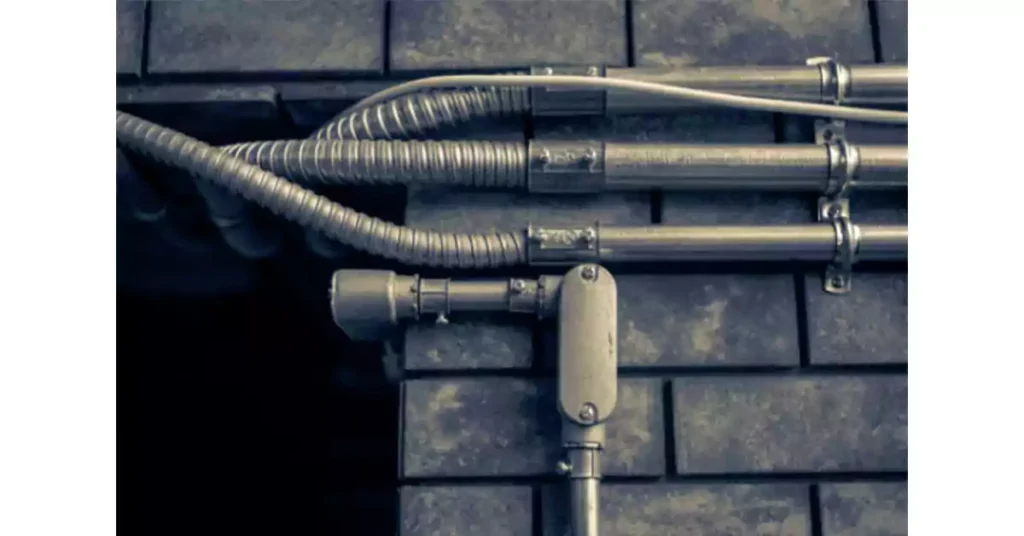
Selecting the right electrical conduit for a given application involves balancing a range of factors, each of which influences the safety, efficiency, and cost-effectiveness of the installation. Both metallic and non-metallic conduits have distinct characteristics that make them more or less suitable for different environments, project sizes, and electrical requirements. Here, we will explore the key factors to consider when choosing the best conduit for your electrical project.
The location and environment of your installation will play a significant role in determining the best type of conduit to use. Factors such as whether the system is located indoors or outdoors, exposure to corrosive materials, or potential fire hazards all influence conduit selection.
Indoor vs. Outdoor Installations: For indoor applications, non-metallic conduits like PVC and ENT are often preferred due to their ease of installation, cost-effectiveness, and resistance to corrosion. However, for outdoor applications, particularly those exposed to severe weather, metallic conduits like RMC or IMC provide superior protection from physical damage, moisture, and temperature fluctuations.
Corrosive Materials: In environments exposed to chemicals, metallic conduits (such as RMC) offer excellent durability and can withstand corrosive substances, making them suitable for industrial settings like chemical plants or manufacturing facilities. For non-corrosive environments, PVC conduits are sufficient and cost-effective for residential and commercial projects.
Fire Hazards: In areas with potential fire risks, such as data centers, industrial plants, and solar installations, metallic conduits may offer better protection due to their ability to contain fires and prevent electrical sparks from igniting nearby materials. Non-metallic conduits like PVC and LSZH (Low Smoke Zero Halogen) conduits are also useful in settings where fire safety is a priority, as they produce minimal smoke and toxic gases in the event of a fire.
The electrical current and voltage requirements of your system are key considerations when choosing conduit. Conduit selection needs to account for both the capacity of the electrical system and the type of wiring used. For higher voltage applications, metallic conduits such as RMC, IMC, and EMT provide enhanced protection due to their ability to handle increased electrical loads and prevent interference.
High Voltage and Heavy Duty Loads: For high-voltage applications or heavy-duty industrial settings, metallic conduits are often the preferred option. They can withstand larger current capacities and provide superior shielding from electromagnetic interference (EMI), which is crucial for maintaining the integrity of sensitive electrical systems.
Low Voltage and Light Duty: For residential or light commercial applications, non-metallic conduits like PVC are often sufficient to handle the current requirements of typical wiring systems. They are lighter, easier to install, and are more cost-effective for smaller-scale projects.
The scale and complexity of your electrical project will influence the conduit choice. For simple, small-scale installations, non-metallic conduits like PVC or ENT may be all that is needed, as they are easier to work with and more affordable.
Simple Residential Projects: For homes or small office spaces, PVC and ENT conduits are commonly used due to their flexibility, ease of installation, and cost-effectiveness. These conduits are ideal for running wiring through walls or ceilings without requiring additional protection against physical damage.
Large, Complex Installations: For larger, more complex installations, such as industrial plants, data centers, or solar farms, metallic conduits like RMC, IMC, and LFMC are better equipped to handle the physical demands of the project. These conduits offer stronger protection against environmental factors, are suitable for heavy-duty electrical systems, and are better able to manage the large-scale wiring required.
Specialized Applications: In certain industries, like electric vehicle charging stations or telecommunications, the need for flexibility and complex wiring setups means that both metallic and non-metallic conduits will need to be considered. For example, flexible metal conduit (FMC) or liquid-tight flexible non-metallic conduit (LFNC) may be required for systems that demand both flexibility and protection.
Cost considerations are often one of the deciding factors when choosing conduit. While metallic conduits are generally more expensive due to the material cost and added labor for installation, they offer significant advantages in terms of durability and long-term performance.
Lower Budget Projects: For residential or small commercial projects where cost is a primary concern, non-metallic conduits like PVC or ENT are often the preferred choice. These materials are less expensive, easy to install, and suitable for standard electrical systems where the demands are lower.
Long-Term Investment: For larger, more complex, or higher-risk installations where long-term durability is critical, investing in metallic conduits may be worthwhile. While the initial cost may be higher, these conduits provide superior protection and are more likely to withstand wear and tear over time, reducing the need for future replacements or repairs.
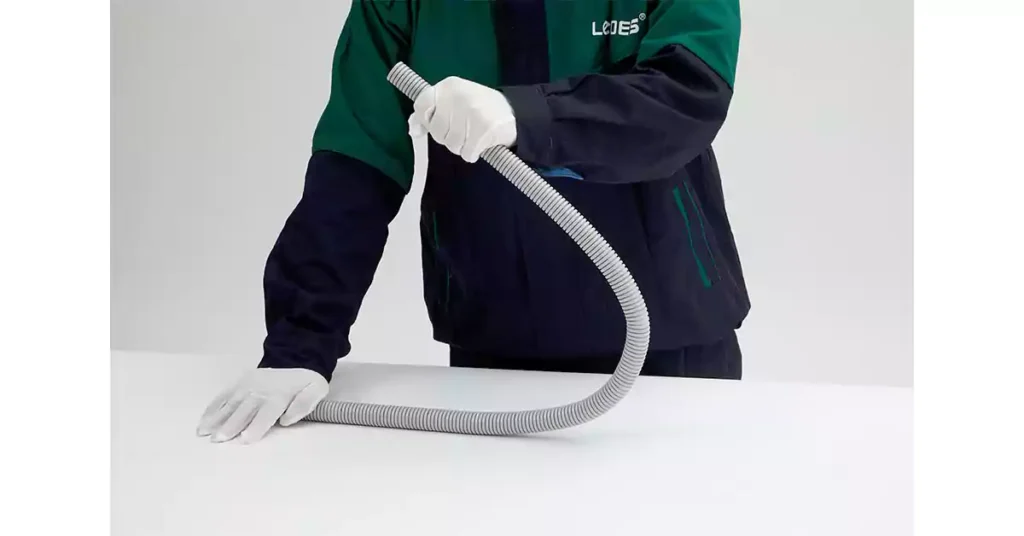
Another key factor in conduit selection is the level of flexibility required for the installation. For areas that require tight bends or the ability to easily navigate obstacles, flexible conduits like FMC (Flexible Metal Conduit) or LFNC (Liquid-tight Flexible Non-Metallic Conduit) are ideal. These conduits offer both ease of installation and protection in areas where rigid conduit is impractical.
Flexible Installations: FMC is commonly used in areas where wiring needs to be routed around corners or installed in tight spaces. LFNC offers flexibility for outdoor installations where moisture or water exposure is a concern.
Ensuring that the chosen conduit meets local electrical codes and safety standards is essential. Different types of conduit are required for specific environments and applications, with codes such as the NEC (National Electrical Code) or UL (Underwriters Laboratories) setting the requirements for electrical installations.
National Standards Compliance: Always verify that the selected conduit is compliant with the relevant standards and certifications for your area or type of project. This can include checking the conduit’s fire resistance, electrical rating, and environmental suitability.
Selecting a reliable electrical conduit supplier is just as important as choosing the right type of conduit for your project. A good conduit pipe supplier ensures that the materials you purchase meet industry standards, offer reliable performance, and are delivered on time.
A supplier’s reputation in the industry is a crucial factor when making your decision. Established suppliers with years of experience are more likely to offer high-quality products and reliable service. Look for suppliers who have been in the business long enough to understand the nuances of the electrical conduit market and have a track record of successfully delivering products to customers in various industries, from residential to industrial and emerging markets like electric vehicle (EV) charging stations and data centers.
Years of Operation: Suppliers with a long-standing presence in the industry are generally more trusted and have had time to perfect their processes, products, and customer service.
Customer Testimonials: Seek out feedback from other customers in the same field or industry. Reviews, testimonials, or case studies can provide insights into the supplier’s performance and reliability.
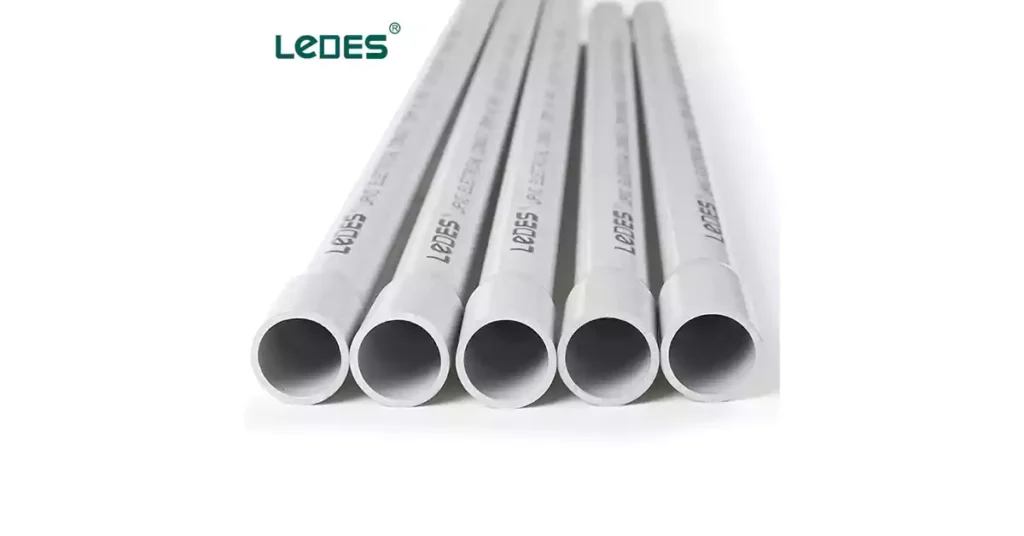
The quality of the electrical conduit you purchase directly affects the safety and performance of your installation. It’s essential to choose a supplier that offers products meeting the necessary quality standards and certifications.
Industry Certifications: Look for suppliers that provide UL (Underwriters Laboratories) approved products or those that meet the required standards set by organizations like NEC (National Electrical Code), IEC (International Electrotechnical Commission), and CE (Conformité Européenne). Products that have these certifications ensure they meet safety, performance, and reliability standards.
Material Sourcing: Ask suppliers about the sourcing and quality control of their materials. The best suppliers will work with top-tier manufacturers and regularly conduct quality assurance tests to ensure their products are up to standard.
A reliable supplier should offer a comprehensive range of products to suit various electrical applications. Whether you’re looking for rigid PVC conduit, flexible metal conduit, or non-metallic tubing, having a supplier with a diverse catalog can make it easier to source all your materials in one place.
Wide Product Selection: A supplier with a broad range of products will be able to meet your needs regardless of the project’s scale or complexity. They should offer various conduit types (e.g., PVC, RMC, EMT, LFMC, HDPE) and related accessories such as elbows, couplings, and adapters.
Stock Availability: Check if the supplier can deliver products quickly. Some projects might require fast delivery due to tight schedules, so it’s important to confirm that the supplier has sufficient stock or can get the products to you on time.
In some cases, you may need customized conduit solutions to meet specific installation requirements. For example, specialized bends, fittings, or longer lengths of conduit might be needed for a complex installation in data centers, solar power systems, or EV charging stations.
Tailored Solutions: Look for suppliers that offer customization services, especially if your project requires non-standard conduit or accessories.
Technical Expertise: The best suppliers will have in-house technical support to assist with creating tailored solutions and helping with any unique needs your installation might have.
Good customer service can make or break the supplier relationship. A supplier who is easy to communicate with, responsive to inquiries, and proactive in addressing issues will be a key asset to your project’s success.
Clear Communication: Ensure that the supplier has a dedicated support team that is responsive and willing to help with any questions or concerns. They should be easy to reach via phone, email, or live chat.
After-Sales Support: A reliable supplier should offer after-sales support in case issues arise with the product. Whether it’s handling returns, warranty claims, or providing guidance on installation, good post-purchase service is essential.
Pricing plays a key role when selecting a supplier, but it should never be the sole determining factor. Choosing the lowest-priced option can lead to subpar products or delayed deliveries, ultimately increasing the total cost of the project.
Competitive Pricing: Compare the prices of several suppliers to ensure you’re getting fair rates for the quality and quantity of product you need.
Payment Terms: Understand the payment terms and conditions upfront. Some suppliers may offer bulk discounts, credit terms, or payment options that could help with budgeting.
In this article, we’ve explored the key differences between metallic and non-metallic conduits, highlighting their respective strengths and weaknesses. Metallic conduits such as RMC, EMT, and IMC offer superior protection against physical damage, corrosion, and environmental hazards, making them ideal for heavy-duty, outdoor, or industrial applications. On the other hand, non-metallic conduits like PVC, ENT, and HDPE provide cost-effective, easy-to-install solutions that are well-suited for residential, light commercial, and certain outdoor applications. They are generally lighter, more flexible, and resistant to corrosion, but may not provide the same level of mechanical strength or fire resistance as metallic conduits.
The best conduit choice ultimately depends on the specific needs of your project, including factors like the environment, electrical requirements, budget, and the complexity of the installation. Whether you choose metallic or non-metallic conduit, it is essential to weigh these factors carefully and select the one that ensures both safety and efficiency.
For professional advice, it is always a good idea to consult with a qualified electrician who can assess your specific requirements and help you make the best decision for your project. Their expertise will help ensure that you comply with relevant electrical codes and that your installation is both safe and reliable.
We’d love to hear your thoughts! Which conduit do you think is better for your application: metallic or non-metallic? Share your opinions and experiences with us in the comments below!