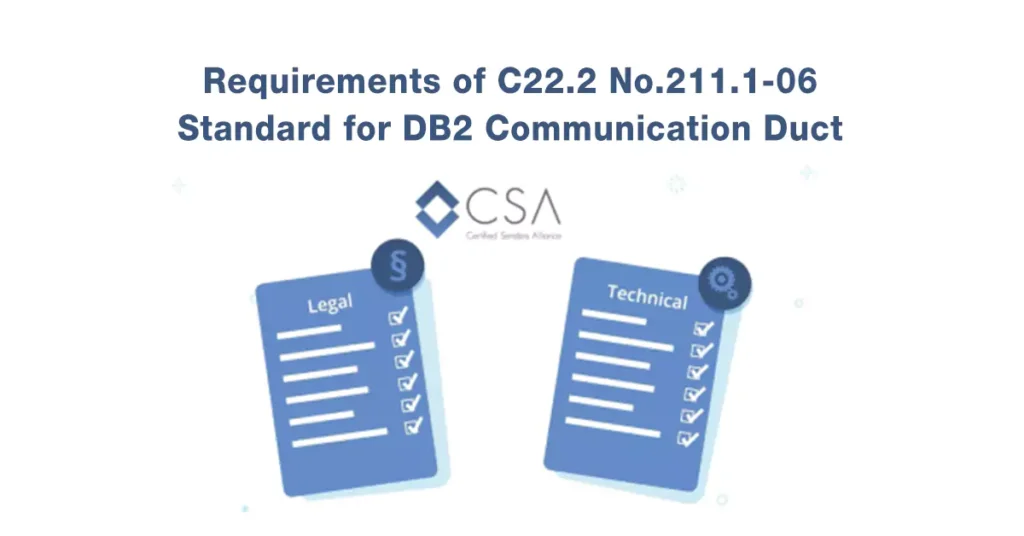
جدول المحتويات
As telecommunications infrastructure expands to support increasing data demands, the importance of compliant and reliable underground duct systems has never been greater. The CSA C22.2 standard for DB2 communication duct sets the benchmark for safety, durability, and performance in buried conduit applications across Canada.
With the 2024 update, the standard introduces stricter requirements for impact resistance, fire performance, and long-term reliability, ensuring DB2 ducts can withstand modern installation challenges. These updates align more closely with North American safety and performance standards, reinforcing their role in fiber optic networks, telecom installations, and electrical raceways.
Why Compliance Matters: The Risks of Non-Adherence
Ignoring CSA C22.2 standards or relying on outdated installation practices poses significant risks:
Safety Hazards
Non-compliant DB2 ducts may lack the required impact resistance, fire-retardant properties, or UV protection, increasing the likelihood of premature failure, electrical faults, or structural damage.
Legal & Financial Consequences
Canadian regulatory bodies enforce penalties on non-compliant installations, which can lead to costly fines, project delays, or even forced removal and replacement of improperly installed ducts.
Performance & Longevity Issues
The latest CSA updates enhance the durability and reliability of DB2 ducts, ensuring they withstand environmental stressors like moisture, temperature fluctuations, and soil pressure. Using outdated materials or installation methods can reduce system lifespan and increase maintenance costs.
In this guide, we’ll break down each critical aspect of the CSA C22.2 standard for DB2 communication duct, covering material classifications, performance criteria, installation best practices, and compliance verification. By the end, you’ll have a clear understanding of how to implement CSA-compliant DB2 systems in 2025 and beyond.
The relevant standard test methods and table data mentioned in this text are sourced from the CSA C22.2 No.211.1-06 and ASTM official standard documents for reference purposes.
What is the CSA C22.2 Standard?
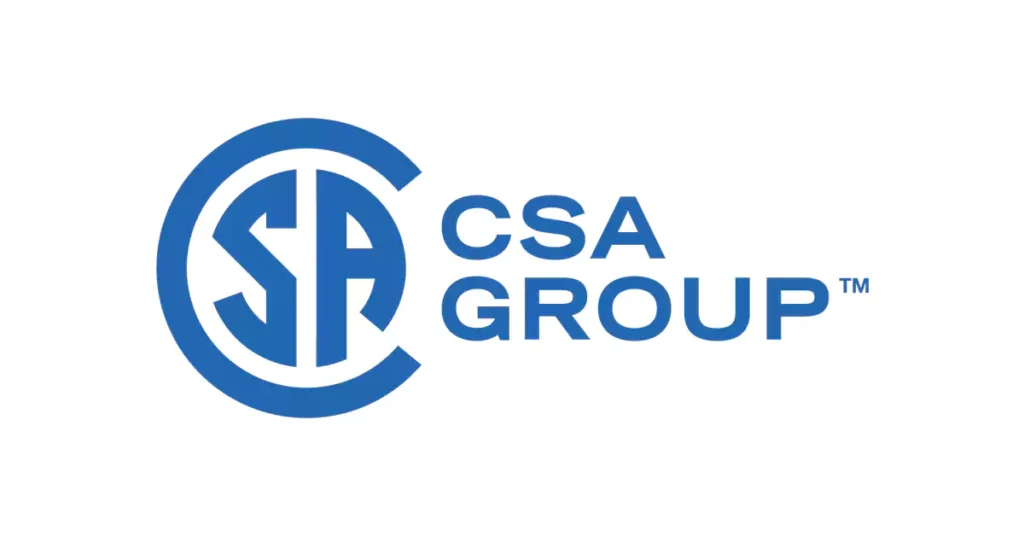
The CSA C22.2 Standard is a series of electrical safety standards established by the Canadian Standards Association (CSA). It defines the technical and performance requirements for a broad range of electrical equipment and components, ensuring compliance with the Canadian Electrical Code (CEC), Part I.
Within this extensive framework, CSA C22.2 No. 211.1 specifically applies to rigid PVC conduit systems، مشتمل:
- Type EB1 – Designed for encasement in concrete or masonry.
- Type DB2/ES2 – Intended for direct burial or encasement applications.
These conduits play a critical role in protecting electrical and communication cables from physical damage, moisture, and environmental stress. By adhering to CSA C22.2 No. 211.1, manufacturers and installers ensure that DB2 ducts meet strict impact resistance, crush strength, and fire performance standards, making them reliable for long-term underground installations.
The Importance of CSA C22.2
Compliance with CSA C22.2 is more than a regulatory requirement—it’s a commitment to safety, quality, and long-term performance. This standard establishes a rigorous framework to ensure that electrical components, including DB2 conduit and rigid PVC conduits, meet strict mechanical, chemical, and environmental durability criteria.
Its importance can be seen through several key aspects:
Ensuring Safety and Preventing Hazards
السلامة الكهربائية: By setting stringent performance criteria, CSA C22.2 minimizes the risks of electrical faults and failures. This is critical in preventing fires, electric shocks, and other hazardous conditions in both residential and industrial settings.
الحماية الميكانيكية: The standard ensures that electrical components, such as rigid PVC conduits (e.g., types EB1 and DB2/ES2), can withstand physical stresses like impacts, vibration, and environmental wear. This durability protects both the conduit system and the sensitive cables within.
Mitigating Legal and Financial Risks
Non-compliance with CSA C22.2 can result in severe penalties, project shutdowns, and liability risks. The standard aligns with the Canadian Electrical Code (CEC), Part I, making it a mandatory benchmark for electrical installations. Manufacturers and installers who fail to meet these requirements risk failing inspections, facing legal consequences, and dealing with costly rework or system failures.
For example, in 2024, a major Canadian telecom company faced $1.2 million in fines due to the use of outdated, non-compliant DB2 ducts. This case underscores the real-world consequences of ignoring CSA standards—both financially and operationally.
Pro Tips: You can read our last post of the CEC 2025 guide to learn more about the details of the Canadian Electrical Code.
Ensuring Market Acceptance and Industry Trust
Products that comply with CSA C22.2 are widely recognized and approved across Canada, making them the preferred choice for engineers, contractors, and utility providers. Compliance enhances credibility, assuring clients that electrical systems meet the highest safety and performance benchmarks.
Furthermore, CSA C22.2 serves as an industry benchmark that drives innovation. By enforcing strict performance requirements, the standard encourages manufacturers to develop more durable, efficient, and sustainable conduit solutions.
CSA C22.2 Standard Test & Performance
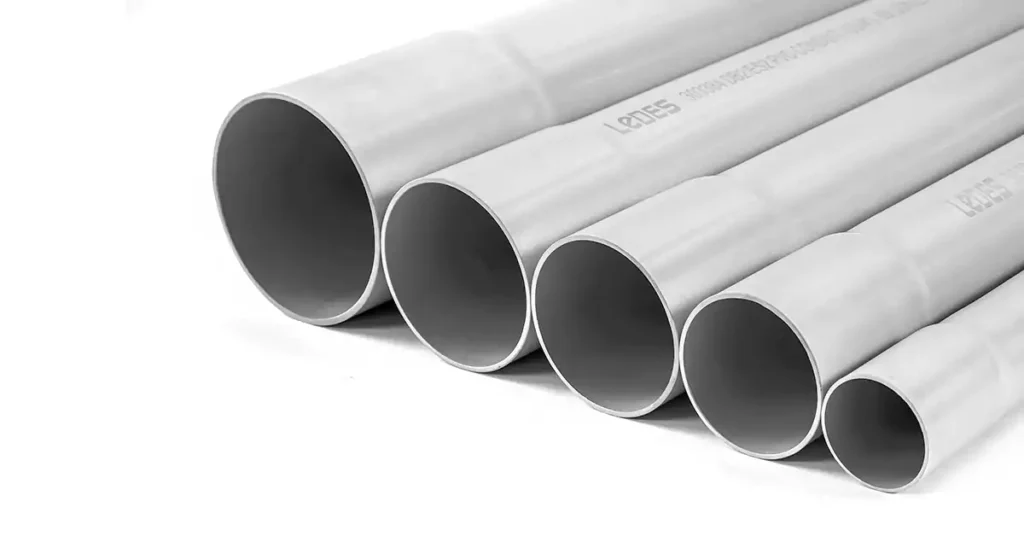
Ensuring that a conduit meets the CSA C22.2 standard involves multiple testing protocols. These tests simulate real-world conditions and evaluate the product’s performance from various angles.
CSA C22.2 No. 211.1 sets the minimum safety and performance requirements for rigid PVC conduit systems, specifically Type EB1 (Encased Burial) and Type DB2/ES2 (Direct Burial or Encased in Concrete). This standard establishes criteria for dimensions, material properties, mechanical strength, and environmental resistance, ensuring that conduits can withstand the stresses of underground electrical installations.
Manufacturers must subject their DB2 ducts to rigorous testing to verify compliance, with key areas of evaluation including:
متطلبات الأبعاد
One of the fundamental aspects of ensuring the quality and compliance of DB2 conduit is verifying that its diameter and wall thickness meet the strict requirements set by CSA C22.2 No. 211.1-06 and ASTM D 2122. These dimensional controls are essential for maintaining uniformity, structural integrity, and long-term performance in underground electrical applications.
Diameter Consistency
To ensure a precise fit and seamless integration with electrical systems, the conduit’s outside diameter must remain consistent along its entire length. According to ASTM D 2122:
• The maximum allowable deviation between the specified outside diameter and the measured average must not exceed 2%.
• This tight tolerance prevents misalignment issues during installation and enhances compatibility with fittings and connectors.
Wall Thickness & Multi-Layer Construction
For multi-layer conduits, additional structural requirements apply to maintain durability and ease of inspection:
• The inner and outer layers must each be at least 10% of the total specified wall thickness.• The center layer must be distinguishable by a contrasting color, making it easier to detect defects and ensure proper manufacturing quality.
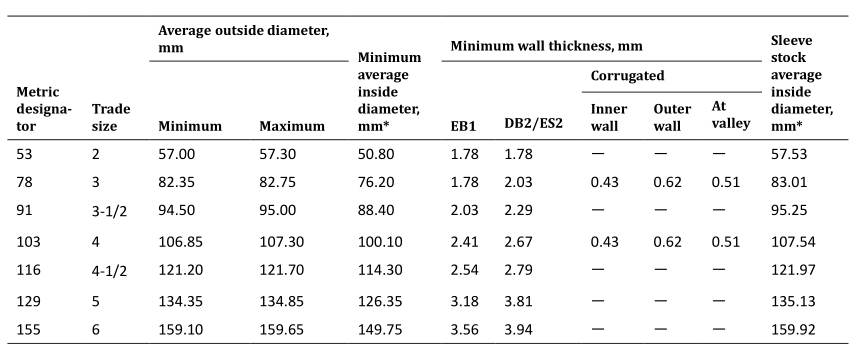
Straightness Requirement
To avoid installation difficulties and ensure that the conduit lays properly underground, its straightness is measured in accordance with ASTM D 2122:
• The maximum allowable deviation is 10 mm per meter of conduit length.
• This ensures that the conduit does not have excessive warping, which could compromise ease of handling and long-term performance.
Conditioning Testing
Before undergoing mechanical and physical performance tests, DB2 conduits must first be conditioned in a controlled environment to ensure consistency in testing results. This pre-conditioning phase is a critical step in evaluating the conduit’s durability and reliability under real-world conditions.
Standardized Conditioning Requirements
To create a uniform baseline, the conduit specimens must be conditioned as follows:
Maintained at a temperature of 23 ± 2°C.
Exposed to a relative humidity of 50 ± 5%.
Conditioned for a minimum duration of 40 hours.
Purpose of Conditioning
This process is more than just a formality—it eliminates external environmental factors that could affect material properties and skew test results. By stabilizing the conduit under controlled conditions, this step ensures that:
Performance tests are consistent and repeatable.
The material behaves as expected under normal installation and operating environments.
Variations caused by temperature fluctuations or humidity changes are minimized.
مقاومة التأثير
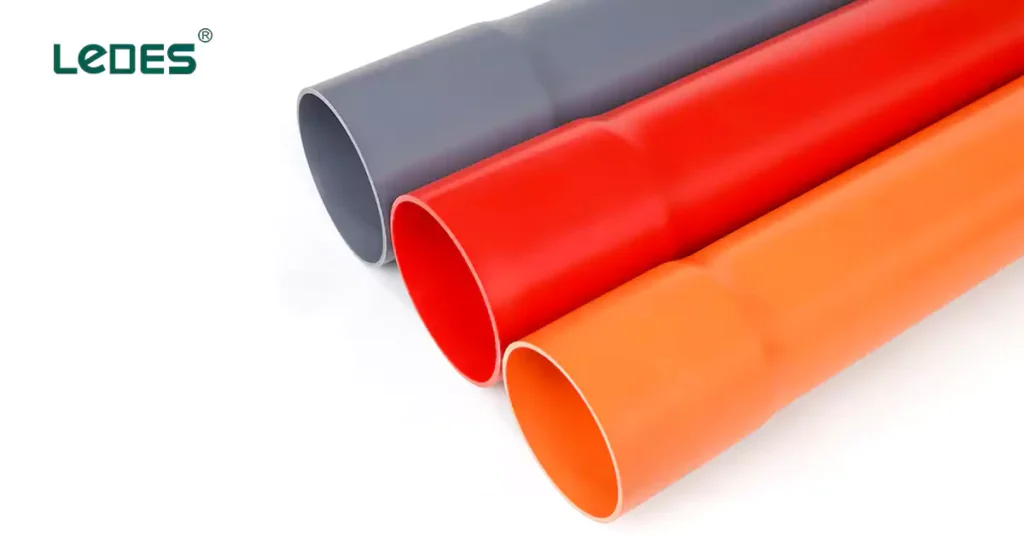
Impact resistance is a critical performance parameter that evaluates the durability of DB2 conduit against sudden mechanical shocks. Since these conduits are often installed underground or encased in concrete, they must withstand accidental impacts during handling, installation, and long-term use without cracking or splitting.
Test Methodology
The impact resistance test follows Method A of Clause 6.3.1 in CSA C22.2 No. 211.0, where conduit specimens are subjected to the following impact energies:
61 Joules at 23°C (room temperature)
34 Joules at -18°C (cold temperature)
This dual-temperature assessment ensures that the conduit remains reliable in both standard and extreme cold conditions, reflecting real-world environmental challenges.
Evaluation Criteria
A total of ten specimens are tested at each temperature level.
At least nine out of ten must show no visible cracks or splits—both internally and externally—when inspected with normal or corrected-to-normal vision.
This rigorous testing protocol guarantees that DB2 conduits provide consistent mechanical protection, even in harsh environments where physical stress is unavoidable.
Crush Resistance
DB2 and EB1 conduits are often subjected to mechanical stress during installation, backfilling, and long-term underground placement. The crush resistance tests evaluate how well the conduit retains its shape and functionality under heavy loads, ensuring it does not deform excessively or fail under pressure.
Crush Resistance Test
This test determines how much the conduit deforms under load and recovers after the pressure is removed.
شروط الاختبار: Five conduit specimens are tested at 23 ± 2°C, following the procedure outlined in Clause 6.9 of CSA C22.2 No. 211.0.
Measurement Metrics: The percentage decrease in diameter is calculated both under load and after recovery to assess deformation levels.
Acceptable Limits:
Type EB1: The diameter reduction must not exceed 12% under load and 5% after recovery.
Type DB2/ES2: The diameter reduction must not exceed 10% under load and 5% after recovery.
Coupling Crush Test
Since conduit couplings play a crucial role in maintaining a secure and continuous pathway for electrical wiring, their strength is also tested under compressive force.
إجراء الاختبار: The coupling is placed between two parallel plates that extend at least 3 mm beyond its length to ensure even force distribution.
Crushing Process: The plates apply gradual pressure until the coupling’s inner diameter is reduced to 50% of its original size, typically over a 2 to 5-minute period.
معايير النجاح: The coupling must exhibit no visible cracks or structural failures when examined under normal or corrected-to-normal vision.
These crush resistance tests confirm that both the conduit and its couplings can endure mechanical loads without deformation or failure, making them suitable for underground and high-pressure environments.
Residual Stress Test
To assess the dimensional stability of two specimens, a test is conducted following Method A of Clause 6.12.1 in CSA C22.2 No. 211.0. The objective is to ensure that the internal vertical diameter of each specimen does not decrease by more than 0.5%.
Here are the steps involved in the test:
- Each specimen is prepared to a length of 250 ± 3 mm.
- The vertical inside diameter of each specimen is measured and recorded.
- The specimens are placed in an oven that has been preheated to 65 ± 2 ℃, ensuring that the measured vertical inside diameter remains in the vertical position. The specimens are then kept inside the oven at 65 ± 2 ℃ for a duration of 4 hours.
- After 4 hours, the oven door is opened, and the specimens are allowed to cool to 23 ± 2 ℃ inside the oven.
- The specimens are then removed from the oven, and the vertical inside diameter is remeasured. The percentage change in diameter is calculated by comparing the initial measurement with the final measurement.
By following these steps, the test helps determine if the specimens maintain their dimensional stability when exposed to elevated temperatures. It ensures that the internal vertical diameter does not undergo excessive contraction, verifying the suitability of the specimens for their intended application.
المقاومة الكيميائية
To evaluate the chemical resistance of the test specimens, a chemical resistance test is conducted following the guidelines specified in CSA B137.0. The aim is to ensure that the specimens undergo a mass change of no more than 2% when exposed to the specified solutions listed in Table below. The immersion period lasts for 7 days.
After the immersion period, each sample is used to prepare both test and control specimens. The apparent tensile strength of these specimens is determined in accordance with CSA B137.0. The tests are performed within 1 hour of removing a sample from the reagent. At least three test specimens are taken from each large sample and subjected to testing at a crosshead speed of 12.7 mm/min ± 25%.
The average tensile strength of the test specimens is then compared to the average tensile strength of the control specimens. The acceptable difference between these two averages should not exceed 15%. This criterion ensures that the chemical exposure does not significantly affect the tensile strength of the specimens, indicating their ability to resist chemical degradation and maintain their structural integrity.
By conducting these tests and adhering to the specified parameters, the chemical resistance of the specimens can be accurately assessed, ensuring their suitability for applications where exposure to various chemicals is expected.
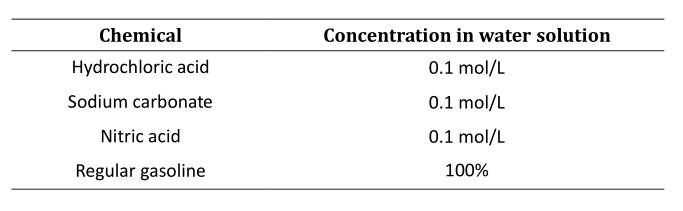
ضيق المفاصل
To assess the tightness of a joint, a test is conducted following Method A of Clause 6.11.2 in CSA C22.2 No. 211.0. The purpose is to determine if the joint can withstand water pressure for a specified duration without rupturing.
Here are the steps involved in the test:
- Two lengths of conduit, each measuring 1 ± 0.1 meters, are solvent-cemented to a coupling. The assembly is then allowed to cure for 24 hours at room temperature.
- Suitable closures are applied to the ends of the conduit to create a sealed assembly.
- The assembly is filled with water, ensuring that all air is properly evacuated.
- A gauge pressure of 35 kPa is applied to the assembly for a duration of 4 hours.
By subjecting the joint to this water pressure test, its tightness is evaluated. The goal is to verify that the joint can withstand the specified pressure without any leakage or failure. This test ensures that the joint is securely sealed, providing reliable containment and preventing water or fluid from escaping the conduit system.
الكزازة
To assess the stiffness of the conduit, a test is conducted following the guidelines of ASTM D 2412. For type EB1 conduit, it should have a minimum pipe stiffness of 200 kPa, while type DB2/ES2 conduit should have a minimum pipe stiffness of 300 kPa. This test measures the ability of the conduit to resist deformation under a specified deflection of 5%.
Bond strength
The bond strength of a conduit specimen is evaluated by attempting to cleanly separate the inner and outer walls at the corrugation valley using a sharp probe or knife point. The test is performed at eight equally spaced points around the circumference of the conduit.
The test is considered successful if it is not possible to cleanly separate the walls. This indicates a strong bond between the inner and outer walls, ensuring the integrity and structural stability of the conduit. By conducting this test, the ability of the conduit to maintain its structural integrity is assessed, providing assurance of its reliability and durability.
Key Updates in CSA C22.2 - 2021
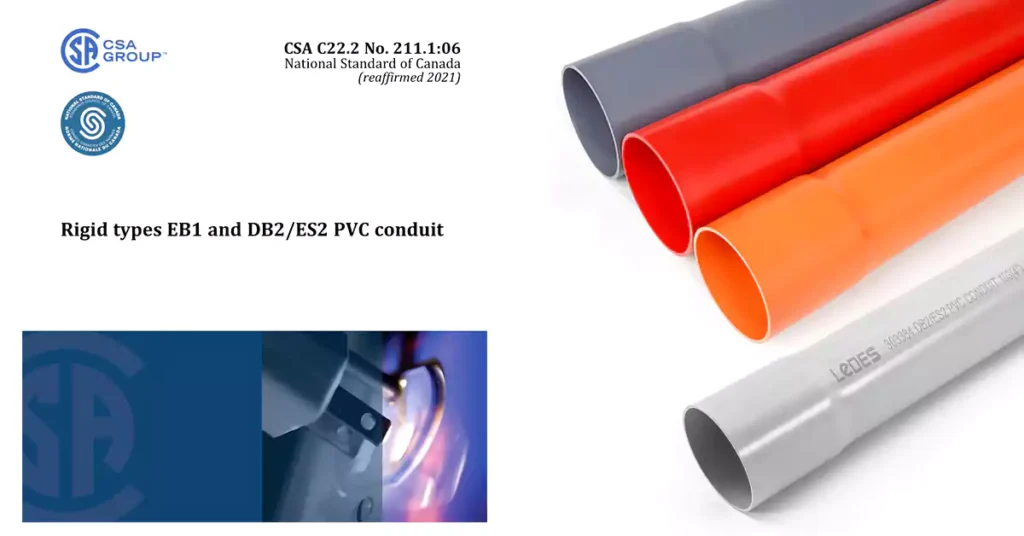
The reaffirmation of CSA C22.2 No. 211.1:06 (R2021) introduces essential updates that align with evolving safety, material, and performance standards for rigid PVC conduits (Types EB1, DB2, and ES2). These changes reflect industry advancements in sustainability, durability, and harmonization with international standards, ensuring compliance with modern electrical infrastructure needs.
1. Standardized Metric Designators for Trade Sizes
One of the significant updates in the R2021 edition is the adoption of metric designators for trade sizes. This modification enhances compatibility with global electrical and construction standards, simplifying cross-border projects and procurement. By aligning conduit sizing with international practices, the standard facilitates easier integration into multi-national supply chains and ensures better interoperability in diverse markets.
2. New Guidelines for PVC Industrial Scrap Usage
To support sustainable manufacturing practices, the latest edition establishes specific requirements for incorporating PVC industrial scrap into conduit production. This update helps manufacturers:
Enhance material consistency while maintaining performance integrity.
Reduce environmental impact by minimizing virgin material usage.
Ensure compliance with CSA mechanical and electrical performance criteria, preventing degradation due to inferior recycled materials.
This move aligns with the growing industry emphasis on eco-friendly production while maintaining stringent quality standards for rigid PVC conduits.
3. Structural and Performance Enhancements for Multi-Layer Conduits
As multi-layer conduit designs become more prevalent, the R2021 edition introduces refined requirements for their construction and performance. Notably:
Bond Strength: Multi-layer conduits must meet a minimum bond strength of 1.5 kN/m to prevent delamination, ensuring structural reliability in high-stress installations.
Improved Wall Thickness and Tolerances: Adjustments to Table 4 refine wall thickness specifications and out-of-roundness limits, improving conduit fitment with fittings and couplings.
Enhanced Mechanical Testing: Additional cyclic pressure and temperature tests have been introduced to validate conduit performance under extreme environmental conditions (e.g., -40°C to +60°C thermal cycling for DB2 and ES2 conduits).
These updates improve the overall durability and longevity of conduits used in buried, encased, and direct exposure applications.
4. Compliance and Safety Testing Enhancements
Safety remains a core focus in the R2021 reaffirmation, with modifications addressing fire resistance and mechanical performance:
Fire Rating Compliance: The updated standard aligns with UL 94 V-0 flame rating requirements, reducing fire propagation risks in plenum and high-risk environments.
Impact and Crush Resistance Improvements: Revised impact resistance tests and crush resistance criteria (per CSA C22.2 No. 211.0) ensure conduits maintain structural integrity under mechanical stress.
These refinements reinforce the standard’s commitment to protecting electrical wiring in harsh environments, ensuring conduits remain resilient against physical and environmental challenges.
5. Documentation, Labeling, and Harmonization Updates
To improve traceability and compliance tracking, the R2021 edition introduces key documentation and marking requirements:
QR Code Integration: Digital traceability via QR codes replaces manual logs, simplifying audit and verification processes for inspectors and contractors.
Updated Warning Labels: The standard now requires the term “Warning” instead of “Caution”, aligning with CSA C22.2 No. 0 hazard communication guidelines.
Cross-Standard Harmonization: Strengthened alignment with CSA C22.1 (Canadian Electrical Code) and UL 651 (U.S. PVC conduit standards) facilitates cross-border project compliance.
These enhancements modernize conduit marking and traceability, ensuring a more streamlined regulatory process across North American markets.
Industry Impact and Compliance Considerations
For manufacturers, contractors, and engineers, the reaffirmed CSA C22.2 No. 211.1-2021 introduces critical updates that impact product development, installation, and compliance. Key takeaways include:
- Ensuring PVC materials meet enhanced durability requirements (e.g., UV stability, corrosion resistance).
• Verifying conduit dimensional tolerances for improved compatibility with fittings and couplings.
• Adapting to updated testing protocols, particularly for impact, crush, and fire resistance.
• Incorporating digital traceability methods (QR codes) for regulatory compliance.
With these updates, the R2021 edition strengthens the reliability, sustainability, and safety of rigid PVC conduits, ensuring they meet the demands of modern electrical infrastructure projects.
For a detailed comparison of 2006 vs. 2012/R2021 revisions, refer to the Standards Update Service on CSA Group’s platform.
DB2 Communication Duct - Installation & Code Compliance
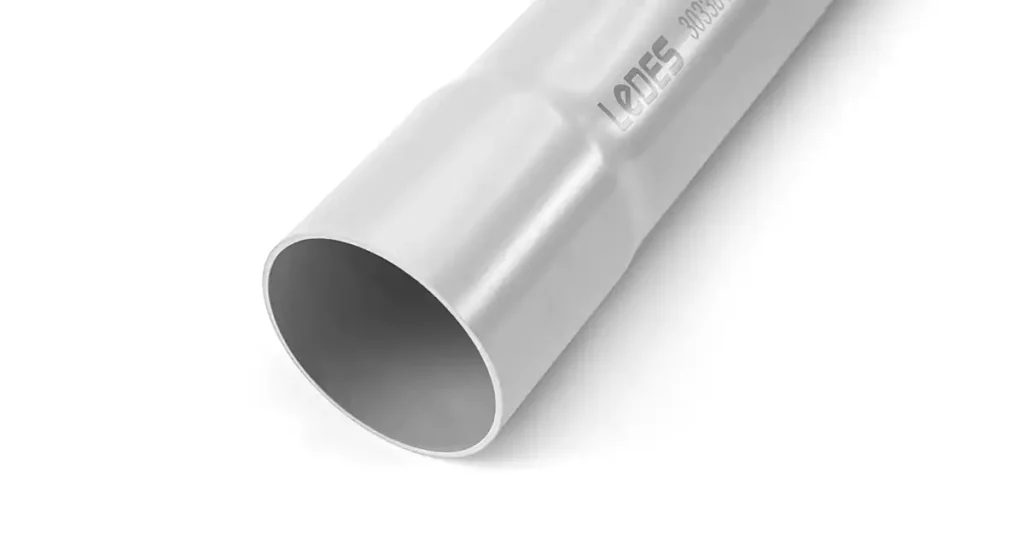
DB2 communication ducts are a crucial component in underground electrical and telecommunication infrastructure, providing mechanical protection for cables while ensuring long-term reliability in buried applications. Proper installation and compliance with CSA C22.2 No. 211.1:06 (R2021) and related standards are essential to maintain safety, performance, and regulatory adherence.
Key Compliance Requirements for DB2 Ducts
Adherence to Safety and Performance Standards
DB2 conduits are designed primarily for cable protection rather than personnel safety, differentiating them from enclosures meant to contain electrical hazards. Key compliance considerations include:
Mechanical Integrity – Sufficient impact resistance to withstand underground conditions.
Moisture Protection – Resistance to water ingress to protect internal cables.
Crush Resistance – Ability to endure external loads from soil pressure and vehicular traffic.
Applicable Standards:
CSA C22.2 No. 211.1 (R2021): Defines conduit types (e.g., DB2 for direct burial) and their performance criteria.
القانون الكهربائي الكندي (CEC): Specifies requirements for underground conduit installation, including depth and separation distances.
NEMA TC-6/TC-8: U.S. standards that may impact cross-border projects.
Material Specifications and Corrosion Resistance
DB2 communication ducts must meet stringent material requirements to withstand environmental stressors.
المقاومة للتآكل – For outdoor applications, it’s imperative that the conduit materials exhibit high resistance to environmental factors. This includes the use of materials that can withstand prolonged exposure to moisture and soil acidity, thereby preventing degradation over time.
Fire Ratings – In areas where fire safety is a concern, DB2 ducts should comply with UL 94 V-0 standards, particularly in plenum spaces where fire resistance is critical.
Data Spotlight: A 2023 NFPA report found that 12% of communication duct fires were caused by the use of non-compliant plastics, highlighting the importance of proper material selection.
2 Common Mistakes Need to Know
- Misinterpreting Scope:
Application Misalignment: A frequent error is the incorrect application of DB2 ducts for purposes beyond their intended use, such as utilizing them for power wiring, which violates standard regulations. It’s essential to adhere strictly to the specified applications to maintain system integrity and compliance.
- Overlooking Regional Differences:
Standard Variations: Installation standards and requirements can vary between regions, notably between Canada and the United States. For instance, junction box standards differ, and failing to account for these differences can lead to non-compliance and potential safety hazards. Professionals must be vigilant in understanding and applying the correct regional standards during installation.
By meticulously adhering to the material specifications and understanding the scope of CSA C22.2 No. 211.1:06 (R2021), while being cognizant of regional standard differences, professionals can ensure the safe and compliant installation of DB2 communication ducts.
Benefits & Implications of Compliance
Adhering to the CSA C22.2 standard for DB2 PVC conduits is not merely a regulatory requirement—it serves as a cornerstone for ensuring safety, reliability, and long-term cost efficiency. Compliance with this standard delivers numerous advantages, enhancing both performance and durability while mitigating potential risks. Below, we explore the tangible benefits and broader implications of using certified DB2 communication ducts.
Safety & Performance Advantages
Reduced Risk of Electrical Failures
CSA – certified DB2 ducts undergo strict testing to ensure they can withstand impact, pressure, and extreme temperatures. This helps prevent cracks, water damage, and electrical shorts that could disrupt power or data transmission. Non-compliant ducts, on the other hand, may degrade quickly, leading to costly failures.
Durability in Harsh Environments
Underground ducts must resist moisture, chemicals, and soil pressure over time. CSA – compliant conduits offer corrosion resistance and UV stability, making them suitable for challenging environments like coastal areas, high groundwater zones, and industrial sites.
Cost & Project Efficiency
Lower Maintenance & Replacement Costs
While CSA – certified products may cost more upfront, they last longer and require fewer repairs. Poor-quality ducts may lead to expensive excavation and re-installation when they fail, making compliance a cost-saving decision in the long run.
Faster Approvals & Code Compliance
Municipalities and utility companies often require CSA – certified materials. Using compliant products avoids delays, rework, and safety violations, ensuring smooth project approvals and regulatory acceptance.
Competitive & Future-Proofing Benefits
Industry Acceptance & Trust
Electrical contractors and infrastructure developers prefer certified products because they meet safety, reliability, and performance standards. This is crucial in sectors like telecommunications, smart grids, and renewable energy projects, where failures can be costly.
Prepared for Future Upgrades
As technology evolves and regulations tighten, using high-quality, compliant conduits ensures long-term reliability and compatibility. This helps avoid premature replacements and keeps electrical and communication systems ready for future demands.
Applications of DB2 Duct
DB2 ducts are widely used in underground electrical and communication infrastructure due to their durability, corrosion resistance, and compliance with CSA standards. Their applications extend across various industries, ensuring reliable and long-lasting protection for critical wiring systems.
Telecommunications & Fiber Optic Networks
DB2 ducts are essential in telecommunication networks, providing a secure conduit for fiber optic cables. These ducts prevent physical damage, moisture intrusion, and signal degradation, ensuring stable and high-speed data transmission. They are commonly installed beneath roads, sidewalks, and commercial developments where underground wiring is necessary.
Power Distribution & Utility Infrastructure
In electrical utility projects, DB2 conduits offer mechanical protection for underground power lines. Their ability to withstand soil pressure, moisture, and temperature variations makes them a preferred choice for power distribution in residential, commercial, and industrial areas.
Data Centers & IT Infrastructure
DB2 ducts play a crucial role in data centers, where uninterrupted connectivity is vital. These ducts help in organizing and protecting network cabling, reducing the risk of signal interference or cable failures in high-density IT environments.
Transportation & Roadway Projects
Highways, rail systems, and airports rely on DB2 ducts for traffic signal wiring, lighting, and control systems. Their robust construction ensures long-term performance under heavy loads, vehicle vibrations, and environmental stress.
Renewable Energy & Smart Grid Systems
With the rise of renewable energy projects, DB2 ducts are increasingly used to protect solar farm and wind energy cabling. They facilitate the efficient underground routing of power cables while ensuring compliance with safety and performance standards.
Industrial & Manufacturing Facilities
In factories and heavy industrial sites, DB2 ducts provide reliable cable management for machinery and automation systems. Their ability to resist chemicals, oil exposure, and fluctuating temperatures makes them suitable for demanding environments.
Tools & Resources
Ensuring compliance with the CSA C22.2 standard for DB2 communication ducts requires access to accurate tools and resources. This section provides essential materials that help manufacturers, contractors, and inspectors verify adherence to regulatory requirements and stay up to date with the latest industry changes.
1. Compliance Verification Checklist
A step-by-step compliance checklist is an invaluable tool for verifying whether DB2 ducts meet CSA C22.2 requirements. Key elements include:
Duct Type Identification – Confirming whether the DB2 duct is suitable for direct burial applications and complies with CSA C22.2 No. 211.1 for nonmetallic raceways.
Material & Wall Thickness – Ensuring the duct meets minimum wall thickness requirements and material durability standards for impact resistance, moisture ingress, and UV exposure.
Fire & Electrical Safety Ratings – Verifying compliance with UL 94 fire ratings, particularly for ducts used in environments requiring enhanced flame resistance.
Regional Code Variations – Addressing differences between Canadian and U.S. standards, such as requirements for conduit fittings, junction boxes, and allowable installation environments.
Marking & Certification Labeling – Checking for CSA markings and certification labels to confirm product approval for use in electrical installations.
By following this structured checklist, professionals can reduce the risk of installation errors, non-compliance penalties, and safety hazards.
نصائح: You can download the CSA C22.2 code compliance checklist for reference, which makes sure you always compliance the CEC code.
2. 2015 vs. 2024 CSA C22.2 Standards Comparison Chart
As regulatory standards evolve, updates improve safety, durability, and cross-border compatibility. The following table highlights key differences between the 2015 and 2024 versions of CSA C22.2 No. 211.1:
Criteria | 2015 Standard | 2024 Update |
Cross-Border Alignment | CSA – specific | Harmonized with UL 651/NMX-J-235/1 |
Flame Resistance | UL 94 HB (basic requirement) | UL 94 V-0 for plenum-rated spaces |
Documentation | Manual tracking & labeling | QR code traceability for verification |
These updates reflect the need for greater material resilience, improved fire performance, and simplified product verification through digital tracking.
Ledes : Powering the CHPE Project with Safety & Reliability
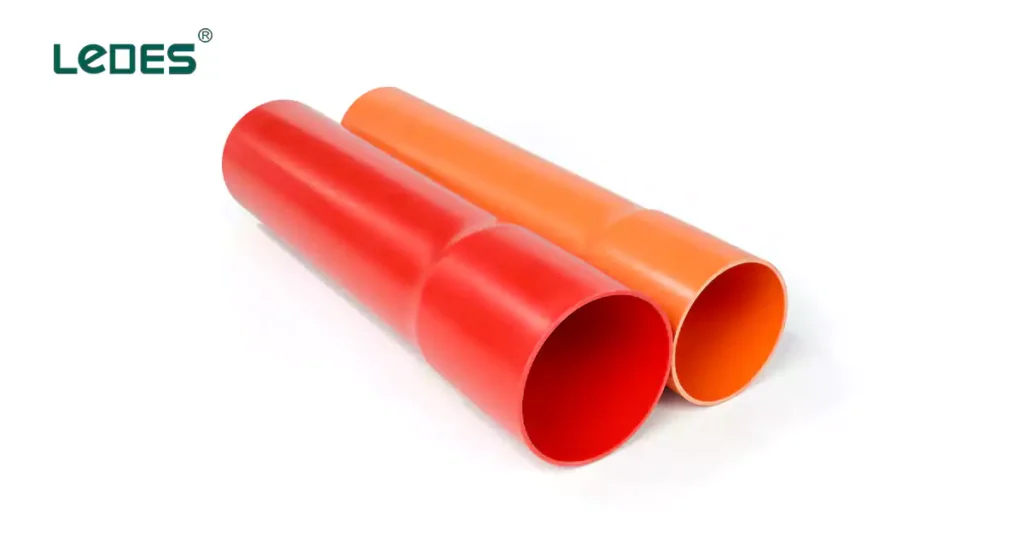
The Champlain Hudson Power Express (CHPE) project is a major energy infrastructure initiative designed to deliver clean, renewable hydroelectric power from Canada to New York. As a high-profile underground and underwater transmission system, the project demands durable, high-performance electrical conduit solutions that comply with stringent safety and regulatory requirements.
Ledes Electrical PVC Conduit & Fittings – A Trusted Choice
Ledes proudly supplied its UL-listed and CSA certified electrical PVC conduits and fittings to ensure safe, reliable, and long-lasting protection for the CHPE project’s underground electrical systems. Our products meet the highest industry standards, providing:
- Superior Durability – Designed for direct burial and resistant to moisture, chemicals, and environmental stress, ensuring long-term performance in underground installations.
- Fire & Electrical Safety Compliance – Certified to UL 651, CSA C22.2 No. 211.2 and CSA C22.2 No.211.1, ensuring compliance with North American safety standards.
- Comprehensive Fittings Selection – Ledes offers a complete range of PVC elbows, couplings, adapters, junction boxes, and custom fittings, ensuring seamless integration for complex underground electrical networks.
- سهولة التركيب والصيانة – Lightweight yet robust, our conduits simplify handling, cutting, and assembly, reducing labor costs and installation time.
لماذا ليديس؟
Ledes is a trusted supplier of high-quality electrical PVC conduit and fittings, providing conduits and fittings that proven by UL, CSA, IEC, CE, AS/NZS and ISO standards for safety, durability, and compliance. With a commitment to excellence, Ledes products meet the highest industry standards, ensuring reliable performance in demanding applications. Whether for large-scale infrastructure projects or specialized installations, Ledes delivers innovative conduit solutions that enhance efficiency, safety, and long-term reliability.
Frequently Asked Questions (FAQs)
Does CSA C22.2-2024 apply to retrofit projects?
Yes, in most cases, the CSA C22.2-2024 standard applies to retrofit projects unless the installation is explicitly grandfathered under a previous version of the code. However, if the retrofit involves significant modifications, expansions, or upgrades, compliance with the latest standard is typically required. Inspectors and regulatory authorities may assess whether the existing installation aligns with the updated safety and performance requirements.
How does CSA compliance impact installation and long-term maintenance costs?
While CSA-compliant products may have a slightly higher initial cost, they provide substantial long-term benefits, including superior durability, enhanced fire resistance, and compliance with evolving industry standards. These factors lead to reduced maintenance expenses, lower failure rates, and fewer system downtimes. Studies from electrical contracting organizations indicate that using certified products can decrease overall maintenance costs by up to 20%, ensuring a cost-effective investment over the lifespan of the infrastructure.
Can DB2 duct be used in harsh industrial environments?
Yes, DB2 communication ducts are designed to perform reliably in harsh environments, including areas with extreme temperatures, high humidity, and chemical exposure. However, it is crucial to select the appropriate material and conduit rating for specific industrial conditions. For example, DB2 ducts made from high-impact PVC offer resistance to mechanical stress and corrosive elements, making them suitable for underground and outdoor installations in demanding settings such as manufacturing plants, data centers, and energy facilities.
What are the installation requirements for DB2 ducts in underground applications?
DB2 ducts must be installed in accordance with CSA C22.2, NEC (National Electrical Code) in the U.S., and local building codes. Key requirements include:
Minimum Bury Depth: Conduits must be buried at specified depths depending on the voltage level and application type. Standard depths range from 450mm (18 inches) to 900mm (36 inches) based on site conditions.
Conduit Alignment & Jointing: All conduit sections should be properly aligned and secured using CSA-approved solvent weld or mechanical fittings to ensure a watertight and secure connection.
Backfill Considerations: Select non-corrosive and well-compacted backfill materials to prevent shifting or damage to the conduit over time.
Expansion Allowance: For regions with extreme temperature variations, expansion joints may be required to accommodate thermal expansion and contraction of the PVC material.
خاتمة
As electrical infrastructure continues to evolve, maintaining compliance with rigorous standards like CSA C22.2 is essential—not only for meeting regulatory requirements but for ensuring safety, reliability, and long-term system performance. Staying informed about the latest standard updates, material advancements, and best practices allows industry professionals to make proactive decisions that enhance the durability, efficiency, and compliance of their installations.
Whether you’re working on municipal infrastructure, industrial upgrades, or high-performance communication networks, CSA-compliant DB2 ducts provide a proven, high-quality solution. The insights, case studies, and expert recommendations outlined in this guide serve as a valuable framework for ensuring code-compliant, efficient, and future-proof installations.
Stay ahead of regulatory updates and industry advancements by choosing reliable, certified products. Contact us today to learn more about our latest CSA-compliant conduit solutions, receive expert guidance, and get access to cutting-edge electrical infrastructure products tailored to your needs.
If you have any questions or are interested in our products, you can contact us by تقديم نموذج الاتصال. Our sales team will reply to your message within one working day.