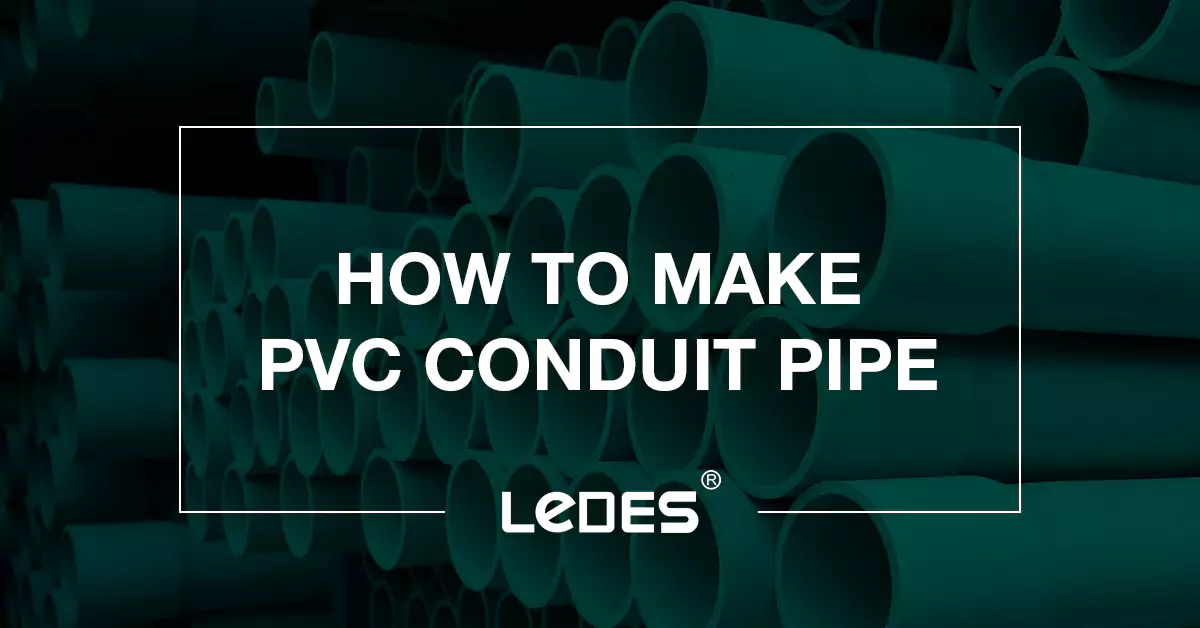
Table of Contents
Due to the impact of COVID-19, many of our customers cannot come to the factory to verify the supplier’s qualifications or even check the order’s status. Even some new customers are emailing us requesting to take a video of the PVC wire pipe production process so that they can understand the production process. So we discuss the PVC electric pipe production process in detail on the blog, as well as the factors affecting quality during the production process.
How is a PVC pipe manufactured?
The production process of PVC pipe or conduit is extrusion. We list the main production steps as follows.
Prep & Mix Materials
For the factory, the materials and additives required for mass production are picked according to the internal production order to ensure that the formula and ratio are correct. And the process is mixing and removing pollutants.
At the same time, all process personnel is ready to clean the machine after receiving the production order. Check and confirm standard operating procedures and wear the necessary protective equipment so that you are ready to go into production.
This step seems to be the simplest, but it is the most important step for buyers. The quality of raw materials and additives mean the quality of products. For example, if we used recycled materials, which are at least 50% cheaper than brand-new raw materials. Additives are almost the same. If inferior additives are used, product design parameters, such as impact resistance, water absorption, etc., can not be reached.
Using low-quality raw materials in production can not make up for product quality even if good craftsmanship is applied. That is why Ledes has insisted on not using recycled raw materials for 14 years.
Mold Installation & Machine Preheating
Install the required molds according to the work instructions, including qualitative molds, sealing baffles, cutting machine fixtures, fixed-length cutting devices, etc. Make sure all connections are good.
Connect and check the extruder heater, perform the heating operation in sections, and observe whether the heating function is normal. If any part does not reach the predetermined temperature, it may lead to insufficient melting of the plastic and affect the quality of the product.
Generally, the heating process takes 2-3 hours. It is necessary to heat the extruder and the mold to the temperature required for production. After performing constant temperature operation, check the torque of the screws at the relevant connecting parts works well. And then turn on the power.
This step is more of the preparation work before production. These steps are listed in standardized processes and operation manuals for mass production factories, and the production workshop can strictly execute them.
Parameter adjustment
After adjusting the extruder to a reasonable speed, the feeding system can start production.
In the beginning, checking whether the PVC is dissolved in place is necessary to ensure mass production quality.
Parameter adjustment depends on the equipment’s understanding and the engineer’s experience. The better the temperature and speed match, the more stable the quality of the finished product.
We cannot list debugging or parameter settings here as this varies from product to product. Even the temperature of the factory may affect the setting of parameters.
Extruding
If everything is ready, it can be mass-produced.
It is necessary to check the tube appearance, inner wall, and cross-section of the PVC pipe and adjust the parameters appropriately. And the machine can reach the best state and make sure product quality.
The principle of the extruder is very simple. That is, by heating the melted plastic, the pressure is formed in the barrel through the continuously rotating screw, and finally, it is extruded through the die to form the wire casing we need.
Extruding is the most important step in the whole wire conduit production, for most problems will be happened in this step. For example, is the mold temperature reasonable? The wire sleeve may be bent and deformed, or the outer wall may be scratched, etc. These problems are generally caused by incorrect parameters, hardware problems, or non-standard operation, which will seriously affect product quality.
Cooling
The cooling device of the available extruder is a vacuum cooling and water cooling system. The purpose of the cooling system is to make the shape. If the cooling system is not working well, the quality of the product will be seriously affected. So the cooling system’s maintenance and cooling water conditions are very high.
The cooling system involves two sets of devices, one is a vacuum machine, and the other is a water cooling machine. The main function of the vacuum cooling device is to preliminarily shape the hot plastic into the final size we need. On the other hand, the water cooling system needs to quickly cool the finally shaped wire conduit and cool down by cold water spray to achieve this purpose.
BTY, different types of resin materials require different cooling methods. For example, PVC material needs rapid cooling and shaping, so the water cooling system works well for PVC resin. On the other hand, PP or PE materials are the opposite. They cannot be rapidly cooled by water cooling. Otherwise, they will break after molding due to the different stress of the materials.
Cutting
Cutting is easy to understand for both of us. Generally, our wire conduits will be packaged and shipped by a fixed length, which is also convenient for consumers to choose from and purchase. For example, the length of the wire conduit under the UL651 standard is generally 10ft or 20ft.
Then we only need to set the length on the machine, and the laser cutting device on the extruder will work. Once the length we set is reached, it will start and cut off the PVC conduit since the wire tube is still at a high temperature and soft, so we can be cut off directly.
But in fact, there are 2 problems in this processing, the first is tolerance control, and the second is the cutting surface quality. It is a test of the factory, and the craftsmanship, because these are details.
Printing
Due to bulk buyers and consumers seeing the specifications of the PVC conduit when purchasing, a printing process is also required, and the printing process is completed mechanically.
Because different locations have different requirements for printing, the content of PVC conduit pipe printing is not the same. However, it generally includes information such as outer diameter, length, compatible standards, and manufacturer, which assures subsequent product traceability.
The general conduit printing with special black ink is not easy to be wiped off, and even if it is buried in the ground for a long time, it will not fade and cannot be seen clearly. An exception is the clear PVC conduit products, which are not printed at all by default.
BTY, with the technology upgrade, a laser engraving machine has done conduit printing. The principle of its realization is to burn the surface layer of the wire pipe with a thickness of about 1 mm by laser to form a printing that will not fall off. The birth of laser printing has boosted productivity, and prints have lasted longer.
Quality Inspection
Everyone knows about this process. The quality control of the product is more important than production sometimes.
Whether using mechanized quality inspection equipment or manual quality inspection, the goal is to take unqualified products off and let qualified products ship to customers.
Hence, we need to simultaneously check the electrical conduit tube’s appearance and printing and the PVC conduit’s inner and outer diameter. Moreover, special testing equipment is required for testing, such as our Schedule 40 PVC Conduit products.
However, our quality inspection department will randomly select a part of the products from each batch and test them on the production line or in the laboratory. The tested items include appearance, printing, diameter, punching resistance, water absorption, burning test, bending resistance test, high and low-temperature test, and so on.
All efforts are made to ensure that every electrical pipe delivered to customers is a qualified product, which is Ledes’ commitment to customers.
Packaging & Shipping
The packaging seems simple, but it is not easy to balance to protect the electrical conduit from damage, reduce the volume, reduce the use of unnecessary packaging materials, and contribute to global environmental protection.
We use standardized operating procedures and more environmentally friendly packaging materials to ensure all the products are safely stored in the warehouse.
However, a good package can better protect the product during loading and unloading. Moreover, our products have clear labels for following traceability of the products.
We will try our best to place more PVC conduit for customers through accurate calculations in the limited container space, which can save freight charges for customers and contribute to global environmental protection.
Extending Reading
How to Made Electrical Conduit Fittings?
The production process of PVC conduit and accessories is similar. The biggest difference is the equipment and mold.
The above 2 points result in differences in the mass production technique. Because the injection molding process produces applied to the fittings, we must create a mold first, and then we can produce. The injection mold creation and production are more difficult than the PVC conduit’s mold.
The general production process of fittings is,
material preparation and mixing – baking material heating – injection filling – pressure holding – cooling – demolding – online sampling inspection – post-processing – full inspection and storage – packaging and shipping.
The most obvious difference is the process of injection and filling. The principle is to inject the heated plastic material into the mold until the filling is completed and finally open the mold and get the fitting.
If readers are interested, we can write a post to explain the detailed production process of line pipe accessories separately in the future.
How are PVC pipes made, and from which material?
We have discussed the production process details of the PVC conduit in this post, and the PVC pipe production is completely compatible. You can check this article for facts.
The raw material of PVC pipe is PVC, which was discovered by German chemist Eugen Baumann in 1872 and commercialized in 1933.
PVC is widely used, especially PVC conduit pipe and accessories, because the PVC material has many advantages, such as lightweight, excellent thermal insulation ability, and recyclability.
What chemicals are used to produce a PVC pipe?
The most used chemicals in PVC conduit or PVC pipe are various additives. The most common additives are plasticizers, metal stabilizers, and heat stabilizers.
The purpose of using these additives is to enhance the sort of performance of PVC. For example, heat stabilizers can increase the temperature durable when PVC begins to degrade. Some people also worry that the abuse of additives will cause problems such as excessive heavy metals. Thanks to the continuous upgrading of technology, additives are constantly being updated. The environmentally friendly additives currently operated by Ledes can solve this problem very well.
Is recycled PVC resin good for pipe manufacturing?
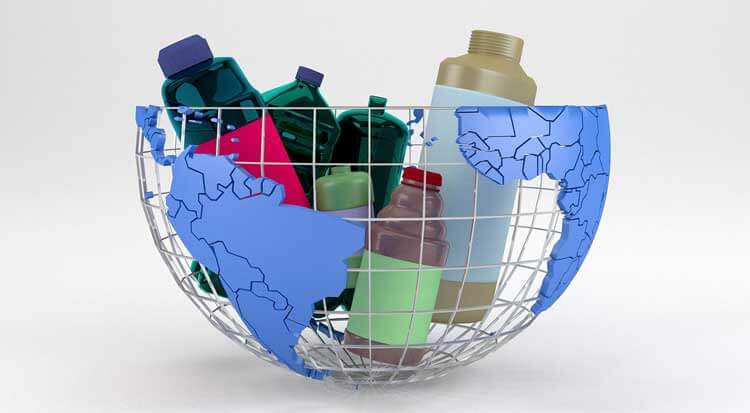
As to PVC resin recycled status, we would like to quote the numbers from Wikipedia,
In Europe, a 2021 VinylPlus Progress Report indicated that 731,461 tones PVC were recycled in 2020, a 5% reduction compared to 2019 due to the Covid pandemic. The report also covers all five sustainability challenges that the sector has set for itself covering controlled loop management, organochlorine emissions, sustainable use of additives, sustainable use of energy and raw materials and sustainability awareness.
After reading this content, you will believe that these recycled plastics must be beneficial to manufacturers to reduce costs, right?
The Wikipedia description also answers this question.
Recycled PVC is used in place of virgin PVC in various applications: coatings for swimming pools, shoe soles, hoses, diaphragms tunnel, coated fabrics, PVC sheets.
Hence, except for some drainage pipes with low requirements approved the recycled materials, the brand new electrical conduit can not apply.
That’s why Ledes will NOT use recycled PVC raw materials. Because excessive addition of recycled PVC raw materials will affect the quality of PVC conduit, which will increase the risk of plastic embrittlement. It is a very serious quality problem for wire conduits that have been buried underground for a long time or exposed to the sun.
Why is PVC used for electrical fittings?
In our opinion, this question should replace with ‘why PVC is used to manufacture and produce PVC pipes and fittings.
The reason is extremely simple, because of the many advantages of PVC, for example,
- PVC is strong and lightweight,
- PVC has good thermal insulation performance and is not easy to burn,
- Waterproof, anti-rust (a great advantage compared to metal conduit), anti-direct sunlight,
- PVC can be used for a long time, and research has proved that the natural degradation cycle of PVC is more than 80 years,
- The energy consumption of PVC in the manufacturing process is less than that of other plastics, which directly reduces energy costs,
- High transparency, good sensory properties, and will not transmit odors to food (in fact, PP is no less than PVC in this regard),
- PVC is easy to process and produce, the production cost is controllable, and the emission of harmful substances in the production process is relatively small, which is more environmentally friendly,
- PVC conduit and fittings are easier to construct due to their lightweight. Not only save labor costs but also reduce carbon emissions during construction,
- PVC is a recyclable raw material that can extend its life cycle, reduce the cost of use, and reduce the emission of harmful substances due to production.
Why are PVC pipes the best for electrical wiring?
As mentioned in our previous question, PVC has many advantages, especially compared with EMT conduit.
First, PVC will not rust, which is important for long-term exposure to air and underground work. Moreover, this will save a lot of repair and maintenance costs, thereby reducing the cost of use; secondly, PVC electrical conduits are cheap, lightweight, and easy to install; thirdly, PVC wire pipe can greatly improve UV resistance performance after using additives, can work in long-term exposure to sunlight, and even its anti-corrosion properties, such as can be used for building pull wire around the sea and chemical plants. Thus, we believe that PVC electric pipe is a cost-effective decoration material.
Moreover, we highlight that PVC pipe and conduit are different products and cannot be mixed.
Especially, PVC pipe cannot be used for wire installation and protection, and its purpose is for drainage, while PVC conduit is used for wire installation because it is designed for pulling wires.
Many think the raw materials are PVC for PVC pipe and PVC conduit, so they must be adaptable, which is a wrong concept.
The testing standards and product acceptance requirements for PVC conduit and PVC pipe are completely different. You can read the industry documents for detailed requirements and learn how they work for electrical/drainage water supply. In a word, if it is a PVC conduit, then the impact resistance, waterproof performance, and anti-sunlight performance of the wire conduit are clearly defined. At the same time, the PVC pipe is the upper limit of its water flow speed and pressure written on the paper too.
So you can be seen that this is a completely different specialization and requirement. PVC conduit does not have the core performance of PVC pipe and vice versa.
What is the advantage of an electrical conduit?
No matter what material the PVC conduit is made of, its purpose is to protect the inner electrical cable from the effects of water, microorganisms, or bad weather. If a metal electrical conduit is operated, it has higher strength and can better prevent physical damage, while PVC conduit does not rust and has good strength.
BTY, we mentioned many of its advantages for PVC conduit, including high strength, lightweight, reasonable price, corrosion resistance, sunlight, water resistance, heating resistance, flame retardant, and easy maintenance. So PVC conduit is currently the most widely used cable conduit.
Can you put a PVC conduit in concrete?
Yes, absolutely. The PVC conduits are designed for direct burial and work well in the concrete slab.
If we want to answer this question, the most important thing is whether cement will affect PVC conduit. The answer is no. Even if cement is installed in cement or underground, it will not corrode PVC because it can resist corrosion (not sensitive to high pH cement). So whether you use PVC pipe or PVC conduit, it’s okay because the two materials are the same.
We often see them pull wire cables without the PVC conduit. So the wires are pulled directly from the concrete slab, which is very dangerous. Although a layer of plastic protects the wire, its hardness and corrosion resistance is weaker than PVC conduit, so we do not recommend pulling the wire in this way. There is one exception where the wires are approved by direct burial, but the cost will be higher.
BTY, we also do not recommend using aluminum conduits directly buried in the ground or installed in concrete slabs because the high pH value of the cement will rust the aluminum pipes, accelerate their aging until it is finally damaged, and your wires will lose protection.
Can you run wires without a conduit?
We advise you do NOT like this as it will affect your personal and property safety.
From a technical matter, it will be very easy to cause short circuits or even leakage accidents if the wires are not protected. If your house is made of wood or flammable materials, a short circuit may cause a fire.
If the wires are not effectively protected, your country’s relevant laws (e.g., NEC) may be punished. If you buy property or insurance for your home, you may be denied coverage by the insurance company, especially in a major accident.
Please don’t count on the poor plastic protection or cover on the wire cable. It is impossible to replace the PVC conduit unless you use the direct buried cable, but the cost should be expensive.
So, place the cable wire in the PVC conduit, which is so easy.
How deep should a PVC conduit be under concrete?
According to Section 300.5 of the 2005 edition of the NEC (National Electrical Code), the depth of the buried PVC conduit shall not be less than 4 inches, but the maximum value is not specified.
The best practice for home or general building installations is 12 to 18 inches deep underground and protected with PVC conduits. The installation location is on a concrete floor (since installed on a concrete floor, the wire pipe can be better protected and used for longer years). Because the voltage of civil electricity is generally not high, it is enough to install at this depth.
If it is a highway or a public place, the depth of the wire conduit installation must be deeper, from 18 inches to 24 inches; because these places usually have high-voltage cables, the deeper burial depth is for safety reasons.
By the way, if you need to bury the low-voltage cable directly in the ground, the burial depth can also be kept in the range of 12 to 18 inches. But the high-voltage wires, especially UF Cables (Underground Feeder Cables), must also be buried 24 inches below the ground to ensure safety.
Where can I find good suppliers for PVC pipe products?
Whether you are a purchasing manager with rich experience in the PVC pipe industry or a new buyer who wants to find good products to serve your customers, we need to tell you that finding a reliable PVC pipe supplier is not easy.
Of course, it is easy to find a dozen suppliers online, such as Alibaba and Google, but Amazon is not recommended.
The PVC pipe conduit looks very simple, but you can not judge the pipes’ quality just at a glance.
First of all, like impact resistance, how do you evaluate it? If you look at the supplier’s product test report, you will think it is a good idea, whether issued by SGS or TüV.
Secondly, how do you know the industry qualifications of suppliers? Yes, we have industry certifications, such as ISO, UL, CSA, or AS certification. If the supplier has these certificates, they can produce PVC pipe that meets these markets’ needs simultaneously. If your suppliers can manufacture products that meet multiple national standards, their technical strength and experience would be great.
Again, how should you know if the supplier’s services are good or not? It is not easy unless you have cooperated with them several times. But we would like to tell you the real service should be after-sales service because you will know whether your supplier will maximum support you or not.
A good supplier ensures that the quality of each batch of products meets the requirements and provides good after-sales service and professional technical support. These can down your cost and improve the customer’s experience.
Ledes is a leading PVC conduit & fitting supplier with 14+ years of industry experience and UL, AS, and ISO-approved factories. Ledes has great technical accumulated and professional engineer team support to solve your problems. You can easily find us via our Contact Us page.
Contact
That’s it. If you have any questions or need help, you can contact us at any time through the website’s contact us page or talk with us by what’s app on the right side or bottom toolbar, and our customer support staff will reply within 1 business day.