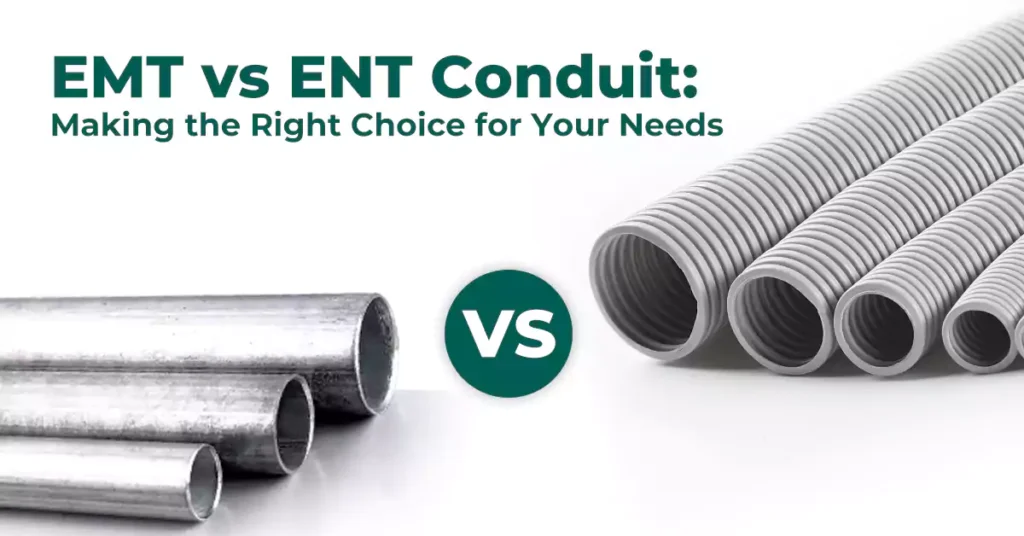
Table des matières
When it comes to protecting and routing electrical wiring in residential, commercial, or industrial installations, choosing the right type of conduit is essential. Two of the most commonly used options are EMT conduit (Electrical Metallic Tubing) and ENT conduit (Electrical Nonmetallic Tubing). While both serve the core function of shielding wires and ensuring safety, their materials, flexibility, installation methods, and typical use cases differ significantly.
Whether you’re an electrician planning your next project, a contractor bidding on a job, or a facility manager reviewing your electrical infrastructure, understanding the differences between EMT electrical conduit and ENT tubing can help you make an informed decision. This article dives into a detailed comparison of EMT pipe and ENT flex conduit, covering everything from composition and performance to code compliance and best-use scenarios.
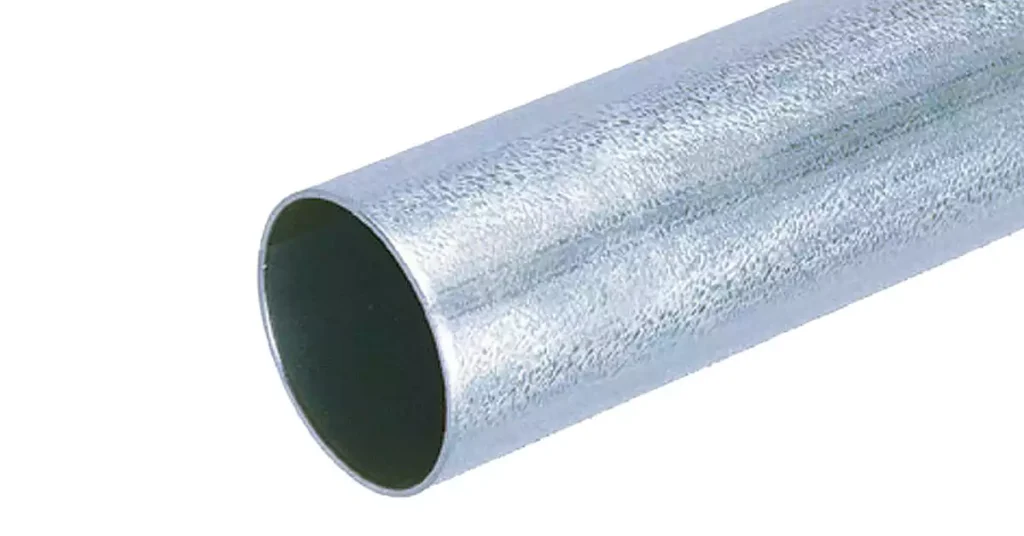
EMT conduit, short for Electrical Metallic Tubing, is a type of metal raceway widely used in electrical installations to protect and route wiring. Often referred to as EMT pipe or EMT electrical tubing, this conduit is typically made from galvanized steel or, in some cases, aluminum, offering a rigid yet lightweight solution for a variety of building projects.
EMT is classified as a metallic conduit, but unlike heavier alternatives such as RMC (Rigid Metal Conduit), EMT is thinner-walled and easier to work with, while still meeting strength and safety standards. It is frequently used in exposed indoor applications and is particularly popular in commercial and light industrial environments where wiring needs to be visible, organized, and protected from physical damage.
EMT is typically manufactured from galvanized steel, offering high strength and durability. Some variants are made from anodized aluminum, which is lighter and more corrosion-resistant in certain environments.
EMT has a thin wall design, making it significantly lighter than RMC and IMC, which translates to easier handling and faster installation. Despite its lighter weight, it provides adequate mechanical protection in many applications.
EMT can be bent on-site using manual or powered conduit benders. This flexibility allows for customized routing around obstacles and structural components without requiring additional fittings.
EMT is zinc-coated (galvanized) for corrosion resistance. However, unlike nonmetallic options, it is not inherently rust-proof, and additional protective coatings or fittings may be needed in damp or corrosive environments.
As a metallic conduit, EMT can serve as an equipment grounding conductor (EGC), reducing the need for a separate ground wire in many cases. However, all connections must be properly bonded to ensure safety.
EMT is non-combustible and does not emit toxic gases when exposed to high temperatures, making it suitable for fire-rated assemblies and critical systems.
EMT works with a wide variety of fittings—compression, set-screw, and threaded types—and can be connected to boxes, enclosures, and other raceway systems using standard accessories.
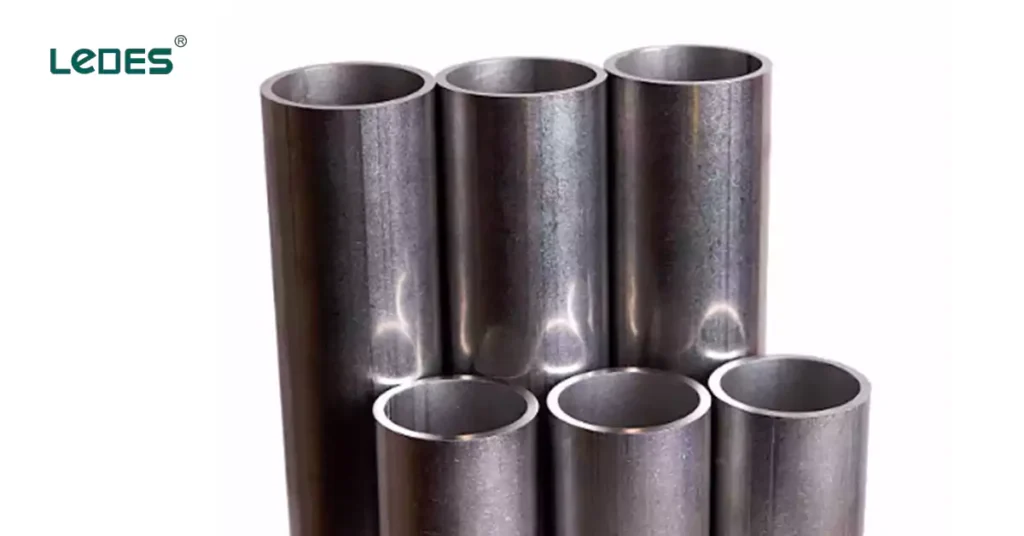
EMT provides solid defense against physical impact, abrasion, and compression, helping safeguard wiring in high-traffic areas or industrial settings.
Being metal, EMT does not support combustion or produce smoke, making it a reliable choice for installations in fire-rated structures or hazardous locations.
Compared to heavier RMC or IMC, EMT offers a more economical metallic conduit solution without sacrificing critical protection.
Its sleek, polished exterior makes EMT ideal for visible installations in commercial buildings, hospitals, schools, and retail spaces where a clean, professional look is important.
EMT’s light weight and ease of bending reduce labor time and material waste during installation, improving project timelines and overall efficiency.
Steel and aluminum conduits are 100% recyclable, aligning with sustainable building practices and environmental compliance standards.
EMT’s galvanized coating offers only limited protection in moisture-prone or chemical-laden areas. Prolonged exposure may result in rust unless additional protective measures – like painting, wrapping, or using PVC-coated variants – are taken.
While EMT is more flexible than RMC or IMC, it still requires tools and expertise to bend accurately. This rigidity can limit its use in confined or irregular spaces.
EMT’s metal composition requires consistent bonding and grounding across the system. Improper bonding can result in electrical hazards or non-compliance with code requirements.
Compared to ENT flex conduit or plastic raceways, EMT adds more weight to the system, which may not be ideal for all structural environments, especially where support constraints exist.
Unlike nonmetallic systems, metallic conduit can conduct electricity. Any damage to insulation inside the conduit may present additional risks if grounding is not properly implemented.
It’s easy to get confused by the names EMT (Electrical Metallic Tubing) and ENT (Electrical Nonmetallic Tubing)—they sound like two versions of the same thing, just made from different materials. But here’s the important distinction:
- ENT is a flexible, corrugated plastic conduit.
• EMT is a rigid, smooth-walled metal conduit.
Even though EMT includes the word “tubing,” it’s not flexible like a hose or ENT tubing. EMT must be bent using a conduit bender and holds its shape after bending—making it part of the rigid conduit family. ENT, on the other hand, is pre-flexible and designed to bend by hand.
So while ENT and EMT differ in material, they also differ in structure and flexibility, which directly affects how and where you can use them in electrical installations.
To ensure safety, performance, and regulatory compliance, EMT electrical conduit must meet specific manufacturing standards. The most recognized standards in North America are:
- UL 797: Standard for EMT – Steel
- UL 797A: Standard for EMT – Aluminum and Stainless Steel
- ANSI C80.3: American National Standard for steel EMT conduit
- CSA C22.2 No. 83.1:07: Canadian standard for EMT
UL 797, developed by Underwriters Laboratories (UL), is the primary standard for steel EMT conduit and elbows. This standard sets the requirements for material, construction, marking, testing, and performance.
EMT must be manufactured from steel.
The structural integrity and long-term durability of EMT electrical conduit are not only reliant on its base material, usually low-carbon steel. But also heavily dependent on its protective coatings, both inside and out. These coatings ensure that the conduit can withstand harsh installation environments, corrosive atmospheres, and electrical system faults.
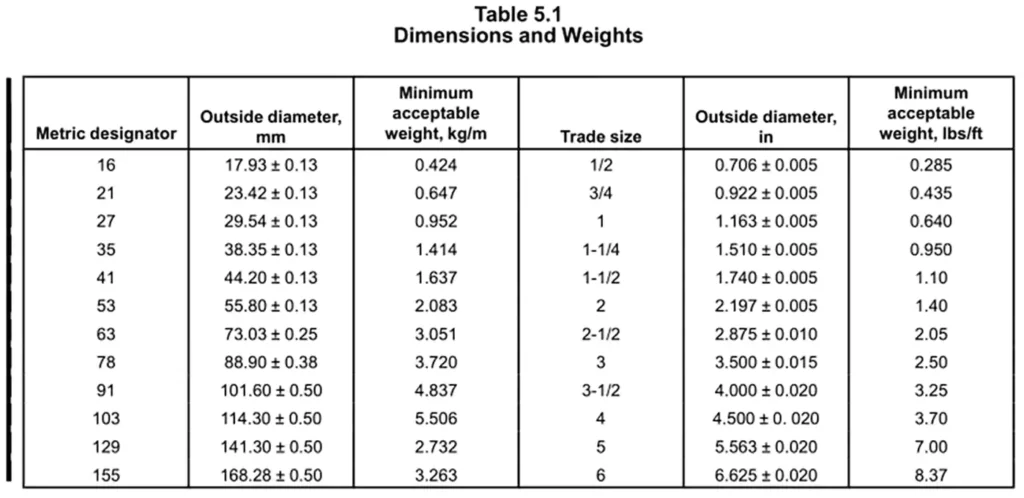
The wall thickness must meet specific minimum values based on trade size to ensure mechanical strength.
Inside and outside diameters are tightly controlled for compatibility with fittings and connectors.
Electrical Metallic Tubing (EMT) must meet strict mechanical integrity standards to ensure safety and durability during handling, bending, and installation.
Ambient Temperature Bend Test
To verify the tube’s ductility and seam integrity under normal installation conditions.
Cold Temperature Bend Test
To confirm the low-temperature flexibility and weld resilience of the finished EMT tube, ensuring safe use in cold climates.
Electrical Metallic Tubing (EMT) must have protective coatings that resist cracking, flaking, and corrosion. UL 797 outlines specific test procedures for three types of coatings: Zinc, Organic, and Alternate Corrosion-Resistant Coatings.
All types of protective coatings—whether applied inside or outside—must:
Withstand mechanical bending without cracking or flaking (visually inspected).
Endure a low-temperature flexibility test at 0°C (32°F) without exposing bare metal or delaminating the coating.
Ensure consistent performance on the smallest trade size tubing available.
For non-metallic coatings, chemical identity must be confirmed through IR spectroscopy, Thermogravimetric Analysis (TGA), and Differential Scanning Calorimetry (DSC).
Zinc coatings are tested using the Copper Sulfate Immersion Test to assess corrosion resistance:
Exterior zinc coating: Must withstand four 60-second immersions without forming a bright, firmly-adhering copper deposit.
Interior zinc coating: Must pass after just one 60-second immersion.
Organic coatings, often applied to the interior surfaces of electrical metallic tubing, must meet mechanical and environmental durability standards.
Elasticity Test
This test evaluates the coating’s mechanical flexibility and ability to withstand deformation without cracking
Warm Humid Air Test
This test assesses the coating’s resistance to moisture absorption, corrosion promotion, and adhesion breakdown under sustained humidity and heat.
Alternate corrosion-resistant coatings (used on steel electrical metallic tubing (EMT)) must undergo rigorous testing to ensure durability, environmental resistance, and mechanical performance. These coatings are typically applied inside and outside the conduit and must meet or exceed the performance of conventional zinc-based galvanizing.
Resistance to UV Light and Water:
Evaluates the coating’s ability to withstand prolonged sunlight exposure and water contact without degrading.
Exposing to a UV light source and water spray in a controlled chamber, and no cracking, peeling, discoloration.
Salt Spray (Fog) Test:
Assesses the coating’s corrosion resistance in a high-salinity environment.
Placing in a salt fog chamber maintained at 35°C and exposed to continuous salt spray, no visible corrosion, pitting, or coating loss on exposed areas.
Moist Carbon Dioxide-Sulfur Dioxide-Air Test:
Tests resistance to acid rain-like and industrial atmosphere conditions.
Exposing to a mixture of moist CO₂, SO₂, and air, simulating harsh urban or factory environments, coating must remain chemically stable, showing no signs of corrosion, blistering, or flaking.
Tensile Strength Test:
Verifies the mechanical strength of the coating.
Coated material is subjected to tensile forces to ensure it maintains integrity and doesn’t tear, delaminate, or fracture under stress.
Cold Impact Test:
Measure brittleness and impact resistance at low temperatures.
Conduit is cooled to a specified low temperature (often -18°C or below) and then struck with a standard weight/force.
No cracking, denting, or coating damage visible after impact.
Flammability Test:
Ensures the coating doesn’t pose a fire hazard during installation or in case of electrical faults.
The coating must self-extinguish, show minimal flame spread, and not drip flaming particles.
To ensure traceability, proper usage, and regulatory compliance, UL 797 specifies clear marking requirements for Electrical Metallic Tubing (EMT). Normally include:
Identification du fabricant
Product Type: “Electrical Metallic Tubing” or “EMT”
Temperature Ratings for Nonmetallic Coated Tubing
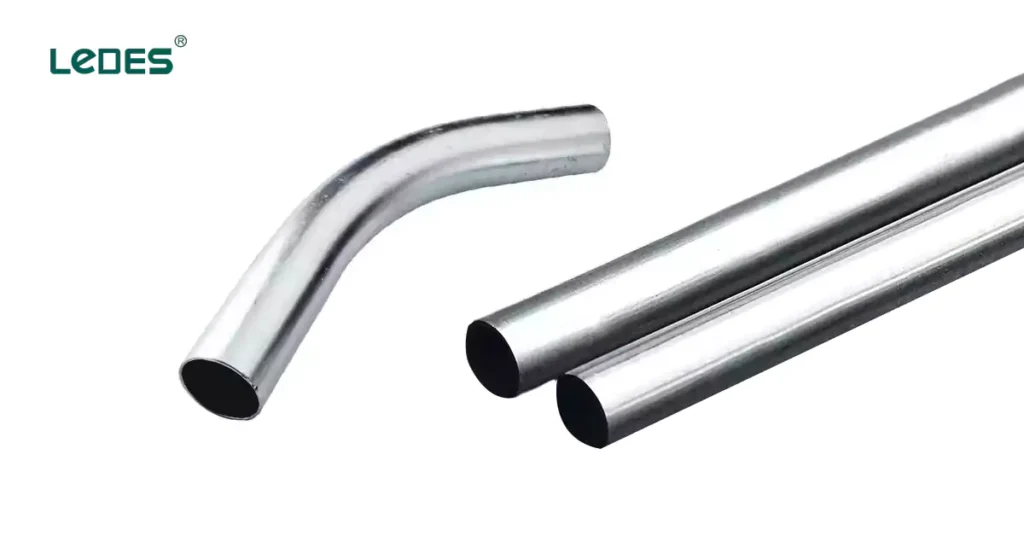
UL 797A is the standard for EMT made from aluminum or stainless steel, developed to address alternative materials with corrosion-resistant properties.
This standard outlines the structure, dimension requirements for the tube itself and its coatings (Aluminum and stainless steel tubing does not require a protective coating, but with exceptions) , as well as the bending performance requirement for finished tubing.
Steel EMT is the industry standard due to its balance of strength, cost, and availability.
UL 797 has broader recognition in construction and industrial applications.
UL 797A is less commonly used because aluminum and stainless steel EMT are more expensive and are usually chosen only for niche environments—such as food processing, coastal, or corrosive industrial settings.
Consequently, demand is lower, and most manufacturers opt for UL 797 listing to serve mainstream needs.
ANSI C80.3 is a key American National Standard that establishes the specifications for Electrical Metallic Tubing (EMT), a commonly used type of steel conduit in commercial, industrial, and residential electrical systems. This standard is published by the American National Standards Institute (ANSI) in collaboration with NEMA (National Electrical Manufacturers Association), and it plays a critical role in ensuring the safety, performance, and interoperability of EMT conduits across the electrical industry.
The standard defines essential requirements for:
- Materials and construction of EMT, primarily manufactured from low-carbon steel with a protective zinc coating to enhance corrosion resistance.
- Dimensional tolerances, including outside diameter and wall thickness, to ensure compatibility with fittings and support uniform installation practices.
- Mechanical properties, such as rigidity, compression strength, and impact resistance, ensuring the conduit can protect enclosed electrical wires in demanding environments.
- Coating performance, particularly regarding corrosion protection, adhesion, and durability under various conditions.
CSA C22.2 No. 83.1:07 is the Canadian equivalent of UL 797, developed by the Canadian Standards Association (CSA).
- Incorporates similar performance criteria for corrosion resistance, mechanical strength, and electrical continuity.
- Recognized under the Canadian Electrical Code (CEC).
In many cases, conduit manufacturers create EMT that complies with both UL 797 and CSA C22.2 No. 83.1:07, making it suitable for use in both the United States and Canada.
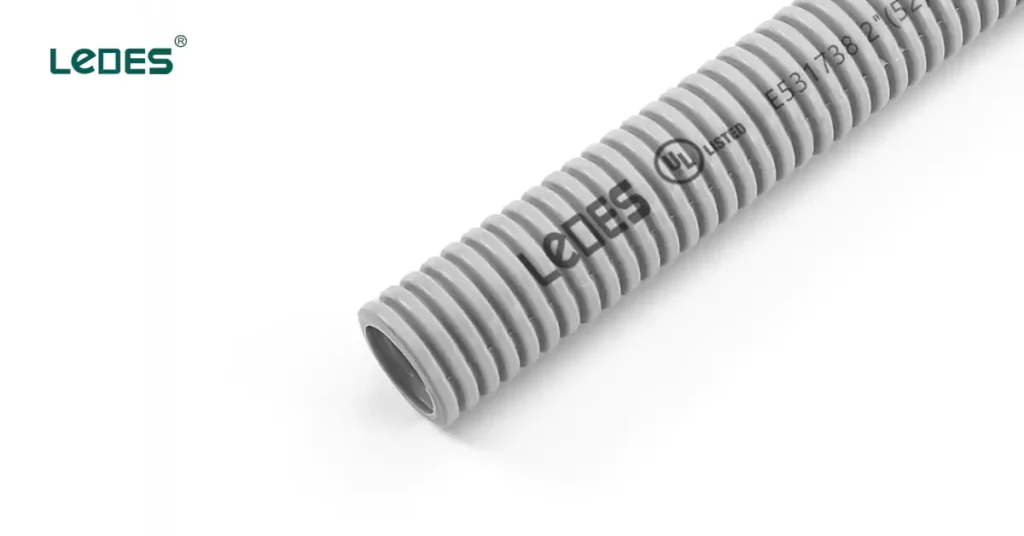
ENT conduit is a type of flexible, lightweight plastic conduit used for electrical raceway systems. ENT is primarily made from PVC (polyvinyl chloride) or other nonmetallic thermoplastics and is designed for use in dry, indoor environments, such as within walls, ceilings, or poured concrete slabs in residential, commercial, and institutional buildings. Unlike rigid conduit systems, ENT offers easy installation and adaptability without sacrificing essential protection for electrical wiring..
Conseils de pro : You can read our last post for the electrical raceway beginner guide if you are still confused about this system.
ENT conduit offers a wide range of benefits:
Lightweight and Flexible: ENT is extremely lightweight and can be bent easily by hand, which eliminates the need for conduit benders or heavy tools.
Quick Installation: ENT reduces installation time due to its flexibility and compatibility with snap-in fittings, leading to lower labor costs.
Non-conductive: Because it is not made of metal, ENT does not require grounding, which simplifies compliance with electrical code.
Corrosion and Moisture Resistance: ENT is inherently resistant to rust, corrosion, and moisture, making it suitable for environments with humidity or in-slab concrete installations.
Flame-Retardant: ENT materials are treated to resist combustion, contributing to improved fire safety in buildings.
Low Cost: ENT is typically less expensive than metallic conduit systems both in terms of material and labor costs.
Compatible with Concrete Encasement: It performs well when embedded in concrete, such as in slab-on-grade foundations or tilt-up wall panels.
Despite its strengths, ENT has several limitations:
Not Suitable for Outdoor Exposure: ENT is generally not UV-resistant and should not be used in locations where it will be directly exposed to sunlight unless rated otherwise.
Lower Mechanical Strength: Compared to metallic conduit like EMT, ENT is more susceptible to physical damage such as crushing, puncturing, or cutting.
Plage de température limitée : ENT typically has a lower maximum temperature rating (often around 50°C or 122°F), limiting its use in high-heat areas like near mechanical rooms or rooftops.
Limited Mechanical Strength: ENT’s flexible plastic construction may not meet the strength and durability requirements for environments with high traffic, heavy equipment, or demanding mechanical protection needs.
Requires Proprietary Fittings: ENT systems rely on specific fittings designed for use with ENT, limiting interchangeability with other conduit systems.
To ensure Electrical Nonmetallic Tubing (ENT) meets essential safety, performance, and construction requirements, it is governed by two primary standards:
- UL1653 – Standard for Electrical Nonmetallic Tubing (ENT)
- CSA C22.2 No. 227.1 – Standard for Electrical Nonmetallic Tubing (ENT)
These standards specify rigorous testing and performance benchmarks for ENT used in both residential and commercial installations in North America. UL 1653 is the benchmark for ENT products in the United States, while CSA C22.2 No. 227.1 governs similar requirements in Canada. Both outline criteria such as flammability resistance, tensile strength, impact resistance, bend radius limitations, dimensional tolerances, and material integrity at various temperatures and conditions.
These standards also regulate ENT fittings and accessories to ensure complete system compatibility and mechanical security. Compliance with either UL or CSA certification is a key assurance of quality and code-compliant performance in construction projects.
For a more detailed explanation of the specific tests and performance requirements included in these standards, please refer to our in-depth article:
ENT Tubing Type, Code Compliance and Performance
While EMT (Electrical Metallic Tubing) and ENT (Electrical Nonmetallic Tubing) are both used to route and protect electrical wiring, they differ significantly in material, flexibility, installation methods, performance characteristics, and code applications.
Aspects | Conduit EMT | Conduit ORL |
Matériel | Steel or aluminum | PVC or other nonmetallic polymers |
Rigidity | Rigide | Flexible |
Coating Protection | Zinc-coated (or other corrosion-resistant coating) | No requirement |
Résistance à la corrosion | Good with coatings; can corrode if exposed | Excellent in damp environments; will not rust |
Résistance au feu | Haut | Modéré |
Résistance aux chocs | Très haut | Moderate; not designed for heavy mechanical abuse |
Poids | Plus lourd | Lightweight and easy to carry |
Installation | Harder; requires cutting, threading, and fastening with tools | Easier; snaps together with simple fittings |
Bending | Requires manual or powered conduit bender | No bender needed; flexible by design |
Raccords | Metal connectors and couplings | ENT-specific plastic snap-on fittings |
Coût | Généralement plus cher | Lower |
Code Reference | UL 797, CSA C22.2 No. 83.1, ANSI C80.3 | UL 1653, CSA C22.2 No. 227.1 |
Applications | Commercial buildings, outdoor, exposed areas, high-stress environments | Indoor use, in walls, ceilings, floors in residential/light commercial buildings |
Selecting between EMT (Electrical Metallic Tubing) and ENT (Electrical Nonmetallic Tubing) isn’t just about preference — it’s about choosing the most appropriate solution based on code requirements, project environment, installation needs, and long-term performance expectations. Here’s a breakdown of the key considerations that can help guide your decision:
- Intérieur vs extérieur :
ENT is primarily intended for indoor, concealed installations, such as in walls, ceilings, or under floors. It is not UV-rated unless specifically marked.
EMT, on the other hand, is suitable for both indoor and outdoor use and performs well in exposed or hazardous environments due to its corrosion- and fire-resistant properties.
- Moisture and Corrosive Exposure:
For damp or corrosive environments, ENT offers excellent resistance to moisture and will not rust, making it ideal for indoor utility rooms or basements. EMT with proper coatings can also handle these conditions, but might require additional corrosion protection over time.
- Heavy-Duty Protection:
EMT is the clear choice where mechanical protection is a priority — for example, in industrial settings, warehouses, or areas where conduit may be exposed to impact.
- Low Impact Areas:
ENT is adequate for residential and light commercial construction where conduit will be concealed and is unlikely to face physical damage.
EMT offers superior fire resistance due to its steel composition. It is often required by code in fire-rated walls or plenum spaces.
ENT must meet specific flame spread and smoke development requirements, but it’s generally not permitted in plenum spaces unless it has been specifically tested and listed for such use.
- Material Costs:
ENT is generally less expensive than EMT due to lower material and labor costs. - Long-Term Value:
EMT may carry a higher upfront cost but offers greater durability and protection, reducing maintenance or replacement over time.
Careful evaluation of these factors ensures your conduit system is not only compliant but also optimized for safety, efficiency, and performance.
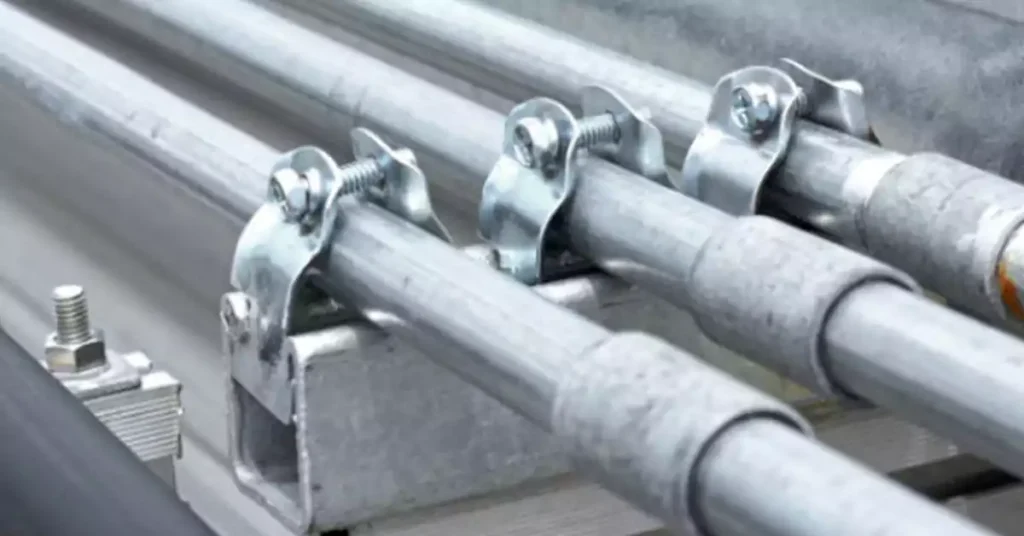
Use the correct tools: EMT requires cutting with a conduit cutter or a hacksaw and bending with a manual or hydraulic bender. Always deburr the ends after cutting to prevent wire damage.
Secure with proper fittings: Use only UL-listed or CSA-certified fittings such as compression or set-screw connectors. Ensure all joints are tight and properly bonded for electrical continuity.
Follow support spacing rules: Per NEC, EMT must be supported within 3 feet (0.9 m) of each box and every 10 feet (3 m) thereafter.
Protect from corrosion: If installed outdoors or in damp locations, EMT should be coated or galvanized and properly sealed at joints to prevent moisture ingress.
Over-bending the tubing, which can flatten the cross-section or crack the coating
Failing to bond metal conduit in grounding paths
Improper use of non-listed fittings, leading to loose or unsafe connections
Lack of support or over-spanning, which can cause sagging and strain on wires
Use ENT-specific fittings: ENT uses snap-in, solvent-weld, or twist-lock type connectors and couplings designed for plastic tubing. Don’t substitute with metal EMT fittings.
Secure during concrete pours: In slab-on-grade installations, ENT must be secured firmly to prevent floating or movement during concrete placement.
Protect from UV exposure: ENT is not sunlight-resistant unless specified. Use it only in concealed spaces like walls, ceilings, or under slabs.
Exposing ENT to direct sunlight, leading to material degradation over time
Improper securing, especially in concrete, which may result in misalignment
Routing in areas requiring higher crush resistance, like exposed industrial floors, where rigid options would be better
Always check the National Electrical Code (NEC) or Canadian Electrical Code (CEC) for the latest conduit installation rules, including allowed uses, support intervals, and environmental considerations. And when in doubt, refer to the manufacturer’s installation guide, especially when working with specialized fittings or accessories.
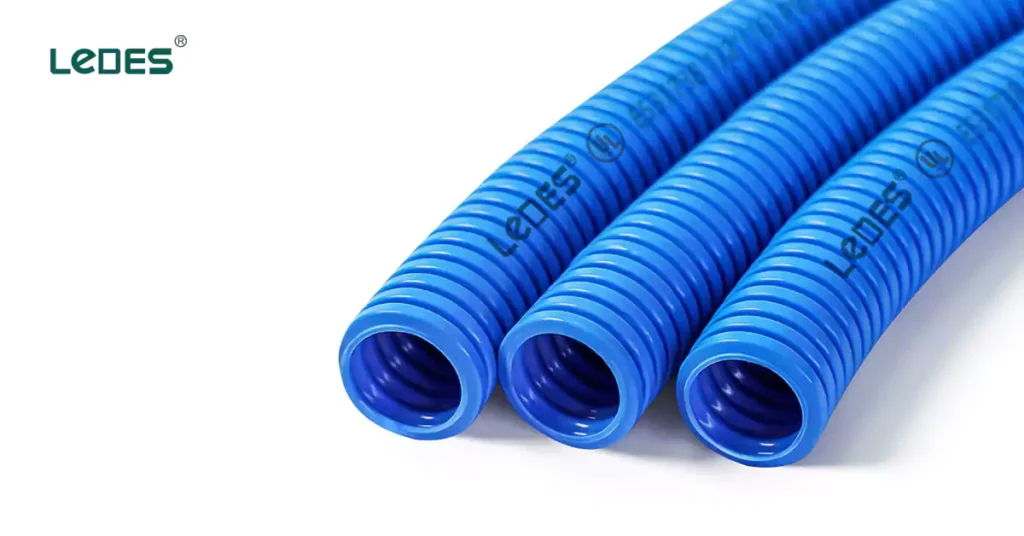
Ledes is a conduit manufacturer and supplier with many years’ experience, stands out for its offerings of high-performance conduit solutions, including the electrical nonmetallic tubing and fittings. Whether you’re working on new construction or renovations, Ledes provides a comprehensive ENT product system designed to meet modern installation demands.
Ledes ENT conduit is available in a wide range of trade sizes to accommodate various project needs. Available in trade sizes from 1/2-inch to 2-1/2-inch, from smaller diameters for lighting and branch circuits to larger sizes for feeders and main service runs, providing the flexibility to match every application.
Quality and safety are non-negotiable. Ledes ENT products are:
- UL listed to UL 1653 for American market
- cUL listed to CSA C22.2 No.227.1 for Canadian market
These certifications ensure full compliance with the National Electrical Code (NEC) and Canadian Electrical Code (CEC), giving installers and inspectors confidence in both performance and safety.
Conseils de pro : Pay more attention about some keywords like ‘UL Compliance’ ENT conduit, this is totally different ‘UL certified’ or ‘UL listed conduit’. You can see our definitive guide for UL Listed Vs. UL Compliance PVC Conduit.
Lédes ENT tubing is manufactured using high-impact resistant PVC material that ensures:
- Excellent flexibility for quick installation around corners and obstructions
- Reliable crush resistance to protect cables during concrete pours and drywall work
- Long-lasting durability that performs well in concealed indoor environments and with UV-resistant property that suitable for outdoor installations.
We don’t just offer conduit, to complete the system, we provide fittings for use with conduit as well, such as:
- ENT Couplings: Snap-in designs that ensure a secure and watertight connection
- Slab Boxes: Designed for use in poured concrete floors and slabs, with multiple conduit entry points
- Wall Boxes: Ideal for mounting outlets and devices in framed walls, compatible with standard and deep box requirements
All fittings are engineered for fast, tool-free assembly, reducing jobsite time and increasing overall efficiency.
Choosing between EMT and ENT conduit comes down to understanding your project’s specific requirements. EMT offers superior mechanical strength and fire resistance, making it ideal for exposed and high-impact environments. ENT, on the other hand, provides excellent flexibility, ease of installation, and corrosion resistance—especially suited for concealed and slab applications.
Both types are governed by strict UL and CSA standards that ensure safety and performance. Ledes supports your needs with a comprehensive range of UL/cUL certified ENT products and fittings, backed by proven quality and service. By evaluating factors like environment, installation complexity, and compliance needs, you can confidently select the right tubing solution for lasting performance and safety.
Can ENT be used in exposed outdoor installations?
Yes. If ENT is rated for UV-resistant, it is permitted for used in exposed outdoor locations.
EMT and ENT, which conduit is more fire-resistant?
EMT offers better fire resistance due to its metal composition. ENT is made of flame-retardant plastic, but it cannot match the performance of metal in high-heat environments.
Can EMT be used underground?
No, EMT is not recommended for underground use, because it can be damaged due to its thin-walled design. And it is not inherently watertight, it would require special watertight compression fittings and corrosion-resistant coatings for underground installations.
Is ENT conduit fire-rated?
No, ENT does not have a fire rating, but many ENT conduits are designed to be fire-resistant to meet required fire safety. Ledes ENT is certified for FT4 rating to meet demand fire safety requirement.
Which conduit is easier to install: EMT or ENT?
ENT (Electrical Nonmetallic Tubing) is generally easier to install than EMT (Electrical Metallic Tubing). Its lightweight, flexible construction allows for quick routing around obstacles without the need for bending tools. ENT can be cut with a utility knife and connected using snap-in fittings, making it ideal for fast installations in residential and light commercial settings. In contrast, EMT requires precise cutting, bending, and the use of compression or set-screw fittings, which demand more time, effort, and tools.
How to cut EMT conduit?
To cut EMT (Electrical Metallic Tubing) conduit properly, follow these professional steps:
- Mesurer et marquer : Use a tape measure to determine the desired length. Mark the cut point clearly using a permanent marker or a scribe for precision.
- Sécurisez le conduit : Place the conduit in a vise or on a stable surface to prevent movement during cutting. Ensure it is held firmly but not crushed.
- Select the Right Tool:
Tubing Cutter: A specialized tool for conduit cutting, it provides a clean, square cut. Rotate the cutter around the conduit, gradually tightening it after each rotation until the cut is complete.
Scie à métaux: Common and versatile, but requires steady hands for a straight cut. Use a fine-toothed blade and apply even pressure.
- Ébavurer les bords : After cutting, the inner and outer edges may have sharp burrs. Use a reaming tool or a round file to smooth out the edges. This step is critical to prevent wire insulation from being damaged during installation.
- Inspect the Cut: Ensure the cut is clean and straight. Re-cut or ream again if necessary.
Can you bury EMT conduit?
Yes, EMT (Electrical Metallic Tubing) can be buried, but only under specific conditions.
By itself, EMT is not rated for direct burial because it can corrode when exposed to moisture and soil. However, it can be used underground if it is installed in concrete encasement or has additional corrosion protection
According to the National Electrical Code (NEC), particularly NEC 358.10(B), EMT is permitted in wet locations, including underground, if corrosion protection is provided and it is not subject to severe physical damage.
How to ground EMT conduit?
To properly ground EMT (Electrical Metallic Tubing), you need to ensure continuous electrical continuity along the entire conduit system so it can serve as an effective equipment grounding conductor (EGC). Here’s how it’s done professionally:
- Use Approved Fittings and Connectors
Connect EMT using listed metallic couplings and connectors that are designed to maintain electrical continuity.
These fittings must be tightened securely to metal boxes or enclosures.
- Ensure Bonding at Enclosures
EMT must be securely bonded to all junction boxes, outlet boxes, and panels.
Metallic boxes automatically bond when EMT is connected with listed fittings. For non-metallic boxes, you must use a separate grounding conductor.
- Supplement with a Grounding Conductor (if required)
In some cases (such as for sensitive equipment or where allowed by code), a separate copper or aluminum grounding wire may be pulled through the EMT as an additional ground path.
- Continuity Testing
After installation, verify electrical continuity from end to end using a multimeter or continuity tester.
This ensures that all connections are conductive and secure.
Under NEC 250.118(4), EMT qualifies as an equipment grounding conductor only when properly connected with listed fittings and not subject to physical damage or corrosion that would impair its integrity.
How to Connect EMT Conduit Tubing?
- Cut the Conduit
Measure and cut the EMT conduit to the needed length using a tubing cutter or hacksaw. - Ream the Ends
After cutting, smooth out the inside and outside edges with a reaming tool or file. This prevents damage to wires. - Choose the Right Fittings
Use listed EMT connectors (to connect conduit to boxes) and couplings (to join two pieces of conduit).
Set-screw fittings are common for dry areas.
Compression fittings are better for wet or outdoor locations.
- Install the Fittings
Push the conduit into the fitting fully, then tighten the screws or compression nut.
When attaching to a box, insert the connector through the box knockout and tighten the locknut inside the box.
5. Ensure Grounding
Make sure all fittings are tight and secure so the conduit maintains electrical continuity. EMT can act as the ground path if installed properly.
- Support the Conduit
Use straps or hangers to support the conduit within 3 feet of a box and every 10 feet along its run, as required by code.
What is the difference between an EMT and a rigid conduit?
The main differences between EMT and rigid conduit (RMC – Rigid Metal Conduit) lies in follow aspects:
1. Wall Thickness and Strength
EMT is thinner and lighter. It’s often called “thin-wall” conduit.
Rigid conduit (also known as RMC – Rigid Metal Conduit) has much thicker walls, offering superior mechanical protection and durability.
2. Threading
EMT is not threaded. It’s connected using set-screw or compression fittings.
Rigid conduit is threaded on the ends and uses threaded fittings and locknuts.
3. Flexibility and Weight
EMT is easier to bend and handle due to its lighter weight.
Rigid conduit is much heavier and harder to bend—usually requiring special tools or prefabricated bends.
4. Applications
EMT is ideal for indoor use in commercial and residential buildings where mechanical protection is needed but weight and cost are concerns.
Rigid conduit is used for harsh environments, underground installations, and outdoor exposure, offering maximum protection against impact and corrosion.
5. Cost
EMT is generally more cost-effective and easier to install.
Rigid conduit is more expensive due to its strength and additional protection features.