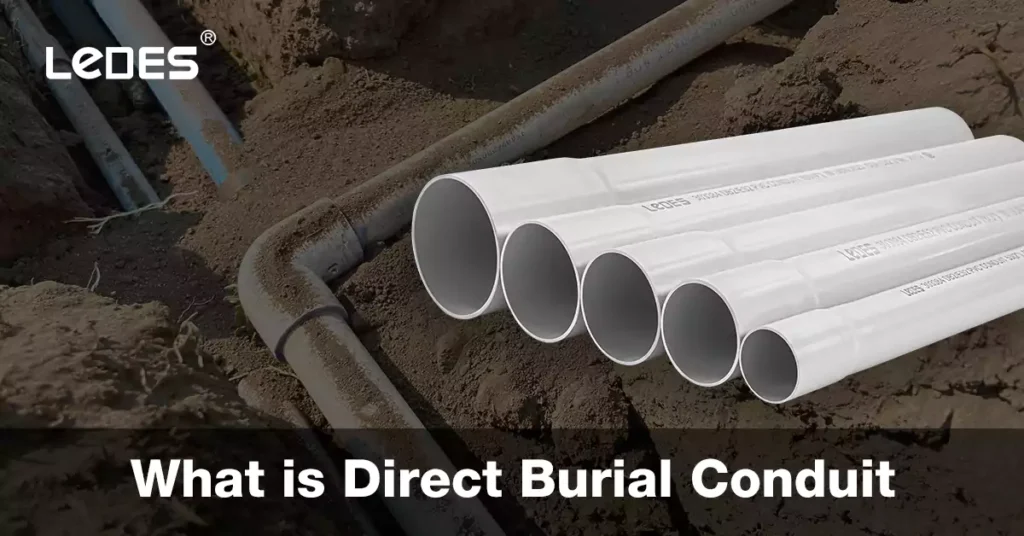
Table of Contents
Direct burial conduit refers to a type of piping or conduit system that is designed and installed underground without the need for additional protection or encasement. It is commonly used for electrical, telecommunications, or data communication applications where cables or wires need to be routed underground.
Direct burial conduit is typically made of durable materials such as high-density polyethylene (HDPE) or rigid PVC (polyvinyl chloride), which provide protection against moisture, soil acidity, and other environmental factors. The conduit is designed to resist corrosion, impact, and crushing, ensuring the integrity of the cables or wires it houses.
There are many types of direct burial conduits on the market and are comply to different standards, here are some commonly used types and the compliance codes.
EB-20 Duct
EB-20 Duct, also known as Type EB-20 conduit, is a specific type of rigid PVC (polyvinyl chloride) pipe that is designed for underground burial applications when encased in concrete. It is commonly used in electrical and communication installations where cables need to be protected and routed between buildings or structures. And the number “20” represents the approximate internal diameter of the conduit in inches. The nominal size of the conduit is used as a standardized reference for identification and compatibility with fittings, connectors, and other components in the conduit system.
Complied Standards
ASTM D1784: This standard specifies the requirements for PVC compounds used in the manufacture of plastic pipes and fittings. It ensures that the PVC material used in EB20 conduit meets the necessary quality and performance criteria.
ASTM F-512: This standard focuses on the requirements for conduits and associated fittings used in underground electrical systems. It covers the dimensions, performance, and testing methods for PVC conduit systems, including EB20 conduit.
NEMA TC 6: The National Electrical Manufacturers Association (NEMA) Technical Committee 6 creates standards for electrical conduit systems. NEMA TC 6 covers PVC conduit, including burial encased in concrete. It defines the requirements for materials, dimensions, performance, and installation procedures.
NEMA TC 8: NEMA TC 8 provides standards for nonmetallic underground conduit with conductors. It includes specifications for PVC conduit systems used in buried applications, such as EB20 conduit.
The standards listed outline various requirements for EB20 conduit, including;
- Material Properties: The standards specify the type of PVC compound that should be used, ensuring it meets specific performance characteristics such as impact resistance, flexibility, and resistance to chemicals and UV radiation.
- Dimensions: The standards define the acceptable sizes and dimensions of EB20 conduit to ensure compatibility with fittings, connectors, and other components of the conduit system.
- Performance: The standards outline performance requirements, such as the ability of the conduit to withstand specified temperatures, pressures, and external forces. This includes factors like crush resistance, impact resistance, and resistance to environmental factors.
- Testing Methods: The standards provide testing procedures and protocols to evaluate the performance and quality of EB20 conduit. These tests may include physical and mechanical tests to assess properties like tensile strength, flexibility, and impact resistance.
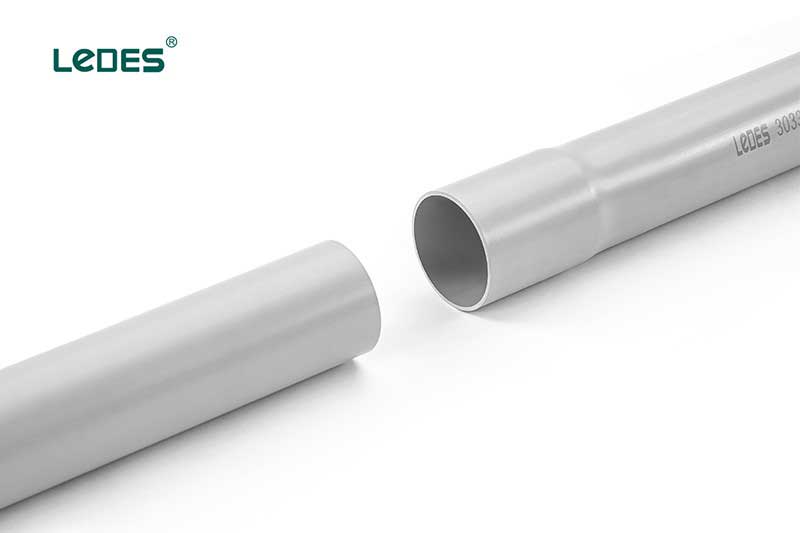
EB-35 Duct
EB-35 duct is a specific type of conduit that is specifically designed for power and communications applications. It is suitable for both direct burial and concrete encased installations. The conduit is available in 20-foot lengths in five different sizes (diameters), while 10-foot lengths are available only in a 5-inch diameter.
Compliance Code
ASTM D1784 ASTM F-512 NEMA TC 6&8. These standards ensure that the conduit meets the necessary requirements for materials, dimensions, performance, and installation procedures.
DB-60 Duct
DB-60 duct is a type of conduit or duct specifically designed for underground burials and encasement in concrete. It is commonly used in electrical and communication installations to protect and route cables between structures or buildings.
DB-60 PVC duct is made from high-quality PVC (polyvinyl chloride) material, which offers excellent durability, corrosion resistance, and moisture protection. The “DB-60” designation indicates its specific characteristics and suitability for underground applications.
Compliance Code
ASTM D1784 ASTM F-512 NEMA TC 6&8.
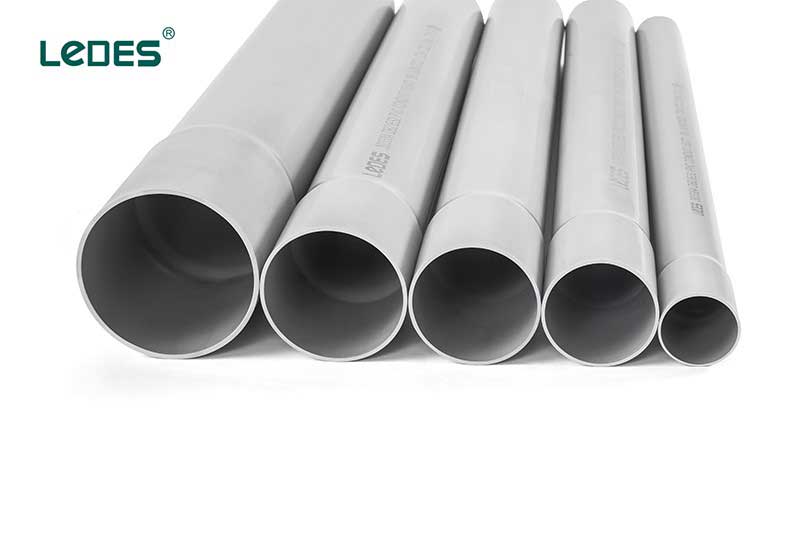
DB-100 Duct
The DB-100 nonmetallic Power & Communication Duct, also known as Type DB, is produced in accordance with NEMA Standard TC-6 & 8 and adheres to the specific requirements set by the State of California. It is specifically engineered for applications involving direct burial or installation within concrete encasements.
Compliance Code
ASTM D1784 ASTM F-512 NEMA TC 6&8.
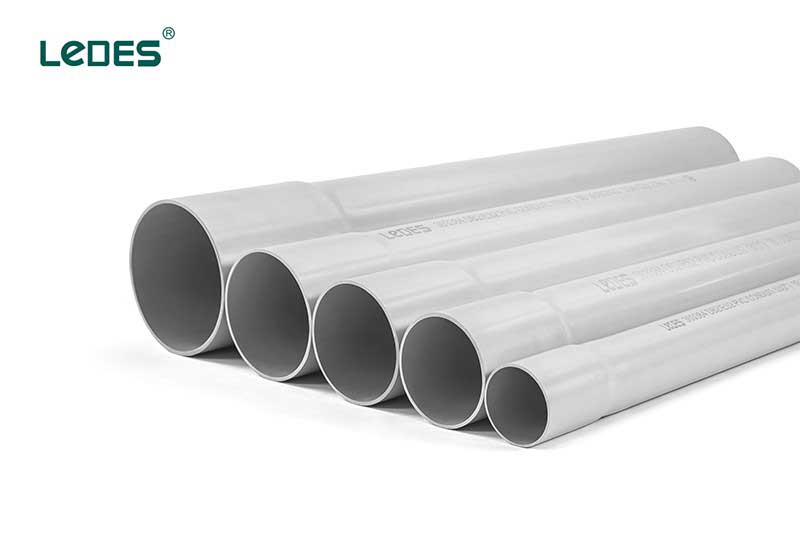
DB-120 Duct
DB120 Duct is a type of rigid, extra heavy wall, non-metallic conduit made from polyvinyl chloride (PVC). It is specifically designed for direct burial or concrete encased installations, providing a reliable and durable solution for routing power and communication cables underground.
Compliance Code
ASTM D1784 ASTM F-512 NEMA TC 6&8.
DB2 Duct
DB2 communication duct refers to a specific type of duct used for communication purposes. It is typically a nonmetallic duct designed to house and protect communication cables, such as fiber optic cables or Ethernet cables. Ledes DB2 duct is made of PVC, certifed by CSA C22.2 No.211.1, and is commonly used in various industries, including telecommunications, networking, and data centers, to provide a conduit for the efficient and organized installation of communication cables.
Compliance Code
CSA C22.2 No. 211.1
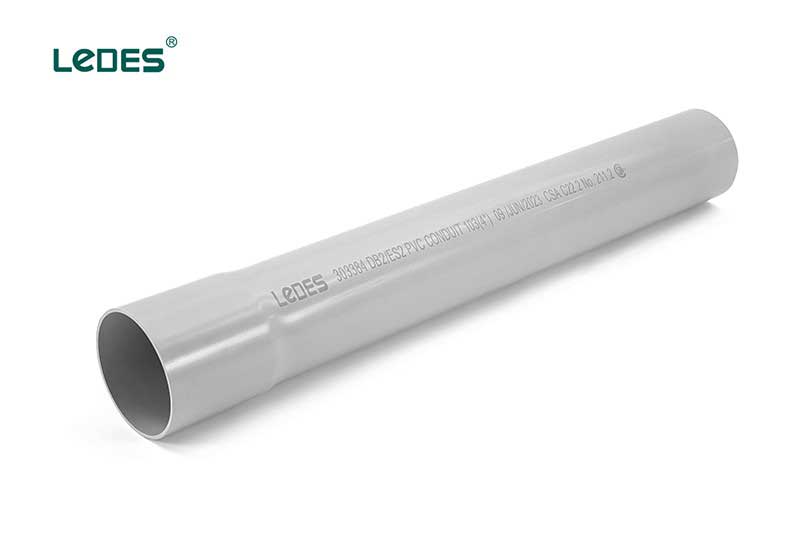
Buried Depth
The depth at which DB duct should be buried can vary depending on various factors, including local regulations, specific project requirements, and the type of installation. However, there are some general guidelines to consider:
Local Regulations: Check the local building codes and regulations in your area. They often specify the minimum burial depth for different types of ducts and utilities.
Environmental Factors: Consider factors such as frost depth, soil type, and ground conditions. These factors can affect the stability and protection of the duct. In regions with freezing temperatures, it is common to bury ducts below the frost line to prevent damage.
Protection and Accessibility: The duct should be buried at a depth that provides adequate protection from external elements, such as excavation, traffic, and environmental factors. Additionally, it should be buried at a depth that allows for easy maintenance and accessibility if needed.
As a general guideline, nonmetallic communication ducts like DB ducts are often buried at a depth of 18 to 24 inches (45 to 60 centimeters). However, it is crucial to consult with local authorities and professionals familiar with the specific project and local regulations to determine the appropriate burial depth for DB duct in your specific location.
Considerations for Direct Burial Conduit in Construction
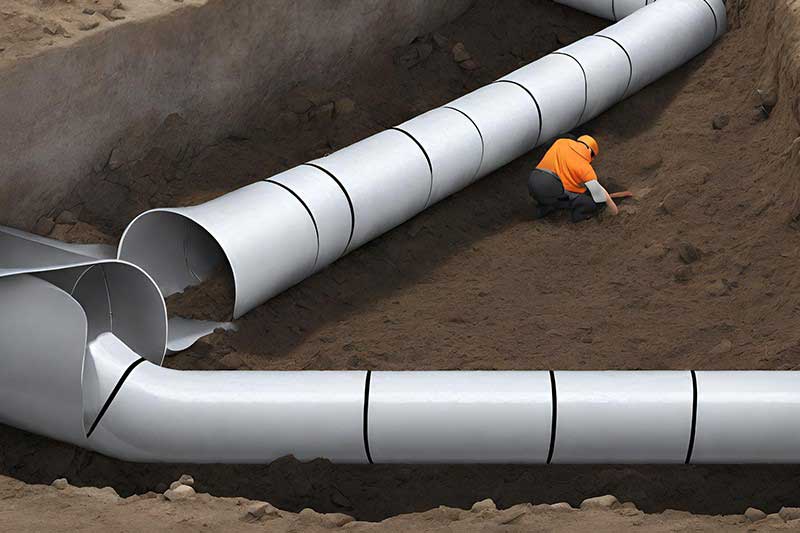
When incorporating direct burial cable and conduit in industrial construction projects, several key considerations should be taken into account:
- Cable and Conduit Selection: Choose cables and conduits that are specifically designed for direct burial applications. They should have appropriate insulation, protection against moisture, and durability to withstand underground conditions. Consider factors such as voltage rating, temperature rating, and the type of cables (e.g., power, communication, fiber optic) required for the project.
- Depth of Burial: Determine the appropriate depth at which the cables and conduits should be buried. Consider factors like local building codes, soil conditions, frost depth, and the potential for excavation or external impact. Burial depth should provide sufficient protection while allowing for future maintenance and accessibility.
- Soil and Environmental Factors: Assess the soil characteristics, including composition, moisture levels, and corrosive properties. Certain soils may require additional measures to protect the cables and conduits from degradation or damage. Consider the impact of environmental factors such as temperature variations, flooding, or seismic activity on the performance and longevity of the installation.
- Protection and Routing: Plan the routing and layout of cables and conduits to minimize the risk of damage during construction or future excavation. Consider using protective measures such as concrete encasement, warning tapes, or markers to enhance visibility and prevent accidental damage.
- Future Expansion and Maintenance: Plan for future expansion and maintenance needs by allowing for additional capacity in the conduit system. Consider the ease of accessing and repairing cables or conduits in case of failure or upgrades. Incorporate provisions for future cable pulls or splices.
- Compliance and Documentation: Adhere to applicable codes, regulations, and industry standards for direct burial installations. Document the installation process, including cable and conduit specifications, burial depths, and any testing or inspection records.
- Price and Labor: During the actual installation and construction process, we have to consider the cost differences caused by different pipes and accessories. According to the relevant content description on Wikipedia, we can see that there are great differences in raw material costs, labor costs, etc. for pipe fittings made of different materials.
Among them, PVC conduit has greater advantages in labor and materials, which is why it is favored by the majority of contractors and contractors.
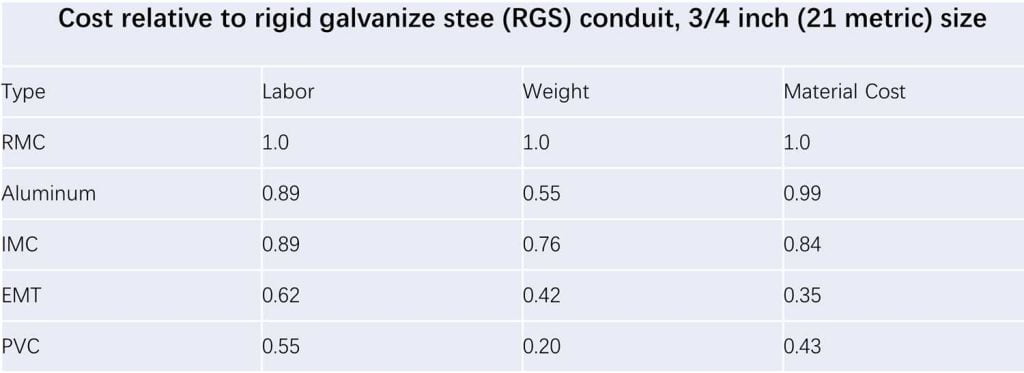
PVC Conduit Materials Price & Labor Cost Vs. Metal Conduit Pipe
DB Direct Burial PVC Duct Installation
- Excavation: Start by digging a trench along the desired pathway for the DB PVC Utility Duct.
- Placement of Duct: Lay rows of DB PVC Utility Duct in the trench, ensuring proper alignment and positioning.
- Cementing and Connection: For each run of DB PVC Utility Duct, cement the belled end of one section to the straight end of the adjacent section. Use a reamer tool to remove any burrs or debris before applying the appropriate PVC Solvent Cement. Apply the cement to the inside of the belled end and the outside of the straight end, then twist the pipe slightly to secure the connection. Repeat this process every 10 to 20 feet, depending on the conduit length.
- Backfill: Once all the runs of DB PVC Utility Duct are properly connected, fill the trench with backfill material. Use smoother select fill dirt as the backfill, ensuring proper compaction to provide stability and support for the duct.
- Termination: Direct the ends of the DB PVC Utility Duct runs into approved electrical devices or boxes, as there are no above-ground applications for Direct Burial PVC Conduit.
- Finishing: Complete the installation by compacting the backfilled material and restoring the surface to its original condition.
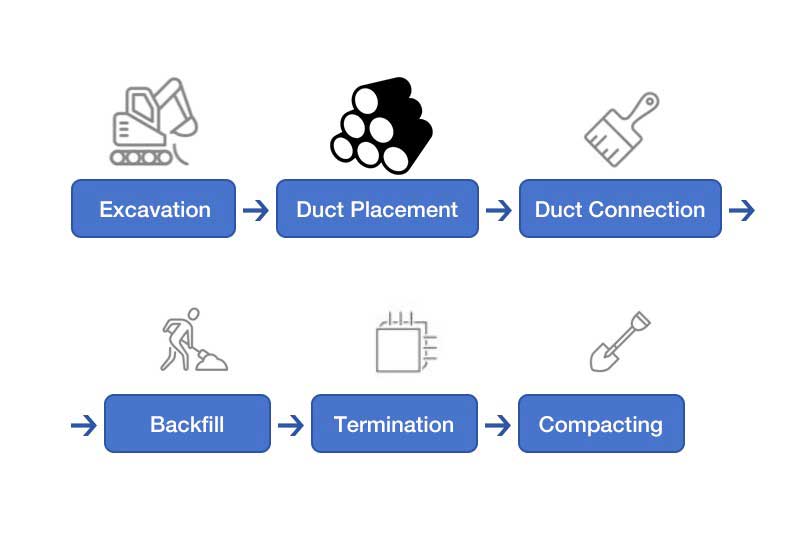
Type DB PVC Conduit Installation Process
EB (Encased Burial) Cement Conduit Installation
- Formwork: Construct formwork or a trench box system to encase the cement conduit.
- Placement: Position the cement conduit within the formwork.
- Spacers: Install appropriate spacers based on NEC requirements for the conduit size and required separation space.
- Cement Pouring: Pour cement or concrete mix into the formwork, completely encasing the conduit.
- Curing: Allow the cement to cure and harden according to the recommended curing time.
- Backfill: Backfill any remaining space around the encased conduit with suitable material.
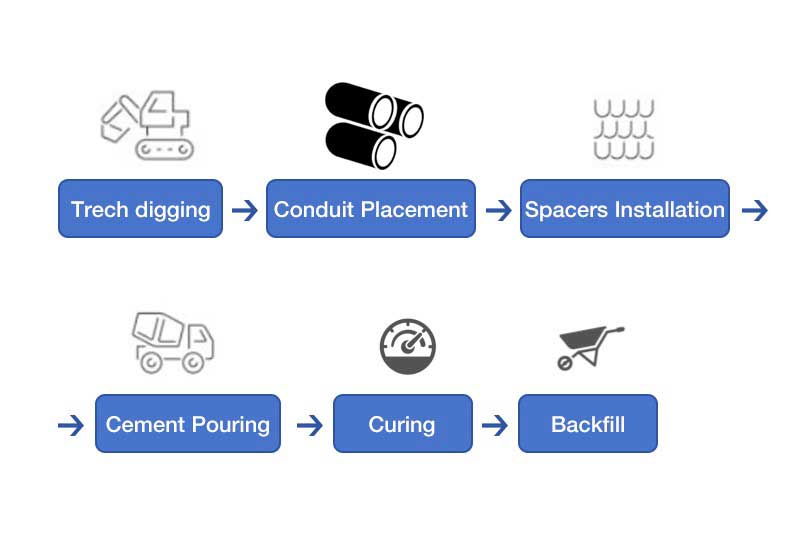
Type EB Cement Conduit Installation Process
It’s crucial to consult the local codes, and regulations specific to your location when installing DB and EB cement conduits. Adhering to manufacturer’s guidelines and seeking professional assistance when necessary will ensure a proper and compliant installation.
What is the disadvantage of underground cables?
While underground cables offer several advantages, there are also some disadvantages associated with their use. Here are some common disadvantages of underground cables:
- Higher Installation Cost: One of the primary drawbacks of underground cables is the higher installation cost compared to overhead cables. Excavation, trenching, and specialized equipment are required for laying the cables underground. These additional expenses can make the initial installation significantly more expensive, especially in areas with complex geographical features or urban environments where extensive underground infrastructure already exists.
- Increased Maintenance and Repair Difficulty: Maintaining and repairing underground cables is more challenging and time-consuming compared to overhead cables. Locating faults in underground cables requires specialized equipment and expertise, and accessing the cables buried beneath the ground can be cumbersome. This difficulty in fault detection and repair can lead to longer downtime and higher maintenance costs.
- Limited Accessibility: Underground cables are less accessible for maintenance and repairs. In densely populated areas or urban environments, accessing underground cables can be particularly challenging due to the presence of buildings, roads, and other infrastructure. This limited accessibility can result in delays and disruptions during maintenance and repair work, further increasing costs and causing inconvenience to service providers and customers.
What are the risks of burying underground cables without conduit?
Burying underground cables without conduit can pose several risks and disadvantages. Here are some of the potential risks associated with not using conduit for underground cable installations:
- Physical Damage: Without conduit protection, underground cables are more susceptible to physical damage from external factors such as rocks, tree roots, construction activities, or accidental digging. Without a protective barrier, the cables are more exposed and vulnerable to potential impacts or compression, which can result in cable insulation damage or conductor breakage.
- Moisture and Water Ingress: Underground environments can be prone to moisture and water infiltration. Without conduit, there is a higher risk of water seepage into the cable system, which can cause insulation degradation, short circuits, and corrosion of conductors or connectors. Moisture ingress can significantly affect the performance and longevity of the cables, leading to service disruptions and costly repairs.
- Chemical Exposure: Underground locations may contain chemicals or substances that can adversely affect cable integrity and performance. Without conduit, the cables are more exposed to potential chemical exposure from soil contaminants, industrial activities, or accidental spills. Chemical interactions can result in cable degradation, insulation breakdown, and overall system failure.
- Difficulty in Cable Replacement or Upgrades: Without conduit, replacing or upgrading underground cables becomes more challenging. The absence of a dedicated pathway can make it difficult to remove and install new cables or make modifications to the existing infrastructure. This limitation can increase the complexity, time, and cost associated with future cable replacements or system upgrades.
- Lack of Cable Identification and Organization: Conduit provides a structured and organized pathway for cables, allowing for easier identification and management. Without conduit, the cables may become tangled or disorganized, making it harder to locate specific cables for maintenance, repairs, or expansions. This can lead to increased downtime and inefficiencies during troubleshooting or system upgrades.
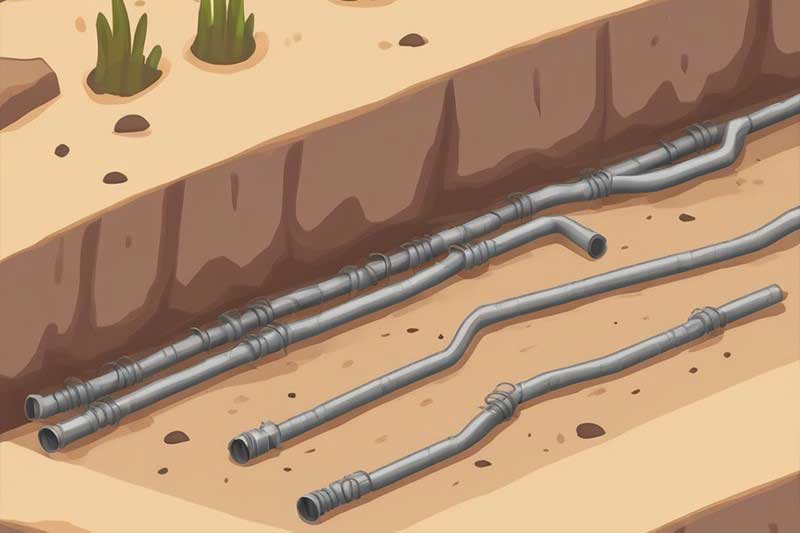
Does a direct burial cable need a conduit?
Direct burial cables do not require a conduit for installation. They are specifically designed to be buried directly in the ground without additional protection. These cables have insulation and jackets that provide resistance to moisture, temperature variations, and physical damage. However, local electrical codes and regulations may have specific requirements, so it’s important to consult them.
While direct burial cables can be installed without conduit, using a conduit may offer additional benefits depending on the specific requirements of the project. Conduit can provide extra physical protection and make cable replacement or maintenance easier. It can also be helpful in challenging environmental conditions or for locating the cable. However, installing a conduit adds cost and complexity to the project.
Ultimately, the decision to use a conduit with direct burial cables depends on factors such as soil conditions, project requirements, and local regulations. Evaluating these aspects and consulting with a professional electrician can help determine the best approach for your specific circumstances.
What is the best conduit for direct burial?
The best conduit for direct burial is commonly recommended to be PVC (Polyvinyl Chloride) due to its durability, stability, and proven performance. PVC conduits have been extensively used and tested for underground installations. They offer several advantages, including:
Sturdiness: PVC conduits are known for their strength and ability to withstand external pressures and impacts. They provide reliable protection for the cables against physical damage from rocks, soil shifting, or other potential hazards.
Moisture Resistance: PVC is highly resistant to moisture and water ingress, making it an ideal choice for underground applications. It helps prevent water from reaching the cables, which can cause insulation degradation or short circuits.
Size Options: PVC conduits are available in various sizes, allowing for flexibility in accommodating different cable diameters or multiple cables within a single conduit. This versatility makes PVC conduits suitable for a wide range of direct burial cable installations.
Cost-Effectiveness: PVC conduits are generally more cost-effective compared to other options like metal conduits. They are less expensive to purchase and install, contributing to overall cost savings for the project.
Additionally, Fiberglass Reinforced Plastic (FRP) conduits are another option for direct burial applications. FRP conduits offer excellent durability, corrosion resistance, and high tensile strength. They are known for their non-conductive properties, making them suitable for installations where electrical grounding is a concern. FRP conduits are particularly useful in corrosive environments or areas with high moisture content.
Is PVC conduit suitable for direct burial?
According to NEC Code 352.10 Uses Permitted, PVC conduit is suitable for direct burial and underground encased in concrete. This means that PVC conduit can be directly buried in the ground without the need for additional protection, as long as it complies with the requirements specified in NEC sections 300.5 and 305.15. These sections provide guidelines for the installation of conduits in underground applications, including direct burial scenarios. Therefore, PVC conduit is considered a suitable option for direct burial installations, as per the NEC regulations.
How deep should electrical lines be buried?
The depth at which electrical lines should be buried can vary depending on several factors, including the type of electrical line, local building codes, and regulations. Here are some general guidelines:
- Residential Power Lines: In most residential applications, electrical lines, such as service entrance cables or underground feeders, are typically buried at a depth of 18 to 24 inches (45 to 60 cm). However, local codes may require deeper burial depths, so it’s essential to consult the specific regulations in your area.
- Commercial and Industrial Power Lines: For commercial or industrial installations, the burial depth of electrical lines is often greater than in residential settings. Depths can range from 24 to 36 inches (60 to 90 cm) or even deeper, depending on the type of electrical line, voltage, and local codes.
- Direct Burial Cables: Direct burial cables, designed for underground installations without conduit, generally have specific burial depth requirements specified by the manufacturer. It’s crucial to follow the manufacturer’s guidelines to ensure proper installation and performance of the cable.
- Other Factors: Besides burial depth, it’s important to consider factors such as soil type, environmental conditions, and the presence of other utilities. Some local codes may require additional depth or clearance requirements to protect electrical lines from damage caused by external factors or future excavation.
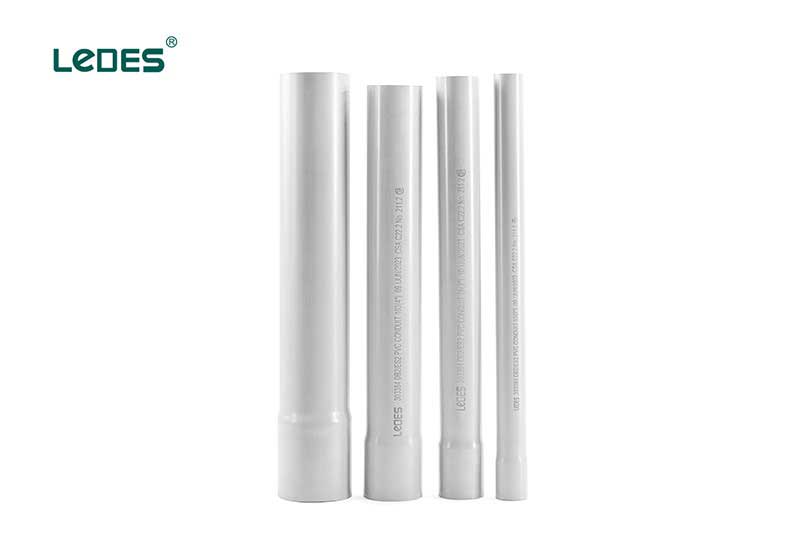
Contact
Our DB and EB series ducts offer reliable cable management and protection solutions for different applications. They are specifically designed for direct burial and concrete encasement, are the ideal choice for underground electrical installations. For more product information, please send us a request form or email us directly. Ledes’ professional team will help you with your questions and projects need.