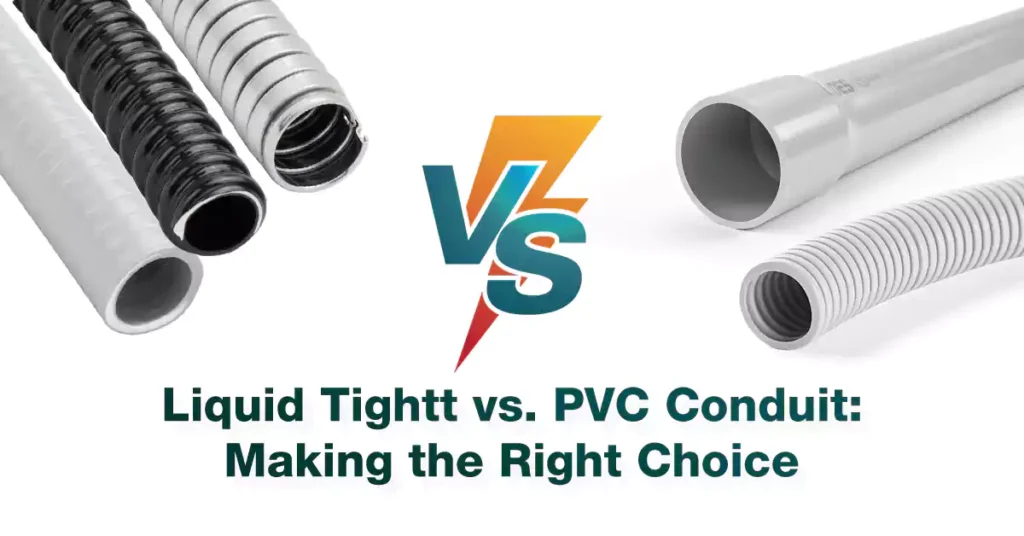
Table of Contents
When it comes to safeguarding electrical wiring, choosing the right conduit is essential. Electrical conduits are protective tubes designed to route and shield electrical wires from physical damage, environmental factors, and other hazards. They play a critical role in ensuring safety, longevity, and compliance with electrical codes.
In wet or damp environments, however, the challenge intensifies. Moisture can corrode wires, short-circuit systems, and compromise electrical installations. This makes it imperative to select a conduit specifically designed to resist water ingress and protect the integrity of the wiring.
Among the many options available, Liquid Tight conduit and PVC conduit are two popular choices for such applications. Each offers unique advantages and is suited to specific scenarios.
This article will explore the key differences between Liquid Tight and PVC conduits, helping you make an informed decision for your project. By the end, you’ll have the clarity needed to select the best conduit for wet locations and other demanding environments.
Understanding the specific types of conduits within each category is crucial to selecting the right one for your project. Let’s define Liquid Tight conduits and PVC conduits while exploring their subcategories.
Liquid Tight conduits are designed to resist moisture, ensuring that electrical systems remain protected in wet or damp environments. These conduits are flexible, durable, and typically constructed with corrosion-resistant materials, making them ideal for both indoor and outdoor applications. Below are the main types of Liquid Tight conduits:
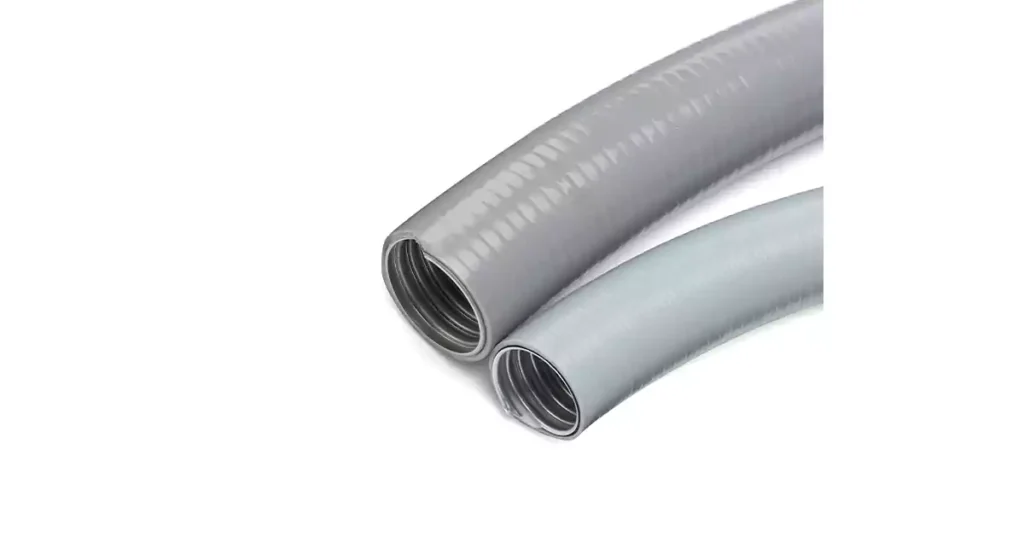
LFMC features a flexible metal core, usually made of steel or aluminum, with a liquid-tight plastic or PVC jacket. This combination provides both mechanical strength and protection against water ingress, making it a preferred choice for industrial settings, HVAC systems, and outdoor installations.
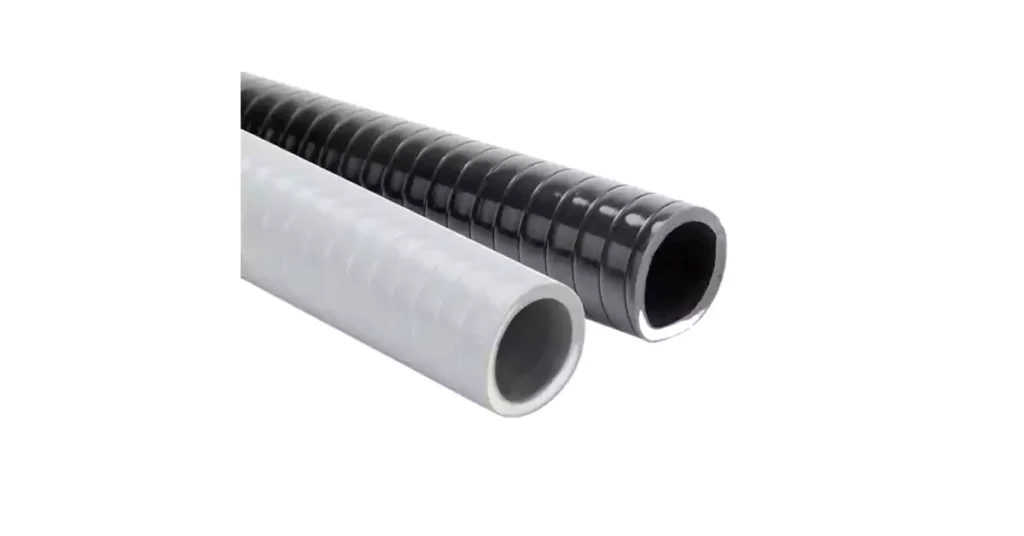
LFNC is a fully non-metallic alternative, composed of a durable plastic core with a watertight jacket. It is lightweight, easier to install than LFMC, and well-suited for residential and light commercial applications requiring protection from water exposure.
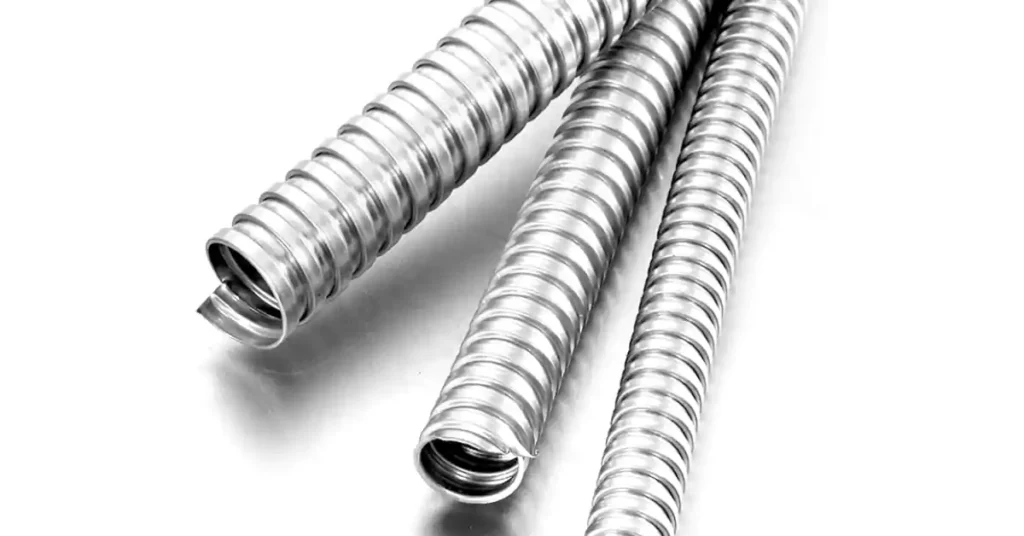
FMT is a highly flexible, metal-based conduit without a watertight jacket. While it is more commonly used for dry environments, versions with added sealing features can serve limited liquid-tight applications. FMT is often employed for short runs where extreme flexibility is required.
PVC conduits are made from rigid polyvinyl chloride, a plastic material that is lightweight, corrosion-resistant, and cost-effective. These conduits are widely used for various electrical installations, particularly in wet or underground environments, due to their natural resistance to water and chemicals. Here are the main types of PVC conduits:
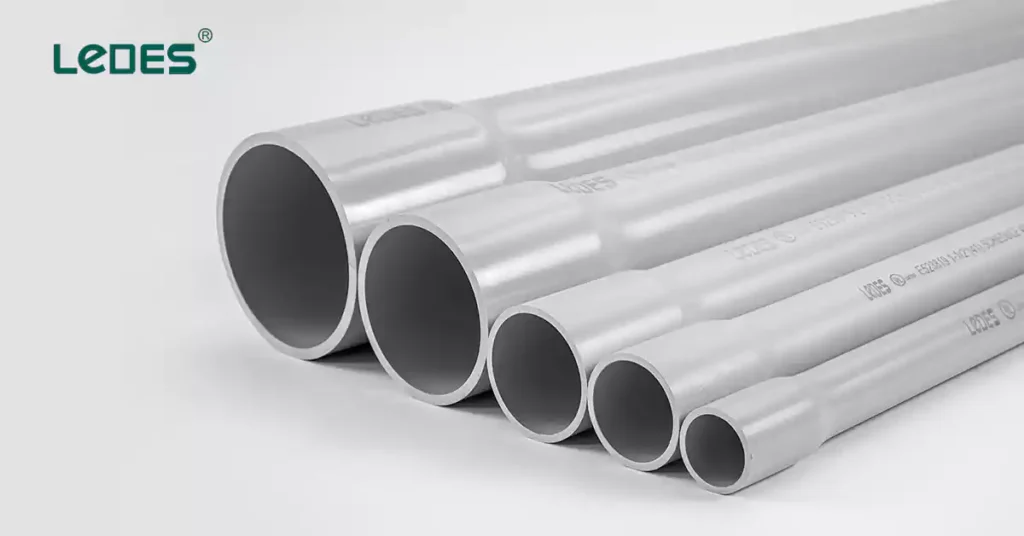
A strong, rigid type of conduit, rigid PVC conduit is ideal for long-term installations in underground or outdoor environments. It is often used in direct burial applications or as part of a conduit system for wet locations. PVC rigid conduit is easy to cut, solvent-weld, and bend with heat, offering versatility and durability.
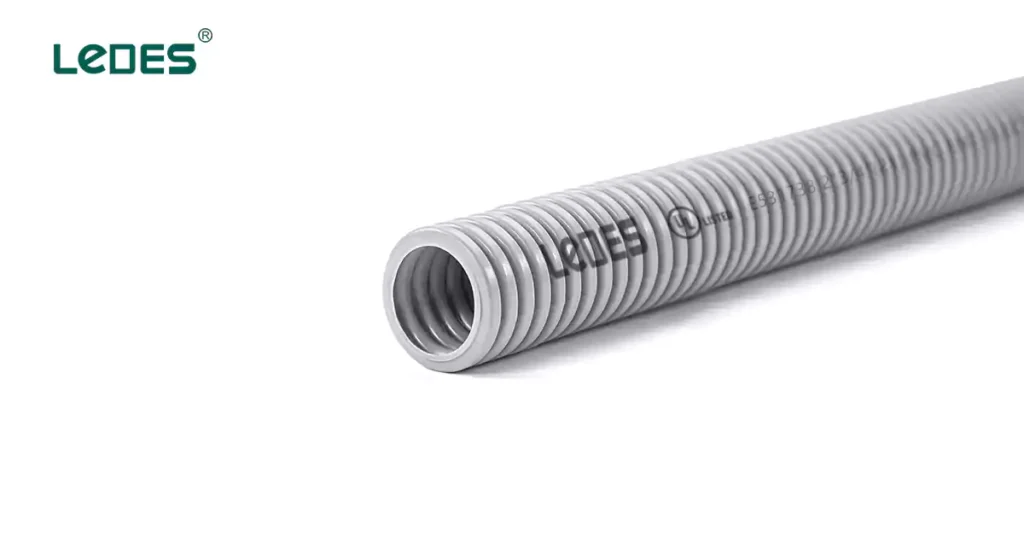
ENT conduit is a flexible, corrugated, and lightweight type of PVC conduit designed for non-metallic electrical installations. It’s commonly used in residential and commercial projects for concealed wiring in walls or ceilings. ENT is less durable than rigid PVC conduit, so it’s not suitable for direct burial or high-impact environments.
To make an informed decision, it’s essential to weigh the advantages and disadvantages of Liquid Tight and PVC conduits. Each type has distinct strengths and limitations that cater to specific applications.
Pros:
Combines the mechanical strength of a metal core with moisture resistance from a plastic jacket.
Highly durable in industrial and outdoor environments.
Retains flexibility for easier routing in complex installations.
Cons:
Higher cost compared to other conduit types.
Requires specialized fittings for a watertight seal.
Moderate UV resistance; additional coatings may be necessary for long-term outdoor use.
Pros:
Fully nonmetallic, making it lightweight and easy to install.
Strong water resistance for residential and light commercial applications.
Flexible and simple to route through tight spaces.
Cons:
Less mechanically robust than LFMC, making it unsuitable for high-impact environments.
Limited UV resistance; prone to degradation under prolonged sunlight exposure.
Higher cost compared to standard PVC conduits.
Pros:
Extremely flexible, allowing for tight bends and intricate routing.
Ideal for short runs in areas where movement or adjustments may occur.
Durable metal construction provides some level of mechanical protection.
Cons:
Lacks inherent water resistance; additional sealing is required for wet environments.
Not as corrosion-resistant as other conduit types.
Less commonly used for applications requiring complete liquid-tight sealing.
Pros:
Durable and corrosion-resistant, making it ideal for underground or wet applications.
Cost-effective and widely available.
Lightweight and easy to cut, join, and install.
UV-resistant options are available for outdoor installations.
Cons:
Less flexible, requiring heat bending or elbows for directional changes.
Can become brittle in extremely cold climates.
Limited mechanical strength compared to metal conduits.
Pros:
Lightweight and flexible, making it easy to install in walls, ceilings, and confined spaces.
Nonmetallic construction resists corrosion.
Lower cost than Liquid Tight options, suitable for indoor concealed wiring.
Cons:
Not designed for direct burial or high-impact environments.
Limited water resistance compared to rigid PVC or Liquid Tight conduits.
Less durable in exposed or outdoor applications.
Comparison Table: LFMC, LFNC, FMT, Rigid PVC, and ENT
Feature | LFMC | LFNC | FMT | RIGID PVC | ENT |
Water Resistance | Excellent; watertight jacket | Excellent; fully watertight | Moderate; needs sealing | Very good; inherently water-resistant | Moderate; suitable for dry areas |
Flexibility | High | High | Very high | Low | Very high |
Mechanical Strength | Excellent; metallic core | Good; nonmetallic core | Moderate; metallic tubing | Moderate; plastic core | Low; nonmetallic |
UV Resistance | Moderate; needs UV protection | Limited; UV degradation possible | Limited; not designed for sunlight | Good; UV-resistant options available | Low; primarily for indoor use |
Durability | High; industrial-grade toughness | Good; sufficient for light use | Moderate; limited by non-sealed design | Good; corrosion and chemical resistant | Low; prone to damage |
Ease of Installation | Moderate; requires fittings | High; lightweight and easy to handle | High; no special tools needed | High; lightweight and simple | Very high; flexible and lightweight |
Cold Weather Performance | Good; remains flexible | Good; retains flexibility | Good; retains flexibility | Moderate; may become brittle | Moderate; not ideal for outdoor cold |
Cost | High | Moderate | Moderate | Low | Low |
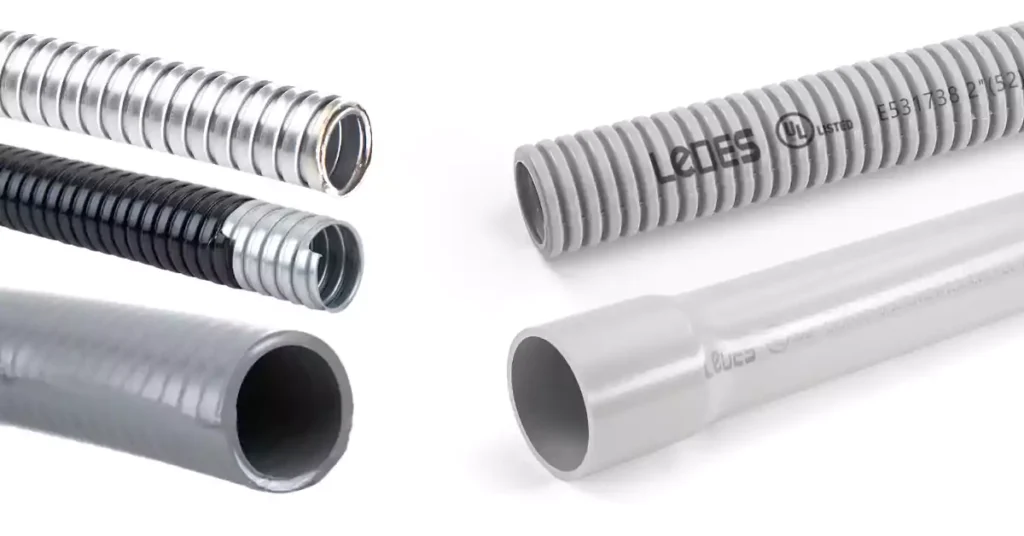
When choosing the right conduit for your electrical installations, especially in wet or damp environments, both Liquid Tight conduit and PVC conduit offer distinct advantages and challenges. While both serve the essential function of protecting electrical wiring, they differ in material, flexibility, durability, cost, and code compliance. Below, we compare these two conduit types across several key aspects to help guide your decision.
Liquid Tight Conduit: Liquid Tight conduits are typically constructed with either a flexible metallic core (in LFMC) or a nonmetallic core (in LFNC), both wrapped in a waterproof plastic jacket. This combination provides excellent water resistance while still offering flexibility for easier installation.
PVC Conduit: Rigid PVC is made of a solid plastic material, offering a lightweight and non-corrosive solution for routing electrical wiring. Some variants, such as schedule 40 electrical pipe, are designed to be used in wet conditions and underground installations.
Liquid Tight Conduit: Liquid Tight conduits, particularly LFMC and LFNC, offer high flexibility, which is crucial for installations with numerous bends or tight spaces. This flexibility allows the conduit to conform to different angles and installation paths, reducing the need for elbows or special fittings.
PVC Conduit: Rigid PVC conduit is far less flexible than Liquid Tight types. It requires additional fittings or heat bending to navigate corners, making it less suitable for installations with a lot of turns or tight spaces. However, flexible PVC options like Schedule 80 or ENT offer more flexibility but still lack the versatility of Liquid Tight.
Liquid Tight Conduit: Liquid Tight conduit provides superior protection, especially when used in industrial or harsh environments. The combination of a metallic or nonmetallic core with a durable, watertight plastic jacket ensures strong protection from mechanical damage and exposure to moisture. LFMC, being metal-based, offers excellent resistance to crushing, impacts, and abrasions.
PVC Conduit: While rigid PVC conduit is highly resistant to corrosion and chemical exposure, it is less durable when compared to Liquid Tight options in terms of physical protection. Rigid PVC is prone to cracking under heavy impact or extreme cold. However, it is still durable enough for underground and wet location use, provided it’s not subject to excessive mechanical stress.
Liquid Tight Conduit: Liquid Tight conduits are typically more expensive than PVC, particularly LFMC. The cost comes from the added benefits of flexibility, mechanical strength, and moisture resistance. Additionally, installation might require more specialized fittings, particularly for ensuring the watertight seal.
PVC Conduit: PVC conduit is a more affordable option, making it the preferred choice for budget-conscious installations. It is easy to install, with standard solvent welding or threading techniques. The lightweight nature of PVC simplifies handling and reduces labor costs.
Liquid Tight Conduit: Sealing Properties: One of the most significant advantages of Liquid Tight conduit (especially LFMC and LFNC) is its sealing capabilities. The waterproof design ensures that the conduit is fully sealed, preventing water, chemicals, and other liquids from entering the conduit and damaging the wires inside. This feature makes Liquid Tight conduit ideal for wet or submerged applications, such as outdoor industrial installations, machinery, or anywhere moisture resistance is critical.
PVC Conduit: Limited Sealing Capabilities: While PVC conduit is inherently resistant to water and corrosion, it lacks the built-in sealing properties that Liquid Tight conduits offer. PVC is suitable for general wet location use but may require additional sealing measures (such as gaskets or fittings) to ensure a completely watertight system in highly exposed or wet environments.
Each conduit type is regulated by different sections of the National Electrical Code (NEC), and understanding these regulations is essential to ensuring proper installation.
Liquid Tight Conduit:
LFMC (Liquid Tight Flexible Metal Conduit) is covered under NEC Article 350, which specifies the requirements for the use of flexible metallic conduit in wet or hazardous locations.
LFNC (Liquid Tight Flexible Nonmetallic Conduit) is addressed under NEC Article 356. This section covers the installation and use of nonmetallic flexible conduit in wet or damp environments, often where non-corrosive materials are required.
Flexible Metallic Tubing (FMT): FMT is outlined in NEC Article 360. It provides guidance on the installation and use of flexible metallic tubing, primarily for lighter-duty applications in dry, damp, or wet locations.
PVC Conduit: Rigid PVC conduit is regulated under NEC Article 352. This article specifies the installation standards for PVC rigid conduit, which is commonly used for wet, underground, or direct-burial installations due to its corrosion resistance.
Electrical Nonmetallic Tubing (ENT): ENT falls under NEC Article 362. This section provides standards for the use of flexible nonmetallic tubing, often used for residential applications or in environments where flexibility and ease of installation are key considerations.
8 Differences Between Liquid Tight Conduit and PVC Conduit
Feature | Liquid Tight Conduit | PVC Conduit |
Material Composition | Flexible metal or nonmetal core with waterproof jacket | Rigid plastic (PVC) |
Flexibility | High (ideal for tight bends and complex installations) | Low for rigid conduit, but high for ENT |
Durability | High; resistant to impacts and moisture | Moderate; prone to cracking under impact or cold |
Sealing Properties | Excellent; fully waterproof and moisture-sealed | Limited; requires additional sealing measures |
Cost | Higher; more expensive than PVC | Lower; more cost-effective for general applications |
Environmental Resistance | Excellent water, moisture, and chemical resistance | Good; resistant to water, but UV-sensitive |
Installation | Requires specialized fittings; moderate difficulty | Easy to install with solvent cement or threading |
Code Compliance | LFMC: NEC Article 350, LFNC: NEC Article 356 | Rigid PVC: NEC Article 352, ENT: NEC Article 362 |
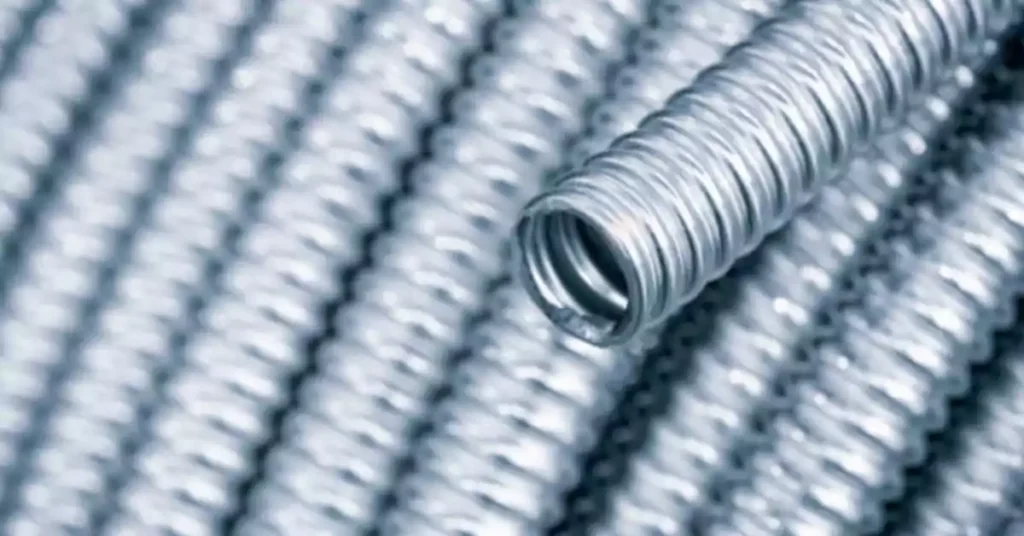
Each type of conduit – whether Liquid Tight or PVC – has its own set of applications as defined by the National Electrical Code (NEC). Understanding these specifications is key to ensuring safety, functionality, and code compliance in various installations. Below, we explore the general applications, as well as permitted and not permitted uses for each conduit type, according to the NEC.
Permitted Applications:
Exposed or concealed locations requiring flexibility and protection from liquids, vapors, or solids.
Hazardous locations as specified in NEC Chapter 5.
Direct burial if listed for the purpose.
Environments with frequent movement or vibrations.
Restrictions:
Not suitable for areas prone to physical damage.
Should not be installed in conditions exceeding its temperature rating.
Permitted Applications:
Exposed or concealed locations where flexibility is needed.
Wet, damp, or dry locations, including outdoor use if listed.
Concrete encasements to provide additional protection.
Restrictions:
Not allowed in hazardous locations unless explicitly listed.
Not suitable for areas subject to physical damage.
Cannot withstand high ambient temperatures unless rated for such use.
Permitted Applications:
Branch circuits in dry, concealed, and accessible locations for voltages up to 1000 volts.
Short, flexible runs where rigidity is impractical.
Restrictions:
Prohibited in underground installations or concrete encasements.
Not suitable for hazardous locations or areas exposed to physical damage.
Limited to a maximum length of 1.8 meters (6 feet).
Permitted Applications:
Concealed, exposed, underground, or concrete-encased installations.
Corrosive, wet, and damp environments.
Installations with high-temperature-rated conductors within the conduit’s listed limits.
Restrictions:
Prohibited in hazardous locations unless specifically approved.
Not suitable for areas prone to direct physical damage unless using Schedule 80 or equivalent protection.
Cannot withstand prolonged exposure to high temperatures beyond its rated limit.
Permitted Applications:
Concealed or exposed installations in residential, commercial, or industrial buildings up to three floors.
Fire-rated concealed installations in taller buildings.
Wet or damp environments, including installations in concrete encasements.
Restrictions:
Cannot be used in exposed locations unless explicitly permitted.
Not suitable for areas with physical damage, direct sunlight, or high temperatures unless rated for such conditions.
Not allowed in hazardous locations.
Applications of Liquid Tight Conduit Vs. PVC Conduit
Conduit Type | Applications | Restrictions |
LFMC | Wet, concealed, hazardous, or flexible areas. | Not for physical damage or high heat. |
LFNC | Wet, flexible, or outdoor installations. | Not for physical damage or high heat. |
FMT | Short runs in dry, concealed locations. | Not for underground or hazardous areas. |
Rigid PVC | Corrosive, damp, or underground environments. | Not for hazardous or high-damage areas. |
ENT | Concealed or fire-rated installations. Wet or damp. | Not for direct sunlight or physical damage. |
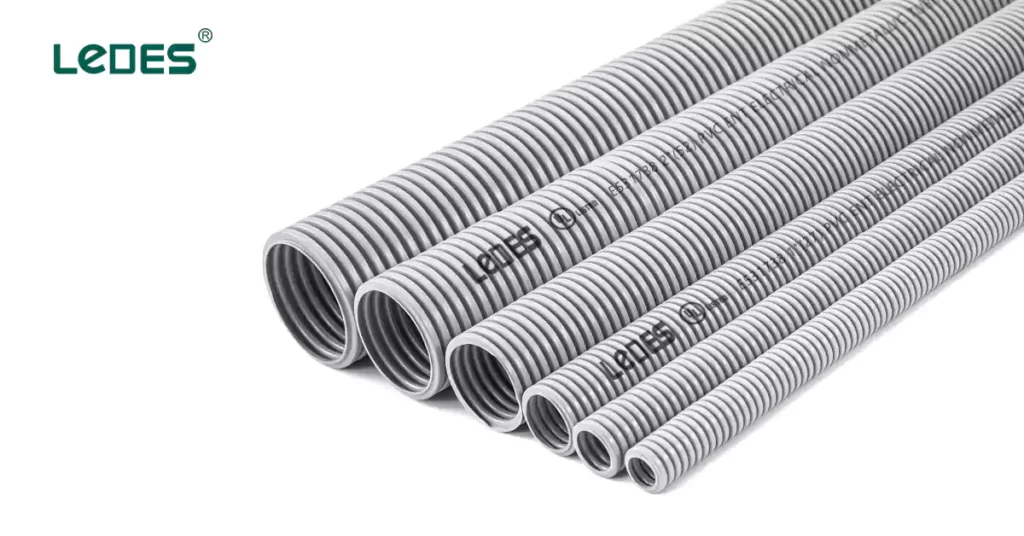
Selecting the right electrical conduit for your project is essential to ensure safety, efficiency, and compliance with applicable codes and standards. Here’s a guide to help you navigate the process:
The choice of conduit must align with codes and standards such as the National Electrical Code (NEC) and UL certified requirements. These regulations provide guidelines for proper usage based on environmental conditions, application needs, and safety considerations.
For instance, UL-listed conduits like UL360 (specific to LFMC) meet rigorous testing criteria, including material and performance standards. In contrast, non-UL conduits may still perform well for general use but lack certification for specialized environments like hazardous locations.
Key Consideration: Always check if UL listing or other certifications are mandatory for your project to ensure compliance and reliability.
Indoor vs. Outdoor Locations:
Indoor Projects: Conduits such as Electrical Nonmetallic Tubing (ENT) or Flexible Metal Tubing (FMT) are ideal for indoor, concealed installations.
Outdoor Projects: For outdoor environments, choose conduits like Liquidtight Flexible Metal Conduit (LFMC) or Rigid PVC Conduit, which offer protection against moisture, sunlight, and temperature fluctuations.
Exposure to UV or Corrosive Elements:
For outdoor or industrial areas, conduits with UV resistance and anti-corrosion properties, such as LFMC or PVC, are crucial.
Temperature Resistance:
High-temperature environments require conduits rated to withstand elevated operating temperatures without degradation.
If your project involves a hazardous area (per NEC Chapter 5 classifications), ensure the selected conduit is approved for these conditions. For instance, LFMC is often required in hazardous locations if it meets the specific standards. Nonmetallic options like ENT may be unsuitable unless explicitly permitted.
The material properties of a conduit influence its durability, flexibility, and resistance to environmental factors:
Metallic Conduits: Ideal for high-strength applications and areas with physical damage risk. Examples include LFMC and Rigid Metal Conduit (RMC).
Nonmetallic Conduits: Suitable for lightweight, corrosion-resistant applications, such as PVC or ENT.
The trade size of a conduit affects its ability to house the required number of conductors without violating NEC fill requirements. Additionally:
Flexible conduits like LFMC and LFNC are ideal for applications requiring frequent movement or difficult routing.
Rigid conduits such as PVC and RMC are better suited for straight runs and structural support.
In projects with fire safety concerns, opt for conduits with flame-retardant properties (e.g., Low Smoke Halogen-Free options or conduits with UL94 flammability ratings).
To simplify the selection process, electrical contractors should:
Identify Compliance Needs: Confirm UL listing or other certification requirements.
Evaluate Installation Areas: Note environmental exposure, such as moisture, UV light, or corrosive agents.
Assess Material Properties: Choose materials offering the necessary protection and flexibility.
Determine Trade Size: Ensure proper sizing to accommodate wiring and connectors.
Account for Location Type: Choose conduits rated for hazardous, wet, or dry locations.
Prioritize Safety: Ensure fire resistance, temperature ratings, and durability align with project demands.
Choosing the right conduit type is a critical step in ensuring the safety, durability, and compliance of your electrical installations. This article has provided a comprehensive overview of the key aspects to consider, including the differences between Liquid Tight and PVC Conduits, an understanding of NEC code requirements, the permitted and restricted applications of popular conduit types, and practical guidance for selecting the best option for your specific project.
From the flexibility and moisture resistance of Liquid Tight Conduits to the cost-effectiveness and corrosion resistance of PVC Conduits, each type serves distinct purposes in different environments. Understanding their strengths and limitations is vital for achieving reliable and compliant results, especially when dealing with outdoor, hazardous, or high-temperature applications.
The NEC plays a central role in defining usage guidelines for various conduit types, helping professionals ensure safety and adherence to local regulations. By carefully evaluating factors such as location, material, environmental exposure, and flame-retardant properties, contractors can make informed decisions to optimize performance and protect wiring systems.
Whether you’re working on residential, commercial, or industrial projects, selecting a conduit that aligns with your application needs and regulatory standards ensures long-term success.
For more information about conduit pipe types, and finding the right solutions for your electrical projects, feel free to reach out to us.