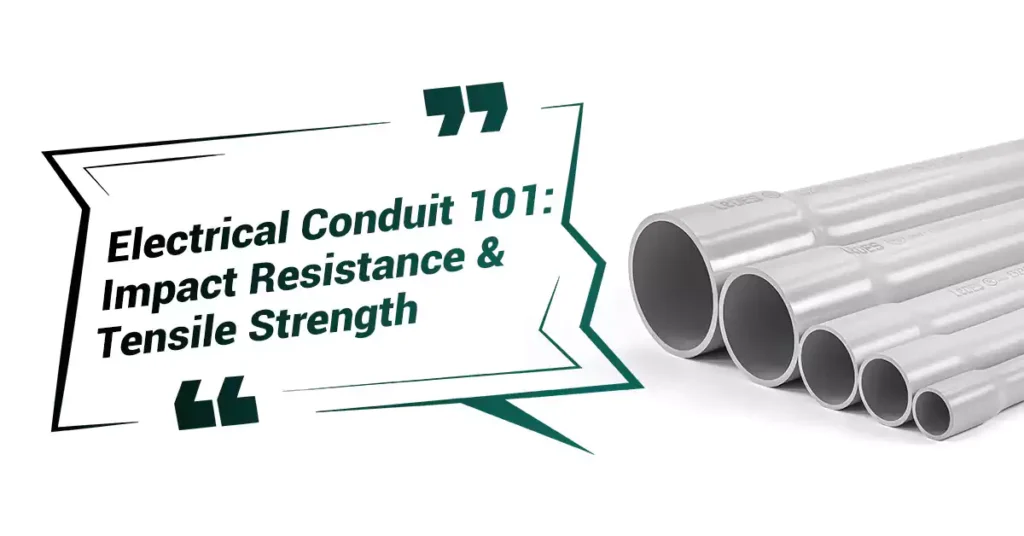
Table des matières
Les systèmes de conduits électriques jouent un rôle crucial pour abriter et protéger en toute sécurité les câbles électriques dans diverses installations, qu'elles soient résidentielles, commerciales ou industrielles. Lors de la conception et de la mise en œuvre de ces systèmes, deux facteurs importants sont à prendre en compte : la résistance aux chocs et la résistance à la traction. Ces propriétés déterminent la capacité du conduit à résister aux forces externes et à maintenir son intégrité structurelle, garantissant ainsi performance et sécurité à long terme.
Afin de garantir des performances constantes et fiables, plusieurs normes ont été établies pour évaluer la résistance aux chocs et à la traction des conduits électriques. Parmi ces normes, UL651, CSA C22.2 NO.211.2, UL1653 et AS/NZS 2053 sont largement reconnues et respectées dans l'industrie. Dans cet article, nous nous concentrerons sur les exigences spécifiées dans UL651, CSA C22.2 NO.211.2, UL1653 et aborderons la norme AS/NZS 2053, notamment concernant les conduits rigides en PVC et les tubes non métalliques ou ondulés.
La résistance aux chocs et à la traction est un critère essentiel dans les systèmes de conduits électriques. Elle garantit leur résistance aux forces externes et aux conditions environnementales, protégeant ainsi le câblage électrique et minimisant les risques de pannes ou d'accidents électriques. Examinons ces propriétés plus en détail et les normes qui les régissent.
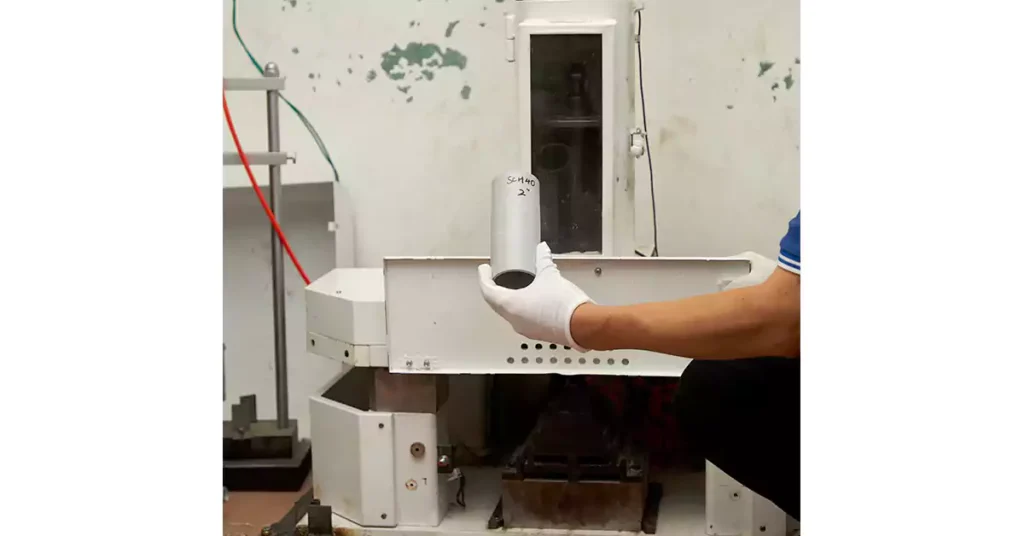
La résistance aux chocs désigne la capacité des systèmes de conduits électriques à supporter des impacts physiques sans subir de dommages ni compromettre leur intégrité structurelle. Il s'agit d'une propriété essentielle qui garantit que le conduit protège le câblage électrique qu'il contient des forces externes et des conditions environnementales.
La norme UL651, établi par Underwriters Laboratories, joue un rôle important dans l'évaluation de la résistance aux chocs des conduits rigides en PVC. UL est un organisme scientifique indépendant de sécurité reconnu mondialement, qui établit des normes rigoureuses pour divers produits et composants électriques. Largement reconnu dans les pays américains.
La norme UL651 définit les procédures et exigences d'essai pour évaluer la résistance aux chocs des conduits rigides en PVC. Cette norme spécifie les niveaux d'énergie d'impact maximaux que le conduit doit supporter sans se fissurer, se fracturer ou subir de dommages importants. Cela garantit que le conduit peut supporter un contact accidentel, des impacts mineurs lors de l'installation ou des facteurs externes sans compromettre ses capacités de protection.
Après avoir testé dix échantillons de conduits, pas plus de 3 échantillons ne devraient présenter de fissures de plus de 0,8 mm sur la surface du conduit.
« Dix spécimens de 6 pouces (150 mm) sans fissures, déchirures ou autres imperfections doivent être découpés
Longueurs finies de conduits rigides en PVC de chaque taille commerciale. Les échantillons doivent être conditionnés à l'air à une température de 23,0 ± 2,0 °C (73,4 ± 3,6 °F) pendant au moins 4 heures avant d'être testés. Les échantillons doivent être testés séparément, dans les 15 secondes suivant le conditionnement, en les reposant sur une plaque d'acier solide et plane d'au moins 13 mm (1/2 po) d'épaisseur, solidement ancrée, sa surface supérieure étant horizontale. Une cage de protection doit entourer les plaques et l'échantillon afin de réduire les risques de blessures causées par des morceaux de conduit brisés en cas de rupture du conduit. Un poids en acier, en forme de cylindre plein de révolution droite, avec une face d'impact plane et des bords arrondis, doit tomber librement à travers un guide vertical depuis la hauteur indiquée au tableau 6.2. Pour les conduits rigides en PVC de type A et EB de type Schedule 40, le poids doit être de 9,1 kg (20 lb) et le cylindre doit avoir un diamètre de 51 mm (2 po). Pour les conduits de type Schedule 80, le poids doit être de 34 kg (75 lb) et le cylindre doit avoir un diamètre de 150 mm (6 po). La face plate du poids doit frapper le centre de l'échantillon sur le diamètre et le long de l'axe longitudinal une fois.
(des dispositions doivent être prises pour éviter que le poids ne frappe l'échantillon plus d'une fois). — Cité de la huitième édition de UL651.
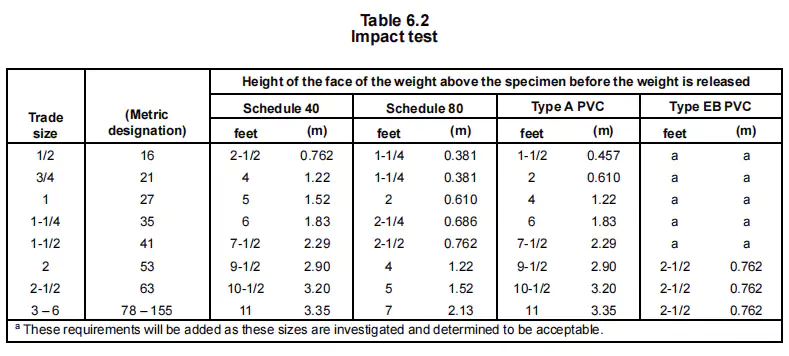
L'Association canadienne de normalisation (CSA) et sa norme CSA C22.2 NO.211.2 jouent également un rôle crucial dans l'évaluation de la résistance aux chocs des conduits rigides en PVC. La CSA est un organisme de renommée internationale qui élabore des normes pour une vaste gamme de produits et de systèmes électriques.
Après avoir testé 10 échantillons de conduits, pas plus de 2 échantillons ne doivent présenter de fissures ou de ruptures à l’intérieur ou à l’extérieur du conduit.
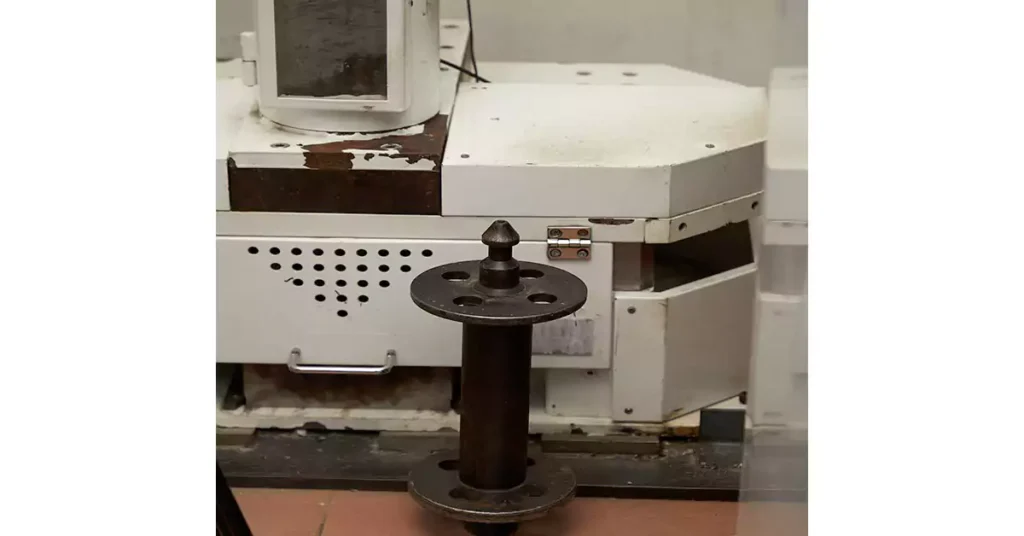
Dix échantillons de conduits doivent être conditionnés à -34 ± 2 °C avec des morceaux de bois dans une chambre froide pendant 4 heures. Après conditionnement, une force de 12 J est appliquée à l'aide d'un marteau en acier à -34 ± 2 °C. Chaque échantillon est soumis à un seul coup de marteau. — Se référant aux normes CSA C22.2 No.211.0 et CSA C22.2 No.211.2
La norme UL1653 est une autre norme importante établie par Underwriters Laboratories. La norme UL651 couvre principalement les conduits rigides en PVC. La norme UL1653 est la norme pour les tubes électriques non métalliques. Les normes UL1653 et CSA C22.2 No.227.1 partagent les mêmes tests et exigences pour les tubes non métalliques, avec seulement de légères différences dans certains tests spécifiques.
Après avoir testé dix échantillons de tubes, pas plus de 2 échantillons ne devraient présenter de fissures, d'éclats ou de ruptures à l'intérieur et à l'extérieur des échantillons.
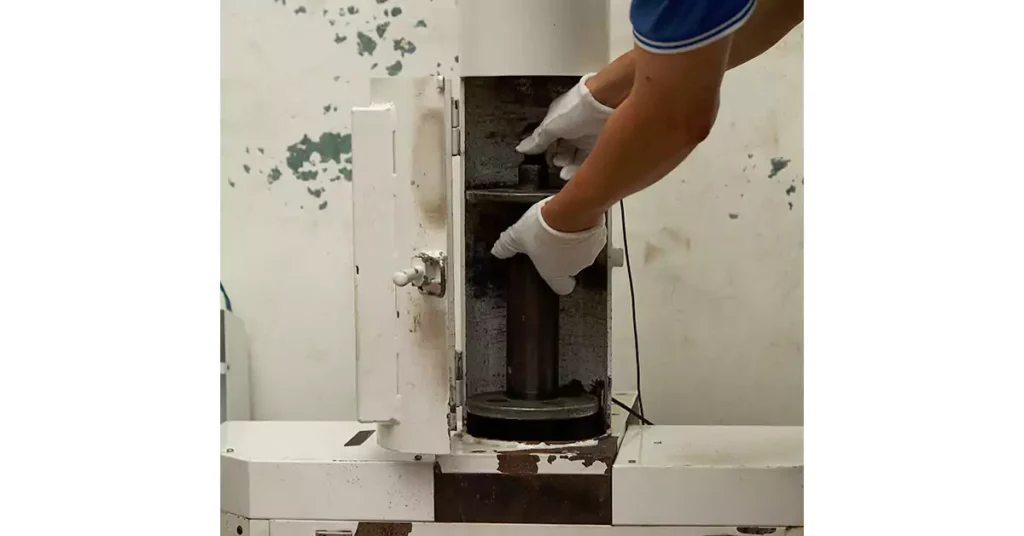
Conditionner 10 échantillons dans une chambre froide à une température de -20 ± 1 °C pendant au moins 4 heures. Les soumettre ensuite à un impact (2,7 J) dans les 15 secondes suivant leur retrait de la chambre avec une plaque plane en acier ou en aluminium. — Se référant à la deuxième édition de la norme UL1653
La norme spécifie également les exigences relatives aux échantillons et aux plaques, y compris les longueurs et les épaisseurs.
AS/NZS2053 Il s'agit d'une norme clé utilisée en Australie et en Nouvelle-Zélande pour évaluer la qualité et la sécurité des conduits en PVC. Elle définit les paramètres d'énergie d'impact et évalue les performances des conduits dans des conditions spécifiques.
Après avoir testé 12 échantillons, pas plus de 3 échantillons ne devraient présenter de signe de désintégration ou de fissures.
Deux chambres de conditionnement, un appareil d'impact, un tampon en caoutchouc spongieux.
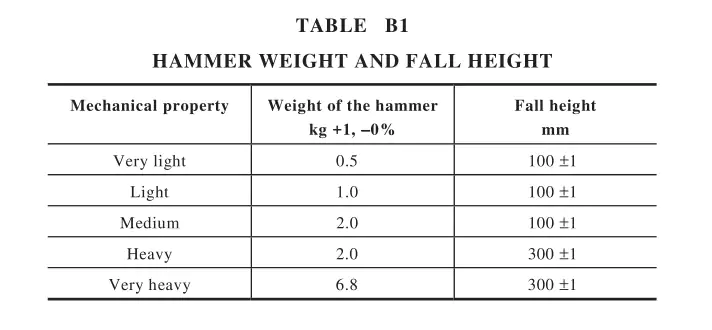
« (a) Placer une éprouvette dans la chambre de conditionnement 1, à la température de service permanente maximale
température spécifiée par le fabricant (avec une tolérance de ±2°C), pendant 240 h.
(b) Placer l'appareil d'essai d'impact sur le tampon de caoutchouc spongieux en conditionnement
Chambre 2. Placez également l’éprouvette dans la chambre de conditionnement 2.
(c) Maintenir la température dans la chambre de conditionnement 2 à la température la plus basse de l'installation
température spécifiée par le fabricant (avec une tolérance de ±2°C).
(d) Lorsque l'éprouvette atteint la température de l'air dans la chambre de conditionnement 2,
ou après 2 h, selon la période la plus longue, placez l'éprouvette sur la base en acier.
(e) Posez la pièce intermédiaire en acier sur l’éprouvette.
(f) Réglez le poids du marteau et la hauteur de chute conformément au tableau B1 et
puis laissez tomber le marteau sur l'éprouvette. Pour les raccords, l'essai est effectué sur la partie la plus faible.
partie du raccord de conduit, sauf qu'il n'est pas appliqué à moins de 5 mm d'une douille
bouche.
(g) En utilisant une vision normale ou corrigée, sans grossissement, examinez l'éprouvette pour
fissures ou désintégration. » — Cité dans AS/NZS 2053.1:2001
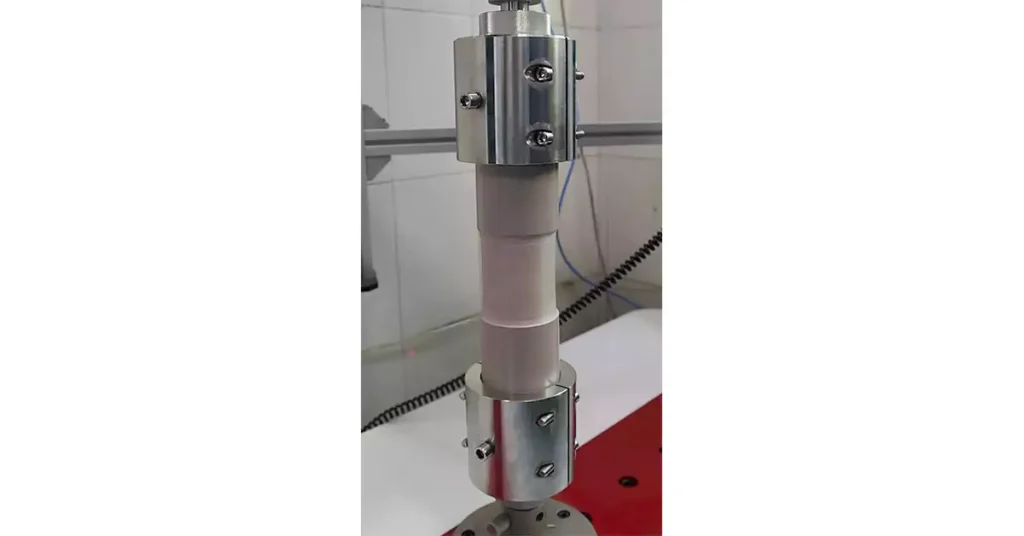
La résistance à la traction désigne la contrainte de traction maximale qu'un matériau peut supporter avant de se rompre ou de subir une déformation permanente. Dans le contexte des systèmes de conduits électriques, la résistance à la traction mesure la capacité du conduit à résister aux forces de traction sans rupture ni dégradation structurelle.
Six échantillons de conduits rigides en PVC, trois vieillis, trois non vieillis, après avoir été soumis à un essai de traction, la résistance à la traction moyenne des trois échantillons vieillis doit être égale ou supérieure à 95 pour cent de la résistance à la traction moyenne des trois échantillons non vieillis.
« Préparez les six échantillons conformément aux exigences standard, y compris la taille, la longueur et la forme du conduit.
Placer trois éprouvettes dans une étuve à 113,0 ± 1,0 °C pendant 168 heures. Retirer ensuite les éprouvettes et les refroidir à l'air libre à une température de 23,0 ± 2,0 °C pendant 16 à 96 heures. Tester ensuite les six éprouvettes successivement à l'aide d'une machine de traction. Pour les exigences spécifiques à la machine de traction et au mode opératoire, se référer à la norme.
La résistance à la traction effectuée sur les échantillons ne doit pas être inférieure à 5 000 psi pour les conduits en PVC rigide de série 40 et de série 80.
Calcul de la résistance à la traction également spécifié dans la norme. » — Se référant à la norme UL651, huitième édition.
Après que les échantillons aient résisté pendant une période d'1 minute, le tube électrique non métallique ne devrait pas se casser.
Français « Préparer six échantillons. Pour les tailles commerciales 16 (1/2) et 21 (3/4), une masse de 90 kg (200 lb) reposant sur le sol doit être fixée à une extrémité de l'ENT et doit être utilisée pour créer une force de tension de 889 N (200 lbf) en soulevant la masse du sol en tirant sur l'autre extrémité de l'ENT et en maintenant la charge pendant 1 min. De même, pour les tailles commerciales 27 (1) et plus, une masse de 1,35 kg (300 lb) reposant sur le sol doit être fixée à une extrémité de l'ENT et doit être utilisée pour créer une force de tension de 1,334 N (300 lbf) en soulevant la masse du sol en tirant sur l'autre extrémité de l'ENT et en maintenant la charge pendant 1 min.
La pince de la machine d'essai doit être desserrée à une vitesse de 50 à 75 mm/min (2 à 3 po/min) jusqu'à ce que l'échantillon atteigne la charge spécifiée ci-dessus pour chaque taille commerciale. Ce niveau de tension doit être maintenu pendant 1 min. — Cité et référencé de UL1653, clause 7.8.
Les conduits sont un élément important de l'installation électrique, car ils garantissent la sécurité de l'ensemble du système électrique et du personnel. Par conséquent, leur qualité et leur performance sont cruciales.
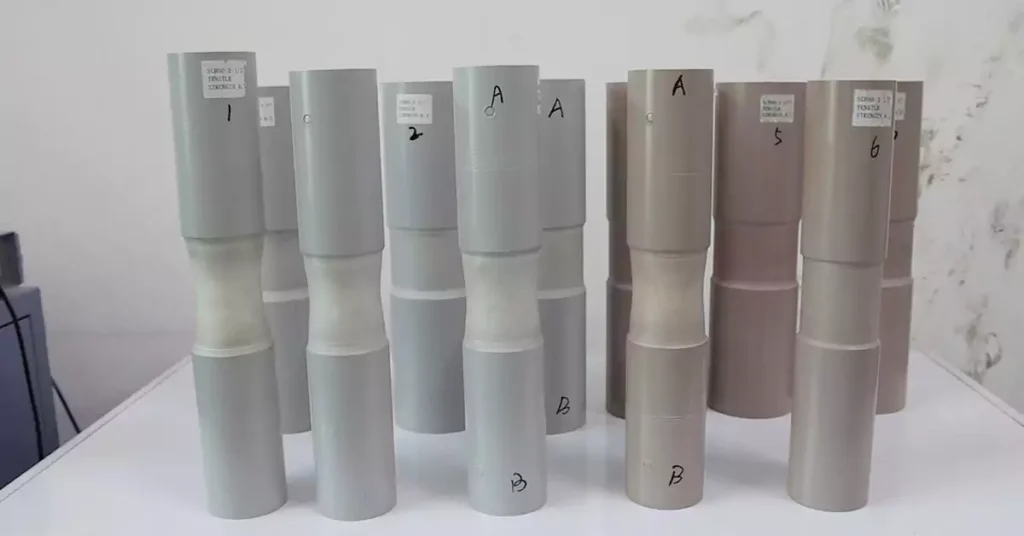
Après la production de systèmes de conduits électriques, il est essentiel pour les fabricants d'effectuer des auto-tests afin de garantir la conformité des produits aux normes et spécifications requises. Ces auto-tests constituent un contrôle qualité permettant de vérifier que les systèmes de conduits présentent la résistance aux chocs et à la traction requise.
Grâce à des tests rigoureux, les fabricants peuvent identifier tout problème ou défaut potentiel dans les systèmes de conduits avant qu'ils n'atteignent les utilisateurs finaux. Cette approche proactive contribue à maintenir la sécurité et la fiabilité des installations électriques, tout en minimisant le risque d'utilisation de systèmes de conduits non conformes ou de qualité inférieure.
L'auto-test peut impliquer de soumettre le conduit à divers tests, notamment des évaluations de résistance aux chocs et à la traction, conformément aux normes applicables telles que UL651, CSA C22.2 NO.211.2 et UL1653. Les fabricants peuvent utiliser des équipements et des procédures de test spécialisés pour simuler les conditions réelles et garantir que les systèmes de conduits répondent aux critères de performance requis.
La longévité des systèmes de conduits électriques sur le terrain dépend de plusieurs facteurs. Comprendre et prendre en compte ces facteurs est essentiel pour garantir la sécurité et la fiabilité à long terme des installations.
Facteurs environnementaux: Les systèmes de conduits sont exposés à diverses conditions environnementales, telles que les variations de température, l'humidité, les rayons UV et l'exposition aux produits chimiques. Ces facteurs peuvent dégrader les matériaux au fil du temps, affectant ainsi la résistance aux chocs et à la traction du conduit. Un choix judicieux de matériaux offrant une résistance adéquate aux facteurs environnementaux peut contribuer à une meilleure longévité.
Contraintes mécaniques : Sur le terrain, les systèmes de conduits peuvent être soumis à des contraintes mécaniques dues à des facteurs tels que les vibrations, les mouvements ou les chocs accidentels. Ces contraintes peuvent progressivement fragiliser le conduit ou l'endommager si elles ne sont pas correctement gérées. Un support adéquat, une fixation solide et un acheminement approprié peuvent contribuer à minimiser l'impact des contraintes mécaniques et à prolonger la durée de vie des systèmes de conduits.
Qualité d'installation : La qualité de l'installation joue un rôle essentiel dans la longévité des systèmes de conduits électriques. Des pratiques d'installation inappropriées, telles qu'un rayon de courbure inadéquat, une fixation insuffisante ou une mauvaise étanchéité, peuvent compromettre l'intégrité et les performances des conduits. Le respect des directives du fabricant et des meilleures pratiques de l'industrie lors de l'installation garantit une installation correcte des systèmes de conduits, réduisant ainsi le risque de défaillances prématurées.
Entretien et inspections : Un entretien et des inspections réguliers sont essentiels pour identifier tout problème ou signe de détérioration des systèmes de conduits. Des inspections périodiques peuvent aider à détecter les signes avant-coureurs de dommages ou de dégradation, permettant ainsi des réparations ou des remplacements rapides. La mise en place d'un programme d'entretien et la réalisation d'inspections conformes aux normes de l'industrie peuvent contribuer significativement à la longévité et à la fiabilité des systèmes de conduits.
Des pratiques d'installation appropriées sont primordiales pour garantir la sécurité, la performance et la longévité des systèmes de conduits électriques. Il est essentiel de respecter les pratiques d'installation suivantes :
- Conformité aux normes : Les installateurs doivent respecter les normes en vigueur, telles que les codes électriques locaux et les directives du fabricant, pour garantir une installation correcte. Ces normes précisent les spécifications relatives au dimensionnement, au routage, à la fixation, au collage, à l'étanchéité et à d'autres aspects critiques des conduits.
- Sélection de conduits appropriés : Le choix du matériau et du type de conduit adapté à l'application est crucial. Des facteurs tels que l'environnement, les contraintes mécaniques prévues et les exigences électriques doivent être pris en compte lors du processus de sélection.
- Rayons de courbure adéquats : Les coudes des conduits doivent respecter des rayons de courbure appropriés afin d'éviter tout vrillage ou contrainte excessive. Le respect des rayons de courbure recommandés par le fabricant contribue à préserver l'intégrité structurelle du conduit et à prévenir les problèmes de performance.
- Fixation sécurisée : Les systèmes de conduits doivent être solidement fixés pour éviter tout mouvement, vibration ou déplacement. L'utilisation appropriée de supports, de colliers, de supports et d'autres méthodes de fixation garantit le maintien du conduit en place en fonctionnement normal et sous l'effet de forces externes.
- Étanchéité efficace : Selon l'application et les conditions environnementales, une étanchéité adéquate peut être nécessaire pour protéger le câblage de l'humidité, de la poussière et d'autres contaminants. L'utilisation de méthodes d'étanchéité appropriées, telles que des joints, des raccords ou des produits d'étanchéité, contribue à préserver l'intégrité du système de conduits.
- Installation professionnelle : Il est essentiel de faire appel à des professionnels qualifiés et expérimentés pour l'installation de conduits. Les installateurs professionnels possèdent les connaissances et l'expertise nécessaires pour garantir des pratiques d'installation appropriées, minimisant ainsi les risques d'erreurs ou d'oublis.
- En adhérant à des pratiques d’installation appropriées, les installateurs peuvent améliorer la sécurité et la fiabilité des systèmes de conduits électriques, maximisant leur longévité et minimisant le risque de pannes ou de problèmes de performances.
Lors de l'achat de conduits électriques pour vos installations, il est essentiel de privilégier les produits certifiés par des normes telles que UL, CSA et AS/NZS. L'achat de conduits certifiés offre plusieurs avantages importants :
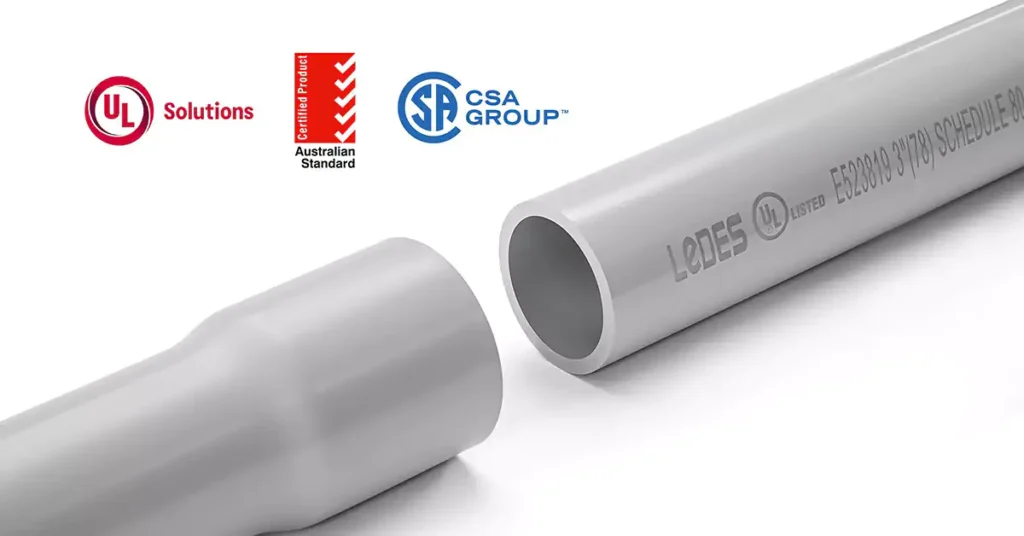
- Assurance de la qualité et de la performance :
Les conduits certifiés selon des normes reconnues garantissent que le produit a été soumis à des tests et évaluations rigoureux pour répondre à des exigences spécifiques. Ces certifications constituent un gage de qualité et garantissent que le conduit possède la résistance aux chocs et à la traction nécessaires à une performance fiable.
Les conduits certifiés sont soumis à des tests complets pour valider leur intégrité structurelle et leur capacité à résister aux forces de traction, aux impacts et autres contraintes. En achetant des conduits certifiés, vous avez confiance en leur qualité et leurs performances, réduisant ainsi les risques de défaillances prématurées et de risques pour la sécurité.
- Conformité aux exigences réglementaires :
Les installations électriques sont soumises à diverses exigences réglementaires et codes visant à garantir la sécurité et la fiabilité. L'achat de conduits certifiés selon des normes reconnues permet de garantir la conformité à ces réglementations.
Les conduits certifiés ont été testés et évalués selon des critères reconnus par l'industrie, conformément aux exigences des organismes de réglementation. Cette conformité réduit les risques de non-conformité lors des inspections ou des audits, ce qui permet de gagner du temps et d'éviter des reprises coûteuses.
- Sécurité renforcée pour le personnel et les équipements :
Les systèmes de conduits électriques jouent un rôle crucial dans la protection du câblage électrique et la prévention des risques tels que les chocs électriques, les incendies et les dommages matériels. La certification des conduits met l'accent sur la sécurité, garantissant que le produit est conçu et fabriqué conformément aux exigences de sécurité les plus strictes.
Les conduits certifiés sont soumis à des tests pour vérifier leur résistance aux chocs, aux forces de traction et autres contraintes mécaniques. Cette validation contribue à la protection du personnel et des équipements en réduisant le risque de défaillance des conduits, susceptible d'entraîner des défauts électriques, des courts-circuits ou une dégradation de l'isolation.
- Fiabilité à long terme et économies de coûts :
Investir dans des conduits certifiés se traduit par une fiabilité à long terme et des économies. Les produits certifiés sont conçus pour résister aux contraintes environnementales, aux contraintes mécaniques et aux exigences d'installation.
En achetant des conduits répondant aux exigences de résistance aux chocs et à la traction, vous avez confiance en leur durabilité et leur longévité. Cela réduit les coûts de réparation, de remplacement et d'entretien, et permet ainsi de gagner du temps et de l'argent sur la durée de vie de l'installation électrique.
- Confiance dans l'intégrité du fabricant :
Choisir des conduits certifiés selon des normes reconnues témoigne également de l'engagement du fabricant envers la qualité et l'intégrité. Les fabricants qui soumettent leurs produits à des tests et à une certification démontrent leur engagement à produire des systèmes de conduits fiables et sûrs.
En achetant des conduits auprès de fabricants réputés qui adhèrent aux normes de l’industrie, vous pouvez avoir confiance dans l’intégrité du produit et dans l’engagement du fabricant à fournir des solutions de haute qualité.
En conclusion, la compréhension des propriétés mécaniques des systèmes de conduits électriques est essentielle pour garantir la sécurité et la performance des installations électriques. La résistance aux chocs et à la traction des conduits joue un rôle essentiel dans la protection du câblage, la réduction des risques de défauts électriques et le maintien de l'intégrité de l'ensemble du système.
L'importance des propriétés mécaniques des conduits est indéniable. Prendre en compte ces propriétés, privilégier le choix des conduits et privilégier les produits certifiés sont des étapes essentielles pour garantir la sécurité, la fiabilité et la performance à long terme des installations électriques. En comprenant les exigences de résistance aux chocs et à la traction et en suivant les meilleures pratiques, les électriciens peuvent créer des installations répondant aux normes de sécurité et d'efficacité les plus strictes.
Des questions ou des exigences concernant les conduits électriques certifiés, Contactez-nous à tout moment.
Norme UL 651 Huitième édition de UL Solutions
Norme UL1653 Deuxième édition de UL Solutions
CSA C22.2 No.211.0 et CSA C22.2 No.211.2 du Groupe CSA
Norme AS/NZS 2053.1:2001 des normes australiennes