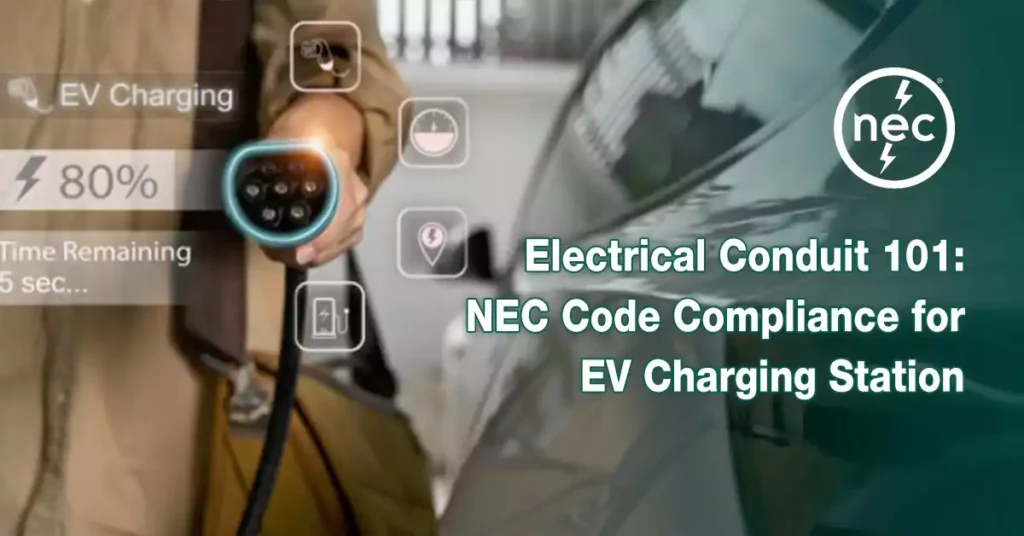
Tabla de contenido
As electric vehicles (EVs) continue to rise in popularity, the need for efficient, safe, and compliant charging infrastructure has become paramount. A key component of that infrastructure is the electrical conduit, which protects the wiring that connects EV chargers to electrical power sources. In the United States, the Código Eléctrico Nacional (NEC) provides the standards that ensure the safe installation and use of electrical systems, including those for EV charging stations.
In this guide, we will explore the latest NEC requirements for EV charging stations, offering a comprehensive understanding of the rules governing conduit systems, wiring, and safety measures. Whether you’re an electrical contractor, engineer, or facility manager, this article will help you navigate the complexities of NEC compliance for EV charging stations.
The National Electrical Code (NEC), also known as NFPA 70, is a set of standards established by the National Fire Protection Association (NFPA) to ensure the safe installation of electrical wiring and equipment. NEC compliance is crucial in preventing electrical fires, minimizing hazards, and ensuring that electrical systems operate efficiently and safely.
As the adoption of EVs increases, NEC regulations regarding EV charging stations have become a critical part of electrical system design. The NEC is updated every three years, with the most recent edition being NEC 2023. This edition introduces new rules and requirements specifically focused on the safe installation and operation of EV charging stations, taking into account the rapid growth in EV charging infrastructure across both residential and commercial sectors.
EV charging stations require robust and reliable conduit systems to protect electrical wiring from physical damage, environmental hazards, and potential fire risks. Selecting the right type of conduit is essential for both NEC compliance and the long-term safety of the installation.
RMC is one of the most durable conduit options, made of steel or aluminum. It provides excellent mechanical protection and is often used in industrial and commercial EV charging station installations where exposure to harsh environments, such as outdoor or high-traffic areas, is expected.
- NEC Requirements: According to NEC Article 344, RMC must be grounded properly to avoid creating shock hazards. RMC can be used for both above ground and underground installations but requires proper fittings and sealing for moisture protection.
- Ventajas: High durability, excellent protection against corrosion (if using galvanized steel or aluminum), and strong physical defense against impact.
EMT is a thinner and lighter conduit compared to RMC, typically made from steel or aluminum. EMT is commonly used in indoor or sheltered environments and is more cost-effective for certain installations.
- NEC Requirements: Under NEC Article 358, EMT must be grounded and bonded appropriately to ensure safety. It is best used in indoor applications or outdoor settings with minimal exposure to physical damage
- Ventajas: Lightweight and easier to install compared to RMC. It is also more cost-effective and less demanding environments.
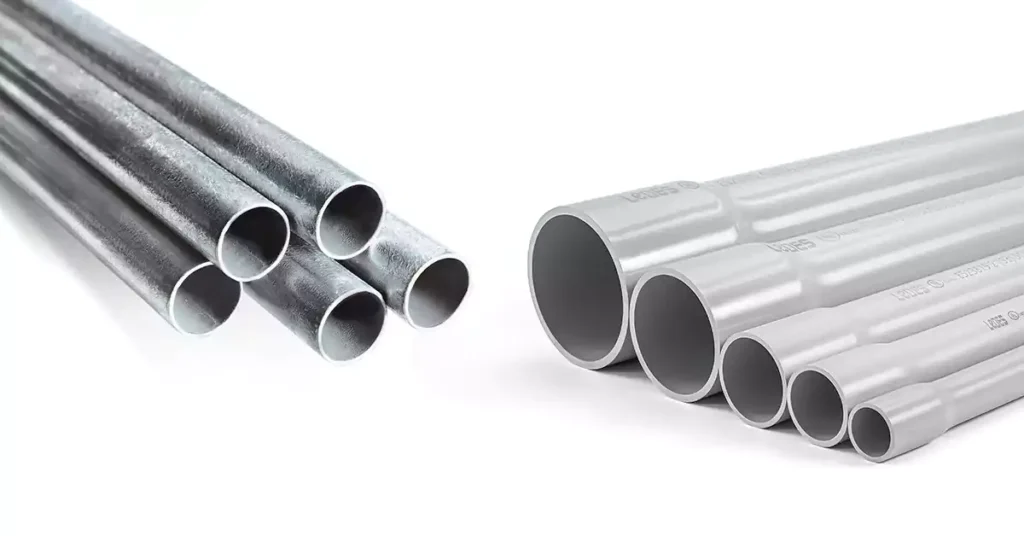
PVC conduits are widely used for both above ground and underground installations due to their corrosion resistance and affordability. Anexo 40 is thinner and is used for general-purpose applications, while Anexo 80 is thicker and offers greater protection against physical damage, making it ideal for high-traffic areas near EV charging stations.
- NEC Requirements: NEC Article 352 outlines the use of PVC conduit systems. These conduits must be installed with appropriate fittings and supported at specified intervals to prevent sagging or movement. Schedule 80 PVC is required for installations where the conduit is exposed to potential damage, such as near EV charging stations located in parking lots or driveways.
- Ventajas: Corrosion-resistant, lightweight, and easy to install. Suitable for both underground and exposed installations.
Especificación | Anexo 40 | Anexo 80 |
NEC Reference | NEC Article 352 | NEC Article 352 |
Minimum Burial Depth | 18 inches | 18 inches |
Aplicaciones | Underground or exposed | High-traffic areas |
Resistance to Physical Damage | Moderado | Alto |
Flexible conduits, such as liquid-tight flexible non-metallic conduit (LFNC), are often used in areas where rigid conduit is impractical, such as tight spaces or installations requiring frequent movement or vibration.
- NEC Requirements: Under NEC Article 356, LFNC must be supported and installed in such a way that it prevents kinking or damage. It is typically reserved for shorter sections that require flexibility.
- Ventajas: Flexibility, ease of installation, and excellent protection against moisture.
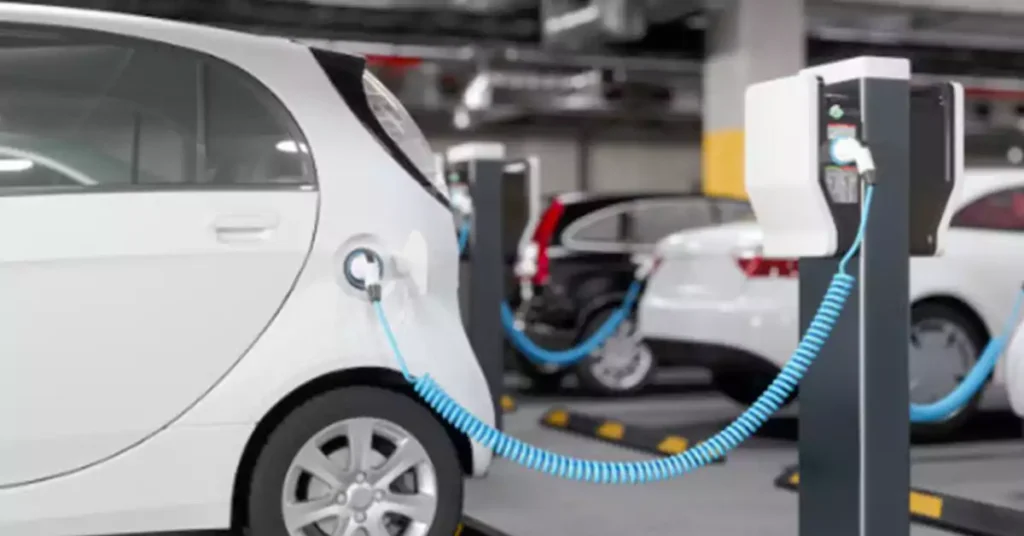
The NEC includes specific guidelines for EV charging infrastructure, primarily covered under Article 625, which governs the installation of electric vehicle power transfer systems. Understanding these requirements is key to ensuring both safety and compliance when installing an EV charging station.
Dedicated Circuits: EV chargers must be connected to dedicated circuits that are separate from other household or building loads. This ensures that the circuit isn’t overloaded and reduces the risk of tripping breakers.
Overcurrent Protection: Appropriate overcurrent protection must be provided for EV charging equipment, sized according to the manufacturer’s specifications and the NEC ampacity tables (NEC Table 310.16).
Disconnecting Means: A means of disconnecting the EV charging equipment from the power source must be installed within sight of the charging station. This allows maintenance personnel to safely de-energize the system if necessary.
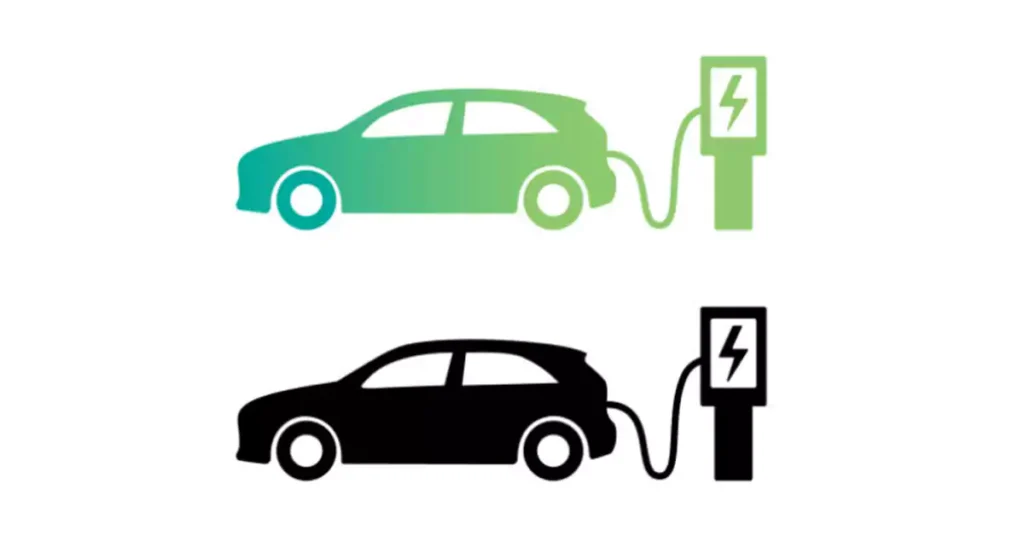
Article 625 provides a comprehensive set of rules specifically for EV charging systems, including the following key points:
Circuitos derivados: All EV charging equipment must be installed on a dedicated branch circuit, separate from other loads, to prevent interference and potential overloading.
Rating: The equipment must be rated for the voltage and current levels expected during normal operation. For residential installations, this typically ranges from 120V to 240V, while commercial or fast-charging installations may operate at 480V or higher.
Métodos de cableado: NEC requires the use of listed wiring methods and materials, such as those approved for wet locations when the conduit is installed underground or outdoors.
Ground-Fault Protection: Ground-fault protection is required for EV charging systems to minimize the risk of shock. GFCI protection is particularly important in outdoor or wet environments.
Ventilation Requirements: If the EV charging system is installed in a location where ventilation is limited (such as a garage), appropriate ventilation must be provided to prevent the accumulation of flammable gases, especially in charging systems with battery backup.
Proper conduit sizing is essential to ensure that the electrical conductors inside the conduit have sufficient space for heat dissipation and air circulation. NEC provides detailed guidelines on how to calculate conduit fill and ampacity.
- Determining Wire Size Based on Current Demand
Wire size is determined by the ampacity—the amount of current that a wire can safely carry. The NEC provides several tables that can be used to determine the appropriate conductor size based on the expected load. For example, a Level 2 EV charger typically requires 240 volts and 40 amps, which means a 6 AWG copper wire would be necessary for proper current-carrying capacity.
- Voltage Drop Calculations
Long conduit runs can lead to significant voltage drops, which reduce charging efficiency. The NEC recommends limiting voltage drop to less than 3% for optimal performance. Installers should compensate for long distances by increasing wire size or choosing larger conduits.To maintain efficiency and prevent overheating, NEC recommends limiting voltage drop to 3% for branch circuits. Voltage drop can be calculated using the formula:
For single phase system: Voltage Drop=(2×Length×Current×Resistivity)//1000
For three phase system: Voltage Drop=(1.73×Length×Current×Resistivity)//1000
If voltage drop exceeds 3%, a larger conductor may be necessary to reduce resistance and improve performance.
- Derating Factors for Conduit Systems
The NEC places limits on how many conductors can be placed in a single conduit. Overfilling a conduit can result in excessive heat build-up, which reduces the ampacity of the conductors. NEC Table 310.15(B)(3)(a) provides derating factors for different conduit fill scenarios.
Número de conductores | Percent of Values in Table 310.15(B)(16) Through Table 310.15(B)(19) as Adjusted for Ambient Temperature if Necessary |
4-6 | 80 |
7-9 | 70 |
10-20 | 50 |
21-30 | 45 |
31-40 | 40 |
41 and above | 35 |
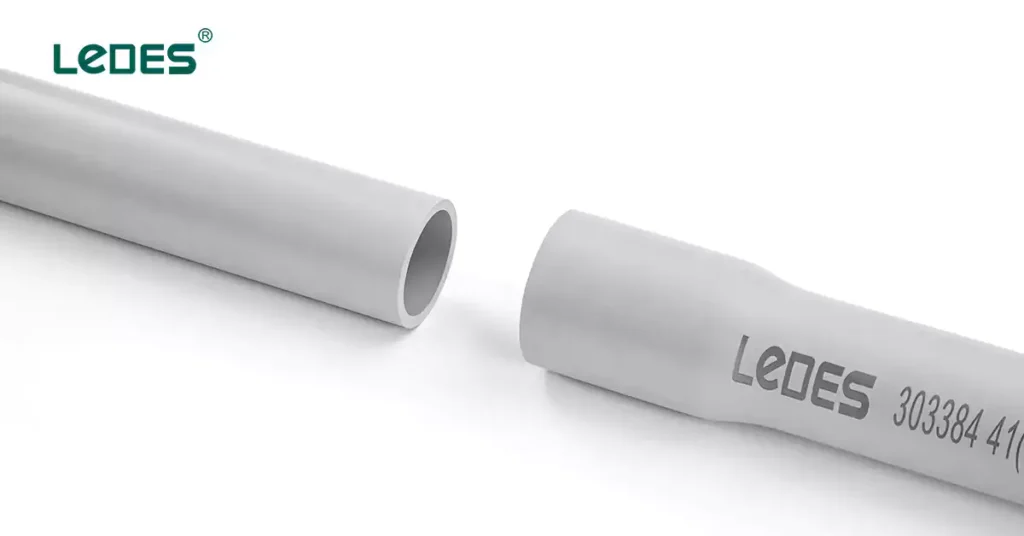
Proper installation practices are essential for maintaining the safety and functionality of the EV charging system. This includes following NEC guidelines for conduit support, bending, and spacing.
For outdoor EV charging stations, conduits are often buried underground to protect them from physical damage and environmental factors. NEC Article 300 provides detailed guidance on the minimum burial depths required for different types of conduits.
- Rigid Metal Conduit(RMC): Minimum burial depth of 6 inches for residential installations and 18 inches for non-residential installations.
- Conducto de PVC: Minimum burial depth of 18 inches for residential installations and 24 inches for non-residential installations.
- Electrical Metallic Tubing(EMT): Typically used for above ground installations, such as on walls or ceilings. The NEC requires a minimum cover depth of 18 inches for both residential and non-residential installations.
NEC Article 352.26 specifies that PVC conduit bends must not exceed a total of 360 degrees between pull points to minimize strain on the conductors. RMC refers to Article 344.24, EMT refers to Article 358.24. Other Additionally, NEC outlines requirements for supporting conduits at regular intervals.
Conduit Size (Inches) | Maximum Spacing Between Supports(ft) |
1/2 – 1 | 3 |
1-1/4 – 2 | 5 |
2-1/2 – 3 | 6 |
3-1/2 – 5 | 7 |
6 | 8 |
Conduit Size (Inches) | Maximum Spacing Between Supports(ft) |
1/2 – 3/4 | 10 |
1 | 12 |
1-1/4 – 1-1/2 | 14 |
2 – 2-1/2 | 16 |
3 and larger | 20 |
For outdoor installations exposed to extreme temperature changes, expansion joints must be installed to accommodate thermal expansion and prevent conduit damage. NEC Article 352.44 covers expansion joint requirements for PVC conduit systems.
Grounding is a critical aspect of NEC compliance for EV charging stations, providing a safe path for fault currents and minimizing the risk of electric shock.
EV charging systems must be connected to a grounding electrode system as specified in NEC Article 250. This includes bonding the equipment to the building’s existing grounding system or installing a new grounding electrode if necessary.
To protect against shock hazards, GFCIs must be installed in areas where water or moisture is present, such as outdoor EV charging stations. NEC Article 210.8 covers GFCI requirements, ensuring that all receptacles supplying EV chargers are protected.
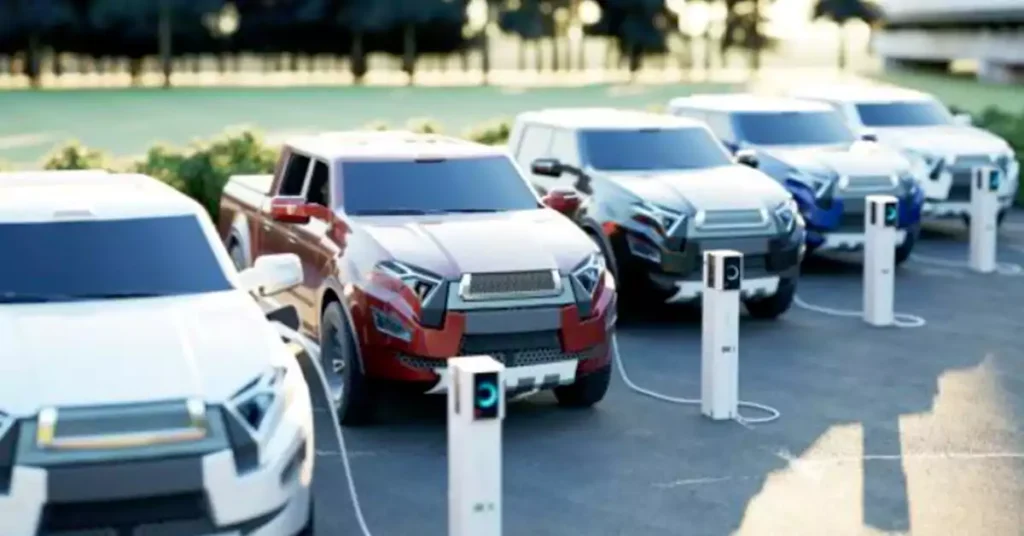
Conduits are often exposed to potential damage during construction, particularly when they are installed in high-traffic areas or underground. Heavy machinery, falling debris, or improper handling can cause cracks or deformities in conduits, leading to compromised wiring and potential safety hazards.
Bracing and Mounting: Properly bracing conduits in vulnerable areas can reduce the risk of damage. Use conduit clamps and supports as per NEC Article 344.30 to ensure that conduits are securely mounted and resistant to physical impact.
Protective Coverings: For underground installations, consider using conduit sleeves or protective coverings to safeguard against potential damage from digging or heavy equipment. In surface installations, install guard posts or barriers to shield exposed conduits from direct impacts.
Communicating with other trades (e.g., excavators, builders) during construction phases is essential to minimize risks to the installed conduits. Ensure that marked areas and maps of underground conduit systems are accessible to prevent accidental damage.
Electric vehicle charging stations handle significant electrical loads, which can increase the risk of overheating and fire if proper safety measures are not in place. Choosing fire-resistant conduit materials is a critical aspect of ensuring the overall safety of these systems.
Fire resistance in conduit materials helps to contain fires and prevent them from spreading. Two commonly used materials that meet fire safety standards are:
- PVC (Polyvinyl Chloride): While PVC conduits are non-metallic and offer excellent corrosion resistance, some varieties are also fire-resistant. PVC has a self-extinguishing property, meaning it will stop burning once the source of the fire is removed. Additionally, Schedule 80 PVC offers extra thickness for better protection in high-risk environments.
- RMC (Rigid Metal Conduit): RMC conduits made from galvanized steel or aluminum provide robust protection against fire and physical damage. Steel has a higher melting point compared to non-metallic conduits, making it more fire-resistant.
Conduit materials should meet specific Underwriters Laboratories (UL) standards to ensure fire resistance. Look for conduits with the UL 94 rating and UL651, which measures the flammability of plastic materials for parts in devices and appliances. For metallic conduits, UL 6 and UL 514 standards address fire resistance and general safety.
Material | Resistencia al fuego | NEC Article | UL Standard |
PVC (Schedule 40/80) | Self-extinguishing | NEC Article 352 | UL 94, UL 651 |
RMC (Steel/Aluminum) | High melting point | NEC Article 344 | UL 6, UL 514 |
Voltage drop is a common issue in large installations or when the charging station is located far from the main electrical panel. To mitigate this, installers can use larger gauge wires or add additional charging stations closer to the power source.
Another common mistake is overfilling conduits with too many conductors, which leads to overheating. Using larger conduit sizes or multiple conduit runs can alleviate this issue and ensure proper heat dissipation.
With the rapid development of EV technologies, it’s important to design charging stations with the future in mind. This could include:
Increased Capacity: Installing conduit and wiring that can handle future upgrades, such as additional charging stations or faster chargers.
Smart Charging Systems: These systems can optimize energy usage by adjusting the charging rate based on grid demand, which can help avoid expensive utility charges.
How to Install a Home EV Charging Station?
Installing a home EV charging station, especially a Level 2 charger, involves several steps to ensure a safe and efficient setup that meets electrical code requirements. Here’s a step-by-step guide:
- Assess Electrical Capacity:
Most Level 2 chargers require a dedicated 240V circuit, typically between 30-50 amps. Check your home’s electrical panel to determine if there’s enough capacity. Older homes might need a panel upgrade to handle the additional load.
- Choose the Right Location:
Select a location near your parking spot for convenient access, usually in a garage or driveway. Ensure that the charging cable can comfortably reach your EV without being stretched or coiled.
- Select the Charging Station:
Decide on the type of charger. A Level 2 charger will provide faster charging (usually adding 20-40 miles of range per hour), and many models come with Wi-Fi for remote monitoring. Check that the charger is UL-listed and compatible with your EV model.
- Install Conduit and Wiring:
If required by local codes, run conduit from the electrical panel to the charger location. PVC conduit or EMT (electrical metallic tubing) can protect wiring, especially in exposed or outdoor areas.
Use the appropriate wire gauge for the circuit amperage, as per the National Electrical Code (NEC). For a 40-amp circuit, typically a 6 AWG copper wire is used.
- Install the Charger:
Mount the charging unit on the wall following the manufacturer’s guidelines. This usually involves drilling pilot holes and securing the charger with screws and wall anchors.
Connect the wires to the charging station. This part is typically best left to a licensed electrician to ensure connections are safe and meet code requirements.
- Test the System:
After installation, test the charging station to ensure it’s functioning correctly. This involves connecting the EV and verifying that it charges without issues or fault indicators.
- Permits and Inspections:
Many areas require permits and inspections for EV charger installations to verify they meet local electrical codes. Check with your local municipality, and schedule any necessary inspections after installation.
By following these steps, homeowners can install a safe, reliable charging station that complies with electrical codes.
What Are the Challenges of Installing an EV Charger at Home?
- Electrical Panel Capacity:
One of the biggest challenges is determining if your home’s electrical panel has enough capacity to support an EV charger. Homes with outdated or undersized panels may require costly upgrades, adding to the installation cost and time.
- Permits and Inspections:
Homeowners must often obtain permits and schedule inspections, which can vary by locality. Navigating these requirements can be confusing and time-consuming, especially if local inspectors have specific requirements for EV chargers.
- Wiring and Circuit Requirements:
Installing an EV charger requires a dedicated circuit, typically 240V, with the correct amperage. Selecting the right wire gauge and conduit is crucial to prevent overheating, but this can be challenging for those unfamiliar with electrical codes.
- Choosing the Right Charging Location:
Finding a spot that is accessible, close to the parking area, and safe from weather elements can be tricky. Outdoor installations, in particular, require weatherproofing and potentially a more robust conduit to protect the wiring from environmental factors.
- Installation Costs:
Costs can add up, particularly if significant upgrades to the electrical system are required. Electricians typically charge a premium for installing EV chargers, and extra costs for conduit, protective covers, and outlet upgrades can increase the total expense.
- Future-Proofing Considerations:
With EV technology advancing, some homeowners might wish to future-proof their installation for higher-capacity chargers. While beneficial in the long run, this increases the upfront cost and complexity as it may require larger wiring, conduit, and panels.
Despite these challenges, working with a licensed electrician and carefully planning the installation can help create a convenient, efficient charging setup for home EV charging.
Conclusión
Understanding and complying with the NEC is crucial for the safe installation of EV charging stations. The code’s detailed guidelines on conduit types, wiring methods, grounding, and protection ensure that charging stations are not only efficient but also safe for both users and the surrounding environment. By following NEC requirements and best practices, electrical professionals can ensure that their EV charging installations meet today’s needs while being prepared for the future of electric mobility.