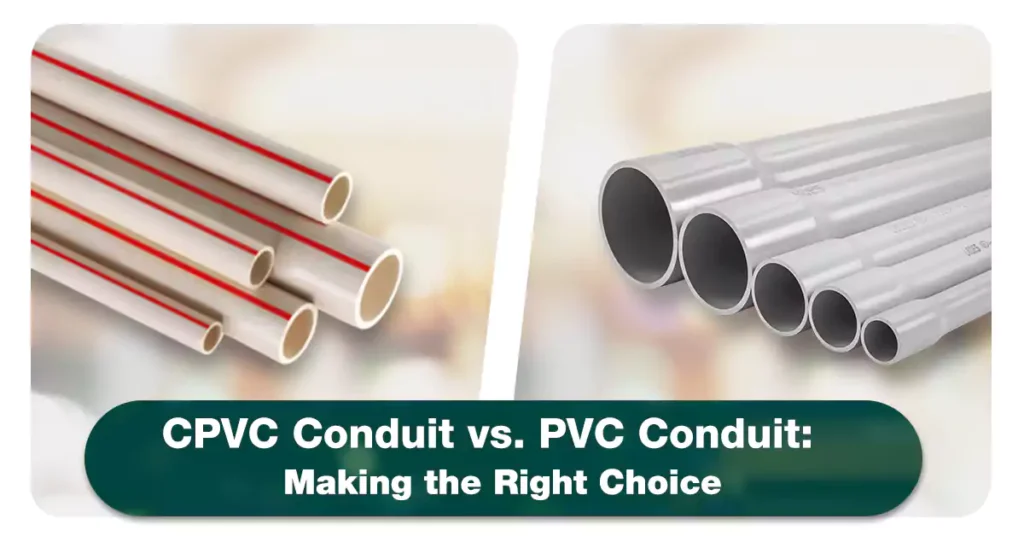
جدول المحتويات
Selecting the right conduit for electrical installations is crucial for ensuring safety, durability, and long-term performance. With various materials available, understanding their strengths and limitations helps electricians, engineers, and contractors make informed decisions that balance cost-effectiveness with compliance to safety standards.
Among the most commonly used conduit materials, PVC (Polyvinyl Chloride) and CPVC (Chlorinated Polyvinyl Chloride) stand out for their widespread applications in electrical systems. While both materials share similarities, their differences in temperature resistance, chemical composition, and mechanical properties make them suitable for distinct environments and applications.
This article aims to provide a detailed comparison of CPVC and PVC conduits, exploring their technical specifications, benefits, limitations, and best-use scenarios. By the end, you’ll have a clear understanding of which conduit type is the right fit for your specific electrical project.
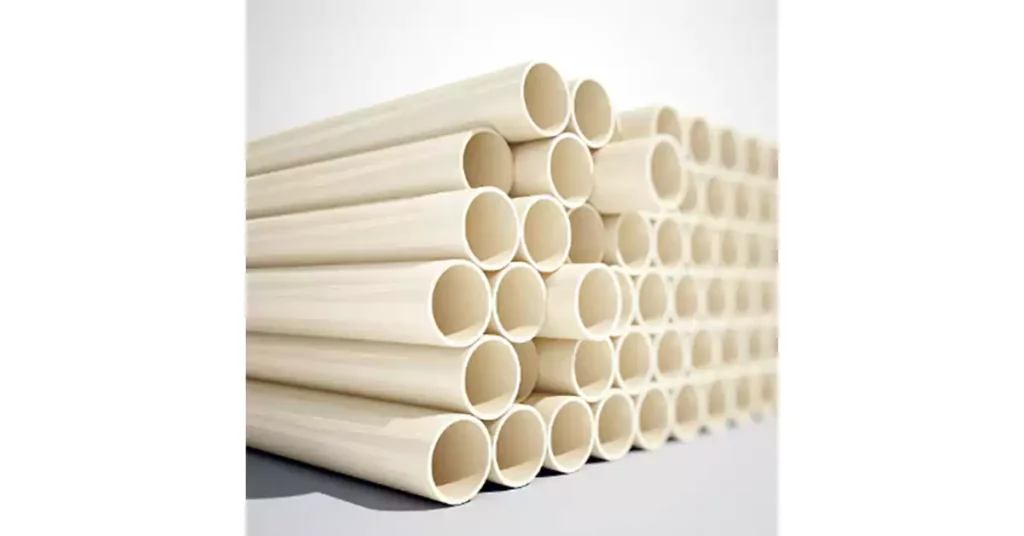
When it comes to electrical conduit systems, PVC (Polyvinyl Chloride) and CPVC (Chlorinated Polyvinyl Chloride) are two widely used materials due to their durability, non-metallic properties, and cost-effectiveness. However, despite their similarities, these materials have distinct differences in temperature resistance, chemical properties, and application suitability.
Polyvinyl Chloride (PVC) is a widely used rigid thermoplastic known for its strength, lightweight structure, and affordability. أنابيب بلاستيكية is specifically designed to protect and route electrical wiring, providing insulation, moisture resistance, and protection against mechanical damage.
- Temperature Resistance: Can withstand temperatures up to 140°F (60°C).
- مقاومة كيميائية: Offers good protection against acids, alkalis, and moisture, making it suitable for various environments.
- القدرة على تحمل التكاليف: One of the most cost-effective conduit options.
- سهولة التركيب: Lightweight, easy to cut, join, and bend with heating techniques or factory-manufactured fittings.
PVC conduit is the go-to choice for many standard electrical installations due to its low cost and reliable performance. It is commonly used in:
- Residential and commercial buildings, where standard temperature and environmental conditions exist.
- Outdoor and underground electrical installations, as it resists moisture and soil chemicals.
- Industrial settings with moderate environmental exposure, where corrosion resistance is needed but high-temperature resistance is not a concern.
Chlorinated Polyvinyl Chloride (CPVC) is a modified version of PVC, with an increased chlorine content (63-69%). This structural enhancement significantly improves CPVC’s heat resistance, chemical stability, and durability compared to standard PVC. As a result, CPVC conduit can withstand higher temperatures and is better suited for extreme environments.
- Higher Temperature Resistance: Can handle temperatures up to 200°F (93°C) without softening or deforming.
- Improved Mechanical Strength: Offers better flexibility and pressure tolerance than standard PVC.
- Superior Chemical Resistance: More resistant to corrosive substances, industrial chemicals, and soil acids, making it ideal for harsh environments.
Due to its high-performance characteristics, CPVC conduit is used in:
- High-temperature environments, such as industrial facilities, power plants, and manufacturing plants.
- Chemical processing plants, where exposure to harsh chemicals and corrosive substances is common.
- Outdoor applications in extreme climates, where high temperatures and prolonged sun exposure could degrade standard PVC.
- Specialized electrical installations requiring enhanced durability and longevity.
When selecting electrical conduits, understanding the differences between PVC (Polyvinyl Chloride) and CPVC (Chlorinated Polyvinyl Chloride) is crucial for ensuring safety, durability, and cost-effectiveness. While both materials are widely used in electrical installations, their distinct chemical compositions, temperature tolerances, and resistance properties influence their performance in various environments.
CPVC and PVC are both derived from polyvinyl chloride, but CPVC undergoes an additional chlorination process, increasing its chlorine content to 63–69%, compared to PVC’s 56%. This modification enhances CPVC’s thermal stability, fire resistance, and mechanical durability.
- قناة PVC: Limited to a maximum temperature of 140°F (60°C), making it suitable for standard electrical applications in residential and commercial settings.
- CPVC Conduit: Withstands temperatures up to 200°F (93°C), making it ideal for high-heat environments such as industrial plants, commercial buildings, and areas with high ambient temperatures.
CPVC offers superior resistance to chemicals, including acids, alkalis, and industrial solvents, making it a preferred choice in chemical plants, wastewater treatment facilities, and corrosive environments.
قناة PVC: Vulnerable to degradation when exposed to chlorine-reactive chemicals or ammonia. While cost-effective for general use, it may fail in settings with frequent chemical exposure.
CPVC Conduit: Resistant to soil acids, aggressive chemicals, and corrosive industrial environments, ensuring greater durability in extreme conditions.
Industrial reports highlight PVC conduit degradation in chemical plants, whereas CPVC conduits remain structurally intact, reducing failure risks and maintenance costs.
One of the main mechanical differences between CPVC and PVC is ductility. CPVC is more ductile than PVC, offering greater flexure and crush resistance, which makes it significantly more flexible, reducing installation complexity and allowing better crush resistance in underground or confined-space installations. Here are the mechanical properties outlined in wikipedia that you can refer to.
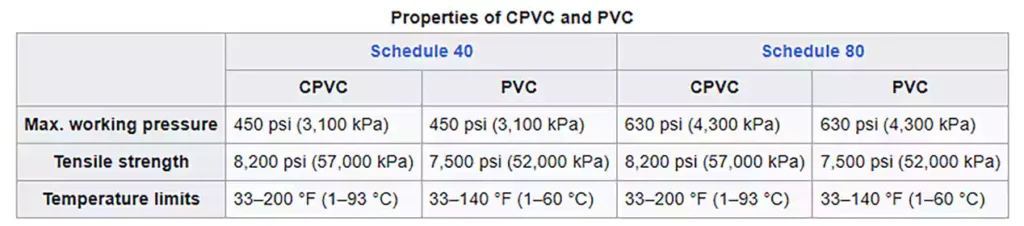
CPVC Conduit:
More ductile and crush-resistant, reducing wiring complexity.
Easier to install with fewer fittings, reducing labor costs.
Less prone to cracking under mechanical stress.
قناة PVC:
More rigid, requiring additional bends and connectors.
Can be more challenging to install in complex routing paths.
Standard choice for general electrical conduit installations.
CPVC is more expensive due to its advanced processing and enhanced performance capabilities.
قناة PVC: 2 to 3 times cheaper than CPVC, making it the economical choice for non-demanding environments.
CPVC Conduit: Higher initial cost but offers long-term savings due to lower maintenance, longer lifespan, and reduced failure risks in harsh environments.
PVC and CPVC conduits cannot be directly joined due to differences in material composition and sizing standards.
PVC and CPVC each require specific solvent cement adhesives.
CPVC connections demand CPVC-specific cement, while بولي كلوريد الفينيل uses standard PVC cement.
CPVC: Excels in high-temperature, chemically aggressive, or high-pressure environments. Third-party studies confirm its superior UV resistance and wear tolerance compared to PVC, making it more reliable for outdoor applications.
بولي فينيل كلوريد: Performs well in moderate conditions but may degrade faster under prolonged UV exposure or mechanical stress.
Both CPVC and PVC conduits must comply with NEC (National Electrical Code) regulations and relevant safety standards.
CPVC Conduit: Often meets higher fire resistance ratings.
Used in applications where additional safety compliance is required.
قناة PVC: Complies with standard NEC regulations but may not be suitable for high-temperature or chemically aggressive environments.
CPVC conduits require a specialized solvent cement due to their unique chemical composition.
CPVC Cement: Must meet ASTM F493 standards and provides high-strength bonding.
أسمنت بي في سي: Must adhere to ASTM D2564 standards but cannot be used for CPVC.
Using incorrect adhesives can lead to bond failure and compromised conduit integrity.
Both PVC and CPVC exhibit fire resistance and self-extinguishing properties, but their combustion byproducts differ significantly.
قناة PVC: When burned, releases hydrogen chloride (HCl) and carbon dioxide, which can pose environmental and health risks.
CPVC Conduit: Similar to PVC in fire resistance but can generate chlorinated dioxins and polychlorinated dibenzofurans when incinerated.
Fire Safety Considerations: In environments requiring minimal smoke and halogen emissions, CPVC still poses some combustion risks.
While CPVC and PVC conduits have their advantages, LSZH (Low-Smoke Halogen-Free) conduits offer superior fire safety by reducing hazardous emissions during combustion. Ledes low smoke halogen free conduits offer:
Minimal Smoke and Toxic Fumes: LSZH conduits do not release harmful halogens or dense smoke, improving air quality and safety in fire situations.
Ideal for enclosed spaces: Used in hospitals, data centers, tunnels, and public buildings, where fire safety is a priority.
Environmental Benefits: LSZH conduits align with green building initiatives by eliminating toxic emissions.
CPVC Conduit Vs. PVC Conduit
ميزة | قناة بي في سي | CPVC Conduit |
Max Temperature | 140°F (60°C) | 200°F (93°C) |
المقاومة الكيميائية | معتدل | Superior |
المرونة | جامد | More flexible |
يكلف | Lower | Higher |
متانة | Moderate lifespan | Longer-lasting |
مقاومة الحريق | Standard | Higher rating |
Adhesive | PVC cement | CPVC – specific cement |
مقاومة الأشعة فوق البنفسجية | Prone to degradation | More resistant |
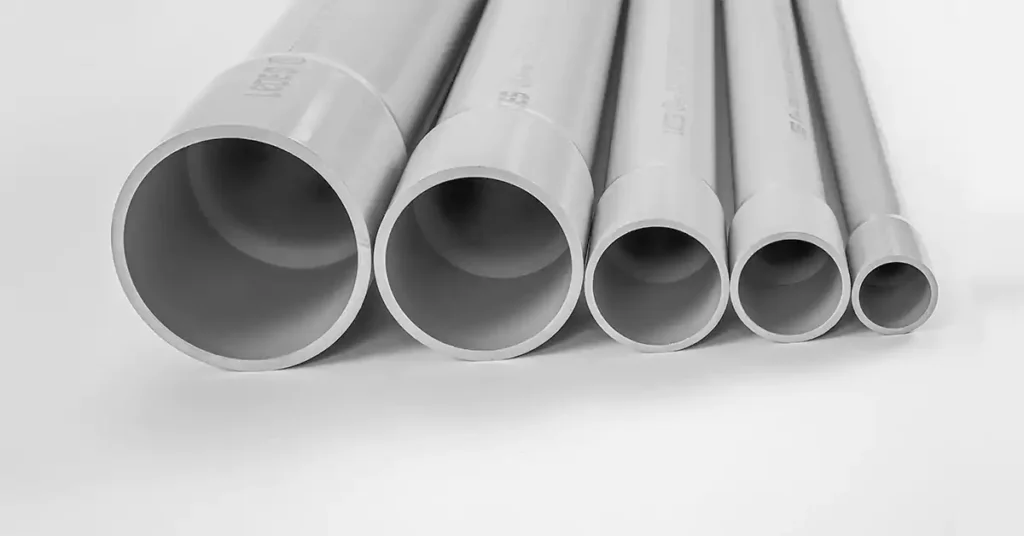
Both PVC (Polyvinyl Chloride) and CPVC (Chlorinated Polyvinyl Chloride) conduits are used in electrical and mechanical applications, but they are governed by distinct standards based on their properties and intended use. Below is a detailed breakdown of the key standards and codes that regulate PVC and CPVC conduits, along with their main requirements.
NEC Article 352 outlines installation requirements, permitted uses, and safety guidelines for rigid PVC conduit.
- It specifies that PVC conduit must be resistant to moisture, non-conductive, and flame-retardant to ensure safe electrical installations.
- Defines minimum burial depths, conduit support spacing, and temperature limitations for different environments.
- Provides guidance on transitioning between PVC and other conduit types (e.g., metal conduit).
نصائح: You can read our last post about the NEC code requirement for PVC conduit.
- UL 651 standard defines performance criteria for PVC conduit, covering aspects like impact resistance, mechanical durability, sunlight resistance, and electrical insulation.
- Requires fire-resistance testing, ensuring that the conduit does not propagate flames beyond allowable limits.
Notes: You can read our definitive guide for UL 651 standard for Schedule 40 & 80 conduit لمزيد من التفاصيل.
- UL1653 is mainly about ENT, which is a flexible, lightweight PVC conduit type.
- Requires compliance with flame resistance, crush resistance, and impact strength standards for indoor and in-wall applications.
- Unlike rigid PVC conduit, ENT is more flexible and easy to install, commonly used in residential and light commercial buildings.
نصائح: Learn more about electrical code compliance for ENT conduit for our last post.
- This standard classifies PVC materials based on their properties, including impact strength, deflection temperature, tensile strength, flammability, and major composition.
- Requires minimum tensile strength, modulus of elasticity, and specific gravity for conduit materials to ensure long-term durability.
- PVC conduit typically uses Cell Classification equal or exceed 12123 as specified in UL651.
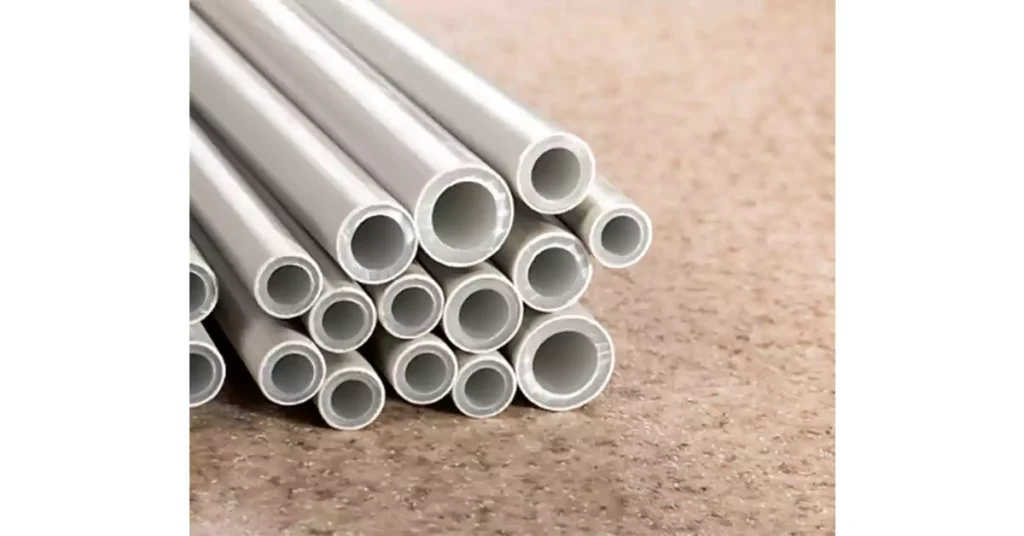
While CPVC conduits is applied for electrical raceways, but they are primarily used in piping applications. The relevant standards for CPVC include:
- Like for PVC, ASTM D1784 establishes classification and material properties for CPVC conduit and pipes.
- CPVC must meet higher temperature resistance requirements compared to standard PVC.
- Ensures CPVC material maintains mechanical integrity at elevated temperatures, typically up to 200°F (93°C), compared to PVC’s limit of 140°F (60°C).
- CPVC materials fall under Cell Classification 23447, which mandates superior heat resistance and tensile strength compared to PVC.
- Specifies pressure ratings, dimensions, and performance criteria for CPVC pipes used in plumbing and mechanical systems.
- Requires CPVC pipes to withstand high-pressure water flow and elevated temperatures without deformation.
- Covers CPVC pipe made in Schedule 40 and 80 sizes and pressure-rated for water, their dimensions, and wall thickness requirements for different applications.
- Requires testing for hydrostatic pressure resistance, chemical resistance, and long-term performance.
- A Canadian standard that most U.S. manufacturers may test to evaluate flame spread and smoke development of CPVC and other non-metallic materials for installations in plenum spaces.
- CPVC must pass strict fire performance tests, with limited flame propagation and low smoke emissions.
- This code governs mechanical and plumbing applications of CPVC in high-temperature environments.
- Defines CPVC conduit and pipe usage limitations based on heat exposure and mechanical stress.
- Includes additional fire protection and thermal resistance requirements for CPVC systems.
PVC conduit remains the dominant choice for electrical raceways due to its clear NEC and UL compliance. CPVC, while offering higher temperature resistance and enhanced fire performance, is primarily used in plumbing and mechanical applications rather than electrical installations. Understanding the applicable standards helps ensure compliance with safety codes and optimal performance for both materials.
Code Compliance of CPVC and PVC Conduit
ميزة | قناة بي في سي | CPVC Conduit & Pipe |
الاستخدام الأساسي | Electrical raceways | Primary plumbing & mechanical applications; some electrical raceways |
Key Standards | NEC Article 352, UL651, UL1653, ASTM D1784-20 | ASTM D1784-20, ASTM F442/F442M-23, ASTM F441, CAN/ULC S102.2 |
Temperature Resistance | Up to 40°F (60°C) | Up to 200°F (93°C) |
Flammability & Fire Standards | Flammability & Fire Standards | Higher fire resistance, tested under CAN/ULC S102.2 |
الخواص الميكانيكية | Impact-resistant, non-conductive, UV-resistant per UL 651 | Higher tensile strength and heat resistance |
Burial Depth & Support | Defined in NEC Article 352 | Regulated mainly for pressure and heat resistance |
Common Applications | Residential, commercial, and industrial electrical installations | Plumbing, HVAC, fire protection, and some electrical conduit use |
Fire & Smoke Development | Must meet NEC and UL fire-resistance requirements | Must pass strict flame spread and smoke development tests (CAN/ULC S102.2) |
Cell Classification | Minimum 12123 per UL 651 | 23447 per ASTM D1784-20 (higher heat and tensile strength) |
Plenum Space Installation | Limited use due to smoke development concerns | More suitable due to lower smoke emissions per CAN/ULC S102.2 |
Pressure Rating | Not pressure-rated | Rated for high-pressure and high-temperature use (ASTM F442) |

Both CPVC (Chlorinated Polyvinyl Chloride) and PVC (Polyvinyl Chloride) conduits serve important roles in electrical wiring protection, but their applications differ due to their distinct material properties, temperature resistance, and mechanical strength. Below is a breakdown of where each type of conduit is best suited for use.
PVC conduit is the most commonly used nonmetallic conduit for electrical wiring applications due to its cost-effectiveness, ease of installation, and general durability. It is best suited for:
PVC conduit is widely used in homes, offices, and commercial buildings for routing electrical wiring in walls, ceilings, and exposed installations.
It provides excellent insulation and corrosion resistance, making it ideal for indoor and outdoor applications where UV exposure is not excessive.
NEC Article 352 allows its use in exposed and concealed locations, provided it is properly secured and supported.
PVC conduit maintains structural integrity at lower temperatures but can become brittle in extreme cold (below -10°F or -23°C).
It is ideal for applications in moderate climates or indoor spaces where freezing temperatures are not a major concern.
Schedule 80 PVC conduit is often preferred in colder regions due to its thicker walls and enhanced impact resistance.
PVC conduit is more affordable than CPVC, making it a preferred choice for projects where cost efficiency is a priority.
It is lightweight and easy to install, reducing labor costs and overall project expenses.
Commonly used in residential construction, small commercial projects, and temporary installations where high-temperature resistance is not required.
CPVC conduit, though less common than PVC in electrical applications, offers superior insulation, greater mechanical strength, and better resistance to temperature extremes and chemical exposure. It is particularly well-suited for:
CPVC conduit is a better choice for direct burial applications, as it resists:
Moisture penetration and soil erosion better than PVC.
Condensation buildup, which can cause electrical failures in buried conduits.
Deformation under soil pressure, due to its higher compressive strength.
It remains structurally stable over time, making it ideal for long-term underground installations in residential, commercial, and industrial settings.
CPVC conduit can withstand higher operating temperatures (up to 200°F / 93°C) compared to PVC (140°F / 60°C).
It is suitable for:
Manufacturing plants, chemical processing facilities, and refineries where electrical conduits may be exposed to high heat or corrosive chemicals.
Power plants and renewable energy facilities where wiring systems require extra durability against thermal expansion and mechanical stress.
CPVC’s superior insulation properties reduce heat buildup inside the conduit, protecting electrical wiring from temperature fluctuations.
CPVC conduit performs better than PVC in both extremely hot and extremely cold environments.
It is ideal for:
Desert regions, high-temperature industrial sites, and tropical climates, where standard PVC may soften or deform.
Cold storage facilities and sub-zero environments, where PVC may become brittle.
Its higher flexibility and impact resistance allow it to maintain structural integrity in harsh conditions.
While PVC conduit remains the go-to choice for general electrical installations, CPVC conduit provides advantages in underground, high-temperature, and chemically aggressive environments. Choosing the right conduit type depends on project-specific requirements, including temperature conditions, moisture exposure, and mechanical stress factors.
Selecting the appropriate electrical conduit for an electrical installation requires careful consideration of several factors, including environmental conditions, budget constraints, and compliance with relevant standards. Below are key aspects to evaluate when deciding between PVC and CPVC conduits for your project.
PVC: Works well in most environments but may soften in extreme heat and become brittle in very cold temperatures.
CPVC: Handles higher temperatures, making it better for industrial or high-heat applications.
PVC: Suitable for general use but may degrade in harsh chemical environments.
CPVC: More resistant to chemicals and moisture, making it ideal for underground and industrial settings.
PVC: Commonly used for above-ground and residential installations.
CPVC: Better for underground installations because it resists condensation and pressure from soil.
The cost of conduit materials should be weighed against long-term performance:
PVC conduit is more cost-effective upfront, making it the preferred choice for budget-conscious projects such as residential wiring and commercial electrical systems.
CPVC conduit is more expensive due to its enhanced material properties, but it offers greater durability in harsh conditions.
PVC may require replacement sooner in environments with high temperatures or chemical exposure.
CPVC lasts longer in demanding applications, leading to lower maintenance costs and fewer replacements over time.
For PVC conduit, must comply with NEC and other UL, ASTM standards as required.
Regions with extreme climates may enforce stricter requirements for UV resistance or thermal stability, and CPVC conduit would be a better choice. But no matter it is PVC conduit or CPVC conduit, all need to meet the local safety standard requirements
Selecting a reliable PVC or CPVC conduit manufacturer is crucial for ensuring quality, compliance, and durability. Here are the key factors to consider:
To ensure quality, compliance, and long-term reliability, one of the first things to check is whether the manufacturer adheres to recognized industry standards, such as NEC, UL, and ASTM for PVC conduits and ASTM, CAN/ULC, and local mechanical codes for CPVC. Compliance with these regulations guarantees that the conduit meets essential safety and performance requirements.
Beyond certifications, the overall quality and durability of the conduit should be assessed. This includes material composition, resistance to mechanical stress, and the ability to withstand environmental factors such as heat, moisture, or chemical exposure. Reliable manufacturers will have strict quality control processes and conduct rigorous testing to ensure their products meet industry benchmarks.
Experience and reputation also play a key role. Established manufacturers with years of expertise tend to offer better product consistency and technical support. Checking customer feedback, case studies, or real-world applications can provide insight into how well their conduits perform over time. A manufacturer with a solid reputation is more likely to produce reliable products that meet project needs.
Availability and supply chain efficiency are equally important. Delays in product delivery can disrupt project timelines, so it’s essential to choose a manufacturer with a stable supply chain and an efficient distribution network. Some manufacturers also offer customization options for conduit size, wall thickness, or special requirements, which can be beneficial for specific installations.
Lastly, cost considerations should go beyond just the initial price. While PVC is generally more affordable, CPVC offers better performance in high-temperature and underground applications, potentially reducing long-term maintenance costs. Comparing pricing, warranty policies, and bulk purchase options can help balance affordability with quality and longevity.
By evaluating compliance, product quality, reputation, availability, and overall value, selecting the right manufacturer ensures that electrical installations remain safe, durable, and code-compliant for years to come.
CPVC and PVC conduits each offer distinct advantages depending on the project requirements. CPVC stands out for its superior heat resistance, chemical stability, and durability, making it ideal for high-temperature, corrosive, or underground applications. On the other hand, PVC remains a cost-effective and widely used option for general electrical installations, particularly in residential and low-risk environments.
When selecting the right conduit, it’s essential to consider factors like temperature exposure, installation conditions, and compliance with electrical codes. If you’re unsure which material best suits your needs, consult Ledes team to ensure optimal safety, performance, and cost efficiency for your electrical project.
Can CPVC and PVC Be Used Together?
While CPVC and PVC share similarities, they are not typically used interchangeably in the same system due to differences in material properties and installation requirements. Both materials are made from polyvinyl chloride, but CPVC undergoes additional chlorination, giving it enhanced heat resistance, chemical durability, and mechanical strength compared to standard PVC.
One of the main challenges in combining CPVC and PVC is their differing temperature tolerances and pressure ratings. CPVC can withstand higher temperatures, making it more suitable for industrial or underground applications, whereas PVC is preferred for general-purpose electrical conduit systems in residential and commercial settings.
Another important consideration is the type of solvent cement or adhesive used for joining. PVC and CPVC require different solvent cements, as CPVC’s chemical structure demands a stronger bonding agent that can handle higher temperatures and pressures. Using the wrong adhesive could lead to weak joints or failures in the conduit system.
However, there are situations where PVC and CPVC can be connected using transition fittings, designed specifically to accommodate both materials. These fittings ensure a secure and leak-proof connection while maintaining the integrity of each conduit type.
CPVC vs. PVC: Which Lasts Longer?
When comparing longevity, CPVC generally outlasts PVC due to its superior material properties. CPVC conduits can last over 50 years, while PVC conduits typically have a lifespan of 25 to 40 years, depending on environmental conditions and usage.
CPVC’s extended lifespan is mainly due to its higher heat resistance, better chemical durability, and greater mechanical strength, making it more suitable for demanding applications such as industrial environments, underground installations, and high-temperature areas. It resists cracking, warping, and chemical degradation better than PVC, ensuring a longer service life in extreme conditions.
PVC, while still durable and long-lasting, is more susceptible to UV exposure, freezing temperatures, and chemical wear over time. It remains a reliable and cost-effective choice for above-ground electrical installations, residential wiring, and general-purpose conduit systems, but may degrade faster in harsher environments.
Is CPVC Worth the Extra Cost?
CPVC is typically more expensive than PVC, but its enhanced durability and performance make it a worthwhile investment for certain applications. If your project involves high temperatures, corrosive environments, or underground installations, CPVC is the better choice due to its higher heat resistance, chemical stability, and superior mechanical strength.
In industrial settings or areas with harsh environmental conditions, CPVC’s longer lifespan and lower maintenance needs can offset the initial cost, providing better long-term value. However, for general electrical installations, residential wiring, and budget-conscious projects, PVC remains a cost-effective and reliable option.
The decision ultimately depends on the specific project requirements—if extreme conditions are a concern, the extra investment in CPVC can lead to greater durability, safety, and longevity.