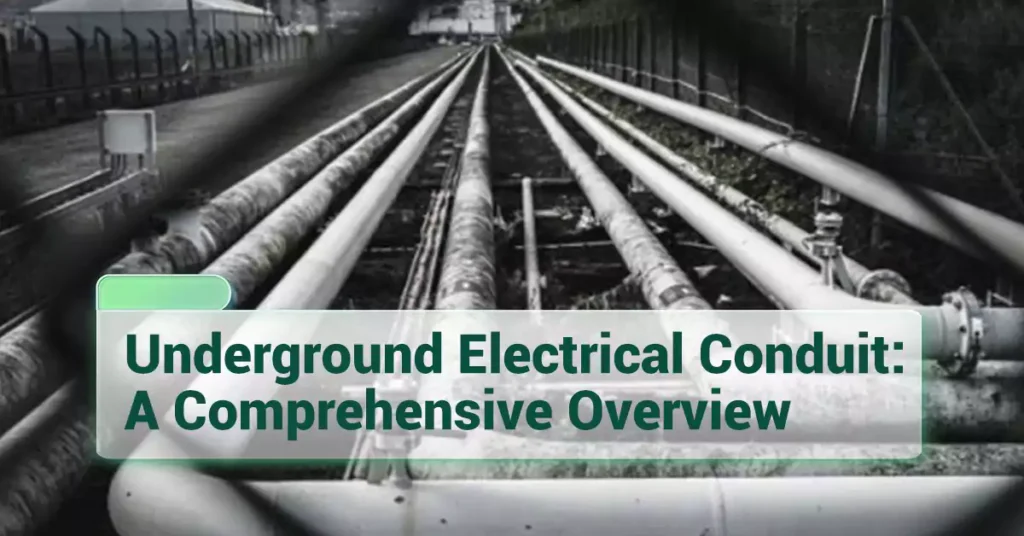
목차
Underground electrical conduit is a vital component of modern electrical systems, providing a safe and efficient means of routing and protecting electrical wiring below the ground surface. It serves as a conduit, both literally and figuratively, for the seamless transmission of power and data in various applications. In this article, we delve into the comprehensive exploration of underground electrical conduit, shedding light on its definition, purpose, and significance.
What is Underground Electrical Conduit?
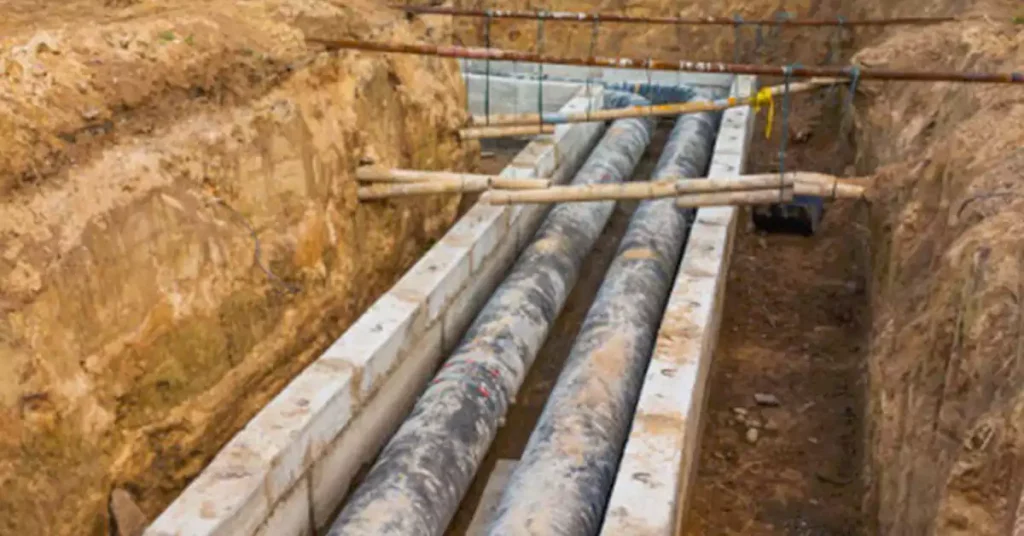
Underground electrical conduit refers to a system of pipes, tubes, or channels specifically designed to house and safeguard electrical wiring and cables beneath the ground. It acts as a protective conduit to shield the wiring from physical damage, moisture, and environmental factors.
The primary purpose of underground electrical conduit is twofold. Firstly, it ensures the safety of electrical installations by preventing accidental contact with live wires and reducing the risk of electrical hazards. By securely enclosing the wiring, conduit minimizes the chances of electrical shocks, short circuits, and fires, making it an essential safety measure.
Secondly, underground conduit facilitates efficient and organized routing of electrical cables, enabling the seamless transmission of power and data. It allows for the concealment and consolidation of multiple cables, simplifying maintenance and troubleshooting processes. Moreover, conduit systems provide flexibility for future modifications or upgrades to the electrical system, ensuring adaptability and scalability.
Why Underground Electrical Conduit Important?
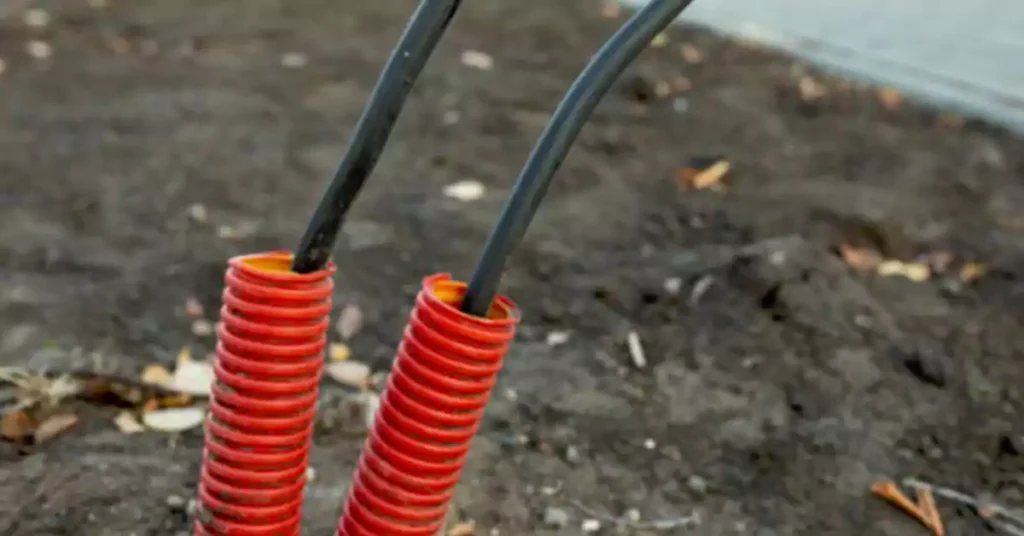
The importance of underground electrical conduit cannot be overstated, particularly in modern infrastructure and construction projects. Here are some key reasons highlighting its significance:
Protection of Electrical Wiring: Underground conduit safeguards electrical wiring from physical damage caused by external forces such as construction activities, vehicle traffic, or natural elements. It acts as a sturdy barrier, shielding the cables from impact, abrasion, and other potential hazards.
Prevention of Moisture and Environmental Damage: Underground conduit offers excellent resistance to moisture, humidity, corrosive substances, and other environmental factors. It prevents water infiltration, which can lead to electrical malfunctions and deterioration of cables, ensuring the reliability and longevity of the electrical system.
인력 및 장비의 향상된 안전: By isolating electrical wiring within conduit, the risk of accidental contact is significantly reduced, protecting both individuals and equipment. Conduit systems are designed to meet stringent safety standards, providing an additional layer of protection against electrical hazards.
Versatility in Various Underground Applications: Underground electrical conduit finds extensive use in diverse applications, including residential, commercial, industrial, and municipal projects. It can be installed in underground utility networks, building foundations, parking lots, roadways, and other infrastructure developments, catering to a wide range of electrical needs.
Compliance with Electrical Codes and Regulations: Underground conduit installations must adhere to specific electrical codes and regulations, such as those outlined by the National Electrical Code (NEC). Compliance ensures that the electrical system meets the required safety standards and mitigates potential liabilities.
5 Types of Underground Electrical Conduit
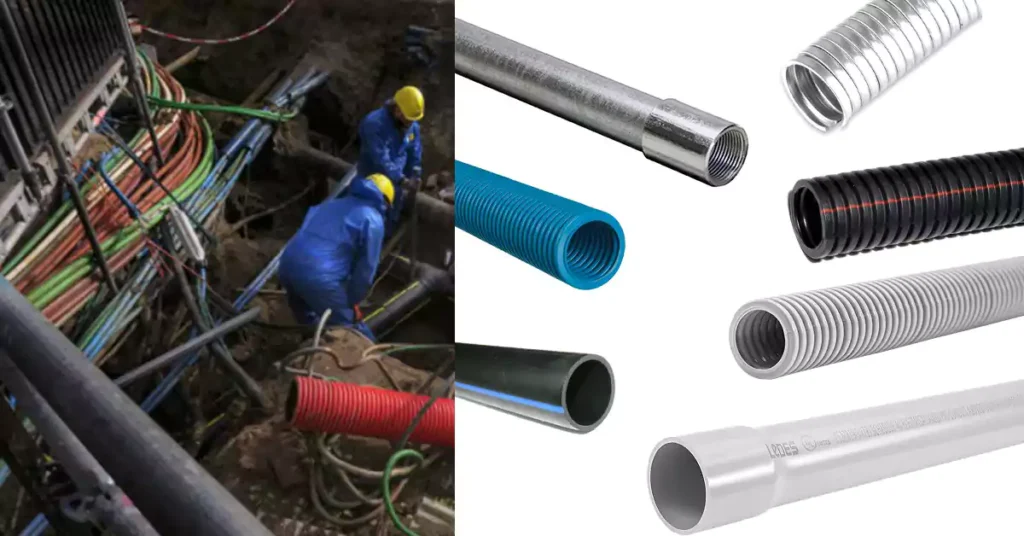
A wide range of conduit options are available for underground electrical installations, each with its own characteristics and suitability for different applications. Understanding the various types of underground electrical conduit is crucial in selecting the most appropriate option based on factors such as durability, flexibility, cost-effectiveness, and compatibility with specific wiring systems. Here are some common types of underground electrical conduit:
강성 금속 도관(RMC):
Rigid Metal Conduit (RMC), also known as galvanized steel conduit, is one of the most robust options for underground installations. It is made of steel and has a thick wall, providing excellent protection against physical damage and impact. RMC is highly resistant to fire, sunlight, and corrosion, making it suitable for harsh environments and areas prone to mechanical stress. However, due to its rigidity, RMC requires careful planning and precise bending when navigating corners or bends.
전기 금속 튜브(EMT):
Electrical Metallic Tubing (EMT) is a lightweight conduit option, typically made of galvanized steel or aluminum. It offers good protection for electrical wiring while being more flexible than RMC. EMT is easy to install and can be bent to navigate corners and bends without the need for specialized tools or equipment. It is commonly used in residential and commercial applications where flexibility and ease of installation are essential.
Fiberglass Conduit:
Fiberglass conduit, also known as reinforced plastic conduit (RTRC), is a non-metallic option that provides excellent resistance to corrosion, moisture, and chemical exposure. It is lightweight, making it easier to handle and install compared to metal conduits. Fiberglass conduit is an ideal choice for underground installations in corrosive environments, such as wastewater treatment plants or chemical processing facilities. It is also non-conductive, offering additional safety benefits in certain applications.
High-Density Polyethylene (HDPE) Conduit:
High-Density Polyethylene (HDPE) conduit is a durable and flexible option for underground electrical installations. It is made of high-density polyethylene, a thermoplastic material known for its resistance to impact, chemicals, and environmental factors. HDPE conduit is lightweight and can be easily bent or coiled, allowing for efficient installation in various settings. It is commonly used in telecommunications, fiber optic, and power distribution applications.
Polyvinyl chloride (PVC) conduit is a popular choice for both above-ground and underground electrical installations. It is cost-effective, lightweight, and offers good resistance to moisture, chemicals, and corrosion. PVC 도관 is available in various sizes and can be easily cut, joined, and installed using PVC-specific fittings. It is commonly used in residential, commercial, and industrial applications where cost-efficiency and ease of installation are important considerations.
Underground Electrical Conduit Codes and Requirements
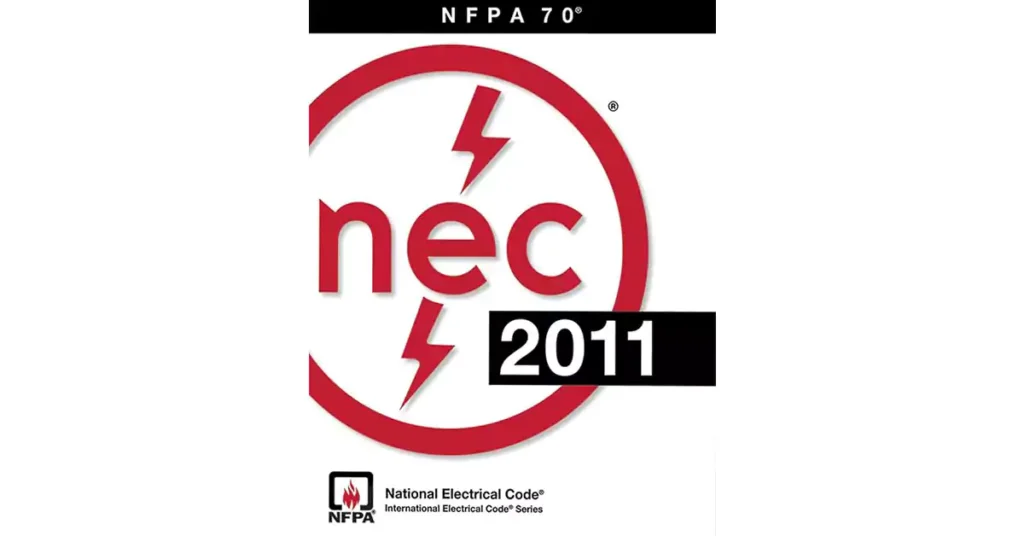
When it comes to underground electrical conduit installations, adherence to specific codes and requirements is crucial to ensure safety, reliability, and compliance with industry standards. There are various codes and requirements that govern underground electrical conduit systems:
UL2420 BG:
The UL2420 BG certification, issued by Underwriters Laboratories (UL), is a widely recognized standard for safety and performance of nonmetallic underground conduit systems. This certification ensures that the conduit meets rigorous testing criteria, including resistance to impact, UV exposure, and environmental stress. UL2420 BG certified conduit provides assurance that it can withstand the demands of underground installations, offering enhanced durability and protection for electrical wiring.
UL94HB Flame Rating:
The UL94HB flame rating is a critical factor to consider when selecting underground electrical conduit. It measures a material’s resistance to ignition and flame spread. Conduit materials with a higher flame rating provide better fire resistance, reducing the risk of fire propagation in the event of a fault or electrical overload. It is essential to choose conduit materials with appropriate flame ratings to comply with fire safety regulations and minimize potential hazards.
국가 전기 규정(NEC):
그만큼 National Electrical Code (NEC) is a set of regulations and standards established by the National Fire Protection Association (NFPA) to ensure electrical safety in the United States. The NEC provides guidelines for the installation, maintenance, and use of electrical systems, including underground conduit installations. It covers various aspects, including conduit sizing, grounding, bonding, burial depth, and wiring methods. Compliance with NEC requirements is crucial to meet safety standards and legal obligations.
Some key NEC requirements related to underground electrical conduit installations are:
도관 크기: The NEC specifies the minimum conduit size based on the number and size of conductors. It ensures adequate space for wire pulling, heat dissipation, and future upgrades.
Bury Depth: The NEC provides guidelines for the minimum burial depth of underground conduit to protect it from damage and ensure compliance with local regulations. Factors such as soil type, location, and environmental conditions may influence the specific bury depth requirements.
접지 및 본딩: Proper grounding and bonding of conduit systems are vital for electrical safety. The NEC outlines specific requirements for grounding conductors, bonding jumpers, and equipment grounding.
배선 방법: The NEC provides guidelines for the selection and installation of wiring methods within conduit systems, ensuring proper insulation, protection, and separation of different types of conductors.
Other Relevant Codes and Standards:
In addition to the NEC, other codes and standards may be applicable depending on the specific application, location, and jurisdiction. These may include local building codes, state regulations, and industry-specific standards. It is essential to consult with local authorities and electrical professionals to ensure compliance with all relevant codes and standards.
Bury Depth Requirements for Underground Electrical Conduit
Proper bury depth is crucial for underground electrical conduit installations, as it ensures the protection and longevity of the conduit system while complying with safety regulations. In this section, we will explore the factors influencing bury depth, the minimum bury depth guidelines according to the National Electrical Code (NEC), and adjustments for specific conditions.
5 Factors Influencing Bury Depth:
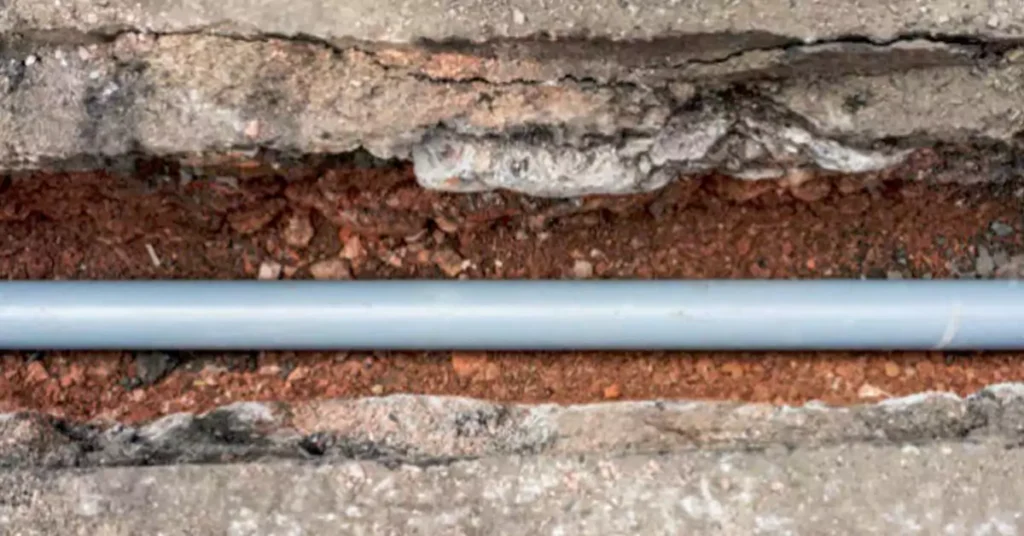
Several factors influence the appropriate bury depth for underground electrical conduit. These factors include:
1. Environmental Conditions:
Soil type, moisture content, and corrosive substances in the soil can affect conduit integrity. Soil with high moisture content or corrosive properties may require deeper bury depths for added protection.
2. Traffic and Load Considerations:
If the conduit is located in an area with vehicular or heavy equipment traffic, the bury depth should be increased to withstand potential mechanical stress and prevent damage.
3. Depth of Cover:
The depth of cover refers to the distance between the top of the conduit and the ground surface. It should provide sufficient protection against accidental contact, excavation activities, and potential damage from landscaping or construction work.
4. Wiring Types:
The type of wiring being installed within the conduit can impact the bury depth requirements. Different wiring types have varying degrees of insulation and resistance to moisture. For example, low-voltage wiring, such as telecommunications or data cables, may have specific bury depth requirements to ensure proper signal transmission and protection against interference. It’s important to consult the manufacturer’s specifications and relevant codes to determine the appropriate bury depth for specific wiring types.
5. Conduit Types:
Different conduit types like PVC conduit and Metal conduit could have different burial depth requirements. Normally, PVC conduit must be buried at least 18 inches deep, while galvanized metal electrical conduits must be buried at least 6 inches deep.
NEC Guidelines for Minimum Burial Depth
Article 300 of NEC states the general requirements for underground installations. And Table 300.5 has clearly listed the required minimum bury depth for different installation situations. Here are requirements for general installations.
Table 300.5(A) Minimum Cover Requirements, 0 to 1000 Volts ac, 1500 Volts dc, Nominal, Burial in Millimeters (Inches) | ||||||||||
Location of Wiring Method or Circuit | Type of Wiring Method or Circuit | |||||||||
Column 1 Direct Burial Cables or Conductors | Column 2 Rigid Metal Conduit or Intermediate Metal Conduit | Column 3 Electrical Metallic Tubing, Nonmetallic Raceways Listed for Direct Burial Without Concrete Encasement, or Other Approved Raceways | Column 4 Residential Branch Circuits Rated 120 Volts or Less with GFCI Protection and Maximum Overcurrent Protection of 20 Amperes | Column 5 Circuits for Control of Irrigation and Landscape Lighting Limited to Not More Than 30 Volts and Installed with Type UF or in Other Identified Cable or Raceway | ||||||
mm | in. | mm | in. | mm | in. | mm | in. | mm | in. | |
All locations not specified below | 600 | 24 | 150 | 6 | 450 | 18 | 300 | 12 | 1501,2 | 61,2 |
Besides the above locations, there are still locations like:
- In trench below 50 mm (2 in.) thick concrete or equivalent;
- Under a building;
- Under minimum of 102 mm (4 in.) thick concrete exterior slab with no vehicular traffic and the slab extending not less than 152 mm (6 in.) beyond the underground installation;
- Under streets, highways, roads, alleys, driveways, and parking lots;
- One- and two-family dwelling driveways and outdoor parking areas, and used only for dwelling-related purposes;
- In or under airport runways, including adjacent areas where trespassing is prohibited.
Each specific installation location and type of wiring method has different bury depth requirements, ranges from 4 inches to 24 inches deep, information can be found in NEC.
Adjustments for Specific Conditions
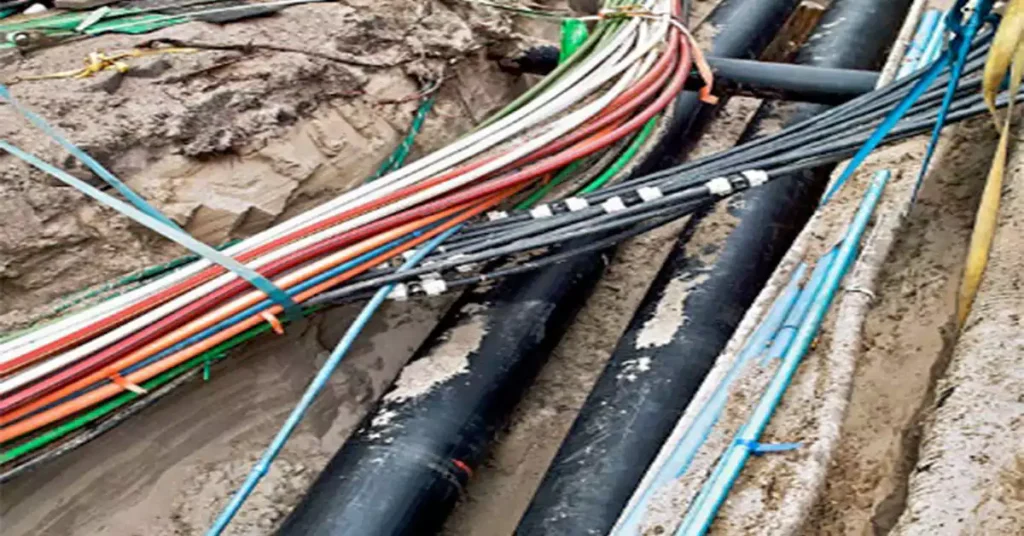
Specific conditions, such as frost lines and local regulations, may necessitate adjustments to the bury depth requirements. Here are some common adjustments:
Frost Lines: In regions experiencing freezing temperatures, bury depth requirements should account for the frost line. The conduit should be installed below the frost line to prevent freezing soil from damaging the conduit or causing ground shifting or heaving.
지역 규정: NEC (National Electrical Code) is just widely used and followed in American region, different countries and regions could have different codes and regulations to follow. Local building codes and regulations may dictate specific bury depth requirements based on regional factors, construction standards, or safety considerations. It is crucial to consult with local authorities and adhere to these regulations.
Considering these factors when determining bury depth requirements for underground electrical conduit installations is essential to ensure the protection, longevity, and compliance of the conduit system.
How to Install Underground Electrical Conduit? (6 Steps)
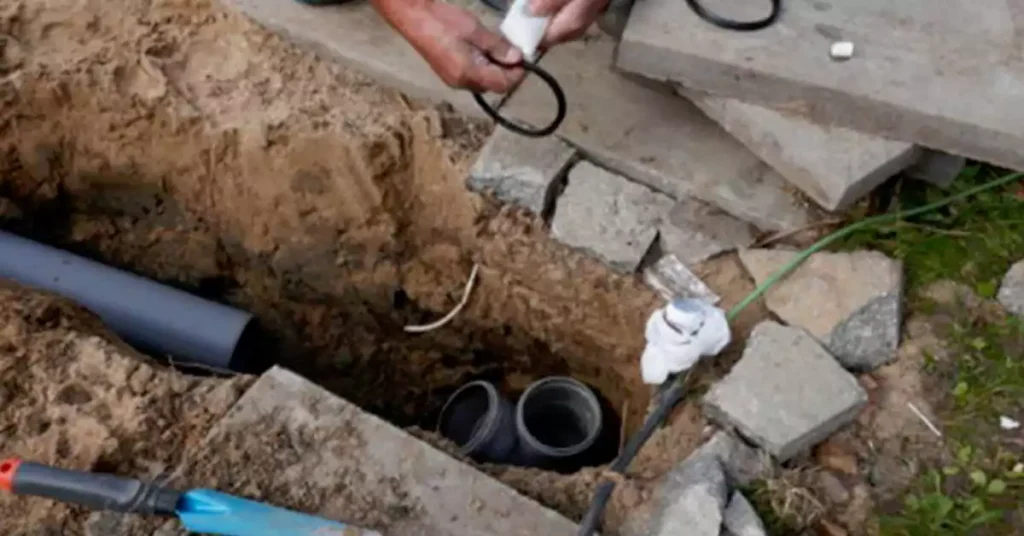
Proper installation of underground electrical conduit is crucial to ensure the safe and effective routing of cables. In this section, we will guide you through the step-by-step process of installing underground electrical conduit, covering site preparation, conduit placement, cable running, cable pulling, sealing conduit joints, and implementing grounding and bonding techniques.
- Site Preparation and Excavation: Prepare the site and dig a trench to the required depth for the conduit installation.
- Conduit Placement and Support: Position the conduit in the trench and use straps to secure it in place.
- Running Underground Cables within Conduit: Run the electrical cables through the conduit following the designated path.
- Pulling and Securing Cables: Use appropriate tools to pull the cables through the conduit and secure them in place.
- Sealing and Waterproofing Conduit Joints: Seal the joints of the conduit to prevent water infiltration and protect the cables.
- Proper Grounding and Bonding Techniques: Ensure proper grounding and bonding of the electrical system for safety and functionality.
Site Preparation and Excavation:
After confirming the wiring installation site, perform the following 5 steps:
- Identify the desired pathway for the conduit and mark it accordingly.
- Contact the local utility companies to locate any existing underground utilities in the area to avoid accidental damage.
- Obtain necessary permits and adhere to local regulations for excavation and construction.
- Excavate a trench along the marked pathway with appropriate width and depth, considering the bury depth requirements discussed earlier.
- Ensure the trench bottom is smooth and free from rocks or sharp objects that could damage the conduit.
Conduit Placement and Support:
After the site and trench are ready, proceed to install the conduit in the following 3 steps:
- Select the appropriate type and size of conduit based on the wiring requirements and bury depth guidelines.
- Place the conduit in the trench, making sure it follows the desired pathway.
- Provide proper support for the conduit using straps, clamps, or conduit hangers at regular intervals to prevent sagging or movement.
Running Underground Cables within Conduit:
After the conduit is ready, follow these three steps to run the wires:
- Prepare the cables by removing any outer sheathing or insulation as required.
- Feed the cables into the conduit, ensuring they are properly aligned and not twisted or strained.
- Use cable lubricant if necessary to facilitate smooth cable pulling.
Pulling and Securing Cables:
Do the following 3 things to ensure safe cables pulling:
- Employ appropriate cable pulling techniques, such as using cable pulling grips or fish tape, to smoothly and safely pull the cables through the conduit.
- Avoid exceeding the recommended pulling tension to prevent cable damage.
- Once the cables have been pulled through, secure them at both ends to prevent movement or strain.
Sealing and Waterproofing Conduit Joints:
Apply the following 3 steps to ensure the conduit connection’s safe and integrity:
- Install appropriate fittings and connectors at conduit joints to ensure a secure and watertight connection.
- Apply conduit sealant or waterproofing compound to the joints to protect against moisture infiltration.
- Use heat shrink tubing or electrical tape to further seal and insulate the connections, if necessary.
Proper Grounding and Bonding Techniques:
During conduit installation, right and proper grounding and bonding are very important, follow these 3 things below to do the right grounding:
- Install grounding electrodes, such as ground rods, at appropriate locations as per local electrical codes.
- Connect the conduit system to the grounding electrodes using copper grounding wire of appropriate gauge.
- Implement bonding techniques to ensure proper electrical continuity throughout the conduit system, including bonding clamps or jumpers between metallic conduit sections.
It is crucial to consult local electrical codes, regulations, and seek professional guidance during the installation process to ensure compliance and safety.
유지 보수 및 문제 해결
Proper maintenance and regular inspections are essential to ensure the longevity and reliability of underground electrical conduit systems. In this final section, we will discuss important considerations for maintaining and troubleshooting underground electrical conduit, including inspections, repair techniques, locating conduit, troubleshooting common issues, and cable maintenance.
Regular Inspections and Maintenance Check List:
– Conduct periodic inspections of the conduit system to identify any signs of damage, corrosion, or deterioration.
– Inspect conduit supports, hangers, and clamps to ensure they are secure and in good condition.
– Check for proper sealing and waterproofing at conduit joints to prevent moisture ingress.
– Inspect grounding connections and ensure proper electrical continuity throughout the conduit system.
– Clear any debris or vegetation that may have accumulated around the conduit system.
Identification and Repair of Damaged Conduit:
– If damage is detected, assess the severity and extent of the damage. Common types of conduit damage include cracks, breaks, or corrosion.
– Repair minor damage using appropriate repair methods, such as using epoxy or repair sleeves to seal cracks.
– For severe damage, consider replacing the damaged section of conduit to maintain integrity and safety.
– Follow manufacturer guidelines and consult professionals for complex repairs or replacements.
Locating and Accessing Underground Conduit:
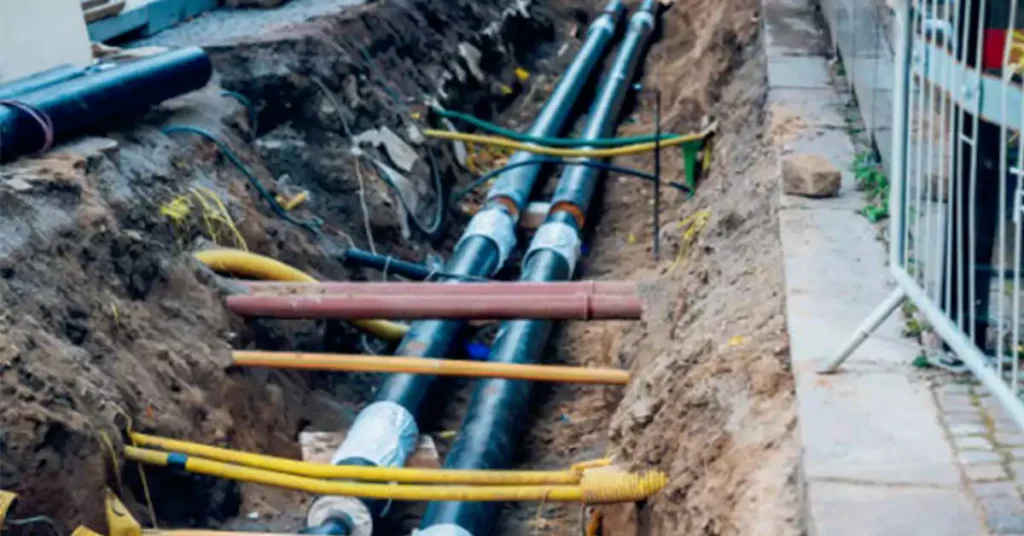
– Maintain accurate records and mapping of the conduit system’s layout, including access points, junctions, and utility connections.
– Use specialized equipment, such as cable locators or ground-penetrating radar, to locate and trace the underground conduit.
– Establish access points, such as handholes or pull boxes, at strategic locations for easier maintenance and troubleshooting.
Troubleshooting Common Conduit Issues:
- Insufficient Capacity: If the conduit system becomes overloaded or lacks capacity for additional cables, consult an electrician to assess the situation and consider upgrading conduit size or installing additional conduits.
- Water Infiltration: If water is infiltrating the conduit system, inspect and repair the seals and waterproofing at conduit joints. Consider applying additional sealant or waterproofing compounds.
- Cable Pulling Issues: If cables encounter resistance or become stuck during installation or maintenance, use lubricants, cable pulling grips, or fish tape to aid in smooth cable movement.
- Grounding and Bonding Problems: Check grounding connections and bonding techniques to ensure proper electrical continuity. Repair or reinforce connections as needed.
Cable Maintenance and Replacement:
- Regularly inspect cables for signs of wear, damage, or degradation, such as cracks, fraying, or insulation deterioration.
- Replace damaged cables using appropriate cable splicing or termination methods.
- Consider implementing cable management techniques, such as cable trays or supports, to prevent strain or damage to the cables within the conduit.
Remember to follow local electrical codes, regulations, and consult professionals when performing maintenance or troubleshooting tasks to ensure safety and compliance.
How to Choose the Right Conduit for Your Application?
Selecting the right conduit for your specific application is crucial to ensure optimal performance, protection, and compliance with electrical regulations.
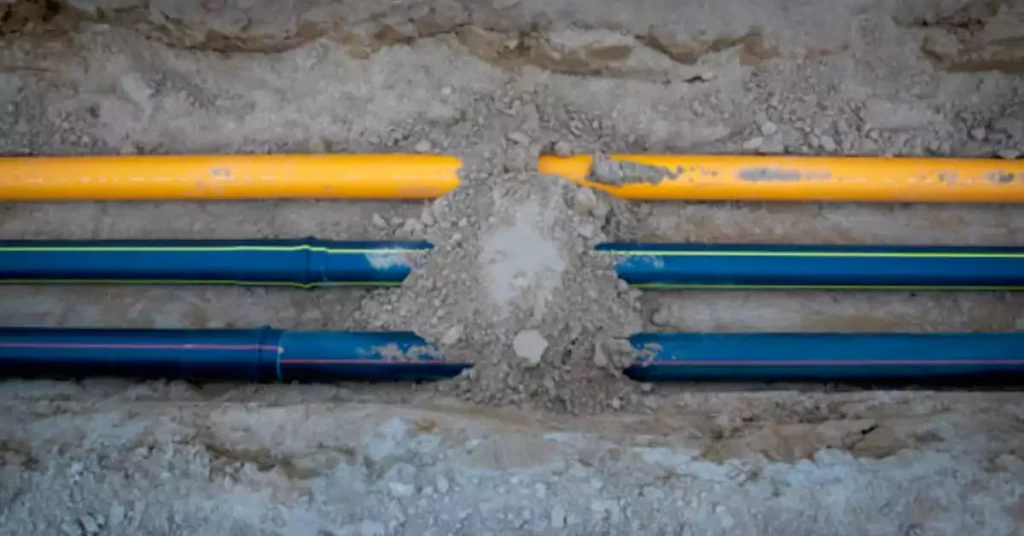
3 Factors Need to be Considered for Choose the Right Conduit
환경 조건: Assess the environmental factors that the conduit will be exposed to, such as moisture, chemicals, temperature variations, UV exposure, or corrosive substances. Choose a conduit material that offers suitable resistance and durability for the specific environment.
Cable Types: Consider the type of cables that will be installed within the conduit. Different cable types, such as power cables, data cables, or fiber optics, may have specific requirements for bend radius, insulation compatibility, or electromagnetic shielding. Ensure the selected conduit can accommodate the cable types effectively.
Voltage Ratings: Evaluate the voltage ratings of the electrical system to determine the appropriate conduit material and size. Higher voltage systems may require conduit with enhanced insulation properties and increased mechanical strength.
Comparing 5 Different Underground Electrical Conduit (Pros and Cons)
Conduit Type | 재료 | Pros | Cons | Cost |
강성 금속 도관(RMC) |
강철 | Excellent mechanical protection; High strength and durability; Good grounding capability |
Heavyweight; Complex installation |
높은 |
전기 금속 튜브(EMT) |
강철 알류미늄 |
Lightweight and easy to install; | Limited physical protection; Not suitable for extreme conditions; Lower durability compared to RMC |
보통의 |
Fiberglass Conduit |
Fiberglass | Corrosion-resistant; Lightweight; Excellent electrical insulation; Easy to install | Limited availability and higher cost; More brittle compared to metal conduits |
높은 |
PVC 도관 |
비닐 |
Lightweight and easy to install; Corrosion and chemical resistant | Lower impact resistance compared to metal conduits; Limited temperature range |
Low |
HDPE Conduit |
HDPE |
Easy to install; Corrosion and chemical resistant; Good impact resistance | Lower mechanical strength compared to metal conduits; Requires specialized tools for installation |
보통의 |
Always seek advice from electrical professionals or consultants who have expertise in conduit systems. They can provide valuable insights and recommend the best conduit types based on your specific requirements and local regulations.
Remember to prioritize safety, compliance with local codes and regulations, and consider long-term durability and maintenance considerations when making your conduit selection.
If you would like to compare direct burial PVC conduit, please refer to our direct burial PVC conduit tutorial.
FAQs about Underground Conduit
Can Electrical Nonmetallic Tubing be used underground?
Electrical Nonmetallic Tubing (ENT) is not recommended for direct burial or underground applications.
ENT is made of plastic, typically PVC, and is primarily used for protecting electrical wires and cables in residential and commercial buildings. It is lightweight, flexible, and easy to work with, making it suitable for surface-mounted or concealed installations within walls, ceilings, or floors.
Using ENT underground could expose it to damage from rocks, soil pressure, moisture, and other elements, potentially compromising the integrity of the electrical system. Therefore, it is important to consult local electrical codes and regulations, as well as professional advice, to ensure that the appropriate conduit is chosen for underground applications to meet safety and compliance requirements.
Are underground electrical conduits watertight?
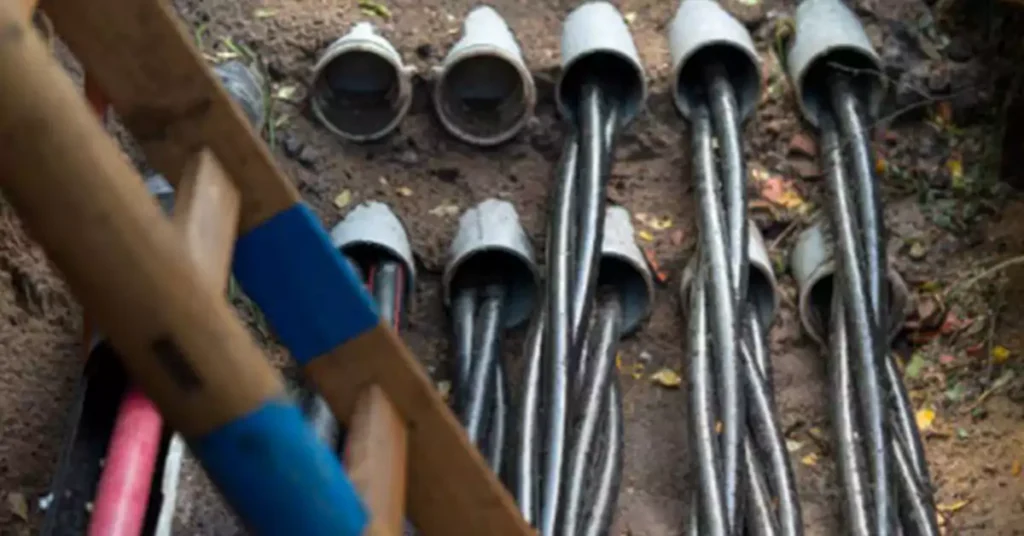
Underground electrical conduits are not inherently watertight. While one might assume that the interior of underground conduits would remain dry, it is important to recognize that they are considered wet locations. Therefore, wires and cables installed in underground conduits must be approved for such conditions.
When a conduit transitions between different temperatures, such as from outside a building to inside, it is necessary to seal the ends of the conduit. This sealing prevents the unrestricted flow of moist air and the buildup of condensation inside the conduit.
It is crucial to prioritize the sealing of underground conduits to prevent water ingress and protect the integrity of the electrical system. By following these guidelines and using appropriate sealing methods, the risk of moisture-related issues can be minimized.
결론
In summary, underground electrical conduit plays a vital role in electrical installations by providing protection, organization, and proper routing of cables. It ensures the safety, reliability, and efficiency of electrical systems while minimizing the risk of damage or accidents. Utilizing conduit offers benefits such as improved cable management, easier maintenance, and reduced downtime during repairs or upgrades.
It is crucial to adhere to local codes, regulations, and safety requirements when installing underground electrical conduit. Compliance with these standards ensures the protection of personnel, property, and the environment. By following the prescribed guidelines, you can mitigate potential hazards, prevent electrical faults, and maintain a safe working environment.
By understanding the importance of conduit, following safety codes, practicing proper installation, and selecting the appropriate conduit type, you can establish a reliable and efficient underground electrical system. Prioritizing these factors ensures safety, compliance, and optimal performance in your electrical installations.
Any questions and electrical conduit requirements, 언제든지 저희에게 연락하세요.